SURFACE TREATMENT AND 3D PRINTING – PRINTING SILICONE MASKS FOR POWDER COATING
Learn how silicone 3D printing provides a new solution to the masking stage of metal surface treatment.
Customized, reusable silicone masks replace masking tape and save time and money for the operator.
SURFACE TREATMENT
Post-treatment is one of the final steps in the manufacturing process of a part. In industry, it consists of carrying out one or more operations to finalize the surface condition of a part: the objective is to improve the appearance or function of the surface to adapt it to the requirements of specific uses.
Many of these operations are grouped in the “surface treatments” family.
Industrial reconditioning companies or surface treatment specialists use these processes every day. Surface treatment processes are an important and advantageous step in the manufacturing cycle of a product for many sectors such as aeronautics, chemicals, energy, electronics and medical.
Within these sectors, different categories of post-treatment can be distinguished. Mechanical, chemical, and thermal post-treatment, finishing (paint, varnish, etc.)
In aeronautics a machined aluminum part may undergo the following treatments: degreasing > shot blasting > dye penetrant testing (non-destructive testing) > OAC – chromic anodic oxidation > primer > finishing.
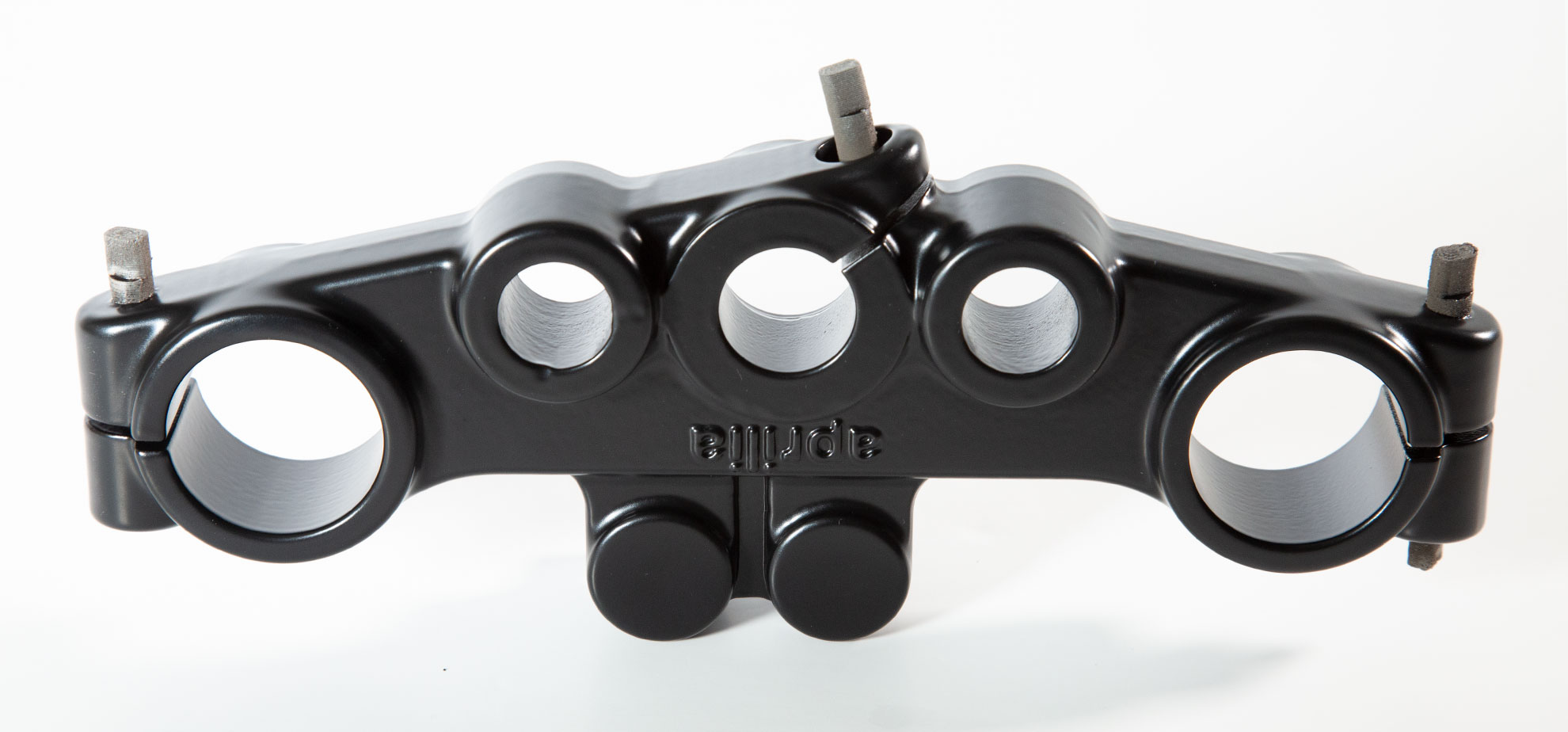
Fork clamp with treatment surface mask printed in 3D (in grey)
While considering the safety, quality, costs and deadlines of the operations, the mission of a surface treatment operator consists of preparing the part and carrying out the necessary actions (shot blasting, sand blasting, technical coatings, etc.) in compliance with precise specifications.
In almost all cases, certain areas of the part must be spared, i.e., not undergo any surface treatment. Masking operations (areas to be masked) are therefore an important issue in terms of complexity of shapes, time, and resources for the operators.
Once the part went through each stage of the surface treatment process, it is checked to validate its conformity.
3D printing provides a unique and economical solution to the problems of post-processing on parts with complex geometry. It allows the production of customized masks for both small and medium-sized series.
HOW DOES 3D SILICONE PRINTING ADDRESS THE CASE OF POWDER COATING?
One of the most common surface treatments of metals is painting.
Industrial paint can be applied in liquid, powder form or by cataphoresis. The choice of the process depends on the material, the shape of the part and its conditions of use after treatment.
Lynxter was involved in a renovation project on a 1989 Aprilia ETX 350 motorbike which included a powder coating process: the paint is sprayed as a statically charged powder which is applied to the surface of the part. After being covered with powder, the part is put in an oven at 200°C to polymerize and fix the paint. This paint treatment is suitable for motor vehicles to limit corrosion and impact marks.
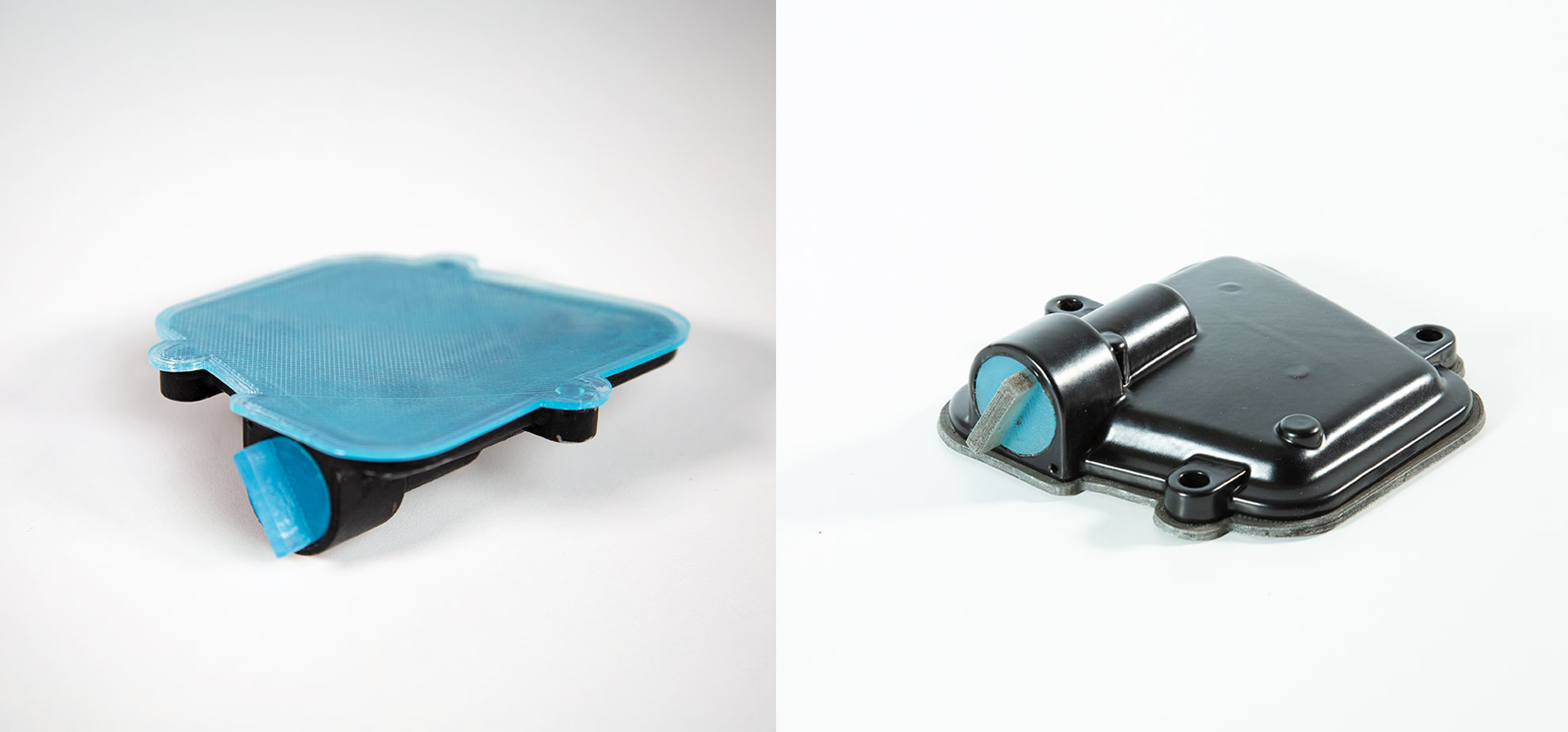
Engine head valve cover with decompressor fitting and 3D printed coating mask (in blue)
The bike was completely disassembled. Each part had to be sandblasted to remove rust and paint before being powder coated.
Facing a unique case like this, the spares and masking are done manually using masking tape, for example. This manual step can be time consuming and can be a pain for the surface treatment agent. Lynxter has therefore created various masking and sparing tools to be fitted to the motorbike pieces.
However, sandblasting and powder coating are aggressive treatments that can cause a reaction with the substrate (abrasive particles that bounce back, exudates), so it is necessary to choose a material that is flexible, inert, and chemically resistant.
The parts are placed in an oven with temperatures of up to 200°C to be polymerized. The material must be then able to withstand high temperatures. It becomes obvious that masking and sparing parts must be printed in silicone.
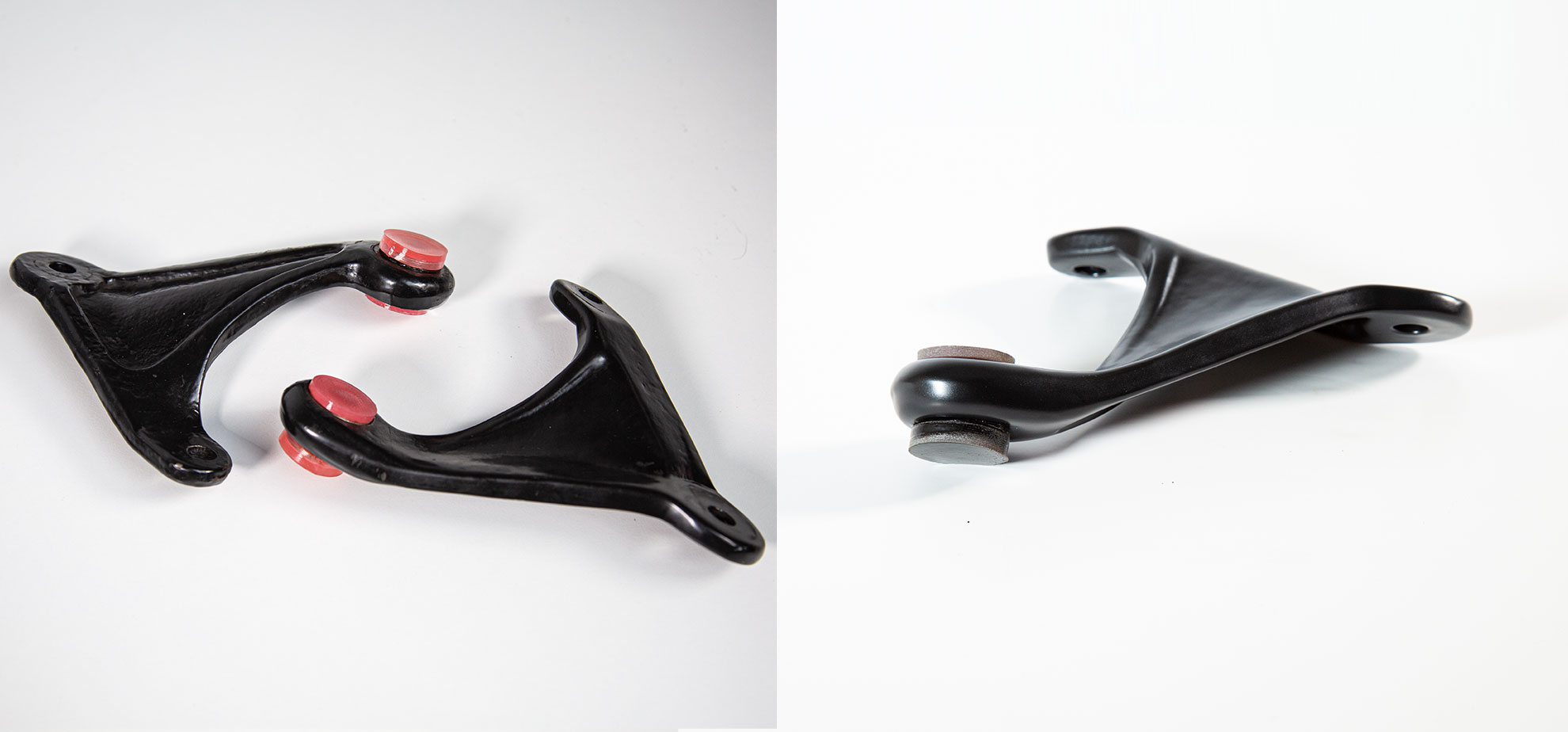
Rear linkage suspension with 3D printed coating masks (in red)
Lynxter chose the driest industrial grade silicone possible to deal with any wettability issues. After some testing, the parts were printed in SIL-001 – 45 ShA industrial silicone using the LIQ21 pump, which is now available on the S300X silicone 3D printer and the S600D modular 3D printer.
Results
– The treated parts underwent each step without incident. All silicone parts held their position and did not move during the surface treatment.
– The masked areas are free of paint and abrasion from sandblasting and powder coating.
– The silicone parts show evidence of the treatments imposed but are not damaged and can be used again. The reuse of these masking parts promotes repeatability of the operation and potentially saves time and manual intervention.
– No deburring is required after the removal of the masking tooling.
– Masking and de-masking time is reduced.
SECTOR | Machinery and transportation |
APPLICATION | Powder paint masking |
MATERIAL | Silicone RTV2 |
DIMENSIONS | Small/td> |
PRINTING TECHNOLOGY | LIQ21 (S600D, S300X 3D Printer) |
PRINTING TIME | Av. 7 min / part |
MATERIAL QUANTITY | Av. 10gr / part |
MATERIAL COST | Av. 3€/ part |
LAYER HEIGHT | 0.30 mm |
NOZZLE SIZE | 0.69 mm |
PRODUCTION VOLUME | Unitary |
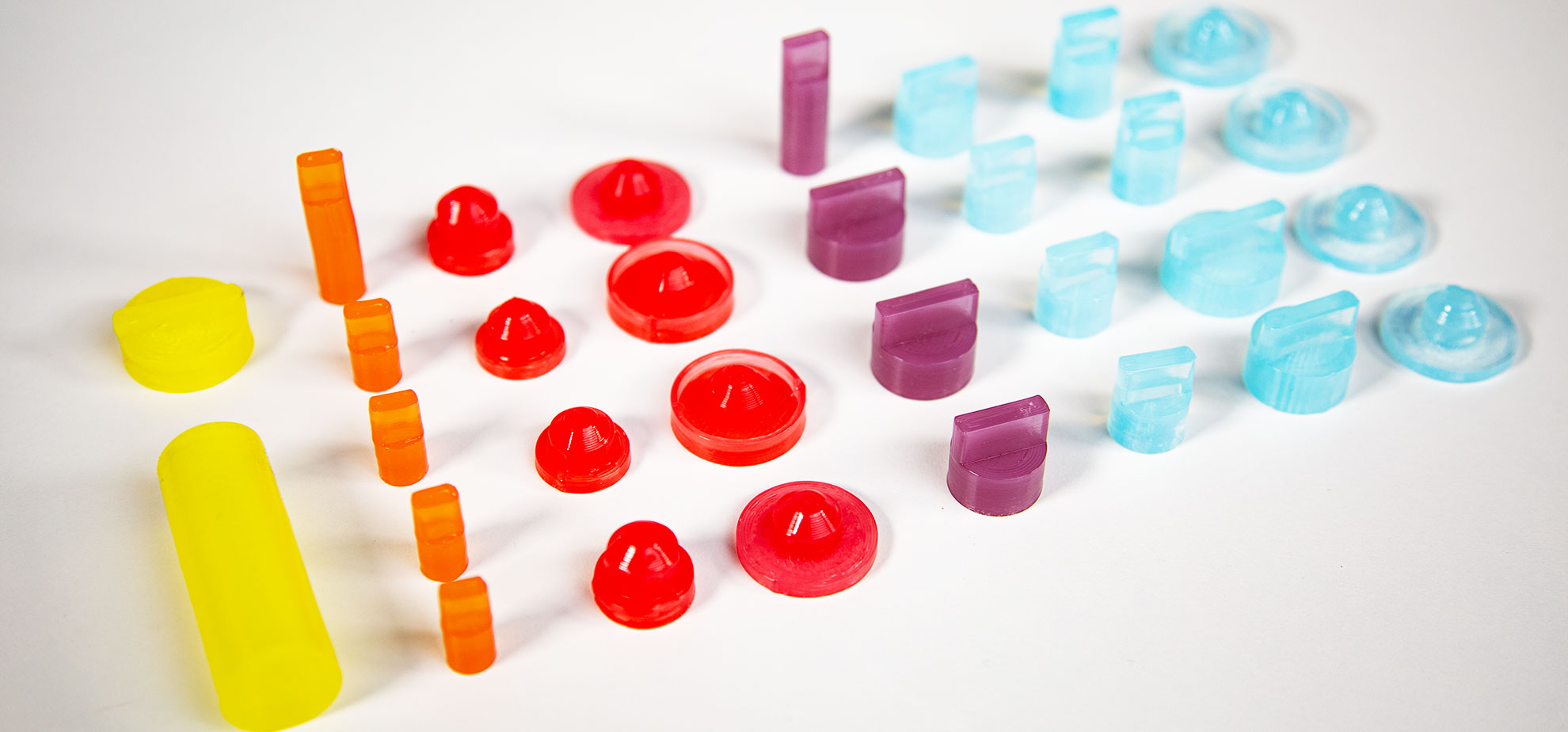
Masks plugs and different covers printed in 3D
CAN WE USE 3D PRINTING FOR ALL TYPES OF SURFACE TREATMENT?
From thermal and thermochemical treatments to surface engineering, it seems clear that additive manufacturing is on its way to provide new solutions to the sector.
Liquid 3D printing can make a customized masking part in its shape, but also in its intrinsic properties: by selecting the right material (silicone, TPU, PU) and the right hardness, the printed part can withstand a wide variety of exposures and processes.
We will see, in a coming article, how the choice of TPU 3D printing can respond to more aggressive surface treatments such as shot blasting.
.