3D Printing for industrial efficiency
Jigs, fixtures, masking, protection, 3D printing can be used to create specific custom made parts to ease production and handling of industrial machines. TPU filament has very interesting hardness, but also flexibility to make parts that absorb shocks and protect elements between them.
Cost reduction, stronger safety, and improved efficiency, we will present our internal application case of a protective part use in the storage of the 3D printer S600D elements and its printing by the Direct Drive FIL21 toolhead.
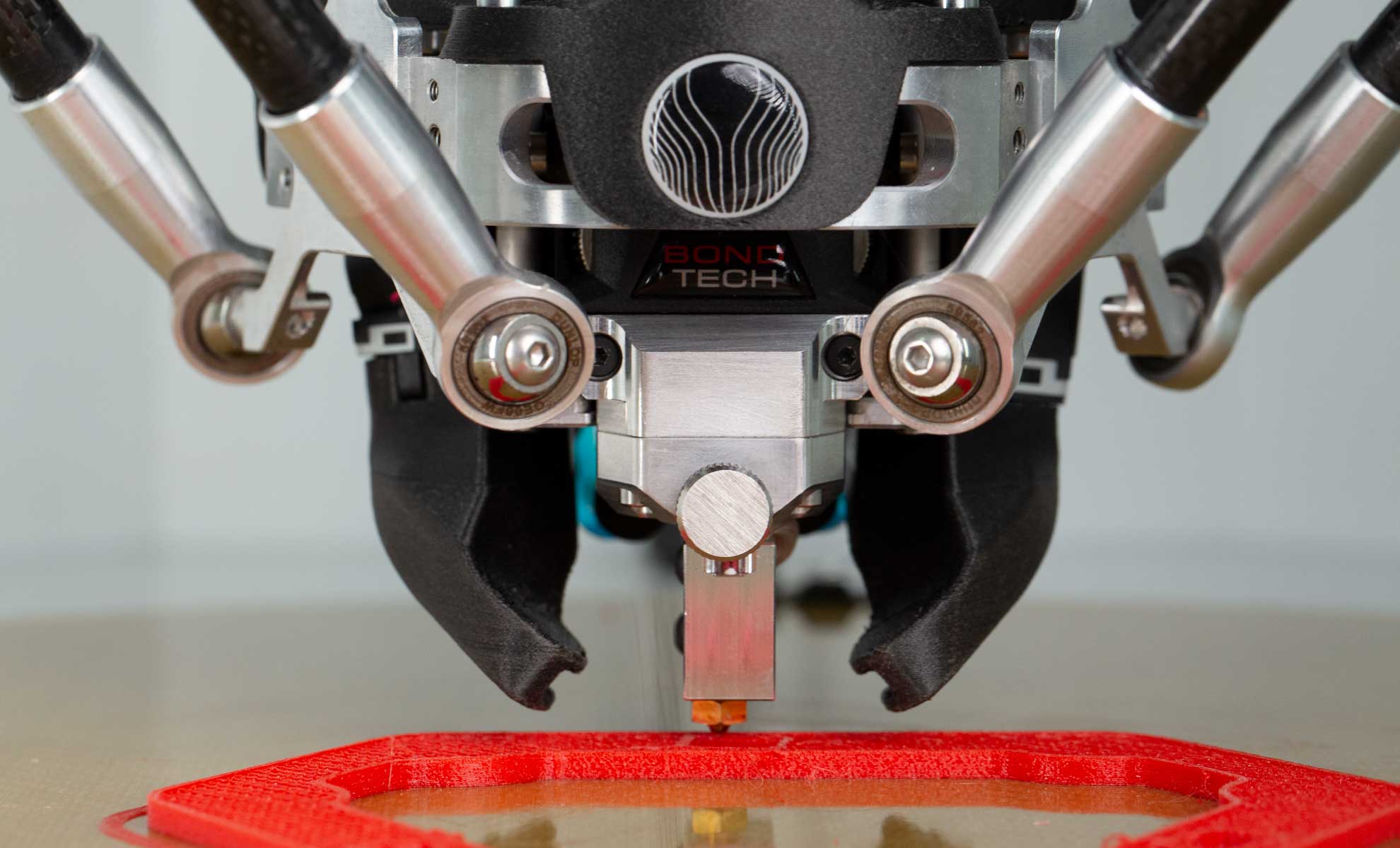
TPU filament printed by the Direct Drive FIL21 toolhead
TPU, ANTI-SHOCK MATERIAL
TPU or Thermoplastic Polyurethanes are thermoplastic copolymers that combine elastomeric and thermoplastic properties. This dual identity offers remarkable performances such as
– Abrasion resistance
– Shock absorption
– Tear resistance
– Flexibility
Recyclable, TPU is a material suitable for 3D printing of flexible and resistant prototypes. Its flexibility and robustness are real assets for making outer soles, sports equipment (masks, fins, protection), medical equipment (prostheses) or automotive components (air filters, ducts, pipes) as some examples.
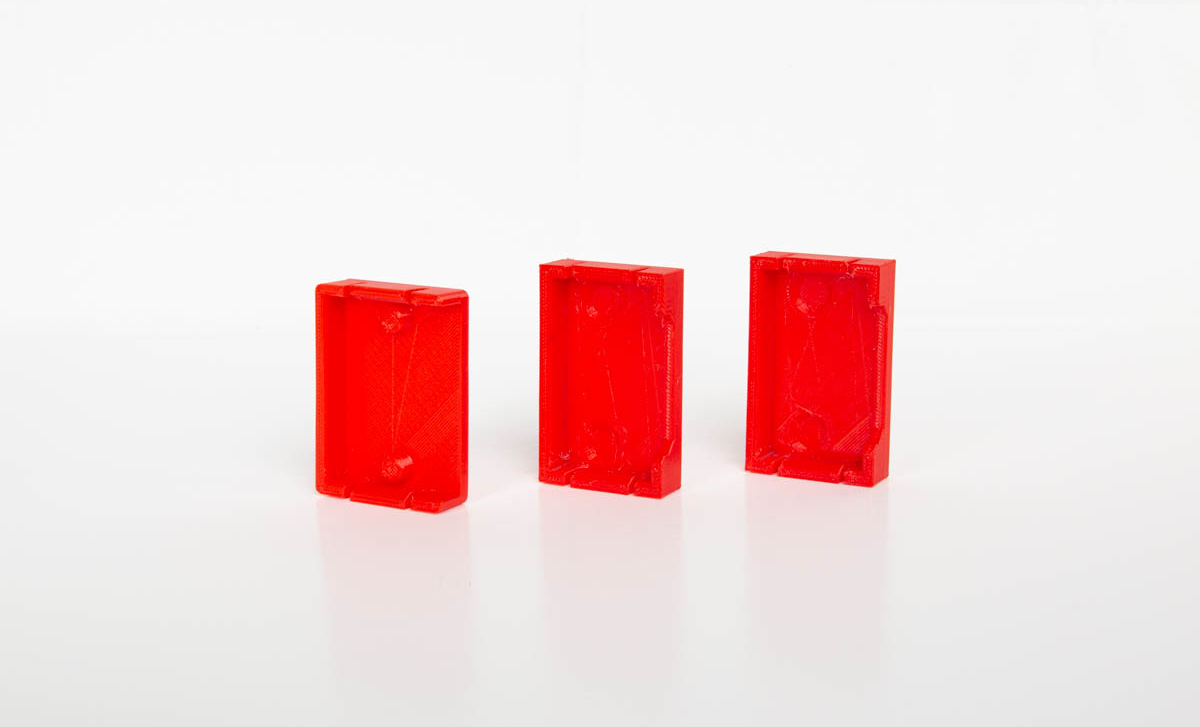
TPU printed machine storage protective part
3D PRINTING OF FLEXIBLE FILAMENTS
As TPU is very flexible, it can sometimes be complex to print.
Simple Bowden system printing cannot handle soft filaments, which can be difficult to push through the tube and therefore difficult to extrude evenly. To overcome these difficulties, Lynxter has designed a new FIL21 direct drive toolhead. The extruder motor is placed directly above the heating block on the print head and drives the flexible filament. By eliminating the distance between the motor and the nozzle, the risk of friction, congestion and filament elongation is radically reduced. This allows for clean and precise printing of the TPU.
Printing prototypes with TPU enable the testing of flexible and strong models with different hardness ranging from 75shA to 95shA. 3D printing can then:
– Reduce costs by eliminating the need for storage space for spare parts with printing on demand as required. Digital inventory replaces physical inventory.
– Reduce production times: forget about minimum parts for orders and long delivery times. 3D printing produces small series of parts within a few hours, eliminating supply difficulties.
– Flexibility and efficiency: parts can be made quickly, their design adjusted quickly and iterated until a final part is obtained. TPU is adaptable in many situations and is very useful for creating custom tooling.
APPLICATION CASE: INDUSTRIAL PROTECTIVE PART
Industrial 3D printing can therefore provide a quick solution to a new situation.
During the production of the industrial 3D printer S600D and the storage of the various assembled parts, the production team wanted to optimize the space by stacking certain machine parts. However, these parts could be damaged by each other (aluminum element on aspect parts) causing various scratches or scuffs. Therefore, the Design Office designed a protective part that would avoid these marks: it had to be flexible and able to absorb the weight of the parts. The choice was made on TPU.
Timelapse and use of the TPU storage cover part
The part needed to be produced in small quantities, so 3D printing was the most suitable solution. Several iterations were made to end on rapid optimization of the final part. Printed in 1 hour and made from TPU 95shA, this part does not require any post-processing and can be fitted directly after printing: it protects the S600D’s trim parts from scratches during storage.
The team also made a part to protect the tool holder of the S600D. The objective is to avoid any scratches on the ball joints of the 3D printing plate during the assembly of the machine. This same part has been designed to have two functions, it can also be used to fit the tool holder parts together without causing any further damage or scratches.
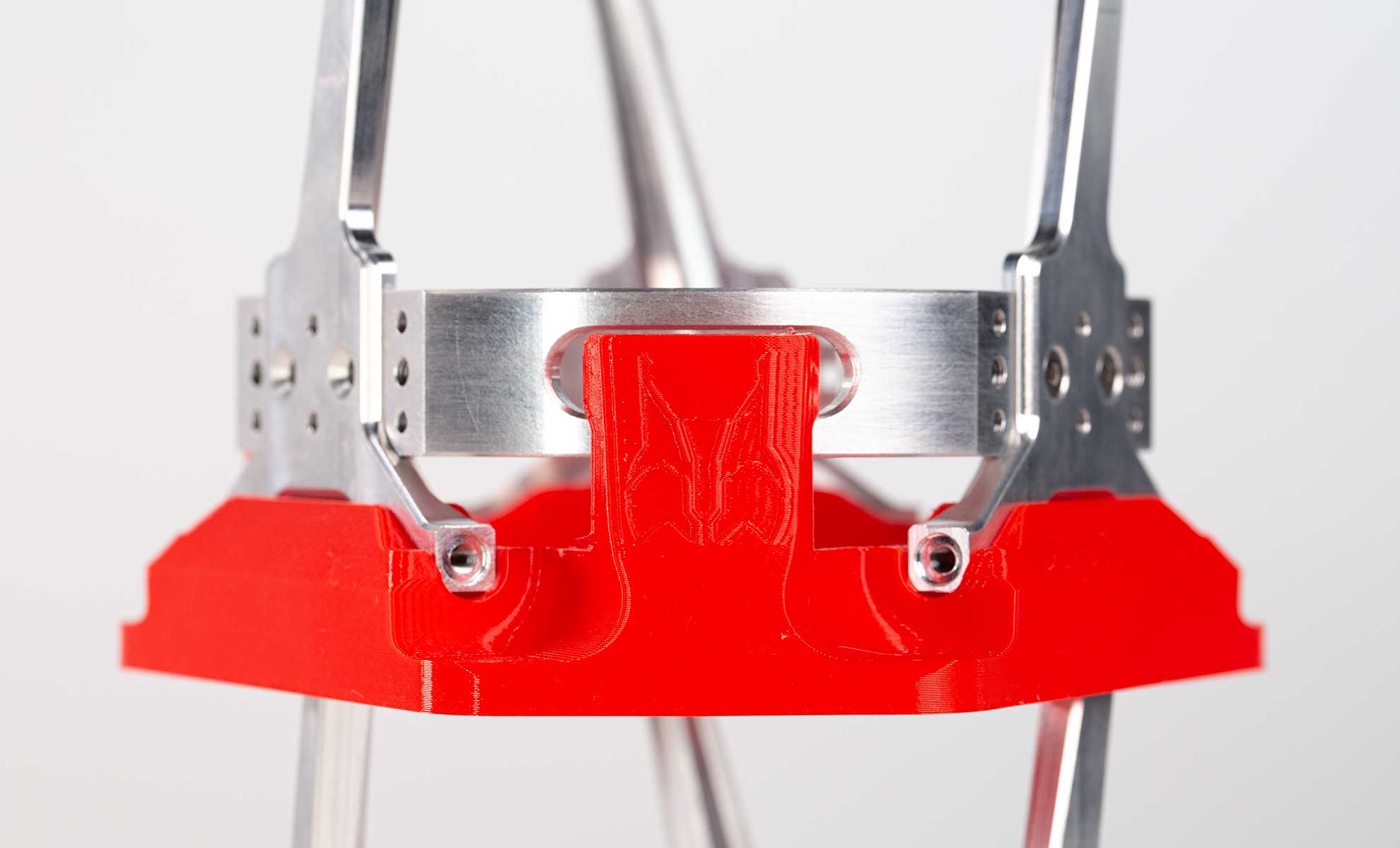
S600D tool holder protection piece in TPU
Thanks to the flexibility of the additive manufacturing machine S600D, Lynxter can manufacture its own tooling to meet the needs of production storage. The new FIL21 Direct Drive toolhead is a game changer with easy printing of very soft materials such as TPU, but also of brittle materials. Thanks to this FIL21 Direct Drive, the protective part was modified and reprinted in a few hours.
Technical summary of the case study : tool holder cover
SECTOR | Manufacture |
APPLICATION | Protective part |
MATERIAL | TPU 95shA |
DIMENSIONS | 150 mm x 133 mm x 44 mm |
PRINTING TECHNOLOGY | S600D 3D printer & FIL21 |
PRINTING TIME | 09H35 |
MATERIAL QUANTITY | 59,19 gr |
MATERIAL COST | 38,8 €/kg |
COAT HEIGHT | 0,2 mm |
NOZZLE SIZE | 0,4 mm |
PRODUCTION VOLUME | Unit |
Want to lean more about this matter ? Contact our team.