SURFACE TREATMENT AND 3D PRINTING – PRINTING MASKS FOR SHOT PEENING
Following our article on using silicone 3D printing to create masking and sparing parts for paint treatment, Lynxter has this time looked at mechanical surface treatments.
More abrasive than paint, Lynxter tested different materials in shot peening conditions to find the right combination of printed material and surface treatment.
TPU printed mask kit for shot blasting in the aerospace industry
MECHANICAL SURFACE TREATMENT PROCESSES
Shot peening, sandblasting, microblasting
There are a multitude of mechanical surface treatments, but three are mainly used:
– Shot peening: This process consists of projecting metal shot, a type of small grain, ball or metal particle onto the surface of an object to improve the external appearance of the part. This surface treatment provides compression for durability (additional protection against fatigue, corrosion, cracking) while strengthening the mechanical properties of the part on the surface. They are also used to clean parts of any contamination (rust, dust, paint, coatings, etc.).
– Sandblasting: This process consists of projecting sand at high speed onto an object. It is mainly used to clean the part of impurities or traces of paint, it also brings a roughness which allows a better adhesion of coatings or paints carried out thereafter.
– Microblasting: Like shot blasting, this process consists of projecting glass or ceramic microbeads onto an object. It allows the part to be cleaned and stripped, but this time with more gentleness adapted to fragile parts and surfaces.
All these operations frequently target specific areas of an object and require blanking or masking tools in order to spare the areas that are not to be treated. These tools are usually made of a flexible material that can conform to curved shapes and can absorb impacts
Shot peening operation and masking test result of the TPU printed part
HOW DOES 3D PRINTING OF SOFT MATERIALS ADDRESS SURFACE TREATMENT NEEDS?
Testing 3D printing in context
LYNXTER wanted to study the efficiency and benefits of additive manufacturing for the post-treatment of a machined part.
The objective was to produce 3 masking tools that would perfectly fit a gear type geometry.
The design of the tooling could be done quickly by 1 industrial designer (about 2 hours of design) and the printing of the 3 parts could be launched in masked time (about 8 hours) on the S600D and the FIL21 toolhead.
To date, the operators make these tools by conventional turning from thermoplastic bars (POM, Ertalon type, etc.). This requires a dedicated and qualified resource, as well as having material in stock. In addition, the process does not allow for all types of geometry.
In other cases, they have to call on subcontractors with lead times of several weeks. This is restrictive.
The integration of 3D printing simplifies the implementation and reduces the masking time. This greatly relieves an operator’s job that is perceived as difficult.
Thus, we were able to develop a fast tooling system that met the need perfectly.
Parameters of the blasting process :
– Type of balls: steel 0.4mm
– Pressure: 30 Psi – 2 Bars
– Duration: 10 seconds
– Average distance between the nozzle and the part: 15cm
Tests were carried out at 60 Psi – 4 Bars for 1 minute (extreme parameters never used) in order to test the abrasion resistance of TPU.
The result validates the use of TPU for these processes:
– Reaction: the TPU coating did not react with the treatment.
– Retention: the part did not move during the treatment.
– Removal: Parts are easily removed and leave no residue.
– Compatibility:
3D printing of TPU and silicone now makes it possible to produce masking parts that are perfectly suited to the post-processing of metal parts.
TPU filament is a flexible, soft and strong 3D printing material. It offers many advantages through its technical properties:
– Good elongation (300 to 580%)
– Hardnesses from 70 to 95 shA
– Good tensile strength
– Good abrasion resistance
– Maximum operating temperature of 80°C
Lynxter’s FIL21 Direct Drive 3D printing toolhead can print soft filaments such as TPU, TPE and TPC.
Inexpensive and easy to print, TPU is an excellent choice for printing masking parts.
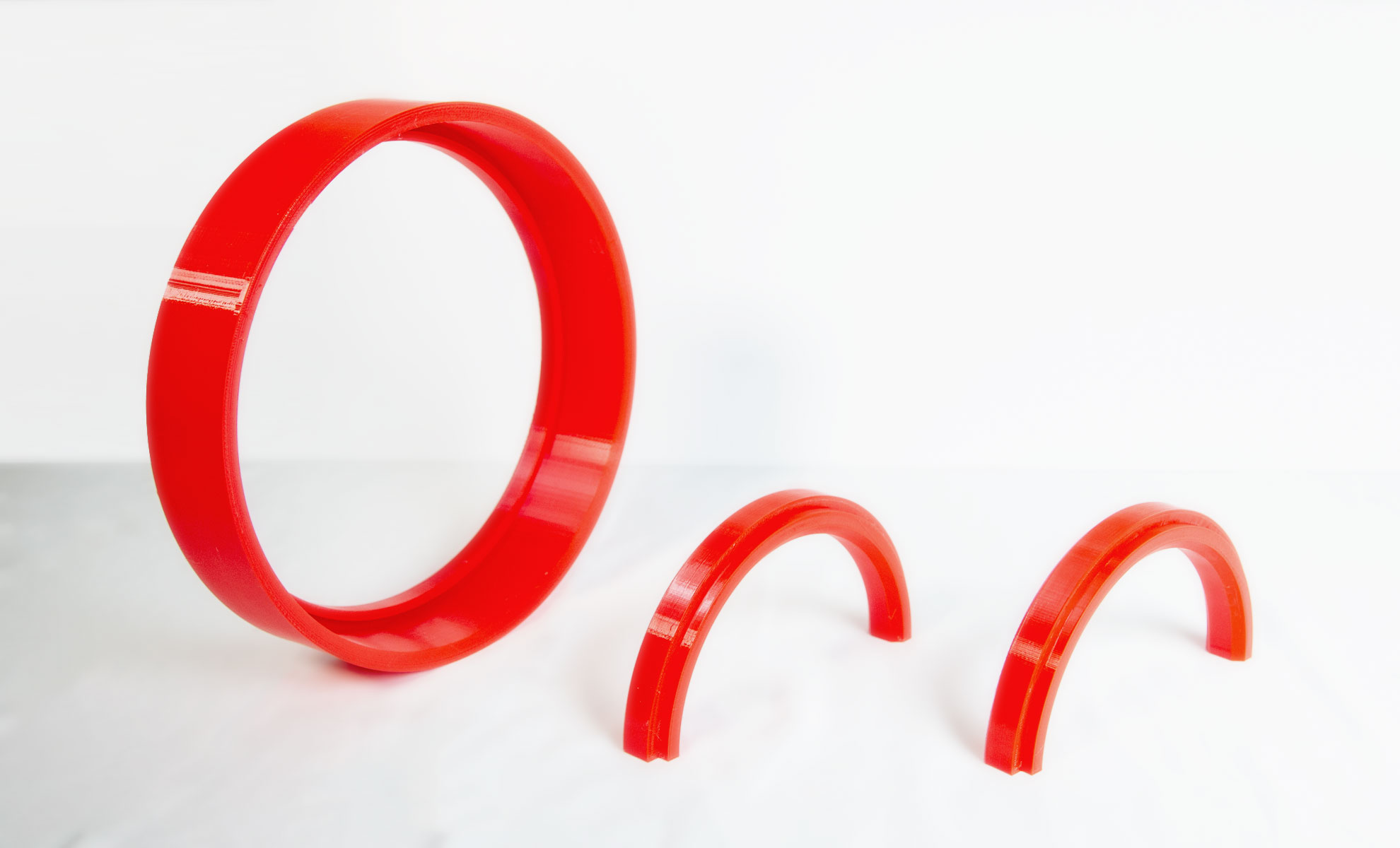
TPU masking piece Ø260 mm x H50 mm for aeronautics
However, chemical post-treatment or paint finishing processes have different constraints: very aggressive and corrosive solvents, high temperature curing, etc. And in these cases, TPU is not the right candidate. However, silicone is capable of meeting all these constraints.
Very few players are currently able to print elastomeric materials. And even less so on material extrusion processes allowing rapid printing and direct use.
Lynxter is a pioneer in liquid 3D printing and offers a 3D printing technology for silicone. With the S600D and S300X professional 3D printers and LIQ11 and LIQ21 silicone toolheads, Lynxter offers the ability to produce silicone parts at lower hardnesses. Like TPU, silicone offers many advantages through its technical properties:
– Excellent elongation (between 300% and 1000%)
– Good chemical resistance
– Temperature resistance: up to 260 °C.
– Hardnesses from 5 shA to 40 shA
The modular 3D printer S600D allows to print on the same machine soft or liquid materials from 5 Shore A to 95 shA, and to answer many industrial masking cases.
The S300X silicone 3D printer can print silicone and polyurethane with a soluble support and thus produce complex geometric shapes.
New materials are being developed to expand this range of materials to provide a new masking solution in extreme conditions.