SURFACE TREATMENT AND 3D PRINTING –PRINTING SILICONE MASKS FOR PLASMA PROJECTION
Learn how silicone 3D printing can be a new solution in the masking stage of surface treatment. Together, the company APS Coating Solutions and Lynxter were able to create and test custom silicone printed masking tools under plasma spray conditions.
Read more about this successful collaboration between APS Coating Solutions and Lynxter and its results in our article.

Surface treatment: plasma projection
SURFACE TREATMENT: PLASMA SPRAYING
Plasma spraying is a surface treatment process providing a solution to deposit a coating on all or specific areas of a part. The deposited coating brings new functionalities to the surface and improves its physical, chemical or tribological properties.
This technique is based on the creation of an electric arc in a mixture of “plasma gas”. The plasma, whose temperature can reach 16,000°C, is used to melt a powder stream as it passes through the torch.
Different plasma gases are used such as argon, helium, nitrogen, or hydrogen. The gas mixture and the projection conditions can be adjusted to modify the thermal properties of the plasma as well as the speed of the particles.
The powder flow used depends on the material to be deposited. It can be metals, metal alloys, carbides, oxides, … whose composition and particle size are finely controlled. This one is propelled by a carrier gas in order to be injected in the plasma gas mixture.
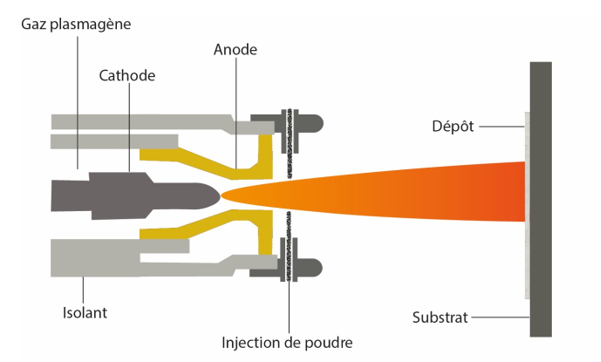
Schematic diagram: plasma projection – Source: APS coatings
Plasma spraying is carried out under atmospheric pressure and is used to reinforce parts intended to be used in extreme conditions.
According to the deposited material, we can obtain the following benefits:
– A better resistance to wear and abrasion.
– A better resistance to high temperatures and oxidation.
– A better resistivity or electrical conductivity.
Coatings obtained by this method are used in many sectors: aerospace, automotive, energy, defense…
APS COATING SOLUTIONS
Founded in 1968, APS COATING SOLUTIONS is a company specialized in the application of drying process coatings.
From prototypes to mass production, APS Coatings develops and applies the most suitable functional coatings to extend the performance of many mechanical parts to any environment.
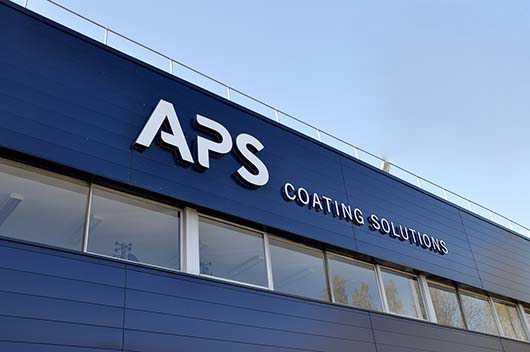
APS Coating Solutions Building, Noisiel
Specialized in the application of coatings by thermal spraying, fluidized dip spin, APS Coatings invests in new surface treatment technologies and continuously modernizes its industrial tool.
It is in this context of innovation that Lynxter and APS Coatings have collaborated to develop silicone 3D printing masking solutions.
TOWARDS NEW MASKING SOLUTIONS WITH 3D SILICONE PRINTING
In April 2022, Lynxter launched a call for projects as part of the development of a new range of materials for additive manufacturing. The call was to select companies using flexible parts (silicone, polyurethane, TPU type) for a trial session for masking, sealing, tooling applications, etc. APS Coatings was one of the selected companies.
After several discussions, Lynxter and APS Coatings identified two cases of masking parts to be printed. These masks will be used for plasma spraying of ceramic on parts for the Aerospace / Defense sector.
For the first case, Lynxter made about 240 masks of 25 mm x 7 mm x 5 mm, which were simply plugged on the areas that needed to be spared.
Silicone 3D printing mask and plasma spraying test
Damien POMAREDE, Materials and Process Engineer at APS Coating Solutions, explains how silicone 3D printing can be an innovative masking solution to accelerate the validation of prototypes or produce small and medium series.
What was your problem, the challenge of the collaboration?
Damien POMAREDE :On this program, we had a relatively complex masking protocol, essentially manual. The execution of the latter requires a great deal of dexterity, attention, and self-control from the operators, with high risks of non-quality.
This operation mode could be suitable for the occasional production of a few prototypes, but it is not compatible with an increase in load and regular production. It was therefore necessary to improve our methods by streamlining this masking stage.
We had already used our SLA 3D printing capabilities to develop a masking solution. However, the specifications of the printed materials were not compatible with the production process.
The objectives of the collaboration with Lynxter were twofold.
• First, we wanted to discover the concept of a multi-material 3D printer developed by Lynxter, and to evaluate the performance of printed silicones. This work is part of a more global reflection carried out by APS Coatings, aiming at identifying the levers for improving our industrial performance. The printing of masks and tools is one of them.
• The second objective was to evaluate the integration of the 3D printer as a tool in our development and production processes and its influence on our organization and operating methods. The impacts in terms of design, manufacturing and testing time, suitability for the need and economic performance were carefully monitored.

3D Printing of 27 parts in silicone in 30 min
Why choose elastomeric 3D printing for plasma spraying?
DP : Today we use a lot of silicone masks to spare parts coated by plasma projection. Our feedback is that some silicone formulations allow us to obtain masks that resist sandblasting and plasma spraying, with a decent durability. This solution also has the advantage of being easily fitted and removed, while guaranteeing a precise delineation and positioning of the masked areas on the parts.
Most of the time, the volumes and the recurrence of the markets totally justify the investment made in the development and manufacturing of this type of masks by more traditional methods with our subcontractors.
In cases where the design of silicone masks, or other types of tooling, is not possible, we must resort to more traditional masking methods, based on the application of adhesive masking tapes adapted to thermal spraying. In this case, the rapid and cost-effective development of a 3D printed silicone masking solution makes perfect sense.
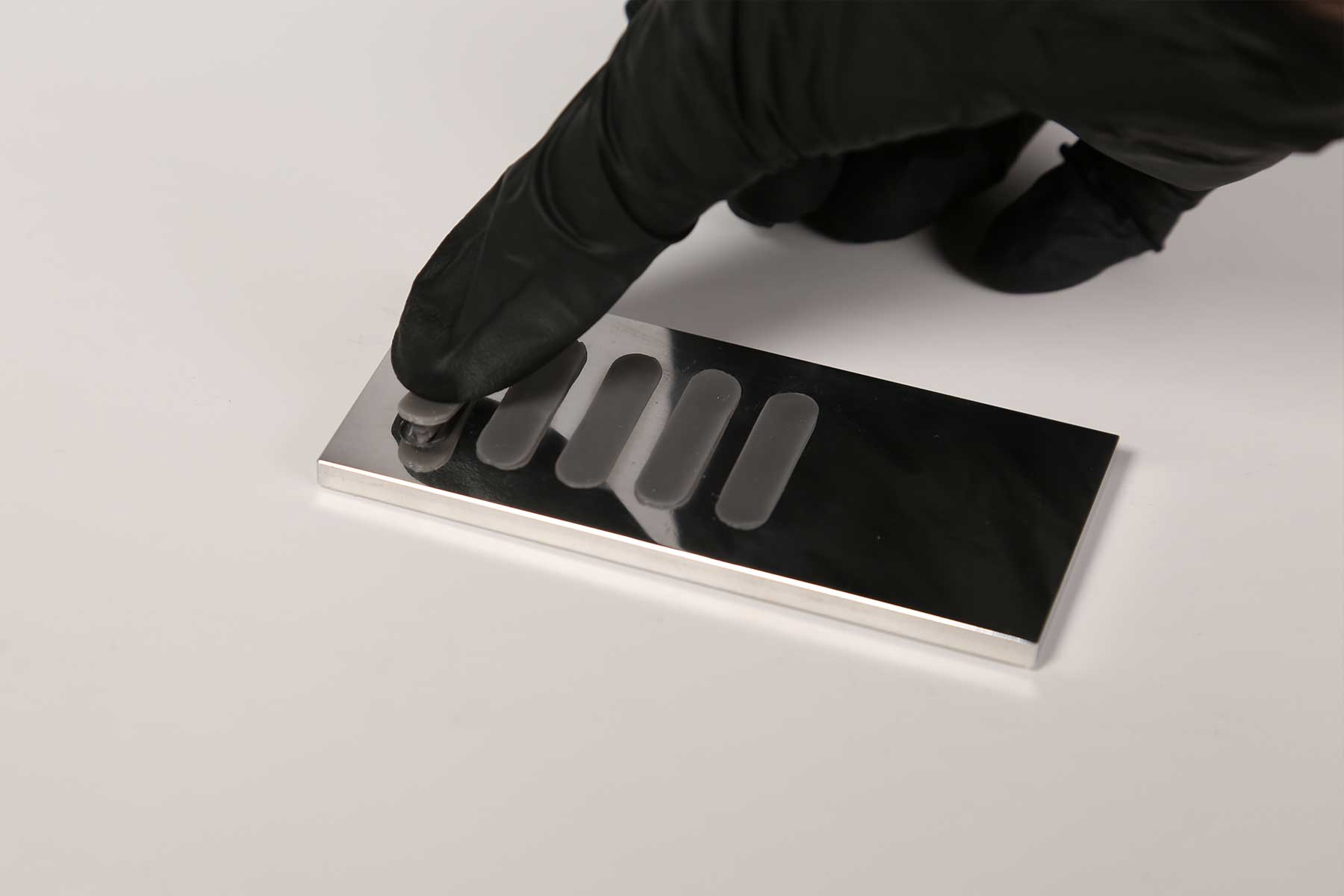
Masking: Application of silicone 3D printed masks
What are the benefits of this new technology in your manufacturing process?
DP : The main gains we identify are of 4 types:
>Reactivity in the design of masking solutions
In-house 3D printing allows us to shorten the time between the development of a design, its manufacture, and its testing in real conditions. Responding faster to our customers’ requests is a real advantage.
>Accuracy of developed masking solutions
3D printing allows us to multiply the feedback loops and thus to respond in a more relevant way to the needs of the application. The use of adapted masks allows us to increase the quality of the finish of the treated parts.
>Adaptation to smaller series
This technology allows us to significantly reduce the investment in manpower and material/service costs when developing our masks and tools. This enables us to consider specific developments, more efficient and effective than masking tapes, for less recurrent or smaller programs. Here again, our ability to excel regardless of the size of the series produced is a major challenge.
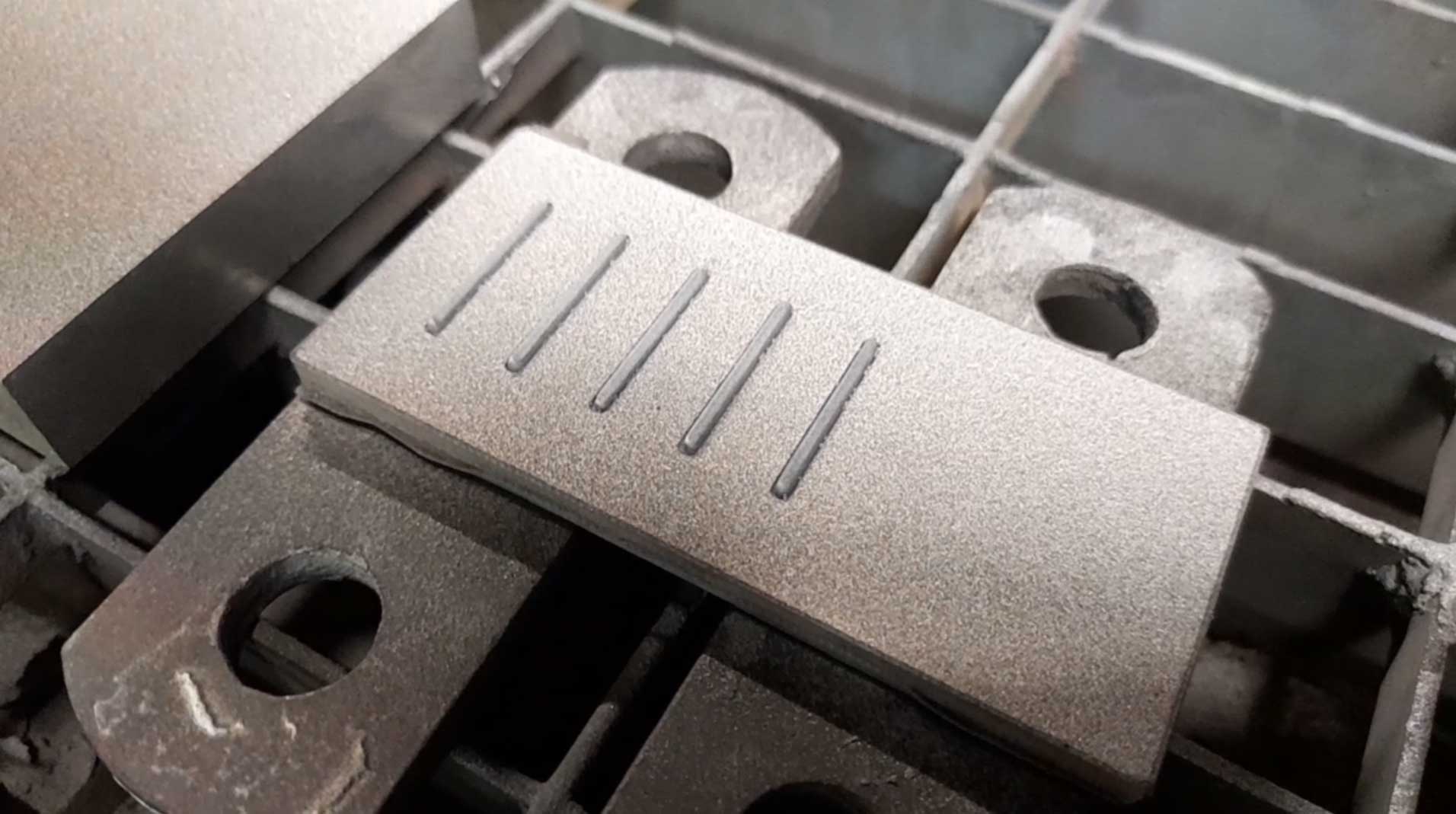
Silicone printed masks after 2 layers of plasma projection
>Securing the value chain
From mask design to manufacturing and, by extension, the production of customer parts, the integration of this technology allows us to consolidate our know-how and to control our costs and lead times much more precisely than the traditional model, based on subcontracting.
The challenge for APS Coatings is to reinforce the confidence of its customers by integrating a production capacity of masks adapted to each geometry.
Is this solution viable for integration as a masking solution in the surface treatment and coating sector?
DP : Our first observations are positive.The parts produced with the masks have all passed all our quality controls. The masks have withstood at least two spraying cycles without losing their function and have provided effective delineation of the coated areas.
In some cases, it will be necessary to fulfill some regulatory requirements to qualify the silicone formulation used. This work is underway at APS Coatings.
Finally, the productivity of the 3D printer seems to be compatible with our needs since it has been demonstrated that the number of masks required to produce a batch could be printed in about ten hours.

Silicone printed masking tools in place before and after plasma spraying.
SUMMARY OF THE MASKING OPERATION WITH 3D PRINTING
TREATMENT USED | Plasma spraying |
TEMPERATURES | Particles are projected at a temperature higher than 2000°C. Plasma temperature : < 16 000°C |
MASKING / UNMASKING TIME | The masking time of the area under study is divided by 2 |
DEBURRING TIME | The deburring time of the area under study is divided by 2 |
RESISTANCE DURING TREATMENT has the part moved? | No dislodging of the mask during the projection. A point of vigilance lies in the proper placement of the mask in its position. This point can be addressed by informing the operators and/or improving the design of the mask. |
REACTION WITH THE TREATMENT | Good resistance of the masks after 2 cycles. Slight abrasion of the mask in the exposed areas |
RESIDUE OR CASTINGS ON THE PIECE | No liquid or gas transfer observed on the masked part. |
SUMMARY OF THE 3D PRINTING OPERATION
SECTOR | Industrial – Aeronautics, Space, Defense/td> |
APPLICATION | Mask for plasma projection of a metal oxide |
MATERIALS | Silicone RTV2 |
DIMENSIONS | 25 mm x 7 mm x 5 mm |
PRINTING TECHNOLOGY | S600D, S300X printer in LIQ21 |
PRINT TIME | 10 h / 240 parts |
MATERIAL QUANTITY | 84 gr |
MATERIAL COST | 24,4€ |
LAYER HEIGHT | 0.35 mm |
NOZZLE SIZE | 0.69 mm |
PRODUCTION VOLUME | Series of 240 parts |
These tests validate to the following findings:
– Simplified and optimized procedures for the preparation and application of specific masks.
– Efficient delimitation of areas that are difficult to spare.
– Easier deburring operations and improved finishing quality.
– The masks are resistant to the spray flow and can be reused for at least two cycles.

Masks after zero, one and two plasma spray cycles.
To expand its study on surface treatment masking solutions, Lynxter continues to produce larger and more complex parts with the S600D and S300X on dry surface treatments such as powder coating.
This new solution empowers for rapid production of custom masks that can be reused and adapted to any shape of part to be treated.
Most importantly, silicone 3D printing brings a gain in efficiency during the masking stage and significantly reduces a complex operation.
Want to lean more about this matter ? Contact our team.