HOW 3D PRINTING CAN BE USED TO RESPOND TO AN EMERGENCY SITUATION IN RAILWAY?
Lynxter and its additive manufacturing machine tool, the S600D, were called upon by a railway sector company to solve a train maintenance problem.
Silicone 3D printing facing the unexpected
The company needed to change a faulty part on one of its trains. However, this part is out of stock. The part is traditionally produced using injection molding and typically requires a manufacturing lead time of several months; a delay that the company could not anticipate due to the unforeseen nature of the incident. When this particular part is damaged or missing, the train may be immobilized, resulting in significant financial loss for the company.
The part in question is a boot seal for a brake system – used to protect the system from water, dust , oil and ballast.
It is not a very exposed part and needs to be made of a really flexible material: silicone is therefore ideal.
Silicone additive manufacturing therefore appears to be an ideal alternative to address this one-off and urgent need.
How then to move from a molded part to a printed part?
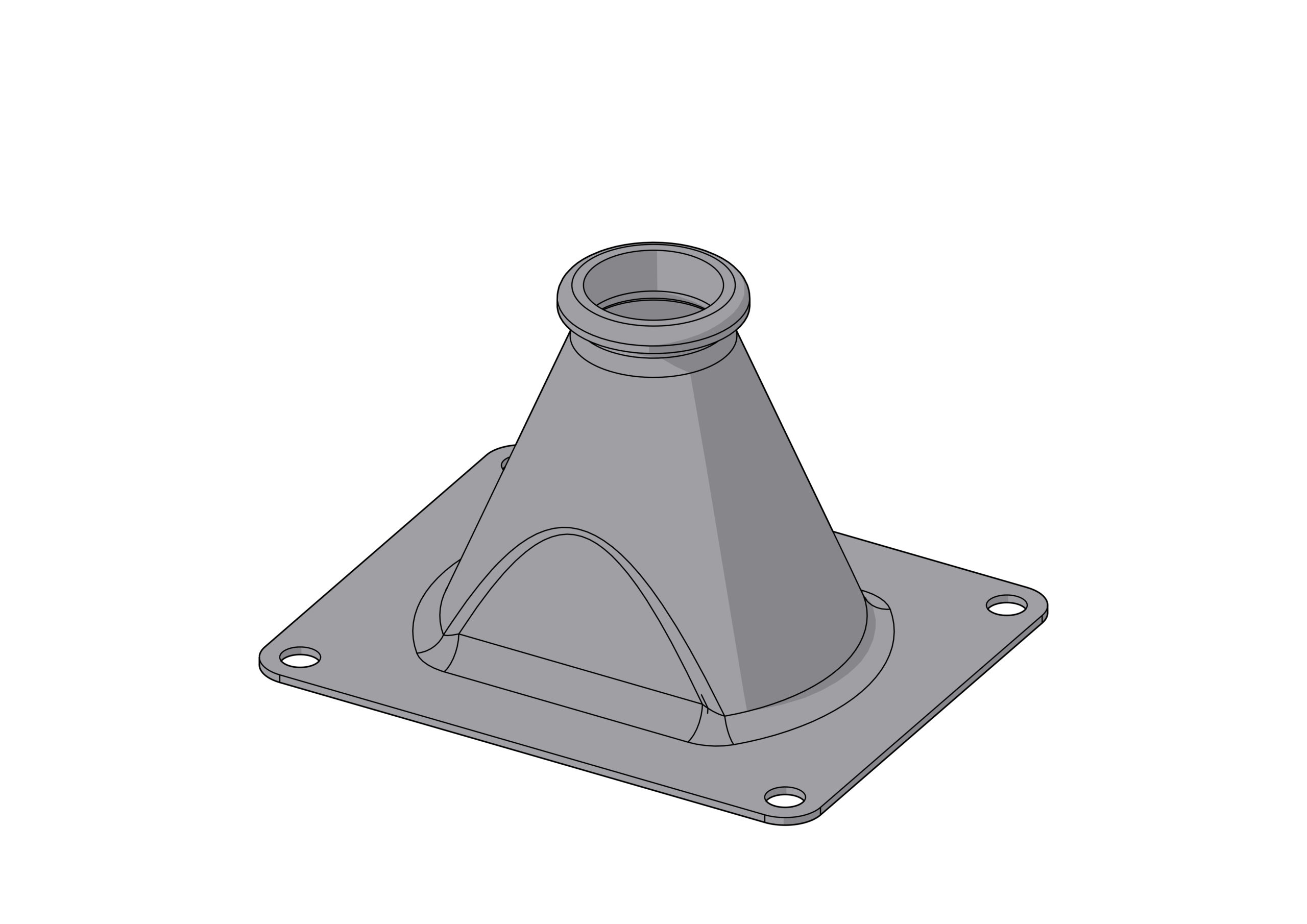
Every process has its own CAD
The boot was printed by Lynxter on the S600D, additive manufacturing machine-tool fitted with the two-component liquid extrusion toolhead, LIQ21. This first version was printed in accordance with the model provided by the company, a model that had been designed for injection molding.
Result: the fillets under the 3D printed part and the upper rim of the boot were not printed correctly.
The conclusion is quick to see; the part designed for injection molding cannot be correctly 3D printed. The defects induced by the limitations of 3D printing are too major to enable the part to be used (burrs, deterioration of supported areas, collapsing due to areas that are too thin).
The design of a part must be adapted to the manufacturing process used to make it: design rules are therefore different depending on the possibilities and limitations of each manufacturing process.
By making small adjustments to the CAD while still respecting the functionality defined by the design office, a second version of the part was produced using additive manufacturing on the Lynxter S600D 3D printer. It is important to remember that the S600D uses a technology based on the printing of successive layers of extruded material. Printing an unsupported layer of silicone is difficult and it should therefore be ensured that the upper layer is completely or partially supported by a layer below. Unsupported overhangs should be avoided as should large fillets.
For the upper edge of the boot, the 90° overhang has been replaced with a chamfer so that each layer can rest partially on a layer underneath.
With regards to the fillet under the part, the rounded angle does not allow for correct successive printing of layers. It is therefore best to use a 45° angle chamfer.
Computer Aided Design (CAD) enables models to be quickly optimized and adapted to liquid extrusion additive manufacturing. As a general rule, for silicone printing it is recommended to use overhangs of less than 45° so that the part can be correctly printed.
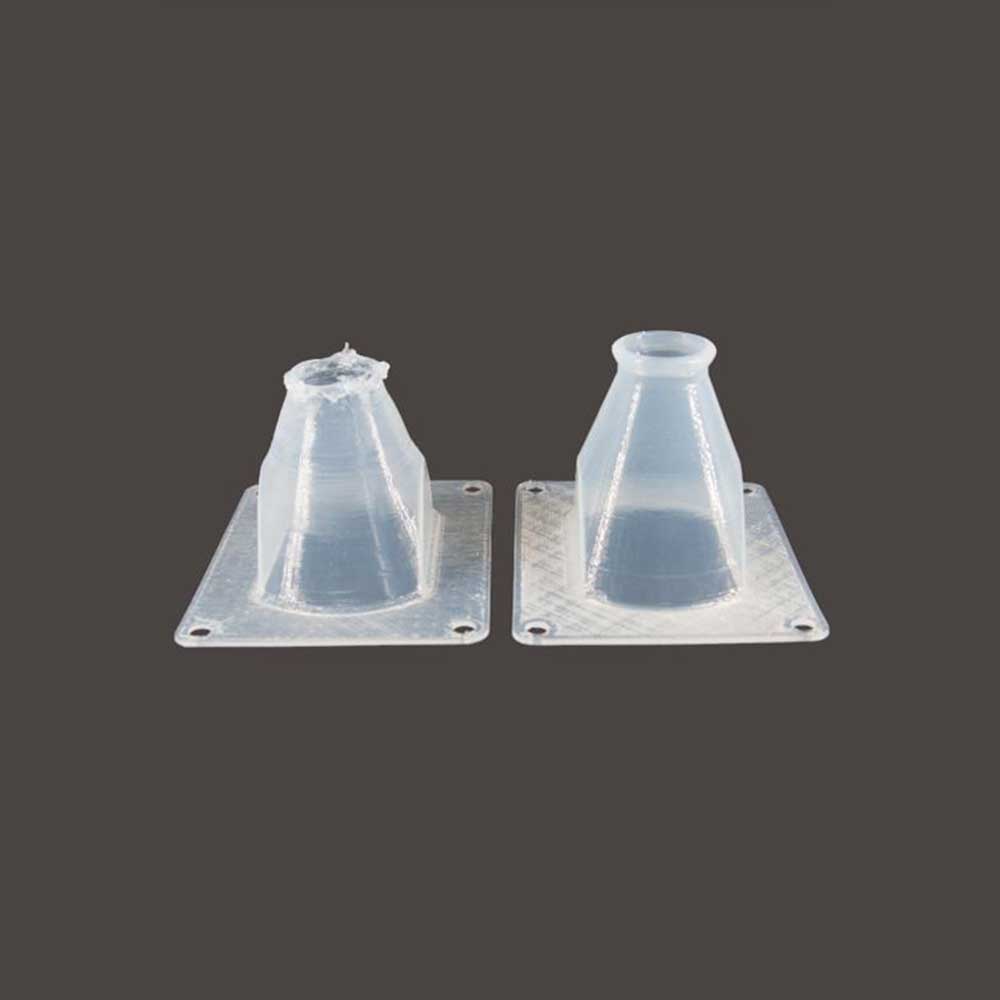
Result: a valuable time saving solution
The deadlock situation was therefore resolved rapidly thanks to additive manufacturing along with a quick modification of the original CAD. This maintenance operation, that would have taken many weeks to resolve with the classic supply chain, was successfully dealt with in just days thanks to the S600D.
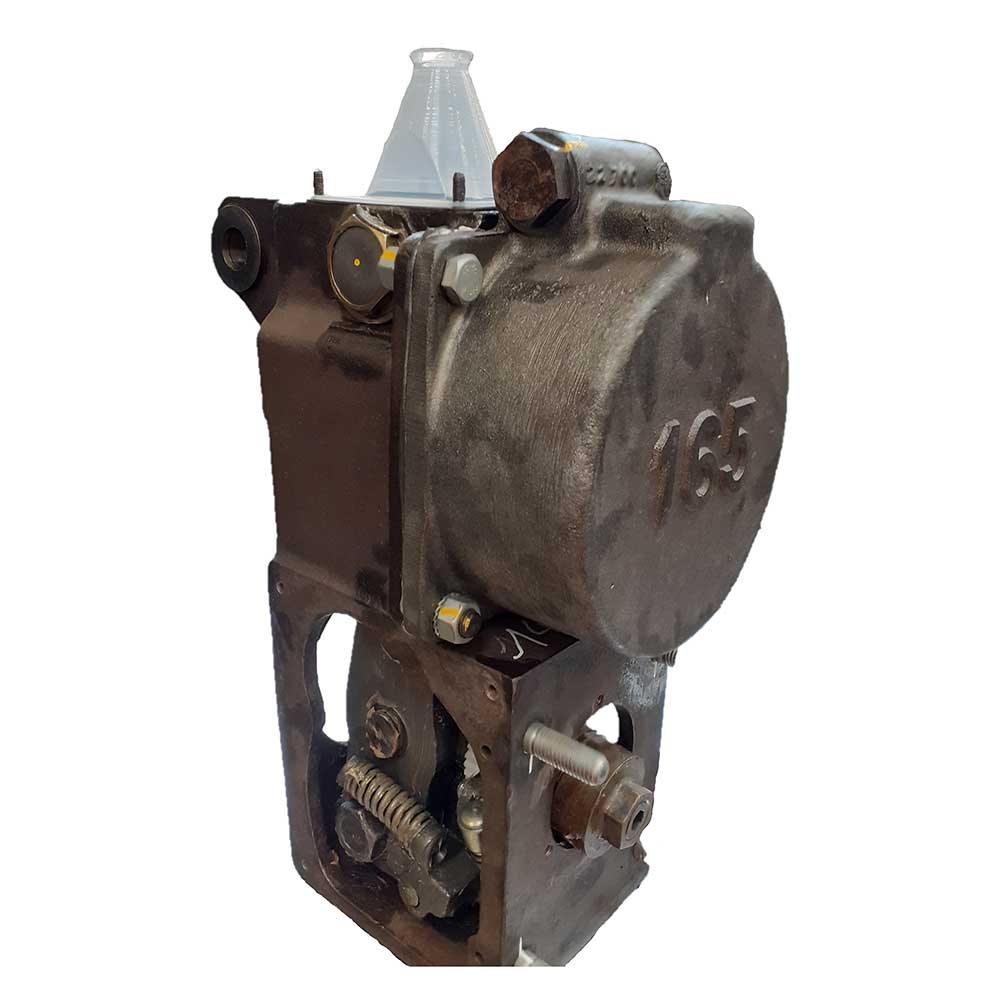