High-performance filaments 3D printing: Renault use case
Which industries are using 3D printing today and how? Through the example of Renault tooling, Lynxter looks at the advantages of industrial 3D printing of high performance filaments in the automotive industry.
Additive manufacturing at Renault
The Renault innovation community
The Renault group needs no introduction. Since 2012, the French car manufacturer has equipped its R&D laboratories with 3D printers at the Guyancourt techno center. Today, more than 170 3D printers, including 30 industrial 3D printers, are involved in Renault’s experimental and industrial approach.
Grouped under Renault Tooling, the additive manufacturing service centers are spread over 3 locations: Meyzieu, Cléon and Le Mans. Each center has a fleet of 3D printers dedicated to the group needs, including a industrial 3D printer S600D from Lynxter.
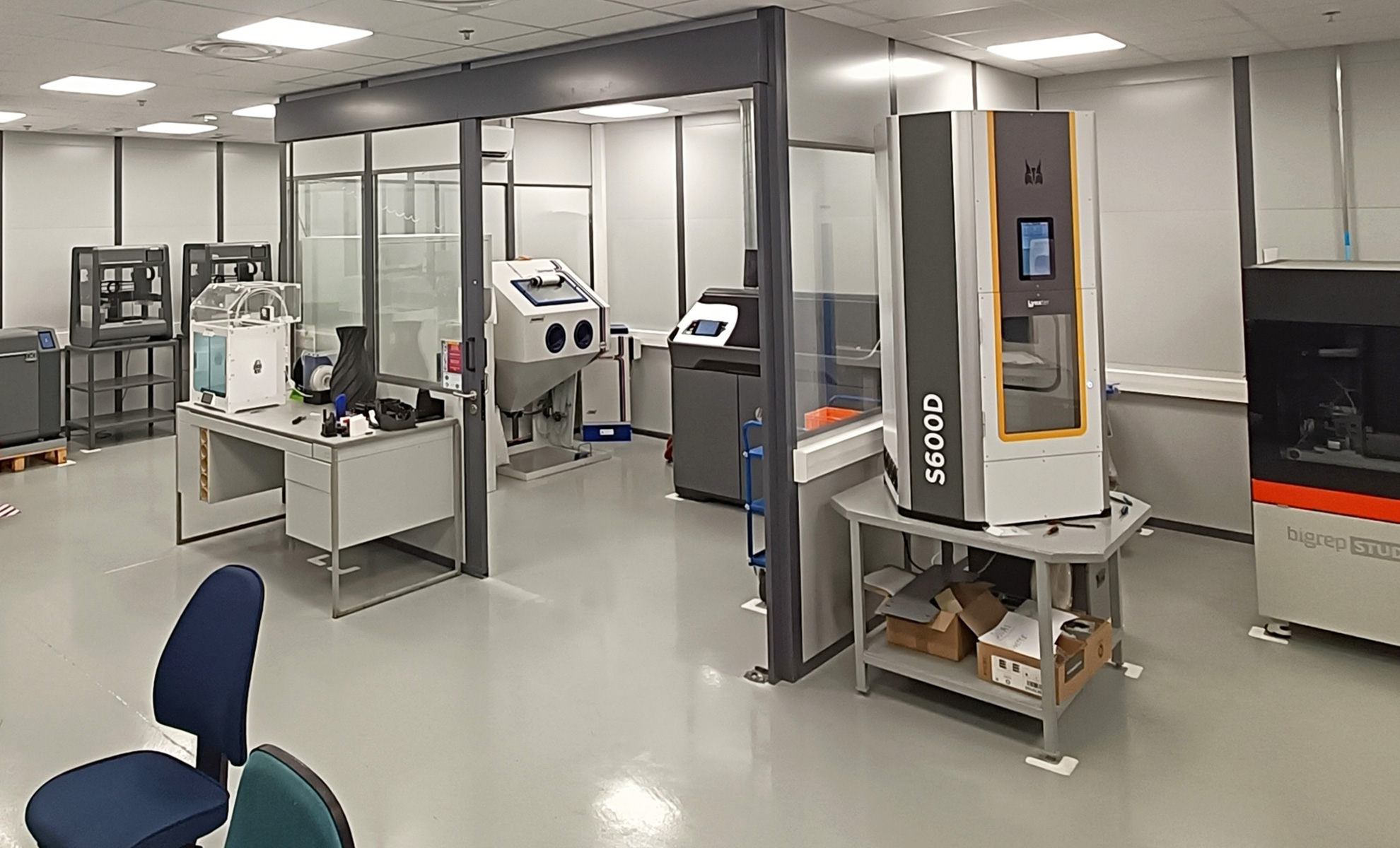
Additive manufacturing center- Renault Meyzieu
How does Renault use 3D printing ?
Additive manufacturing acts as an accelerator within various projects. As strong ideas incubators, internal “Fablab” and Additive Manufacturing (AM) service centers offer the possibility to make rapid progress on product development and allow work on anticipating the uses of future customers.
Today, Renault uses 3D printing to produce both functional prototypes that meet a rapid need on its production lines and spare parts that are not available on the market, intended for garages and private individuals.
Renault Tooling is rethinking the industrial process by offering new tools to optimize production lines. Examples of applications include tooling for welding guides or screwdrivers, setting support such as gearbox supports, assembly tray prototypes, engine sprocket control templates, decanter plug installation tools, and consumables such as gripper protectors, wheel rim protectors, water pump diffusers and cylinder head cover plugs.
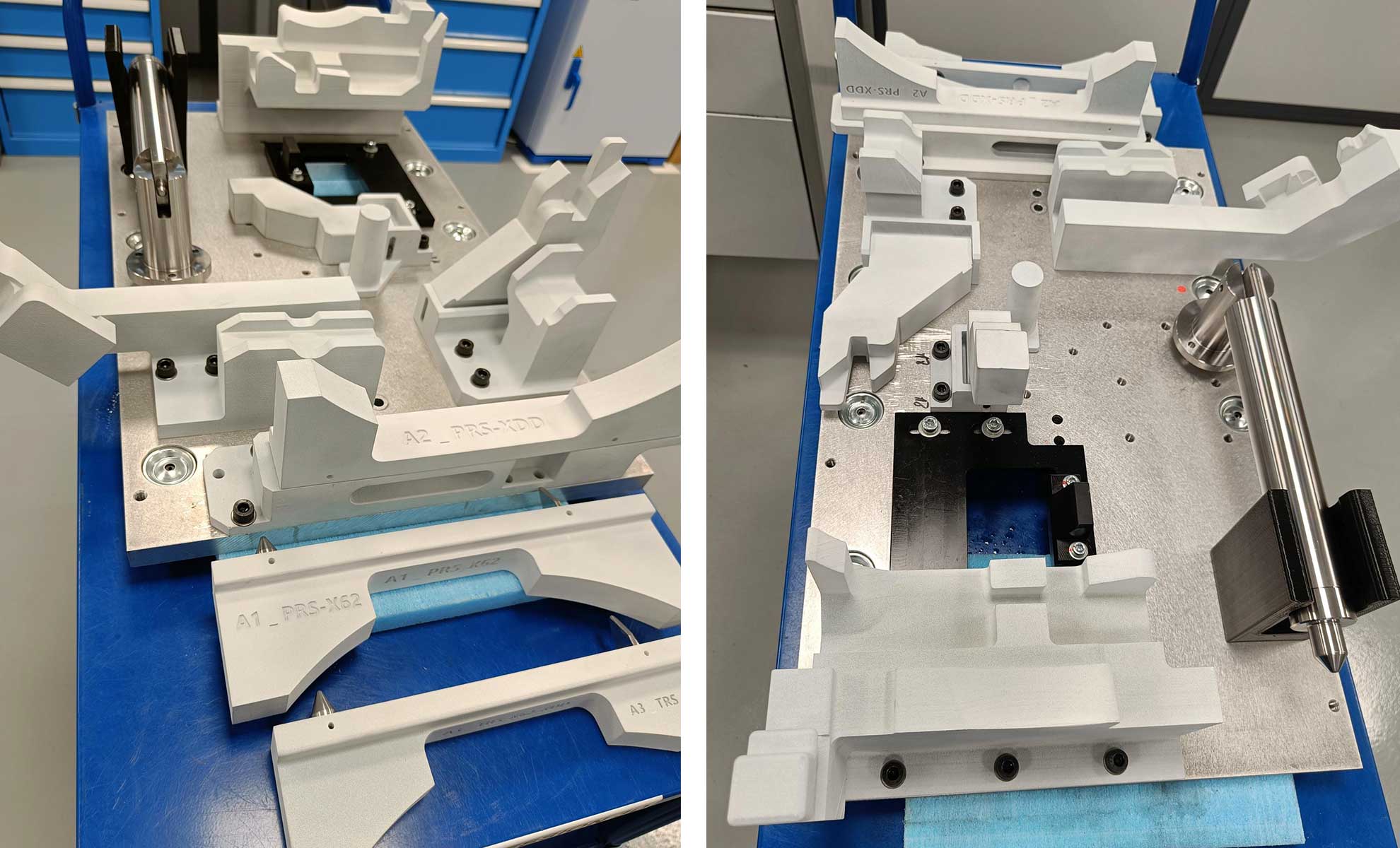
gearbox support printed via SLS
Industrial 3D printing also brings a new autonomy in the production of prototypes, maintenance operations and small series production. Freedom of design, customization, reactivity and savings, the list of advantages of additive manufacturing for the automotive industry is obvious. Motor sports have been quick to adopt and use it: around ten 3D printed parts were produced in a Renault Formula 1 engine in 2018.
User case : PEKK-A 3D printing of a crankshaft inducer cover
The Meyzieu additive manufacturing center was called in to produce a part for a crankshaft inducer cover to close a sub-assembly subjected to heat.
As this part had to withstand a lot of mechanical handling and high temperatures, the team looked at high performance filaments and after some testing, chose PEKK-A.
This part allows Renault to achieve a significant cost reduction. The current part costs 258€, the one produced in PEKK-A only 185€, i.e., a saving of 28%.
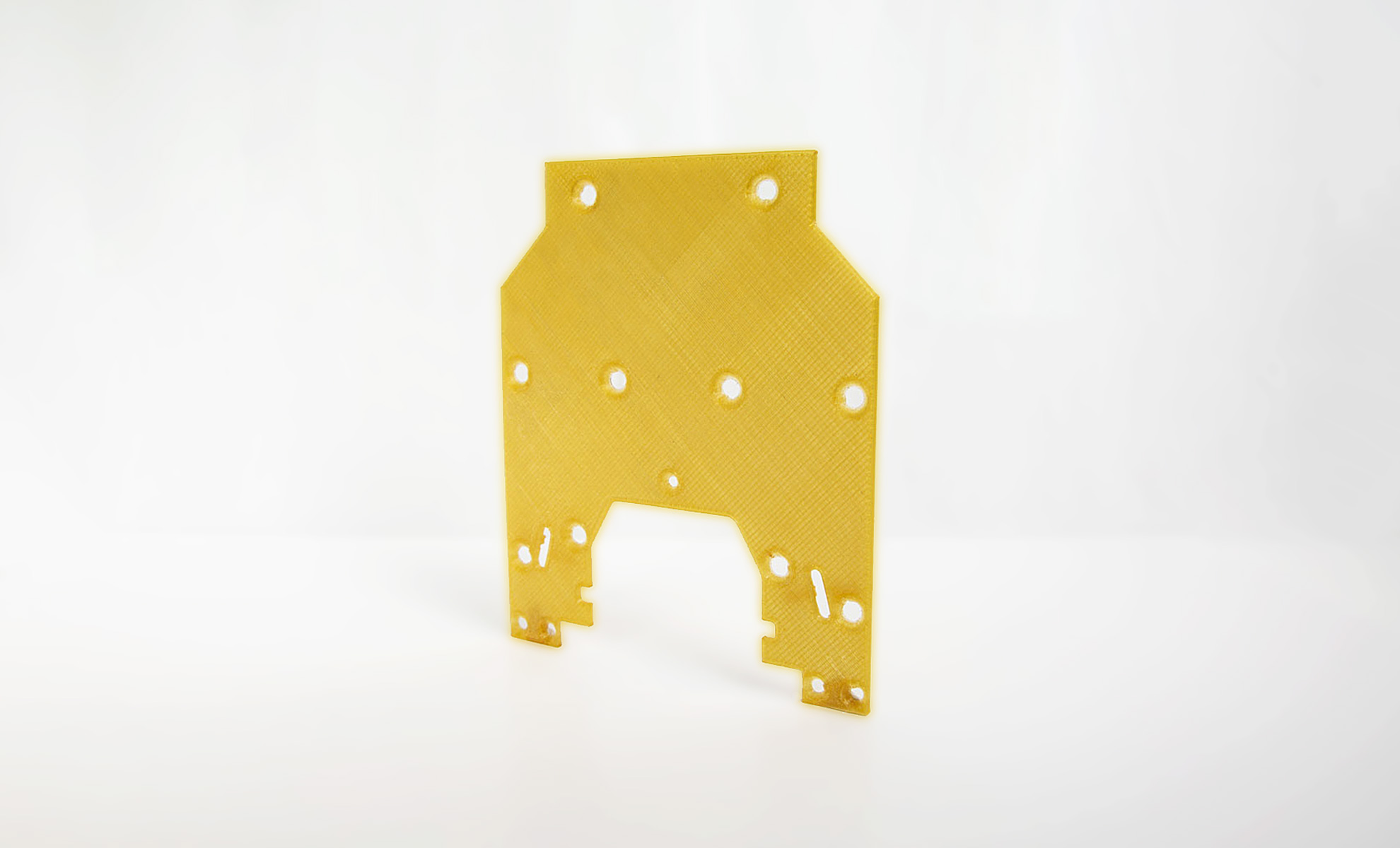
PEKK-A crankshaft inducer cover
Highlight : High-performance Materials
Renault picked PEKK but there are other materials at different costs
PEKK
Polyetherketoneketone (PEKK) is a semi-crystalline thermoplastic polymer of the PEAK family. It has very good mechanical properties at high temperatures (up to 150°C) which makes it particularly suitable for use in extreme environments. Its abrasion resistance, low mass and electrical insulation make it an excellent choice for lightening metal structures while maintaining similar mechanical strength. It is used in the aerospace, marine and automotive sectors. As PEKK is a high-performance material, it cannot be printed by any 3D printer: the chamber needs to be heated evenly to around 80°C to allow the layers to fuse together. Without this heating, the material would easily delaminate and lose all its mechanical properties.Industrial 3D printer Lynxter S600D addresses these technical difficulties with its closed, heated chamber, allowing the printing of high-performance materials such as PEKK, PA-CF or PC using the FIL11 and FIL21 toolheads. (available for pre-order)
PA-CF
Composed of carbon microfibers, PA-CF filament is a semi-crystalline polymer that can also withstand high temperatures (up to 100°C), but which are still lower than those from PEKK. Its good chemical and impact resistance and high rigidity make it ideally suited to the manufacture of mechanical parts. It is widely used in the automotive sector for various prototypes but also for finished parts such as protective housings or pump housing. Like PEKK, 3D printing of PA-CF requires a closed chamber heated to 60°C.
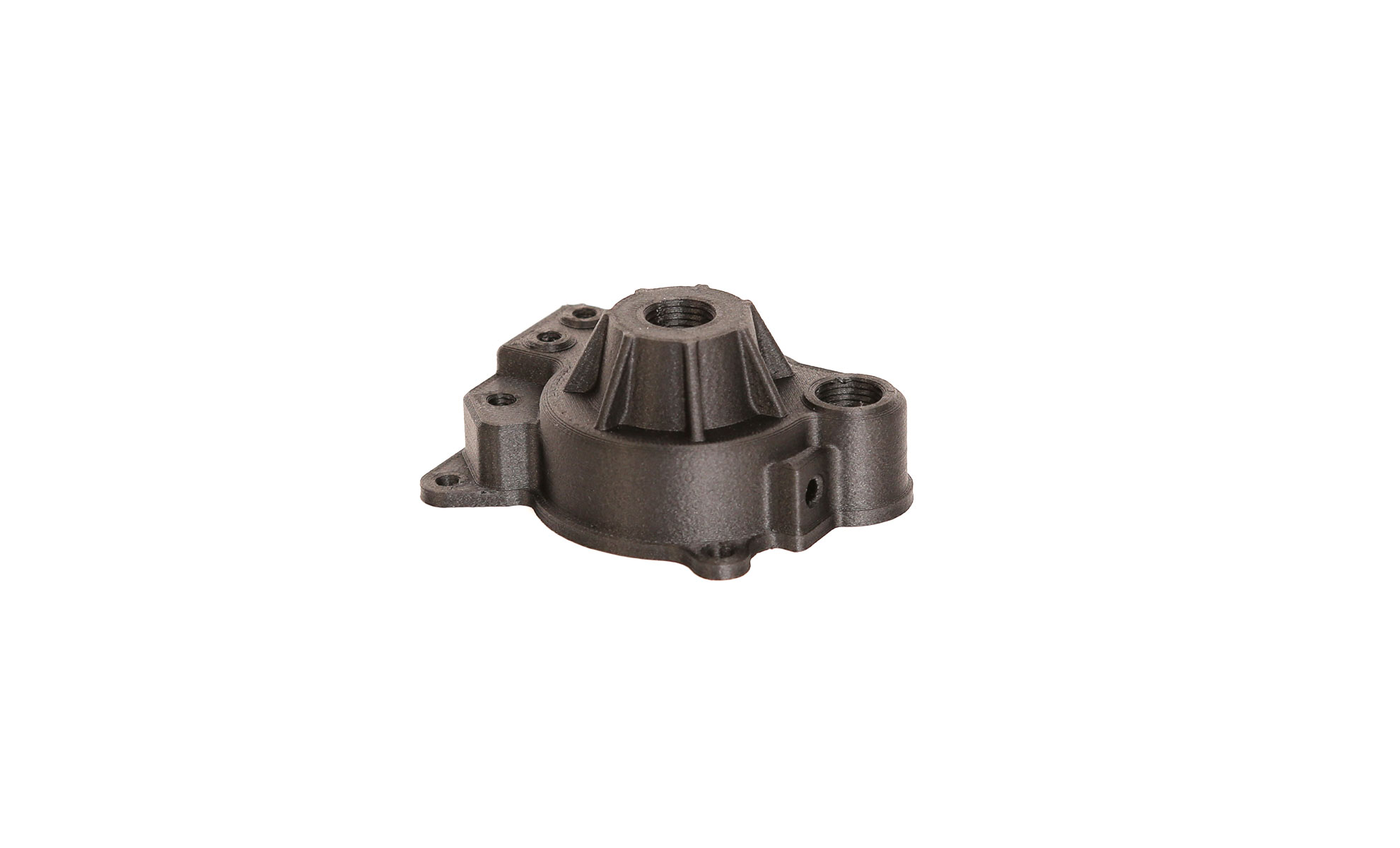
PA-6 CF Printed pump housing
PC
Polycarbonate is an amorphous thermoplastic polymer. It is characterized by its high impact strength and heat resistance (up to 120°C). Its rigidity makes it particularly interesting for functional parts such as gears or other mechanisms. Its printing requires a heated and preferably closed chamber. The finished printed parts have the advantage of being very light.
PEKK, PA-CF or PC, these examples of high-performance filaments are not as easy to print as PLA and require a 3D printer with a temperature-controlled and enclosed chamber to protect its users.
Lynxter S600D machine meets both requirements: the thermal environment of this 3D printer can withstand an 80°C enclosure, its closed chamber blocks possible material fumes and temperature changes. It can then print all these high-performance filaments in complete safety.
A great thanks to Renault Meyzieu and Fabrice Forest for exhibiting and presenting the 3D printing achievements of the site.
References
https://www.sia.fr/evenements/213-fabrication-additive-sport-auto-vehicule-serie-usages-opportunites
https://www.usinenouvelle.com/article/un-fablab-stimule-la-creativite-de-renault.N1859502
https://nanovia.tech