Silicone 3D printing: How and why print silicone?
Lynxter, pioneer and leader in modular 3D printing, looks back at the success of Silicone 3D printing: the choice of this material, its advantages, its extrusion process compared to traditional methods and the users’ cases in Industry 4.0. Discover how Lynxter‘s R&D team defines the basics and experiments every day to change the rules to go beyond what liquid 3D printing is today.
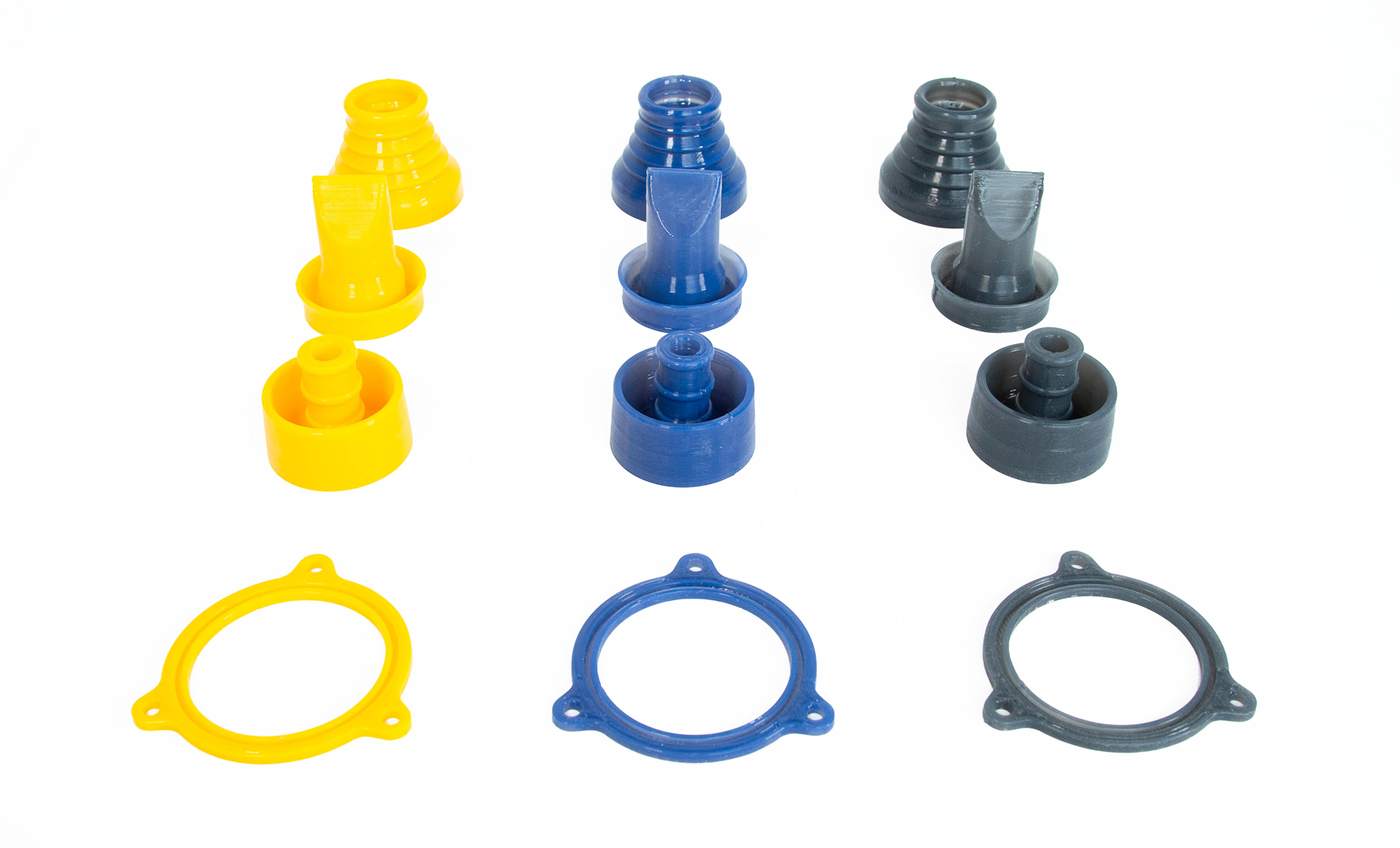
3D printed RTV2 silicone seals
Usually, liquid materials are shaped by molding. This process is interesting for large series, but the manufacturing of a mold is generally long and expensive. This process is viable for this type of production, but it remains limited in terms of geometries since it does not allow the manufacture of non-full parts, optimized in terms of weight or hardness.
Silicone 3D printing therefore provides a new and interesting complementary solution to enrich the inventory of shapes and elasticity.
Silicone
Definition: what is a silicone?
Silicone is the common name for polysiloxane, a class of polymer chains consisting mainly of silicon, oxygen and organic groups. The bonds between the oxygen and silicon atoms allow a high mobility of these polymer chains, which results in a strong deformability of the material at room temperature. This family of polymers differs with their chemical stability as well as their physical and mechanical properties.
Silicone comes in several states depending on its macromolecular structure, the size and size distribution of the chains that compose it. There are silicone oils and gums (used as additives, lubricants, hydraulic fluids), gels (used for example in breast prostheses, bicycle saddles) and finally elastomers. Silicone elastomer is the most commonly used form.
What is an elastomer?
It is the cross-linked state of silicone (a dense three-dimensional network of silicone chains) that gives it its known elasticity properties.
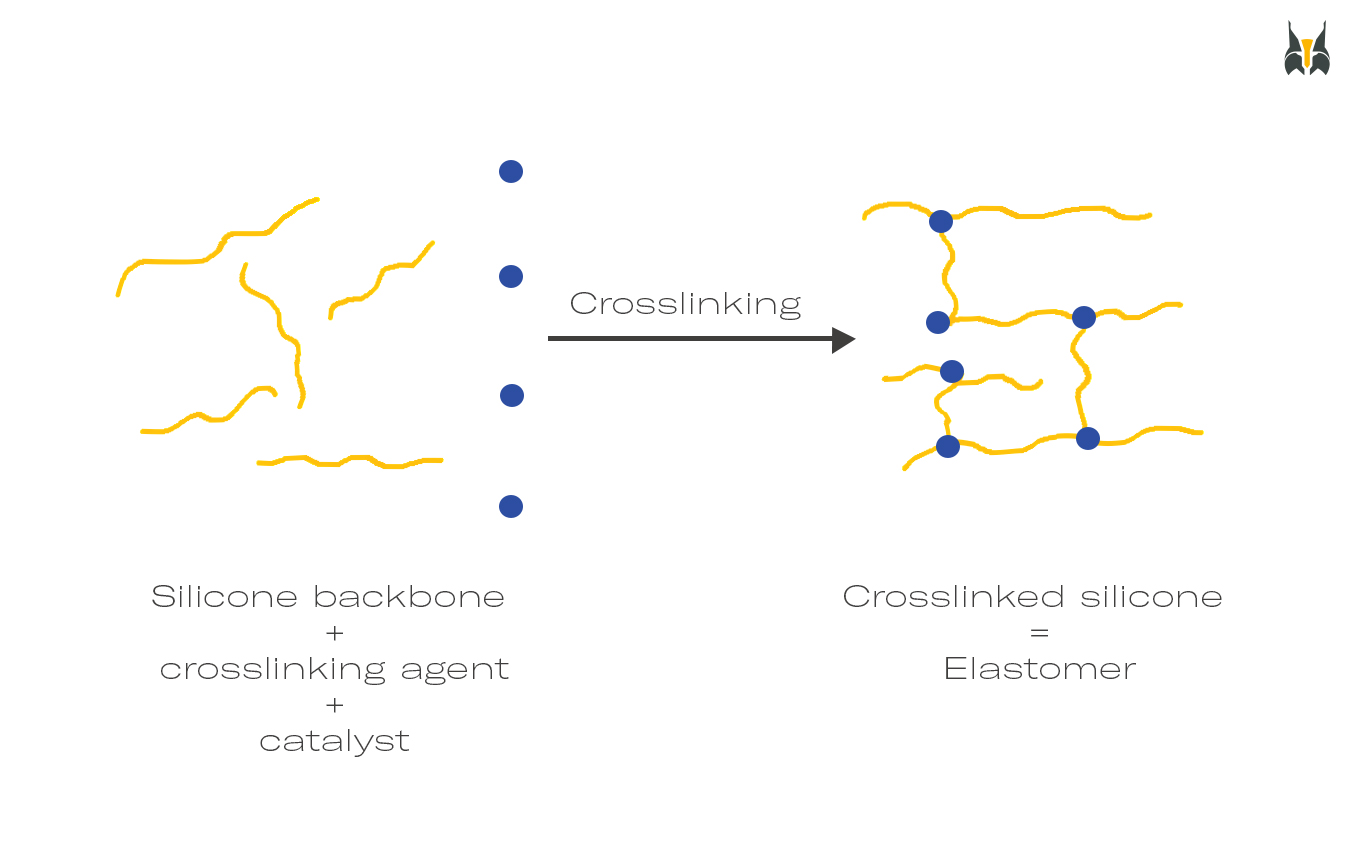
Cross-linking reaction
It is possible to add reinforcing fillers and additives in the formulation to improve the mechanical or thermal properties of the elastomer. There are several categories of silicone elastomers, according to their cross-linking reaction:
· Room Temperature Vulcanization elastomers (RTV)
RTV1 (Room Temperature Vulcanization mono-component) are presented in the form of a rather viscous mono-component liquid which cross-links progressively on contact with air humidity. The cross-linking of these silicones is done at room temperature and can generate reaction by-products (acetic acid for example) which restricts their use. The most common applications for this type of elastomer are glues, adhesives, sealants and hand sealing (e.g. bathroom).
RTV2 (Room Temperature Vulcanization two components) are two relatively fluid liquid parts. The cross-linking of these silicones happen by mixing the two parts at room temperature. Its low viscosity makes it easy to use in general, but more particularly for injection molding or impression taking. It does not emit any reaction by-products and is therefore very interesting for the medical sector. It can therefore be used for uses requiring contact with the skin or even food.In 2023, Lynxter created the SIL-001, the first ready-to-print RTV2 50 ShA silicone.

3D Printing of 27 parts in silicone in 30 min for industrial masking on the S300X
· High Temperature Vulcanization elastomers (HTV)
HCR (High Consistency Rubber) is a paste-like block of single or two component silicone that cures under pressure and high temperature. Traditionally, this type of silicone is processed with roll mixers or calenders to form a silicone with high tensile and tear strength and good aging resistance. This makes it particularly suitable for industrial applications (gaskets, tubes, cable protection).
LSR (Liquid Silicon Rubber) are two liquid parts that are quite viscous and need to be mixed and heated to bring about the cross-linking reaction. This type of silicone elastomer has very good mechanical properties and covers a wide range of hardness. It is very suitable for applications requiring food contact or medical use.
Among all the existing technical elastomers, silicone should be preferred for its very good temperature resistance (from -50°C to 250°C on average) and its chemical inertia: it can be used in demanding environments: in contact with solvents, hydrocarbons but also in contact with skin or Food products.
Comparison of acetone solvent resistance between RTV2 silicone and TPU
Liquid 3D printing by MEX
How to print a liquid material?
Since 2016, Lynxter has been developing several printing technologies on the S600D modular 3D printer: thermoplastic filament extrusion, filled pastes, and single and dual component liquids. The liquid 3D printing technology is available in two toolheads formats designed by Lynxter: the LIQ11 toolhead can print single-component liquids (e.g. RTV1), while the LIQ21 toolhead can print two-component liquids (e.g. RTV2 or LSR) : they need to be mixed together to bo transformed from a liquid to a solid.
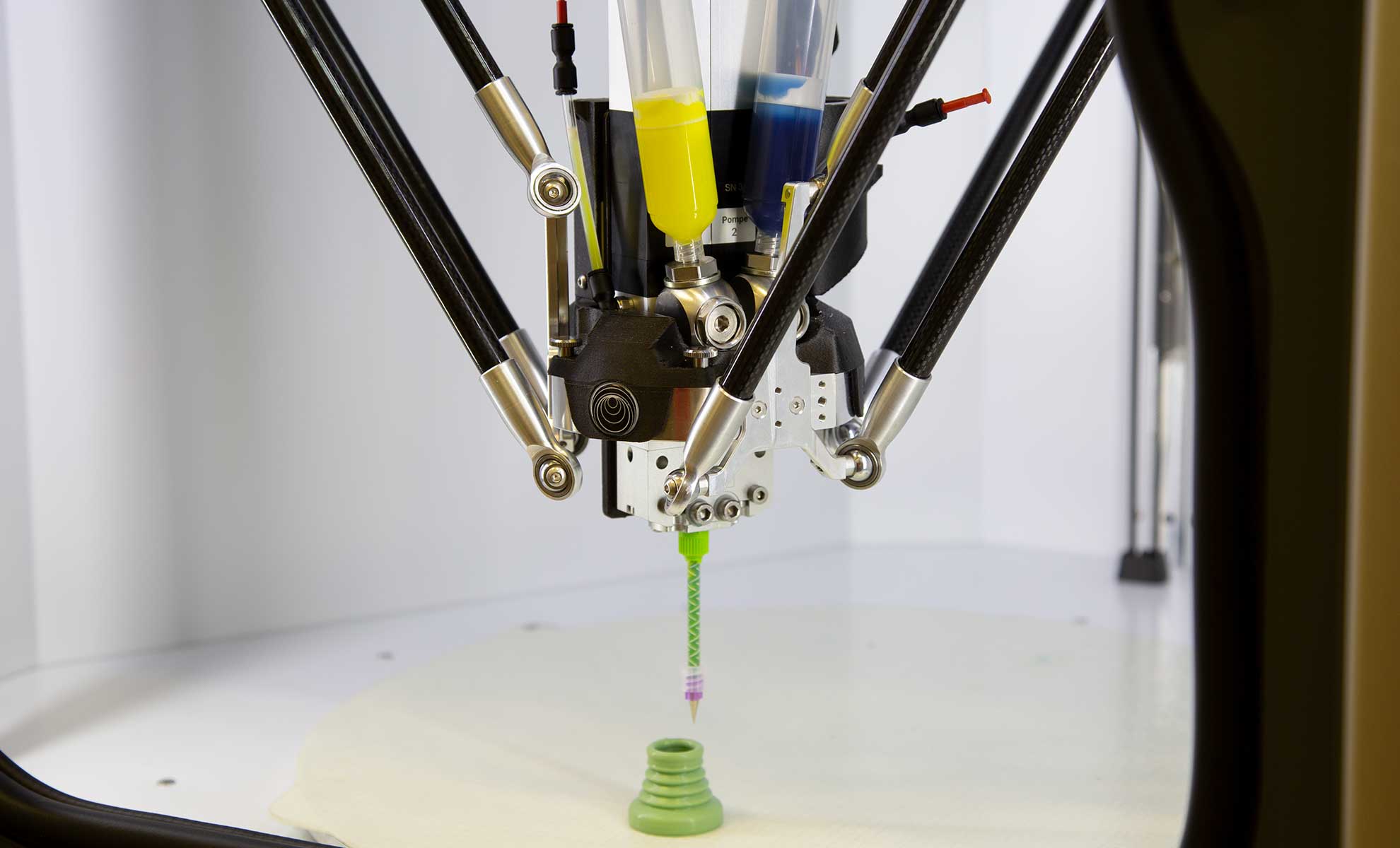
Liquid 3D printing toolhead LIQ21
The liquid to be printed must first be packaged in connectable syringes with a piston. Lynxter’s liquid printing heads are equipped with volumetric dosing pumps that provide high dispensing and dosing accuracy. Pressurized syringes (compressed air) supply these pumps with raw material. The pumps convey and dose the amount of material to be printed, which is deposited by means of a precision nozzle connected to the pump outlet. The LIQ21 toolhead uses a static mixer between the pump and the nozzle, which leads to a homogeneous mixture of the two liquid components to be printed.
The principle of this additive manufacturing process is similar to the FFF/FDM/MEX process: it consists of depositing beads one after the other, layer after layer, until the complete construction of the object to be printed.
However, the deposited bead is not fixed at the nozzle exit (as when the thermoplastic is cooled at the extrusion exit): the printed liquid is formulated to have a specific rheology such that the material can be superimposed on itself without collapsing. The cross-linking reaction takes place during and after the printing process and “freezes” the already shaped material. After cross-linking, the part obtains its final physical and chemical properties.
Thus, the liquid materials that can be printed with this technology are essentially thermosetting (with an elastomeric behavior for silicones).
Silicone 3D printing
Lynxter, expert in silicone additive manufacturing
One of the advantages of 3D printing technologies is their reactivity. In the case of silicon, it can be used to manufacture spare parts in emergency, maintenance or to help supply shortage optimization. The parts manufactured in this way are made of “good material” and therefore directly functional after print.
Since the manufacture of molds is no longer necessary, the design iteration of the parts is done more easily, more quickly and therefore more economically. Once CAD is mastered, it is also possible to think about lightening the final part by adjusting the infill rate and pattern.
3D printed RTV2 silicone suction cup gripper
Silicone parts obtained by additive manufacturing on the S600D have similar mechanical properties to parts obtained by molding or casting. The deposition of liquid material allows the creation of covalent chemical bonds between the layers and thus to obtain completely isotropic parts.
Silicone 3D printing is a true asset for the manufacture of custom parts in health or other fields, it makes the management and monitoring of patients easier. It is possible to adjust and rework a device by adjusting the CAD, without requiring a new impression for example.
Since 2017, Lynxter has been developing its expertise in additive silicone manufacturing. All the work done since then has been done in close collaboration with material partners and has resulted in a range of silicone materials for 3D printing.
Lynxter can count on its laboratory: equipped with formulation and raw material conditioning means, it facilitates and accelerates the technology development. All materials available on the Lynxter ecosystem have a set of print parameters ready to be used in the slicing software. Lynxter’s material and process expertise allow it to provide a plug and play solution and support customers in developing their applications. Currently, the range of silicones compatible with the S600D spans several hardnesses and includes RTV1 and RTV2 silicones. Some of these materials have specific properties such as skin contact (ISO 10993-5).
The different hardnesses of silicones printed by Lynxter
Applications and users’ cases of silicone 3D printing
Today, 3D printing of silicone is used in many sectors for its chemical and thermal characteristics to produce custom parts, or spare parts.
Timelapse of the wafer printed by the silicone 3D printer S300X
An important step in Healthcare
In the medical field, silicone 3D printing is used in the making of suture training supports, in the production of orthopedic parts (podology, orthoprosthesis), but also of medical implants for epithetics or ostomy bag wafer for example.
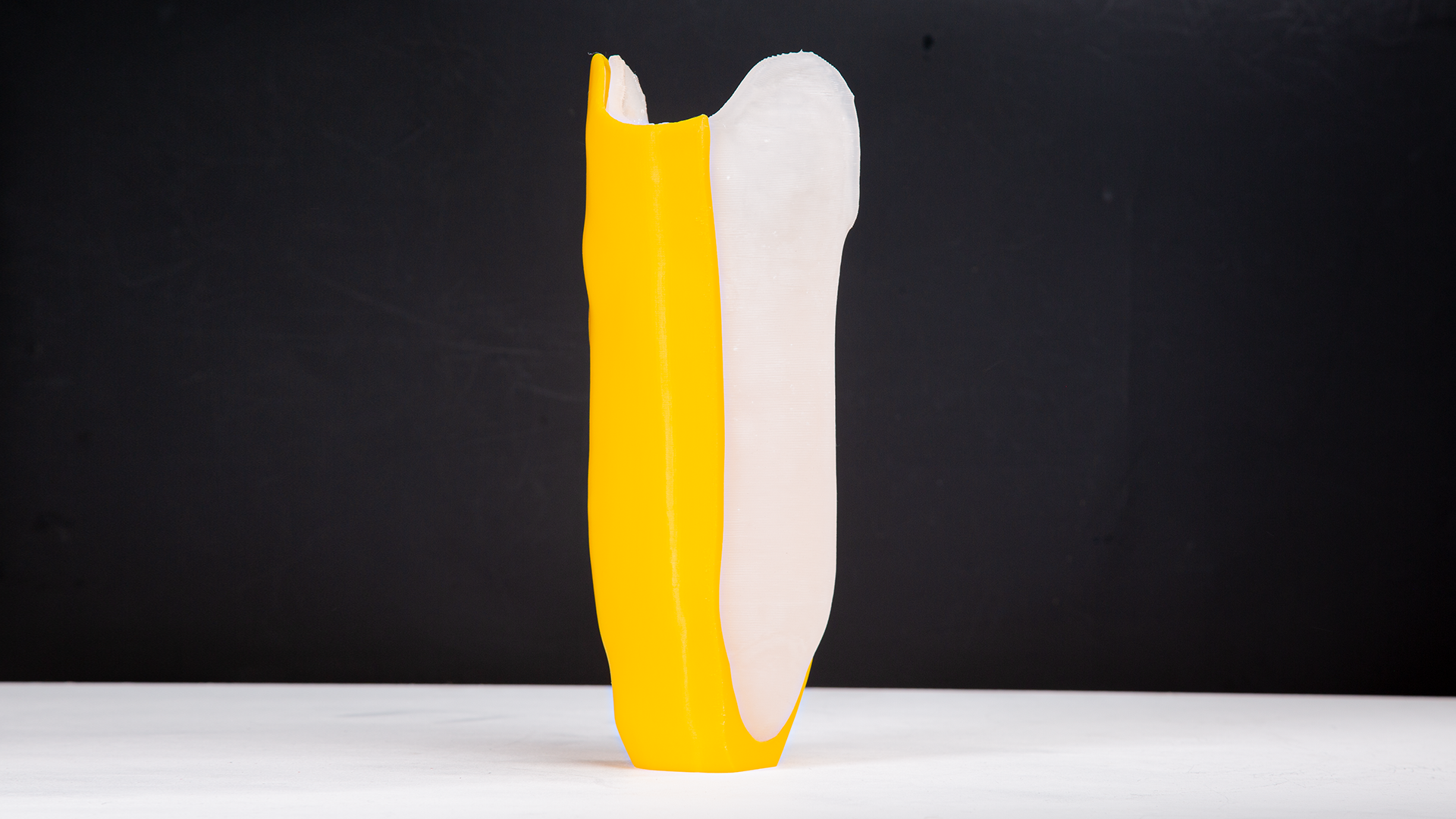
Silicone printing for medical – Orthopedic device
Improved responsiveness in the industry
In industry, this technology can be used in masking applications for surface coating treatments. It is also useful to produce single shape gaskets for any sealing situation. Finally, it plays an important role in the development and production of grippers for soft robotics, which represents a real challenge in the evolution of industrial lines.
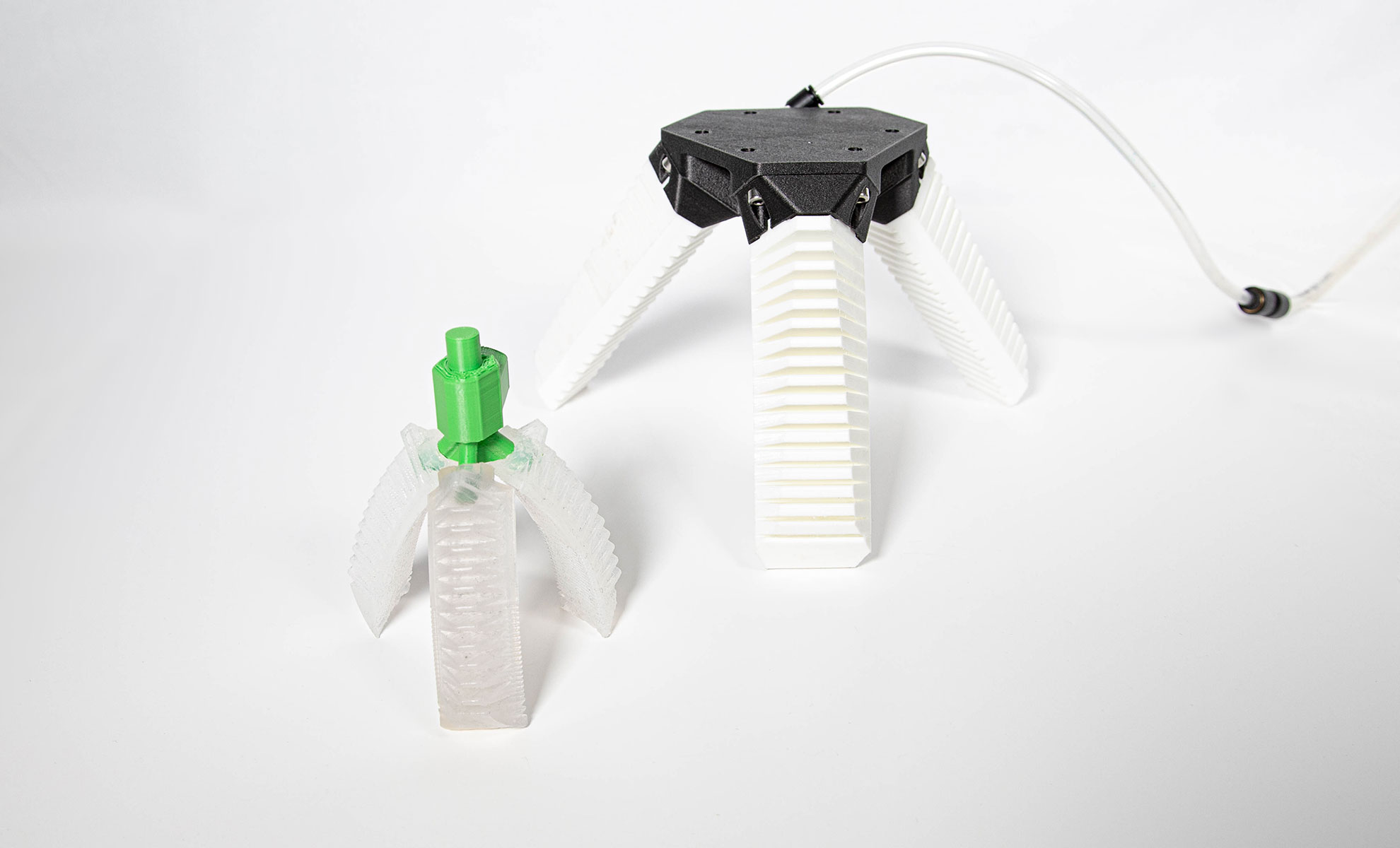
Soft robotics grippers by Schneider Electric
A new experimental playground
Similarly, it is possible to functionalize textiles by printing directly on their surface. Textiles functionalized in this way respond to aesthetic issues in the fashion sector or to the addition of functions, such as anti-slip (socks, stockings).
The textile industry is completely reinvented through silicone printing on fabrics and leather
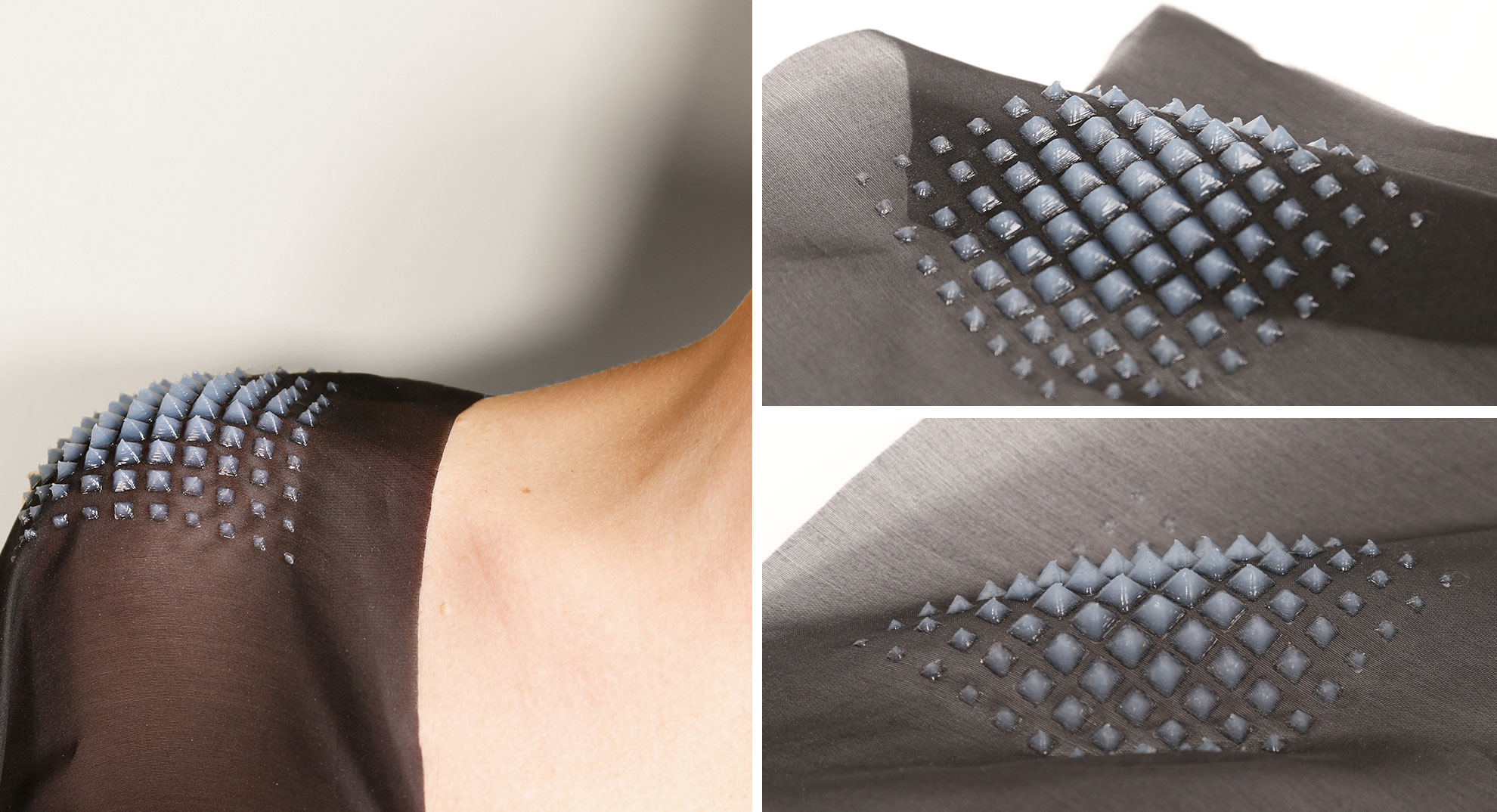
RTV2 silicone printed on textile
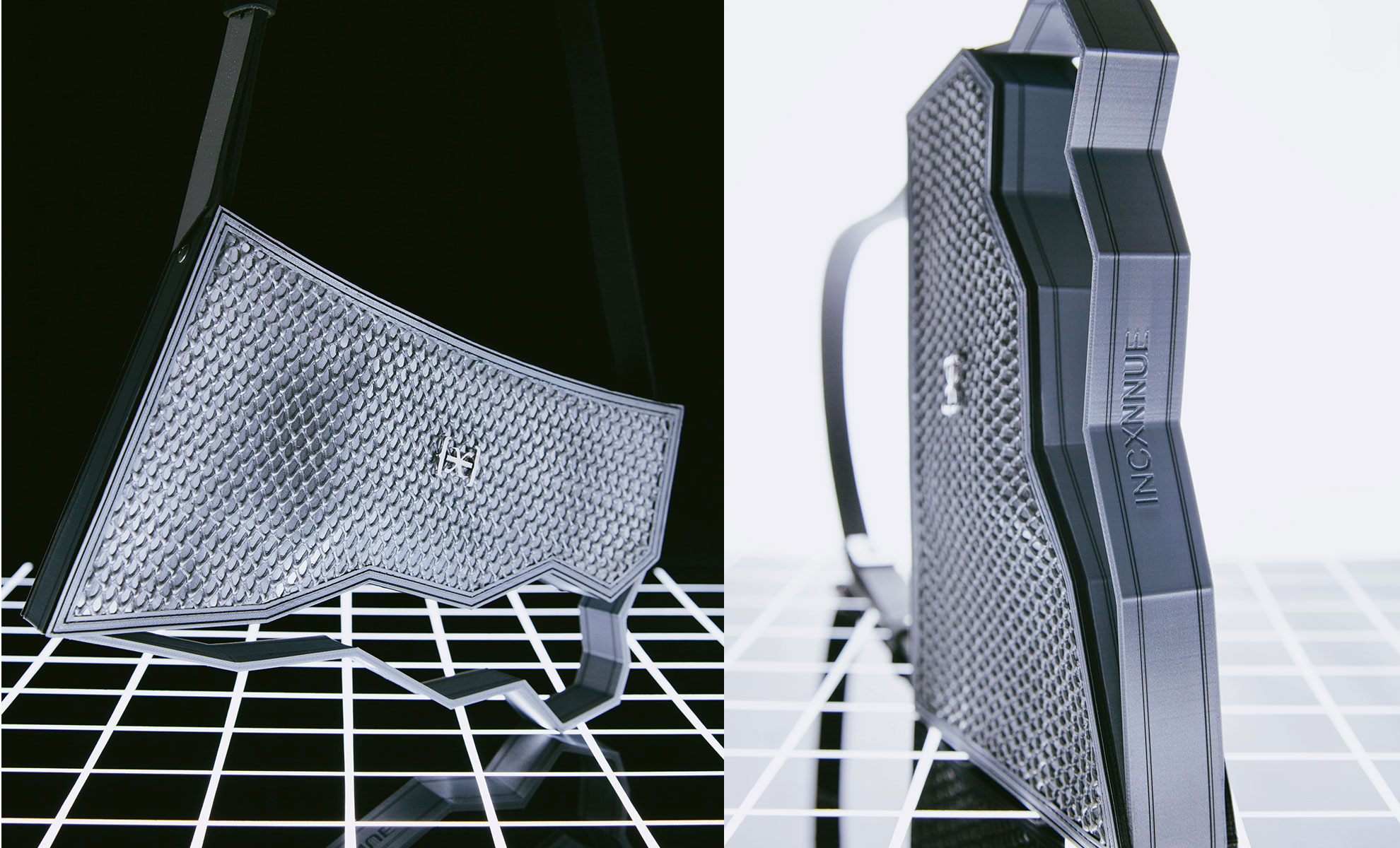
3D printed bag PRYSM Lynxter x Incxnnue
S300X: Advancing Silicone 3D Printing with Support
Lynxter introduces the groundbreaking S300X, a cutting-edge 3D printing machine.
Powered by the innovative IDEX (Independent Dual Extruder) technology,the S300X has the capability to print medical and industrial-grade silicones and polyurethanes, offering support for the production of intricately designed parts.
The S300X contributes to accelerating innovation of elastomers 3D printing . Paired with the water-soluble hydro-support SUP-001, it enables users to explore complex geometries. With the S300X, Lynxter aims to advance silicone 3D printing by opening up new possibilities and fostering progress in this field.
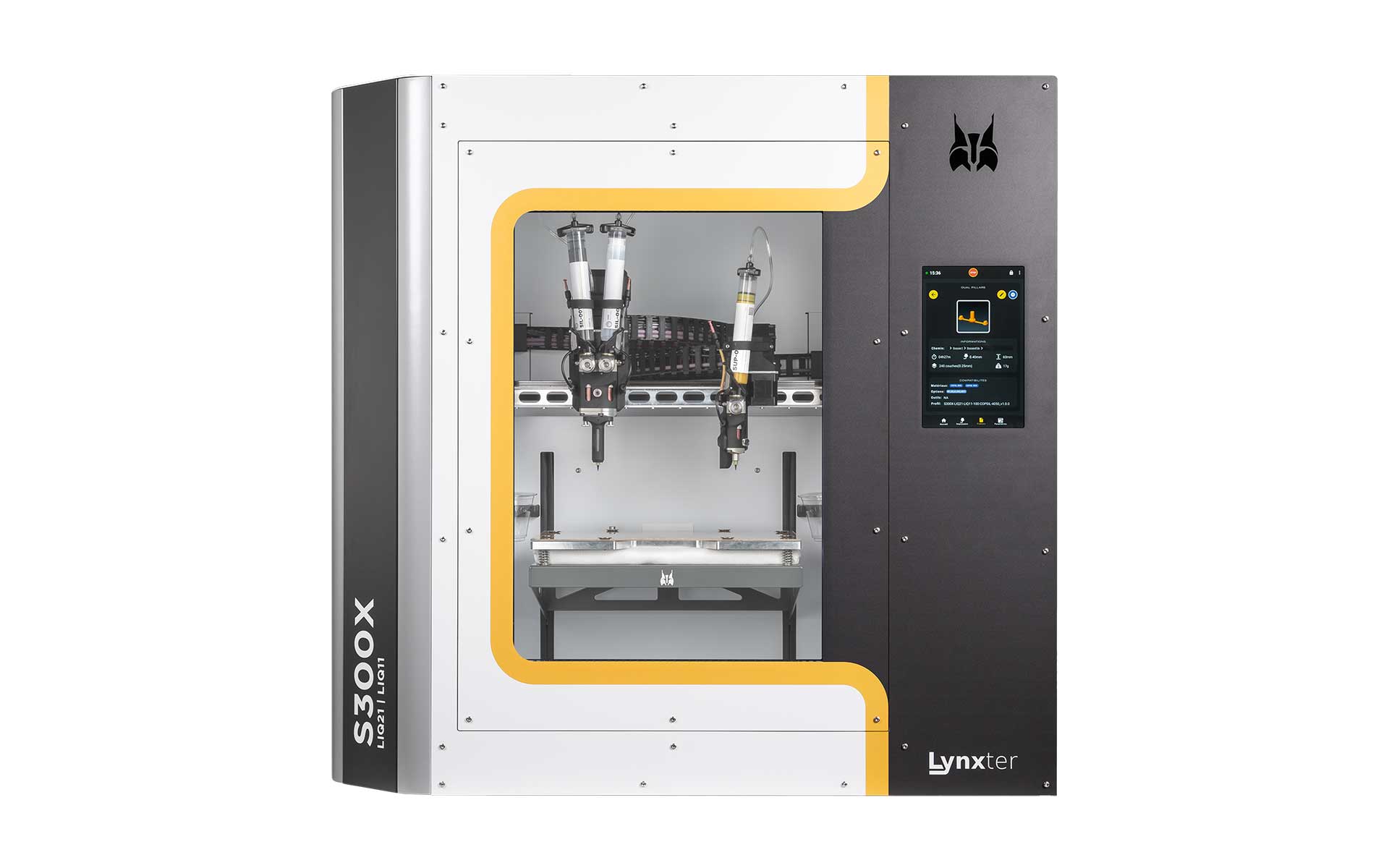
S300X – LIQ21 | LIQ11 – Polyurethane and silicone 3D Printer
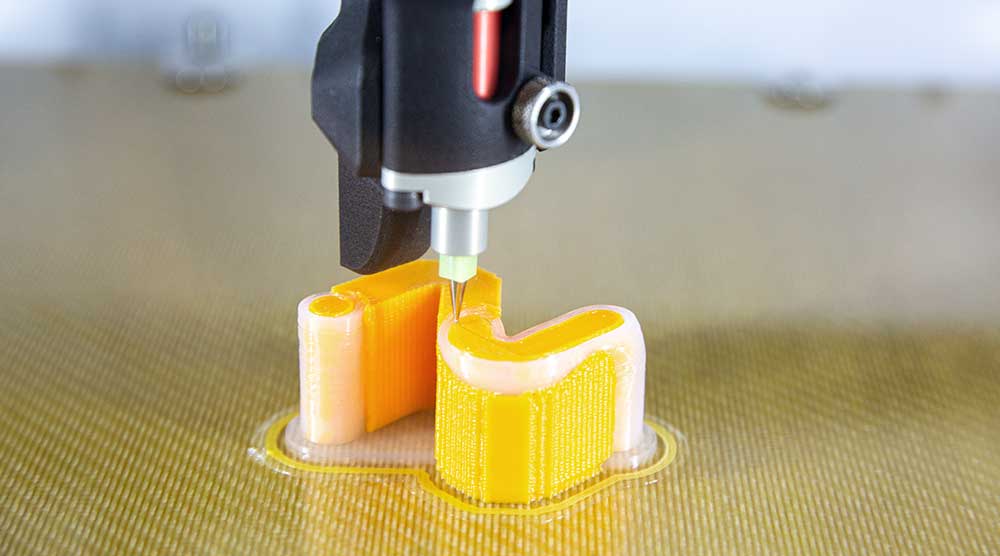
3D Printing a complex-shaped silicone part with support using IDEX technology
With its additive manufacturing technology using liquid silicone deposition, Lynxter is opening up the field of possible geometries and applications. The objective is to further expand the range of printable silicones and materials, to diversify packaging sizes and to continue to push the limits of this technology.
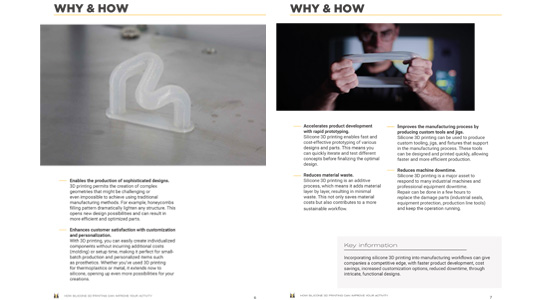
DOWNLOAD THE WHITE PAPER
Download now “Improve your workflow with silicone 3D printing”.
Discover how this new technology can enhance your productivity and innovation.
Don’t miss this opportunity to gain a new competitive advantage.
You should read
ADVANTAGES OF 3D PRINTED SILICONE FOR SOFT ROBOTICS
A NEW MAJOR BREAKTHROUGH IN ORTHOPEDICS: 3D PRINTING OF TAILORED SILICONE LINERS
HOW TO REDUCE THE WEIGHT OF METAL PARTS BY 70% WITH 3D PRINTING