HOW SILICONE 3D PRINTING KEPT A PRODUCTION LINE RUNNING
Learn how Lynxter helped SAPRENA to keep its production line up and running, avoiding operational overheads.
How 3D Printing can help business
SAPRENA is an inclusive company that combines economic performance and social wealth. For more than 30 years, its mission has been to create sustainable jobs for all, with priority given to people with disabilities.
For several decades, SAPRENA has developed recognized know-how in its various areas of expertise: services (cleaning and green spaces), industrial services (packaging and logistics), and catering services.
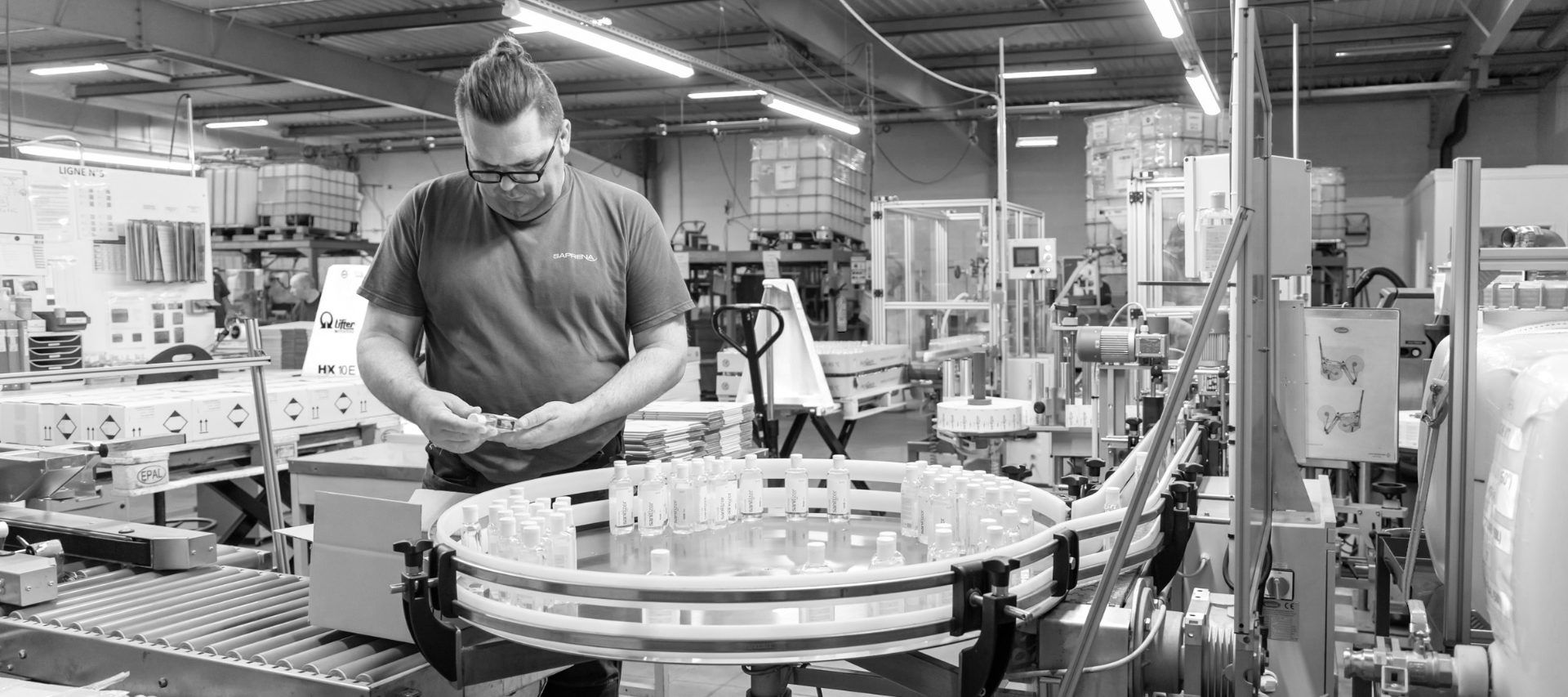
Production line at Saprena – Sources: Saprena
In June 2022, SAPRENA started the first production of a new format of detergent container on one of its packaging lines. It appeared that the existing cap screwer was not working optimally on these new smooth: its “jaws” were wearing out very quickly. To avoid the wear and tear, SAPRENA was proactive and called on Lynxter to develop a permanent solution to replace its worn jaws.
This emergency replacement had to be done as quickly as possible to maintain the production rate and to remove any risk of delay which would lead to additional costs such as :
– Shipping deliveries in 2 stages with an extra cost of €400.
– Cost per hour of non-operation of the line of €100.
Every hour of downtime takes a heavy toll on the company and its employees.
Use of the 3D silicone “jaws” on the line
How silicone 3D printing provided the solution
The part to be repaired is a detergent bottle cap screwing tool. It consists of three parts made of a soft, non-slip material that represents the tool’s clamping “jaw”.
SAPRENA’s current supplier was unable to meet the very tight deadlines requested at that time. This solution was incompatible with SAPRENA’s production and customer commitments.
SAPRENA then turned to Lynxter and liquid 3D printing solutions to produce and replace the current parts that were unsuitable for the new plugs and were at the end of their useful life: non-slip jaws to be integrated into the “screwing machine”.
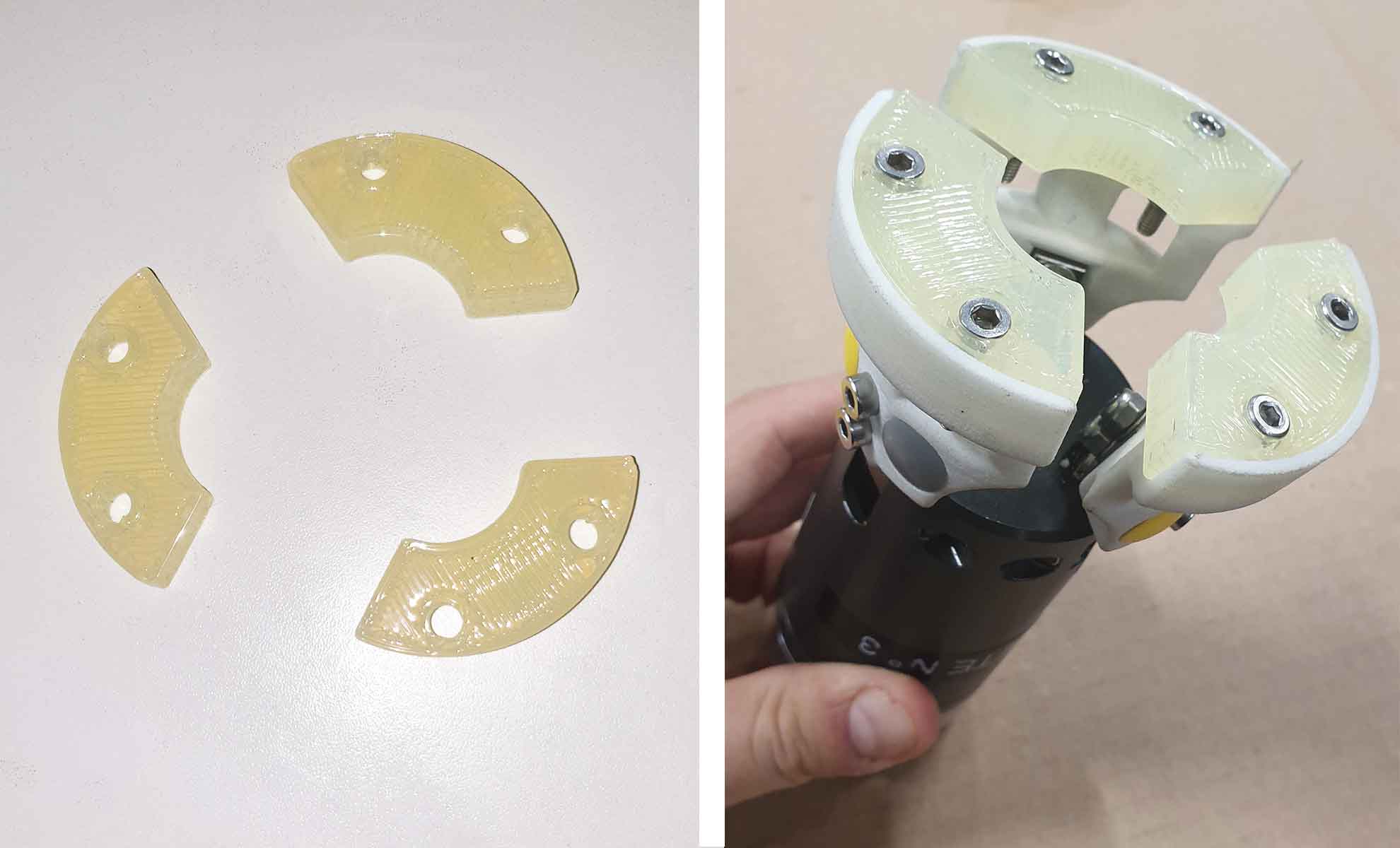
Printed silicone jaws – Clamp for lid screwing machine
The choice of material for the jaws had to be suitable for a small production run without causing excessive wear above 500 cycles.
SAPRENA provided Lynxter with the desired hardnesses and STL files of the jaws. Lynxter choose a RTV2 40Sh industrial grade silicone to print the new jaws. This silicone has good strength and durability while providing the required hardness demand.
The parts were rushed to the site to be set up and tested directly on the production line.
After its installation on the line, the result was very conclusive, and SAPRENA was able to proceed with the validation of the new jaws.
Lynxter enabled SAPRENA to maintain production by printing non-slip silicone grips in less than 72 hours.
By using 3D printing, SAPRENA has been very reactive and has avoided delivery delays and production overruns by quickly replacing worn parts using 3D printing.
Completed in June 2022, the parts are still in place on the production line and have been used to produce the packaging of more than 20,000 containers to date.
This experience has also enabled SAPRENA to see the qualities of industrial silicone (resistance, hardness, durability) and its benefits to minimize the wear and tear of certain production tools. 3D silicone printing is a long-lasting solution that increases the lifespan of wear parts.
This case perfectly illustrates how adopting 3D printing offers a new autonomy, increases quality, saves time and consequently brings an economic gain in the replacement of parts and in the production of functional rapid prototypes.
3D PRINTING SUMMARY
SECTOR | Industrial |
APPLICATION | Clamp for cap screwing machine |
MATERIALS | Silicone RTV2 40ShA |
DIMENSIONS | 3 x 60mm x 90mm x 15mm |
3D PRINTING TECHNOLOGY | S600D, S300X 3D Printer with LIQ21 |
3D Printing time | 2h30 |
QUANTITY | 36g |
COST | 6,93€ |
LAYER HEIGHT | 0.48 mm |
NOZZLE SIZE | 0.69 mm |
PRODUCTION VOLUME | unit |
Want to learn more about this matter ? Contact our team.