Improving orthopedic care through 3D silicone printing
Trinytec and Lynxter, two entities dedicated to research and development, are combining their expertise to develop and enhance current orthopedic solutions. The application’s concept ? Combining the liquid 3D printing capabilities of the S300X – LIQ21 | LIQ11 with Trinytec’s orthopedic expertise to print personalized silicone orthopedic collars.
Silicone orthopedic 3D printing improves patients’ daily lives
Traditional manufacturing processes in orthopedics are complex and often involve multiple steps. Silicone 3D printing offers numerous advantages, including high performance, quality, and reproducibility.
The predominant advantage of silicone 3D printing is the ability to create and design custom orthopedic devices in a shorter time frame and at a lower cost, with a simplified process. The morphology of each patient is unique, so, 3D printing is ideal for designing individualized devices tailored to everyone.
Other benefits emerge from this technological solution:
-Expansion of design and functionality possibilities
-Diverse creativity and design options
-Improved precision and repeatability
-Optimized comfort
-Standardized equipment
-Reduced delivery times
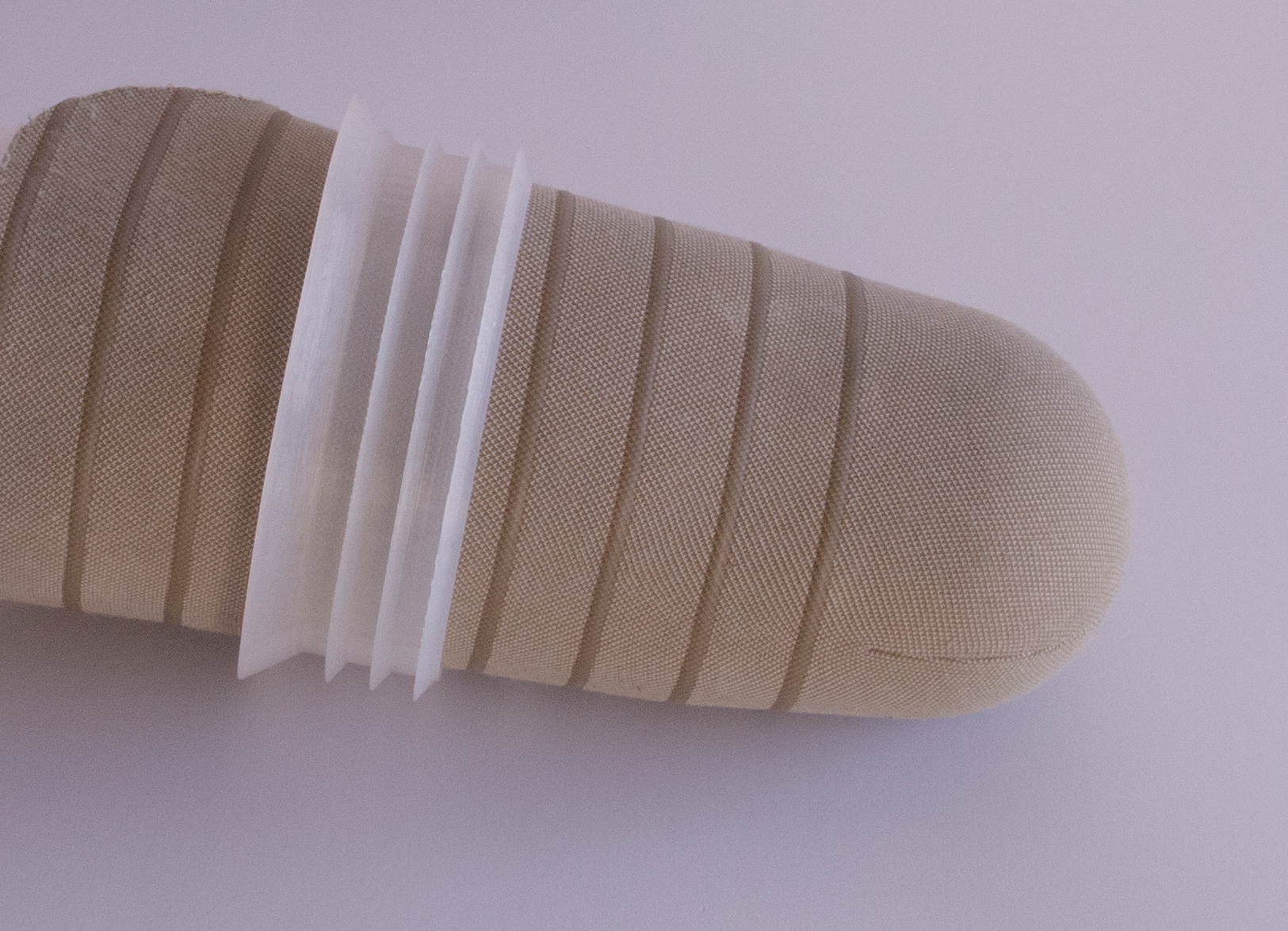
Custom silicone collar on its sleeve
Lynxter’s expertise in silicone 3D printing brings new perspectives to the sector, suggesting new applications such as insoles, sleeves, collars, and more. Lynxter, in partnership with several healthcare professionals, is continually researching the advancement of these solutions and is a driving force in proposing a new solution with the development of the S300X – LIQ21 | LIQ11.
Timelapse of the collar printed by the S300X silicone 3D printer
The Trinytec silicone collar
Orthopedic appliances are devices that can significantly impact a person’s life. They stabilize, immobilize, guide, or alleviate patients from a damaged part of the body. To optimize their support, each must be custom-made to accommodate the various patient morphologies.
The interface between the socket and the patient’s sleeve is often delicate. An ill-fitting sleeve can lead to painful consequences in a patient’s daily life, both physically and psychologically.
The observation: today it is common to have problems adapting the socket to meet the specific needs of patients. This is why Stéphane Paillet from Trinytec came up with a new concept, the orthopedic collar on scan.
Entirely 3D printed in silicone certified skin-contact on the Lynxter S300X – LIQ21 | LIQ11 machine, customized to the patient’s dimensions, the collar, to position on the sleeve, provides an optimal solution for comfort and relief. The choice of silicone is justified by its technical properties, allowing for a lightweight piece while maintaining its durability. This significantly reduces the burden on the patient, a crucial factor for individuals with mobility issues. Silicone is also a durable and resistant material, meaning that orthopedic collars can be worn without requiring frequent replacements.
The IDEX technology of the Lynxter S300X – LIQ21 | LIQ11 is the ideal solution for this application, enabling the printing of silicone and support material for complex geometries.
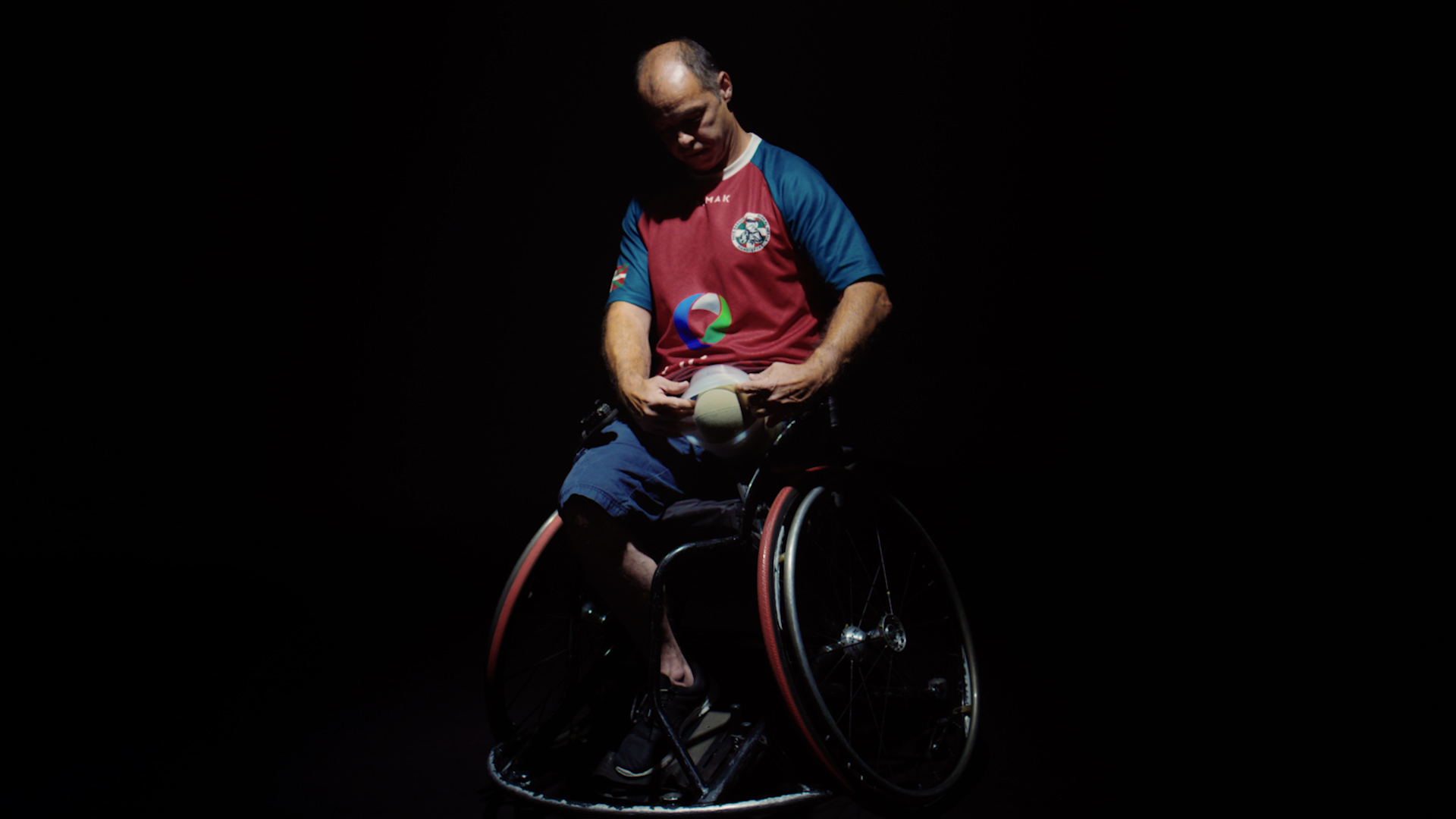
Axel Lavelle is trying on the printed collar
“I had the opportunity to try this collar, and it provides daily comfort due to its practicality and easy installation” – Axel Lavelle
A quick and simplified manufacturing process
Just a few steps are needed to 3D print a silicone collar:
1. Patient measurements are taken.
2. The design file for the custom piece is created.
3. The personalized piece is 3D printed.
4. The collar is delivered.
5. Adjustments and fine-tuning of the piece are made.
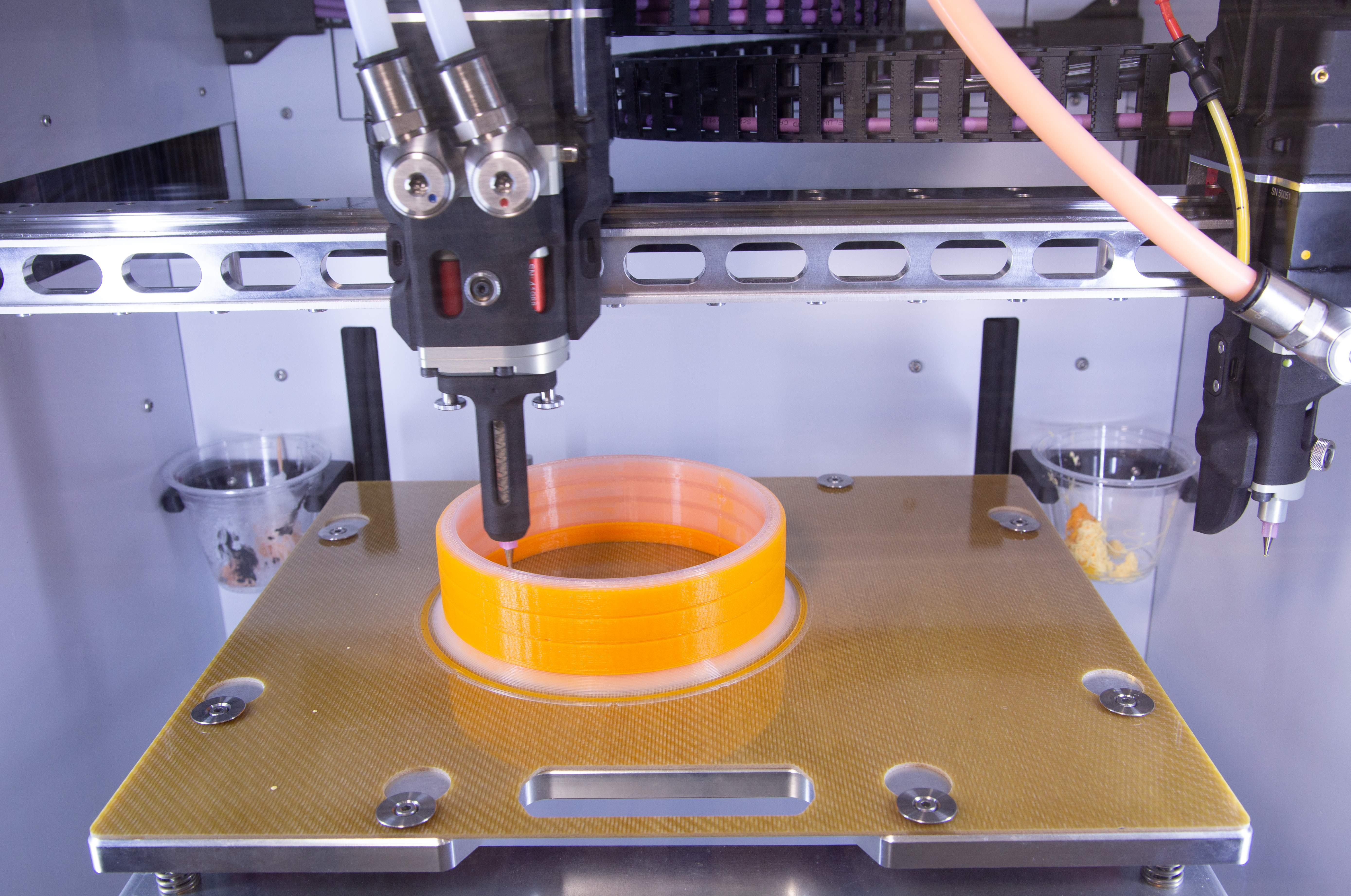
Printing
of the silicone collar on the S300X – LIQ21 | LIQ 11
Technical Specifications of the piece
SECTOR | healthcare, orthopedics |
APPLICATION | orthopedic collar |
MATERIAL | Silicone COPSIL4025 |
DIMENSION | customized to the patient’s dimensions |
PRINTING TECHNOLOGYE | MEX – LIQ with the S600D or S300X LIQ21 | LIQ11. |
PRINTING TIME | 5h / part |
MATERIAL QUANTITY | 50 gr |
LAYER HEIGHT | 0.6 mm |
NOZZLE SIZE | 1 mm |
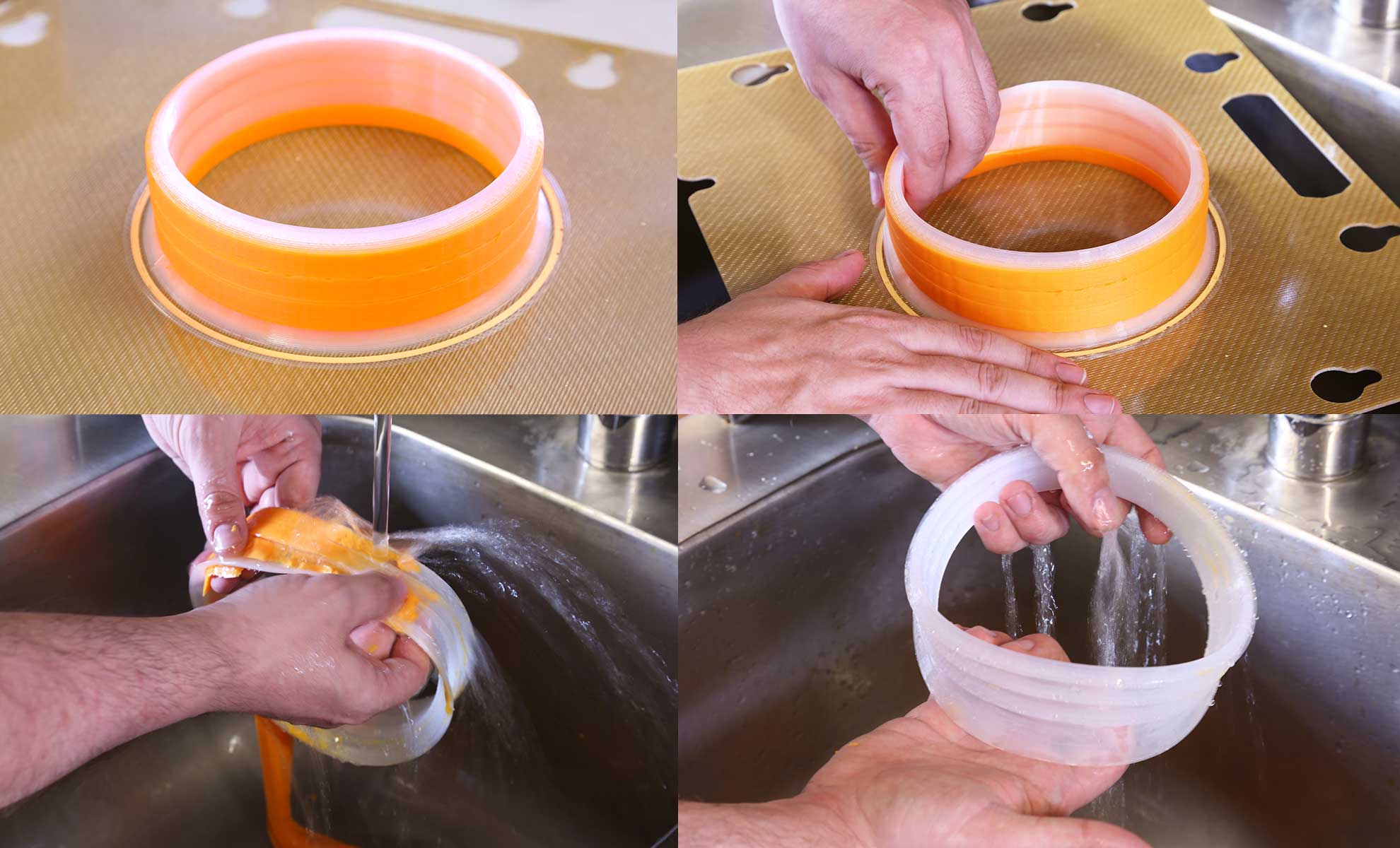
The collar was made with a water-soluble support SUP-001
Future technology
It’s evident that additive manufacturing plays a central role in the medical field, primarily due to the ability to create and customize solutions for everyone. Additionally, advancements in the range of printable materials suggest ongoing innovations.
The orthopedic sector is evolving, and the profession is gradually being reshaped by these developments. More and more patients today are benefiting from comfortable and high-performance devices delivered in shorter timeframes
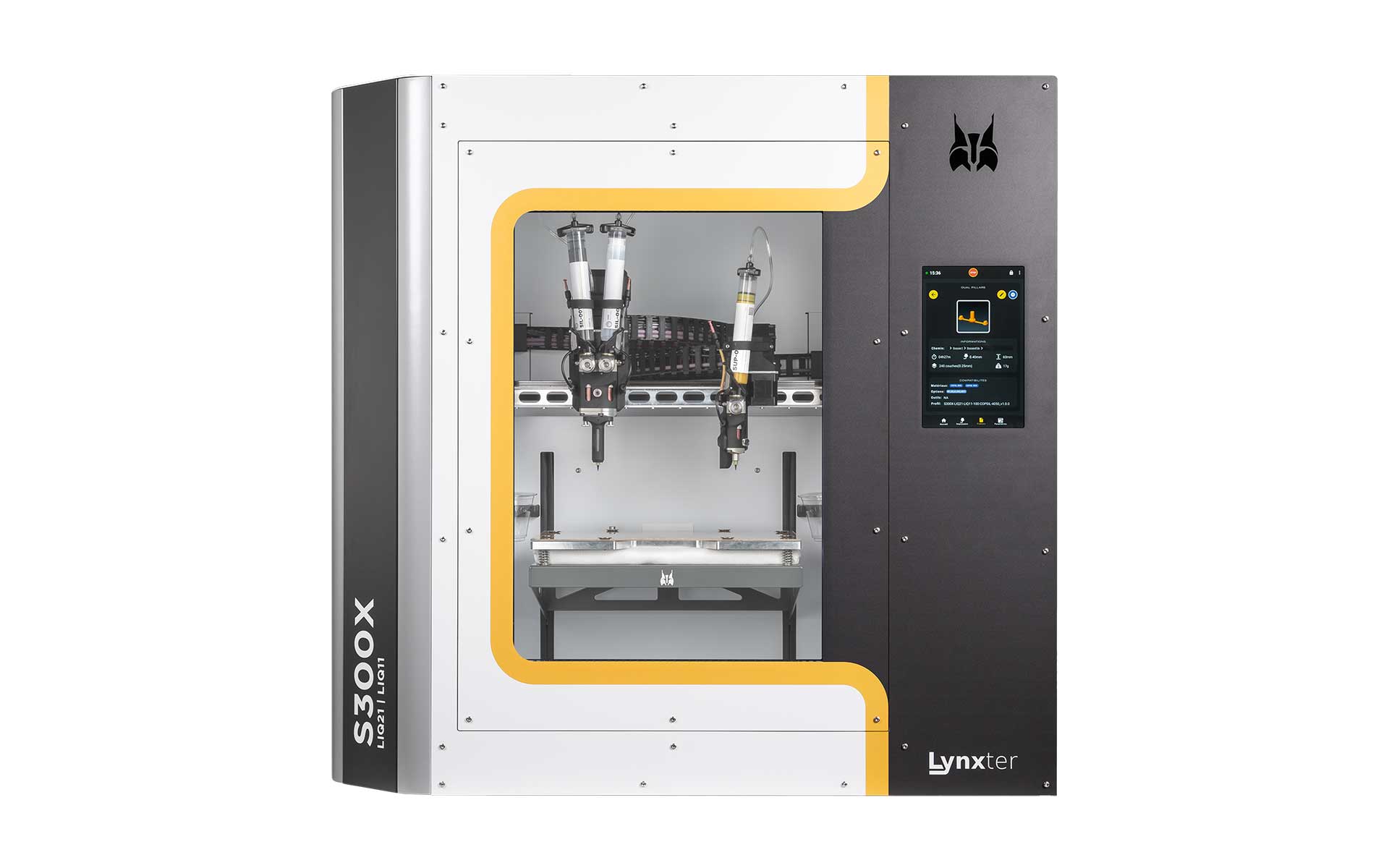
S300X LIQ21 | LIQ 11
About Trinytec
Trinytec, a startup founded in 2018, was born out of the need for research and development. Their engineering office is dedicated to development in the field of medical devices, particularly in orthopedics.
Their engineering activities are now complemented by their team’s experience in the world of 3D design, and their printing facility is open to all projects. Since early 2019, Trinytec has developed a wide range of silicone, pigments, pre-impregnated carbon, as well as all the necessary equipment for their implementation. Their product range now includes over 500 references.
For more information: trinytec.com