ADVANTAGES OF 3D PRINTED SILICONE FOR SOFT ROBOTICS
Have you heard about soft robotics? Deformable, flexible and soft, these new robots are transforming Industry 4.0: Learn how silicone 3D printing can be a real benefit for soft robotics and how the Schneider Electric Openlab is using soft robotics and the Lynxter S600D to make a prototype gripper.
WHAT IS SOFT ROBOTICS?
Soft robotics is a technology that concerns the creation of robots that are almost entirely “soft”: their articulations and their movements are flexible thanks to the use of soft, elastic, bendable or easily deformable structures and materials.
That’s great, but how did we get here? The field of soft robotics is the natural evolution of robotics. It appeared with the development of technical silicones and innovative processes such as the 3D printing revolution. These solutions now make it possible to significantly broaden the variety of robotic motions by integrating mechanical movements of compression, stretching, unwinding and swelling. Robots therefore possess more flexible and softer motion mechanics; some robots can, for example, reproduce the undulating and twisting movement of tentacles.
Object manipulation is more precise and controlled: soft robots drastically minimize risks of danger and damage to the surrounding environment during intervention. This solution is perfectly suited to interaction with unstable or uncertain environments as well as for handling fragile objects in the food, space or medical robotics sectors, for example
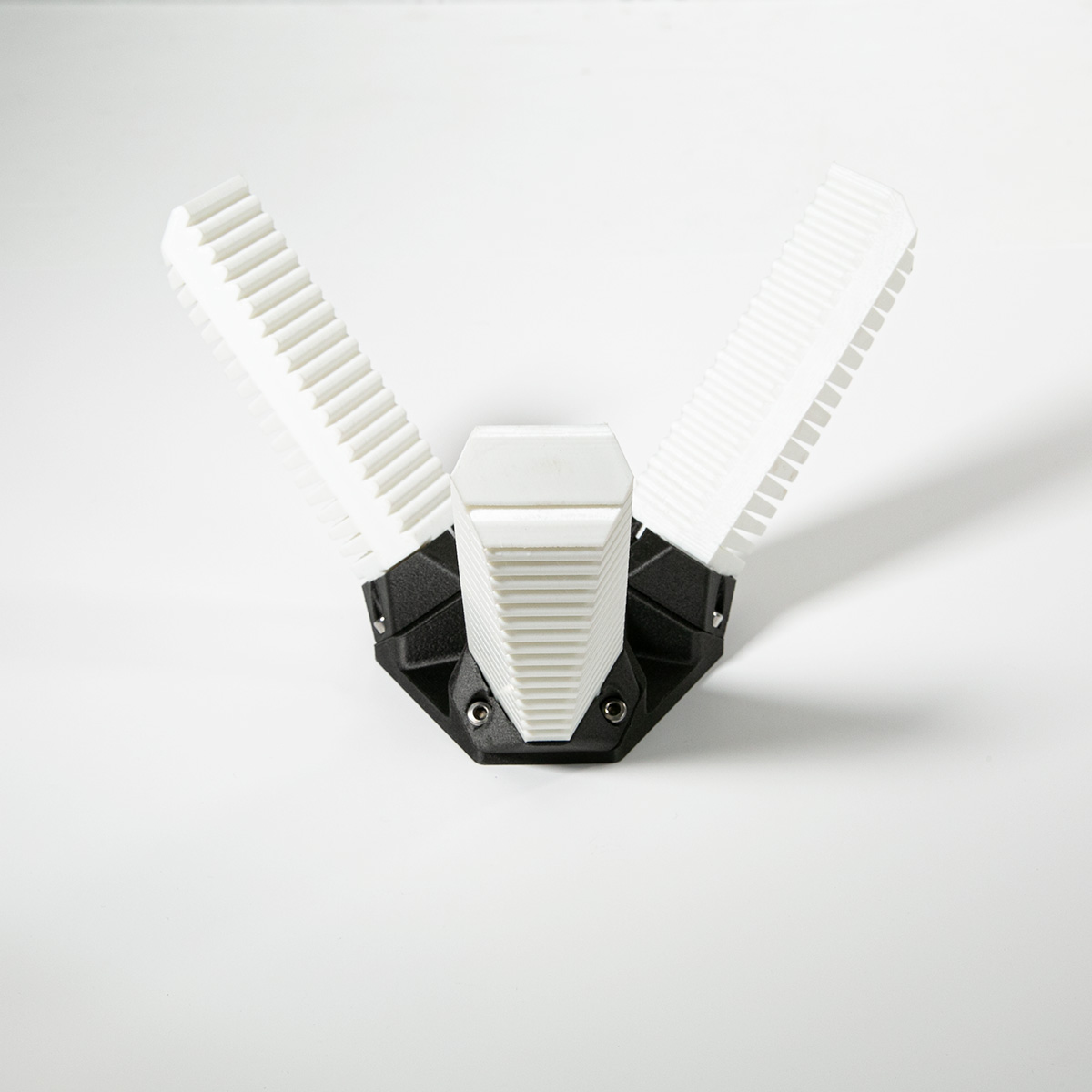
Soft robotics prototype – Gripper made by the R&D team at Lynxter
APPLICATIONS OF SOFT ROBOTICS
Soft robotics is now regarded as a new branch of robotics. Although essentially at the prototype or confidential project stage, these soft robots are a real step forward in terms of security, robustness and cost reduction as they are inexpensive to manufacture and bring versatility and unprecedented flexibility.
Soft Robotics is now being tested for operations where high levels of precision are required in delicate environments such as certain microsurgical procedures: miniature robots weave their way into difficult areas and can deliver drugs to precise locations. Soft robots are therefore able to work in contact with tissues and cells without causing damage.
This technology can also be used for the study of coral reefs where gentle movements are essential in order to preserve the underwater environment
Complementary to current industrial robotics, flexible grippers make it possible to handle many different types of objects without causing damage, for example delicate foods (fruits, vegetables, cakes). Their design makes it possible to grip objects of different shapes, textures, weights and volumes.
The manufacturing industry is currently moving towards robots that enable human-robot collaboration. These collaborative robots or “cobots” minimize the risk of injuries to the user in the event of an impact. Thanks to soft robotics such manufacturing systems can develop: the flexible designs of the cobots ensure the safety of both the machine and the user.
3D PRINTED SILICONE AND SOFT ROBOTICS
Soft robotics is made possible thanks to the use of soft materials such as silicone, plastic, rubber and other polymers, and/or by a light and flexible mechanical structure. The soft robot moves mainly due to the deformation of its structure.
The choice of polymer is essential to its development and its function: the materials used must meet the needs and requirements of the environment in which the robot is to evolve: chemical inertia, electrical insulation, temperature, friction, food contact etc.
This new approach is built on an improved knowledge of flexible polymer materials and on 3D printers capable of printing increasingly high-performance elastomers.
With its excellent insulating properties, its resistance to high temperatures and to chemicals and, above all its great elongation capability, silicone is a polymer that is widely used in soft robotics.
Thanks to the S600D 3D printer and the LIQ21 toolhead capable of printing liquid materials, silicone can be 3D printed and used in robotics.
Silicone 3D printing enables the creation of new experimental shapes. Unlike traditional molding processes, these silicone parts can possess complex internal geometries (microcavities, honeycomb etc.) that would be impossible without 3D printing.
A range of RVT1 and RTV2 silicones from 10 to 40 shore A hardness is already available on the Lynxter ecosystem and these silicones are used in different sectors.
Combining silicone 3D printing and soft robotics opens the door to new possibilities and developments, notably for key applications such as robot self-repair and self-replication using artificial intelligence.
Lynxter’s R&D department works every day on the development and implementation of elastomers with new properties. The 3D printing of parts that are both hard and deformable now makes it possible to combine flexibility and resistance with deformation and facilitates the development of a new generation of soft robots.
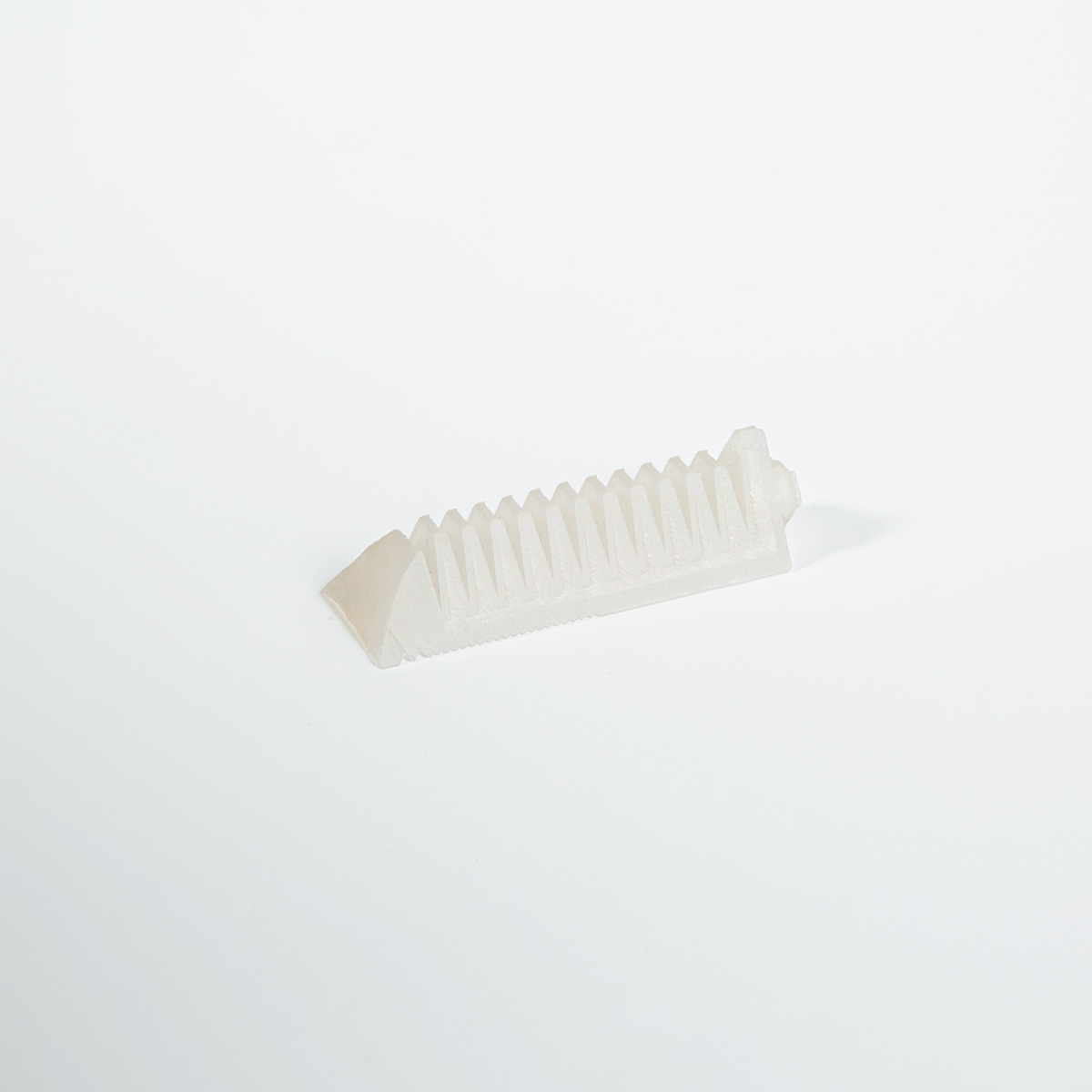
Finger prototype gripper made by Openlab – Schneider Electric
Gripper prototype made by Openlab – Schneider Electric
SILICONE 3D PRINTING USE CASE
THE OPENLAB SOFT ROBOT – SCHNEIDER ELECTRIC
Equipped with numerous 3D printers, including the Lynxter S600D, the Schneider Electric Openlab prototyping unit is conducting different projects to accelerate the innovation of new products and improve profitability on its production lines. One of these projects aims to produce a flexible and modular production line that can be adapted to all types of new projects and to parts of different shapes. The module developed must fit onto a cobot arm to ensure the security of the operator working nearby. For this, the Schneider Electric Open Lab team naturally turned to soft robotics.
The Schneider Electric Openlab has developed a prototype of a silicone gripper with multiple “fingers” compatible with a robotic arm.
Each finger is printed in silicone on the Lynxter S600D, making it easy to rapidly iterate the design and to change the configuration of the gripper according to the current production line project.
Industrial 3D printing provides great flexibility and freedom of form: the assembly configuration can be modified and different models of silicone “fingers” added in just a few hours. The production process gains both flexibility and modularity.
To make the gripper the Openlab team first created the 3D model of the finger optimized for 3D printing in silicone. This finger is moved using compressed air (approximately 0.6 bar).
The finger comprises 2 parts:
• The main body of the finger features a series of pyramid-shaped air chambers. These chambers expand as they inflate, creating the flexing motion of the finger. The chambers are designed in accordance with the design rules for the process.
• The exterior which must grasp and hold the object has a toothed design with a wide notch. The fingertip is solid so that it can return to its original shape with gravity when the air is expired.
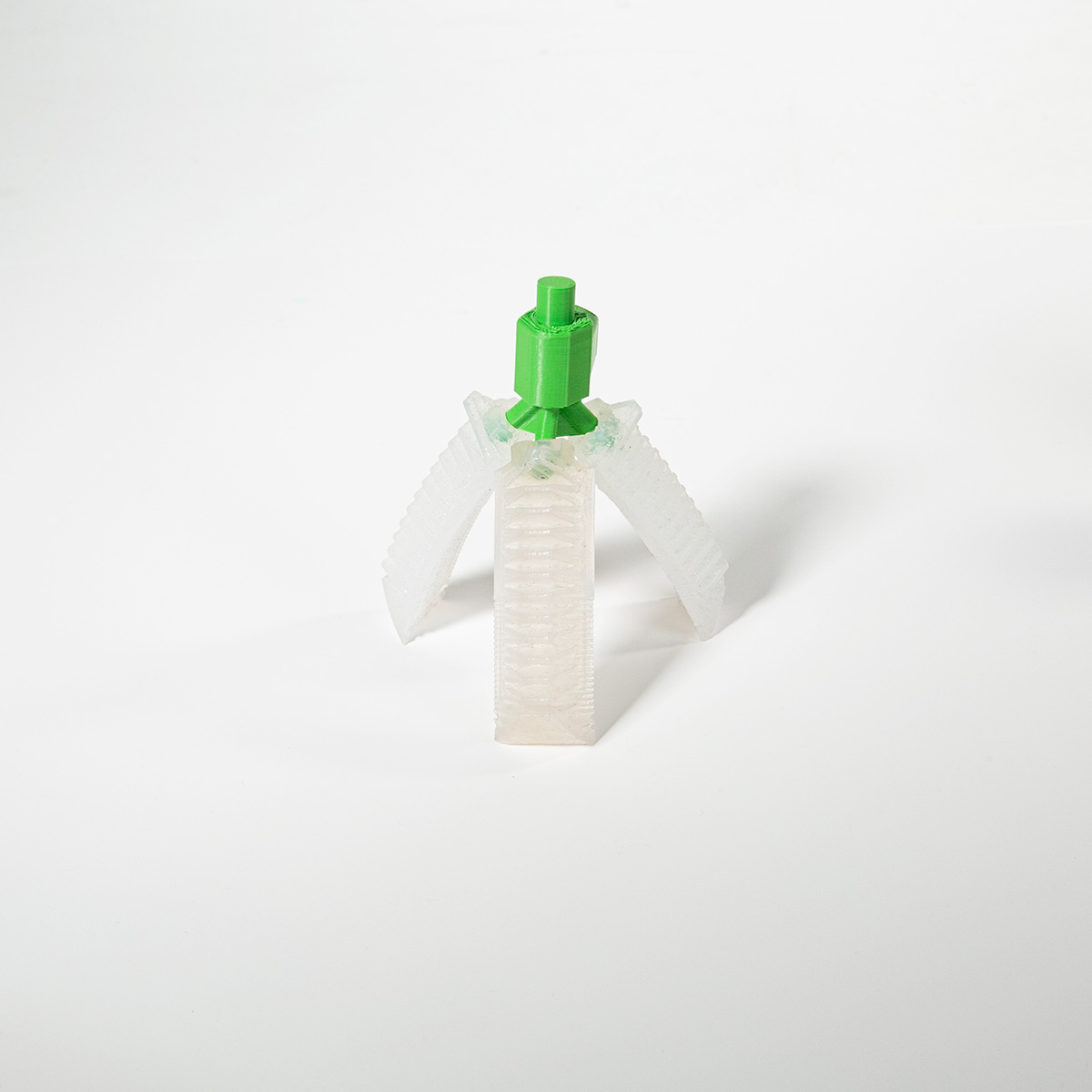
Prototype du préhenseur réalisé par Openlab – Schneider Electric
The fingers were printed in RTV2 40 shoreA silicone with the Lynxter S600D professional 3D printer. This prototype gripper will first be used on the control line before being optimized and duplicated. The gripper will be able to grab cylindrical-shaped objects of ⌀20mm x 25mm for sorting thanks to video recognition and in this manner will participate in machine learning for continually optimized production line performance.
Using the S600D for soft robotics projects provides a high level of reactivity thanks to the machine’s modularity. By simply changing the toolhead the S600D can be used to print a new gripper support in thermoplastic filament with silicone fingers and therefore enables the robot to change its shape quickly and easily.
Soft robotics is a now a rapidly evolving area that requires extensive research into flexible and elastic materials and their behavior. With the S600D and its silicone 3D printing technology, Lynxter is actively contributing to resolving these new scientific and technological challenges.
References :
https://www.sciencesetavenir.fr/high-tech/un-robot-en-materiau-mou_35284
https://en.wikipedia.org/wiki/Soft_robotics
https://rm.is.mpg.de/research_fields/bioinspired-soft-actuators-sensors-robots-and-machines
You should read
A NEW MAJOR BREAKTHROUGH IN ORTHOPEDICS: 3D PRINTING OF TAILORED SILICONE LINERS
SILICONE 3D PRINTING: HOW AND WHY PRINT SILICONE?
HOW TO REDUCE THE WEIGHT OF METAL PARTS BY 70% WITH 3D PRINTING