Using silicone 3D printing for disability support
The silicone proves ideal for external medical applications; however, the hospital environment does not always have access to it. The emergence of silicone 3D printing offers a transformative perspective, paving the way for easier integration of this material into custom medical device production.
This advancement promises to substantially improve patient comfort while enriching healthcare practices. Let’s explore the possibilities that silicone 3D printing unfolds in the medical field and its tangible impacts on medical practice and patient well-being.
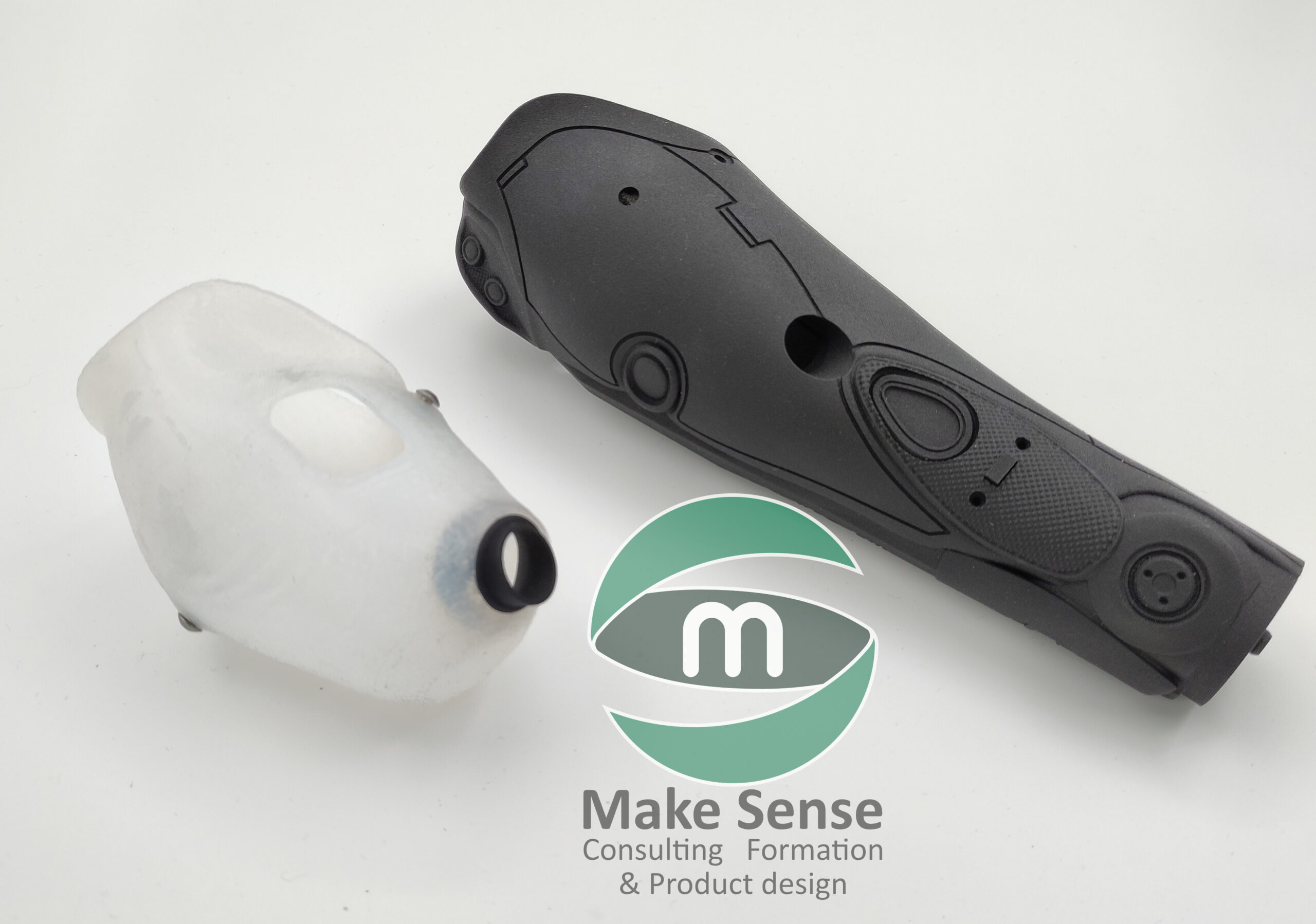
Mechatronic prosthesis by Make Sense and 3D printed socket
Transforming Medical Care with 3D Printing
Silicone, widely adopted in medical devices for its properties such as biocompatibility, flexibility, durability, and ease of sterilization, reduces the risks of adverse reactions, making it an ideal material for various medical devices. Its hypoallergenic properties make it a safe choice for devices in contact with the skin or internal tissues.
Silicone, easily washable, maintains crucial hygiene for long-term use of prosthetics. This feature not only contributes to the patient’s well-being but also simplifies the daily care routine, allowing people with prosthetics to focus more on their personal health. Silicone 3D printing contrasts with the current process of often unpleasant, inaccurate, and prolonged patient molding. The use of 3D scanning provides a less burdensome experience, allowing precise digitization of 3D files of medical devices.
Additionally, the digital process allows for longer and easier follow-up, offering the possibility of adjusting treatment more easily according to the patient’s needs. Silicone 3D printing, combining the advantages of silicone and 3D technology, paves a new path for custom medical solutions, ushering in an era of innovation centered on patient comfort and quality of life.
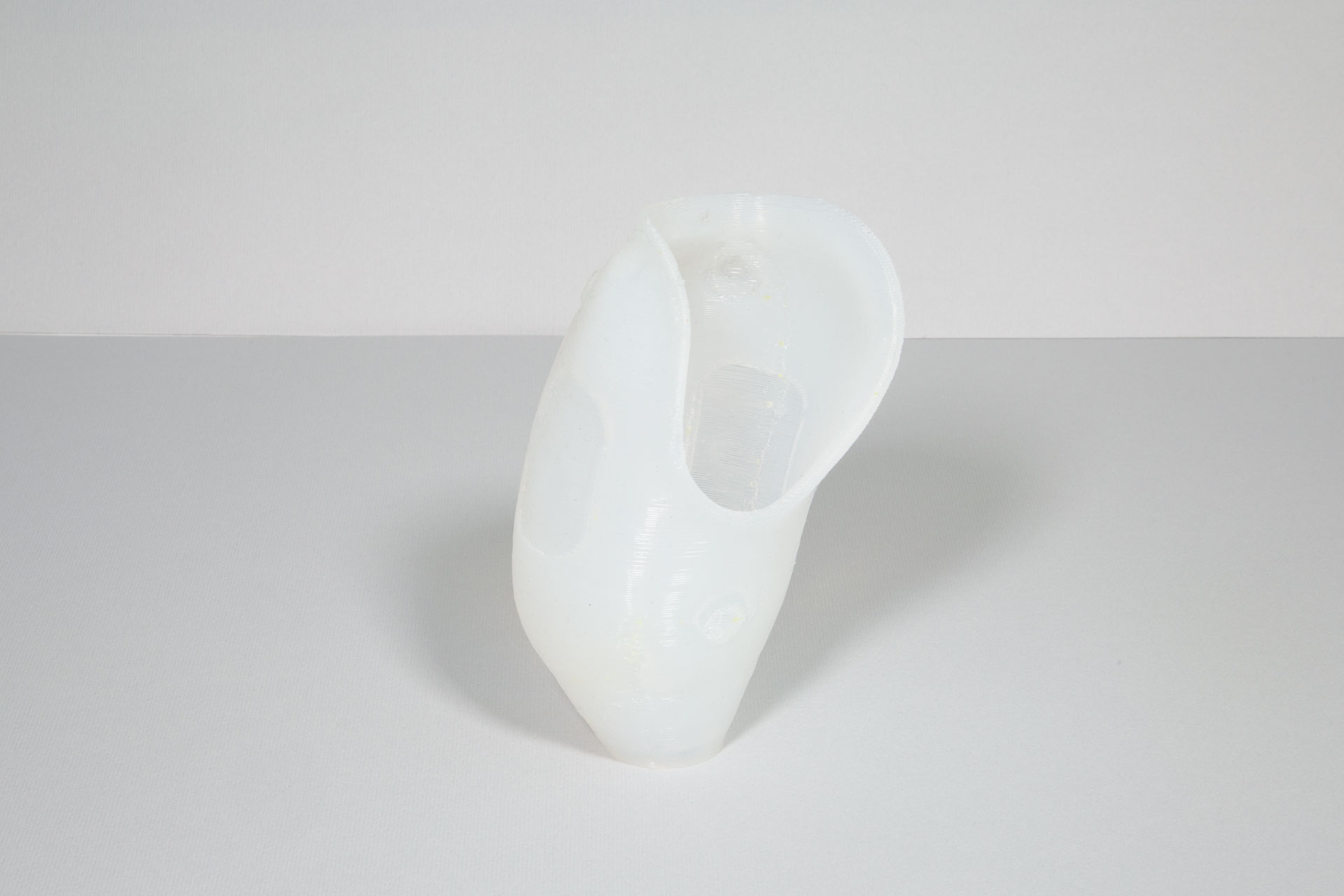
Trans-radial myoelectric (or mechatronic) prosthesis socket 3D printed
Improving Prosthesis Sockets for Upper Limbs
It is estimated that 1.5 million people are amputated each year worldwide, with 15% involving the upper limb. Approximately 65 million people were living with an amputation in 2021.
Silicone 3D printing stands out for its ability to produce prosthetic sockets without requiring the molding step. This technique allows for precise layer adjustments to optimize patient comfort while offering significant advantages in terms of productivity and cost reduction in medical device manufacturing.
By eliminating the constraints associated with molding, 3D printing allows for faster and more precise customization of prosthetic sockets, thereby improving the quality of care provided to patients. It simplifies the production process, accelerating access to prosthetics for the patient. Currently, the development of external medical devices by silicone 3D printing is in development and at the proof-of-concept stage for mechatronic upper limb prosthesis sockets in patients with agenesis or in pediatric cases.
A mechatronic prosthesis, also known as a myoelectric prosthesis, is an advanced artificial limb combining mechanical and electronic engineering. These prostheses use sensors and motors to detect and respond to user muscle contractions, offering a more natural and intuitive range of movements. Mechatronic prostheses aim to improve the functionality and mobility of amputees, providing better control and a higher quality of life compared to traditional prostheses.
They require sensor contact with the skin while offering maximum support and comfort for the patient. Printing this type of socket fits perfectly into a comprehensive CAD/CAM design of the prosthesis. This provides a set of solutions to optimize production, control, renewal, and customization of the medical device, thereby contributing to improving patient care delivery.
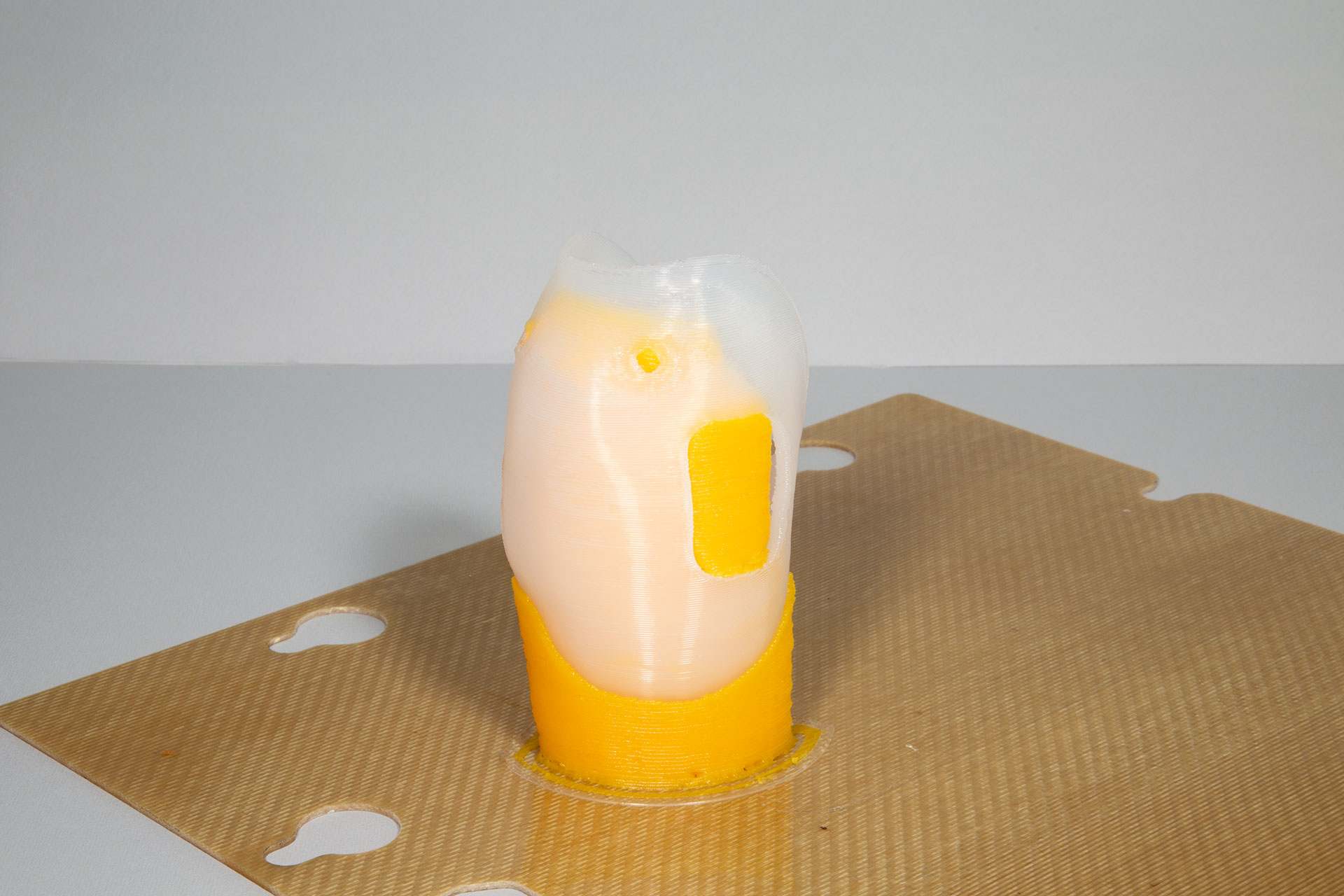
Trial of upper limb socket 3D printed with openings
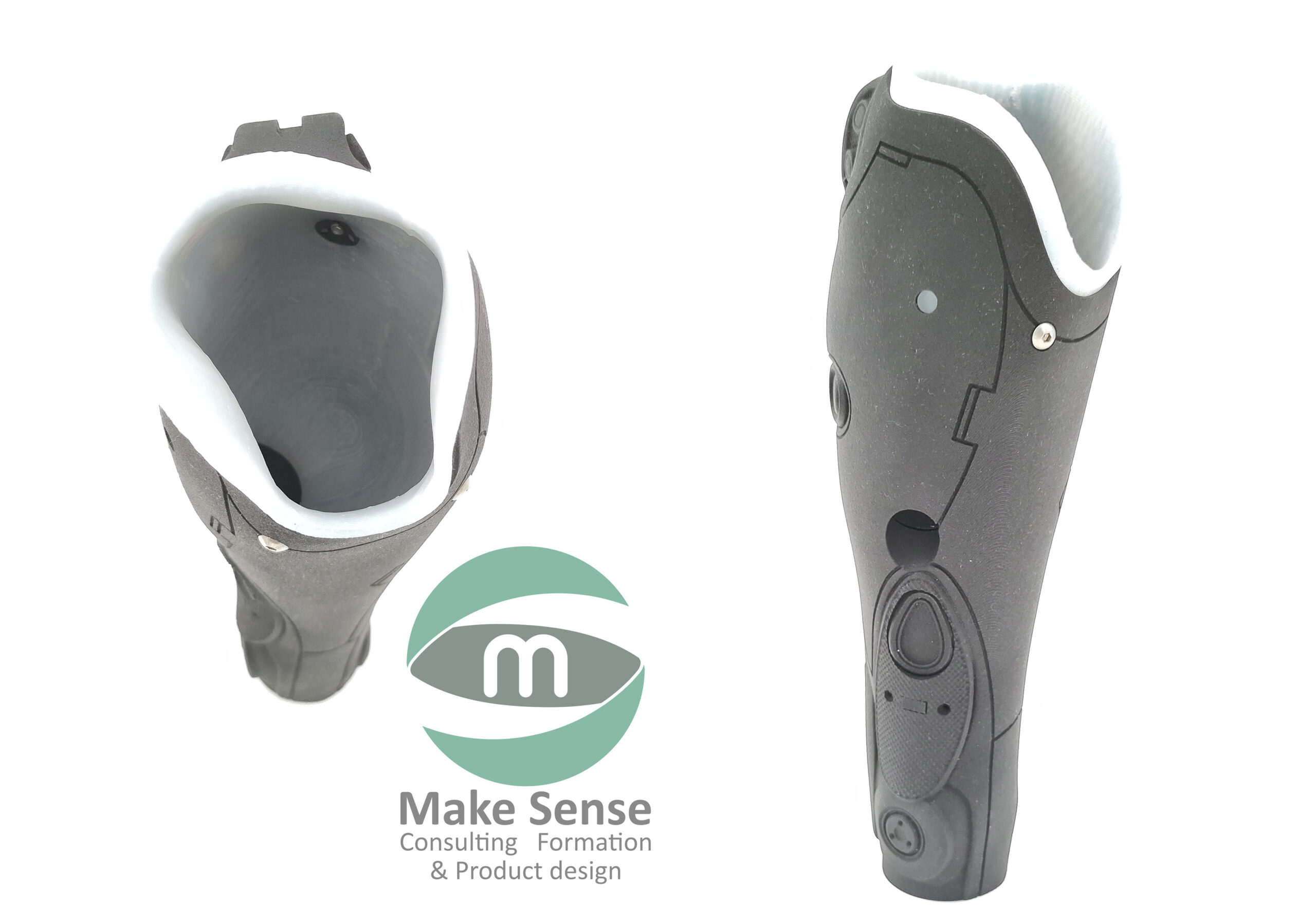
Mechatronic prosthesis by Make Sense and 3D printed socket
They also offer the possibility for healthcare professionals to refocus on their medical and clinical skills by relieving themselves of more delicate production tasks. However, they require healthcare professionals to acquire a set of new “strong” skills upstream (3D scanning and design) to fully exploit their potential.
Owning a 3D printer without mastering digital design could pose a challenge.
3D Printing for Enhanced Personalized Therapeutic Education
The integration of digital technologies and 3D printing in prosthetic production goes beyond mere comfort. It offers patients the opportunity to actively participate in their prosthetic journey (or device project). The customization offered by 3D printing technologies allows for a more collaborative approach between patients and healthcare professionals.
Individuals experiencing limb loss face not only physical challenges but also emotional and psychological obstacles, which can present pathologies related to physical changes and disruption of self-image (identity reconstruction). The opportunity to be involved in the design and creation of their prosthetic components offers a sense of ownership and control. This active participation significantly contributes to the patient’s self-esteem and mental well-being, fostering a positive outlook on their rehabilitation process.
As this technology progresses from proof of concept to widespread implementation, we can anticipate a paradigm shift in how individuals approach and live with prosthetics. The fusion of cutting-edge innovation and patient-centered design paves the way for a future where comfort, self-esteem, and rehabilitation are seamlessly integrated.
Timelapse of ergonomic and non-slip silicone cup grip aid
Silicone 3D Printing for Personalized Assistive Device Design
The use of silicone 3D printing enables the widespread design of silicone assistive devices within hospital fab labs. Occupational therapists can leverage this technology to create personalized silicone assistive devices tailored to the specific needs of individuals seeking autonomy after a stroke or an accident resulting in a form of disability. This technology offers a valuable new service for patients in rehabilitation centers.
A concrete example is this grip aid for cups and glasses, customizable according to individual needs. This aid adapts to all hand ergonomics, offering resistance, grip, and protection against burns. Easy to wash and transport due to the material’s flexibility, it takes up little space, making it a practical assistive device to carry, for example, in a bag. The non-slip silicone ensures that the glass stays in place when the patient needs to remove their hand.
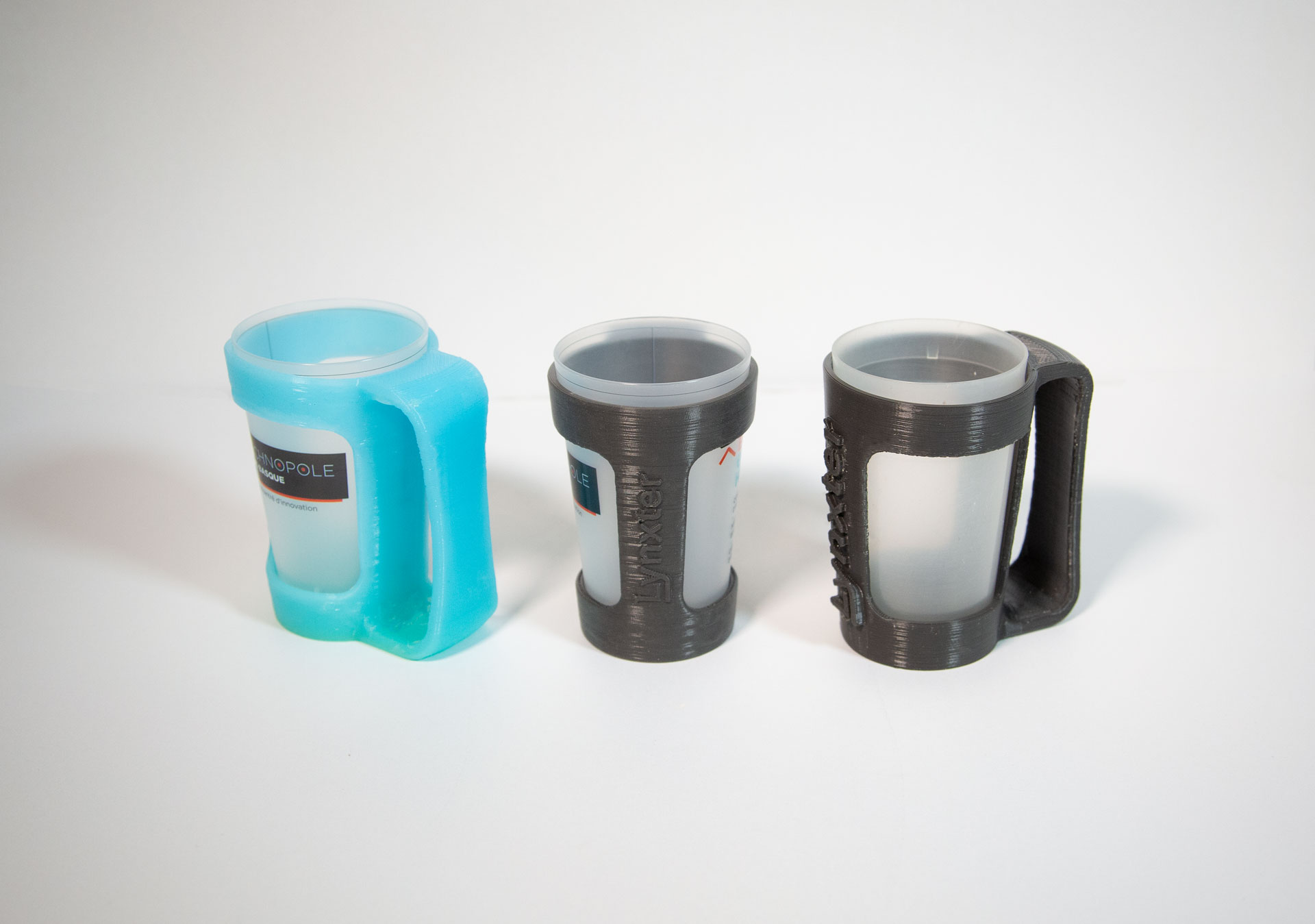
Example of ergonomic and non-slip silicone cup grip aid
Information on Printing
SECTOR | Health, Occupational Therapy |
APPLICATION | Ergonomic cup – assistive device |
MATERIALS | Skin contact silicone |
DIMENSION | 104 mm – 110mm – 78.5mm |
3D PRINTER | MEX – S300X LIQ21 | LIQ11. |
PRINTING TIME | 6H |
MATERIAL QUANTITY | 200 gr |
LAYER HEIGHT | 0.35 mm |
NOZZLE SIZE | 0.69 mm |
Thanks to the S300X Silicone 3D printer, occupational therapists or physiotherapists have a new material for creating custom small parts aimed at improving patient comfort and mobility.
Depending on the needs, the relevant medical service can be trained in 3D design, integrate printers into its service, or use specialized external providers in the production of 3D printed silicone medical devices.
This approach allows for accessible and effective customization, meeting the specific needs of each patient. Thus, silicone 3D printing can be an important new tool for adapting assistive devices, thereby contributing to improving the quality of life of individuals in rehabilitation or living with a form of disability to compensate for daily challenges.
Today, hospital services can start integrating medical 3D printing by collaborating with specialized external providers or by training in CAD (computer-aided design) and 3D printing, thus ensuring a gradual transition to a more personalized and innovative medical practice.
Lynxter and Make Sense can support you in this new project. Contact Lynxter for more information on our research and use cases, as well as the impactful use of the S300X 3D printer.
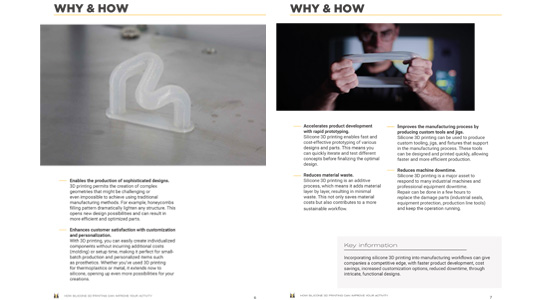
DOWNLOAD THE WHITE PAPER
Download now “Improve your workflow with silicone 3D printing”.
Discover how this new technology can enhance your productivity and innovation.
Don’t miss this opportunity to gain a new competitive advantage.