Silicone 3D Printed Masks for Wet Surface Treatment
Strategies, Benefits, and Diverse Applications
Silicone 3D printed masks are at the forefront of innovation, especially when it comes to surface treatment. In this article, we’ll delve into the strategic advantages, benefits, and the wide-ranging applications of these masks across various sectors, positioning them as essential tools for efficient and precise wet surface treatments.
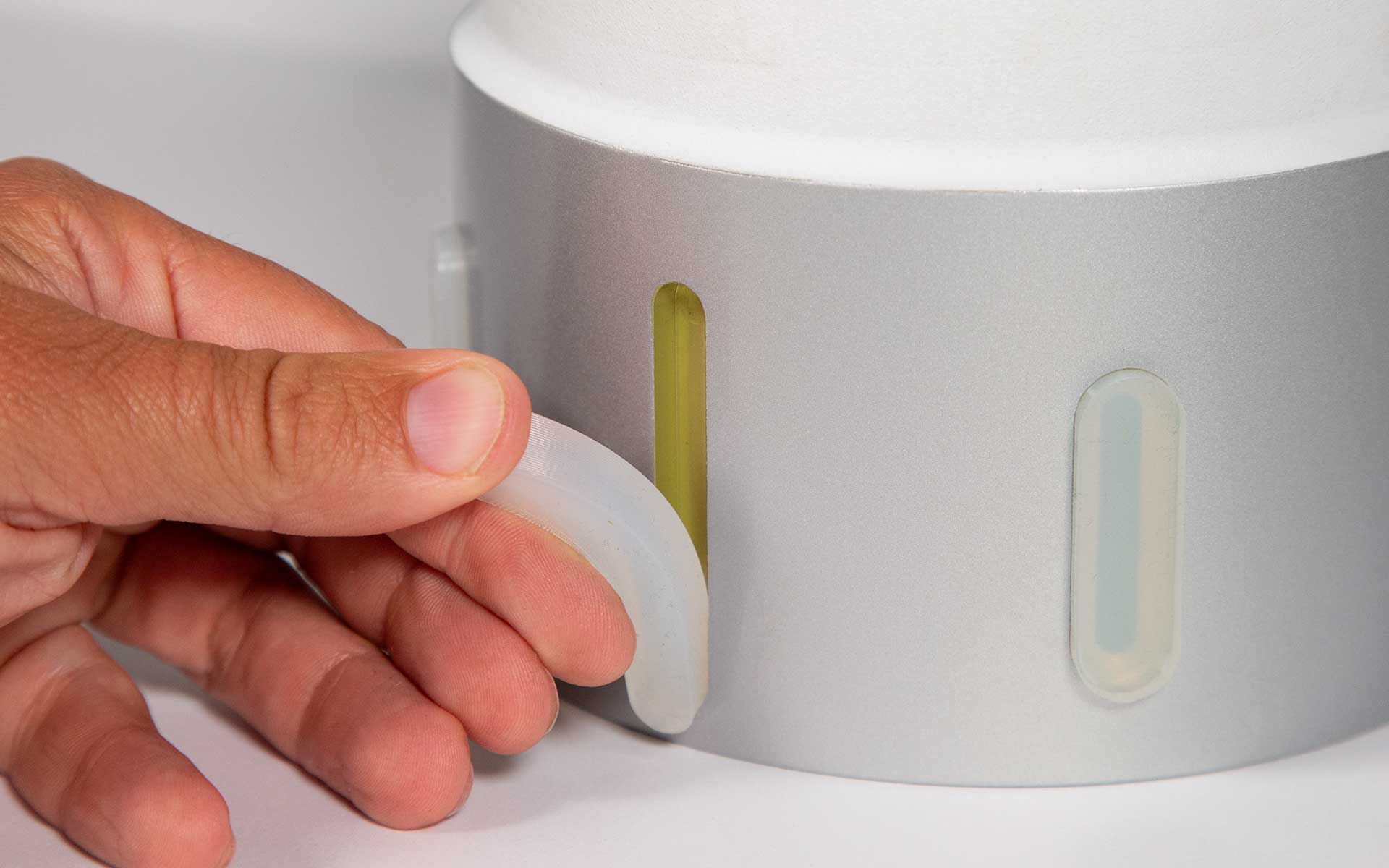
Silicone Printed Masking Cap
Why choose silicone 3D printed masks for surface treatment
Using silicone plugs and masks in surface treatment is a smart way to avoid manual mistakes during masking process. These silicone tools play an important role in the masking and unmasking steps of surface treatment, saving time and improving the quality check for the final part. In cases where the right silicone tools aren’t available (specific geometries for small series or complex form), masking technicians often resort to using tapes to cover the parts that need treatment.
Enter silicone 3D printing, a new solution that allows the production of limited series of customized masks or plugs in silicone with several strategic advantages for this industry :
– Custom-fit precision: Silicone 3D printing enables the creation of personalized masks that fit perfectly, ensuring a precise and effective seal for surface treatment.
– High resistance: Silicone is renowned for its ability to withstand high temperatures and chemicals, making it a suitable choice for numerous coating and surface treatment processes.
– Durable solution: Silicone’s durability ensures that the masks can withstand the demands of surface treatments, providing a reliable and reusable solution, leading to reduced waste.
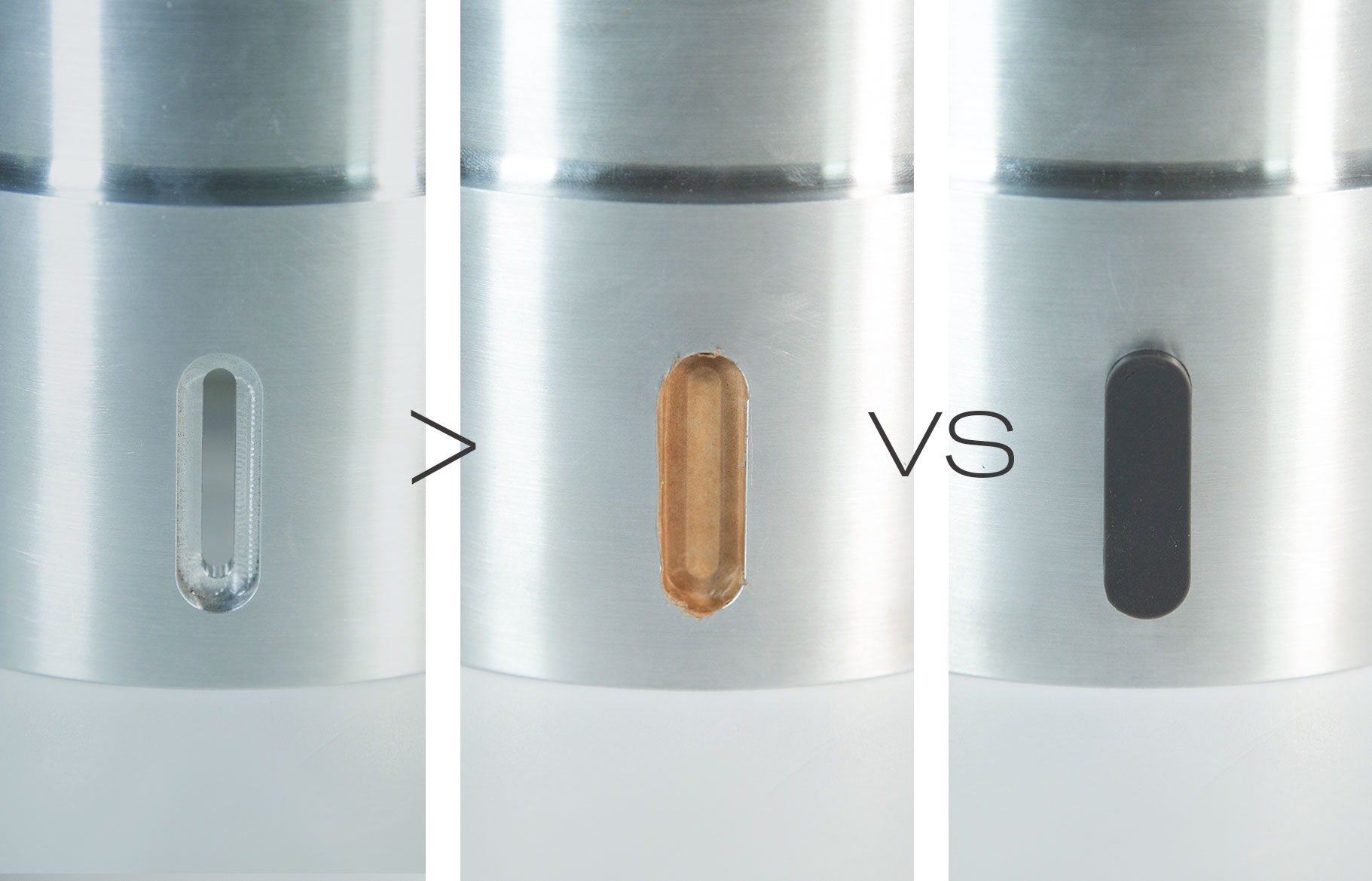
Tape mask vs silicone mask
Benefits of silicone 3D printed masks for wet surface treatment
Wet chemical treatment, also referred to as wet chemical processes or wet chemical etching, is a surface treatment method utilized to modify or transform a material’s surface properties through chemical reactions in a liquid medium, either aqueous or solvent based.
This technique finds widespread application in various industries, including electronics, semiconductor manufacturing, materials science, and metallurgy. Its purpose is to attain specific surface characteristics such as cleanliness, texture, adhesion, corrosion resistance, and more.
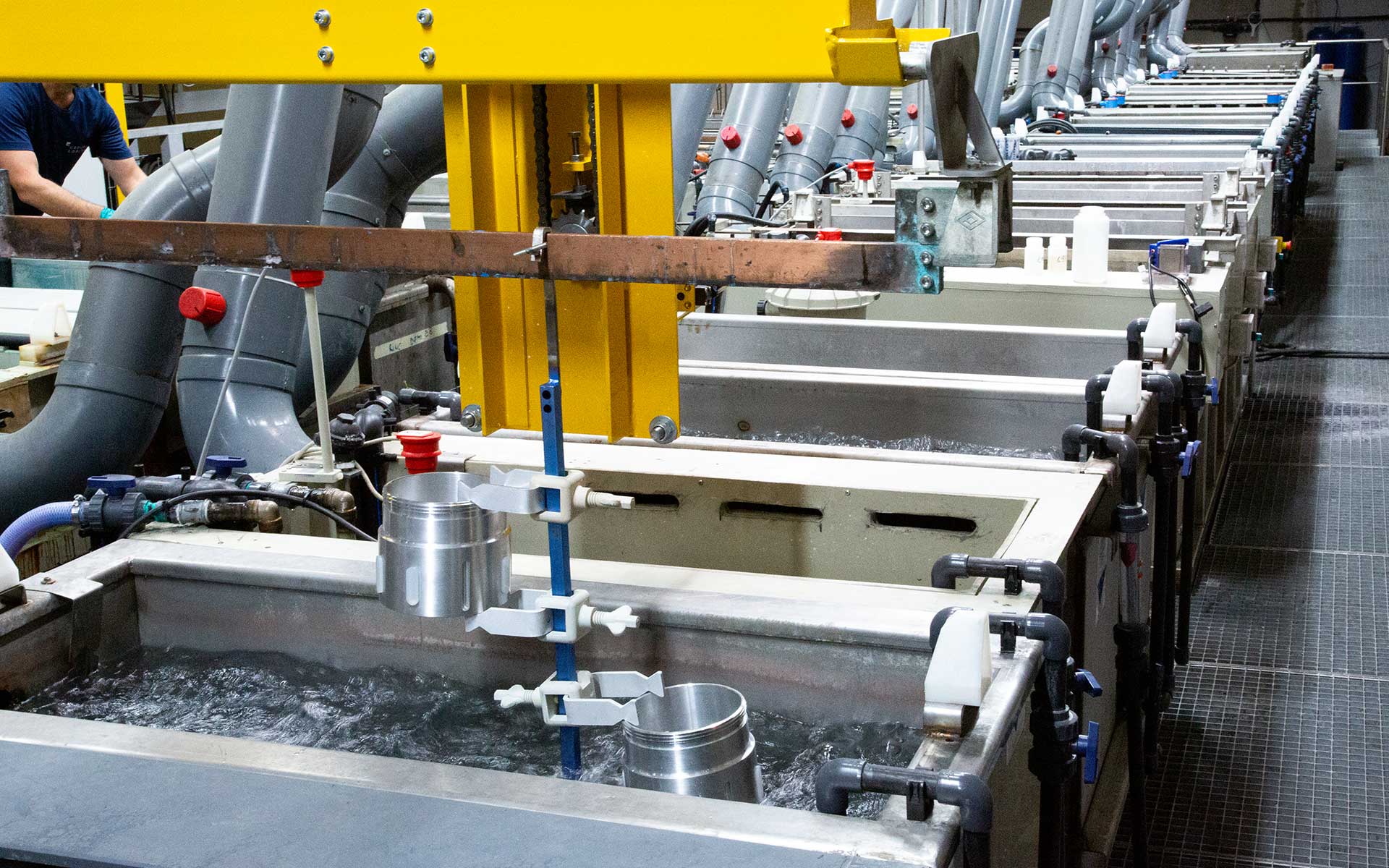
Parts masked by silicone 3D printing plugs immersed in chemical baths
The process entails submerging the material to be treated (typically a solid substrate or component) into a solution containing chemical reagents that interact with the surface at a molecular level. These chemical reactions can result in the removal of specific layers, deposition of new layers, or alterations in surface properties.
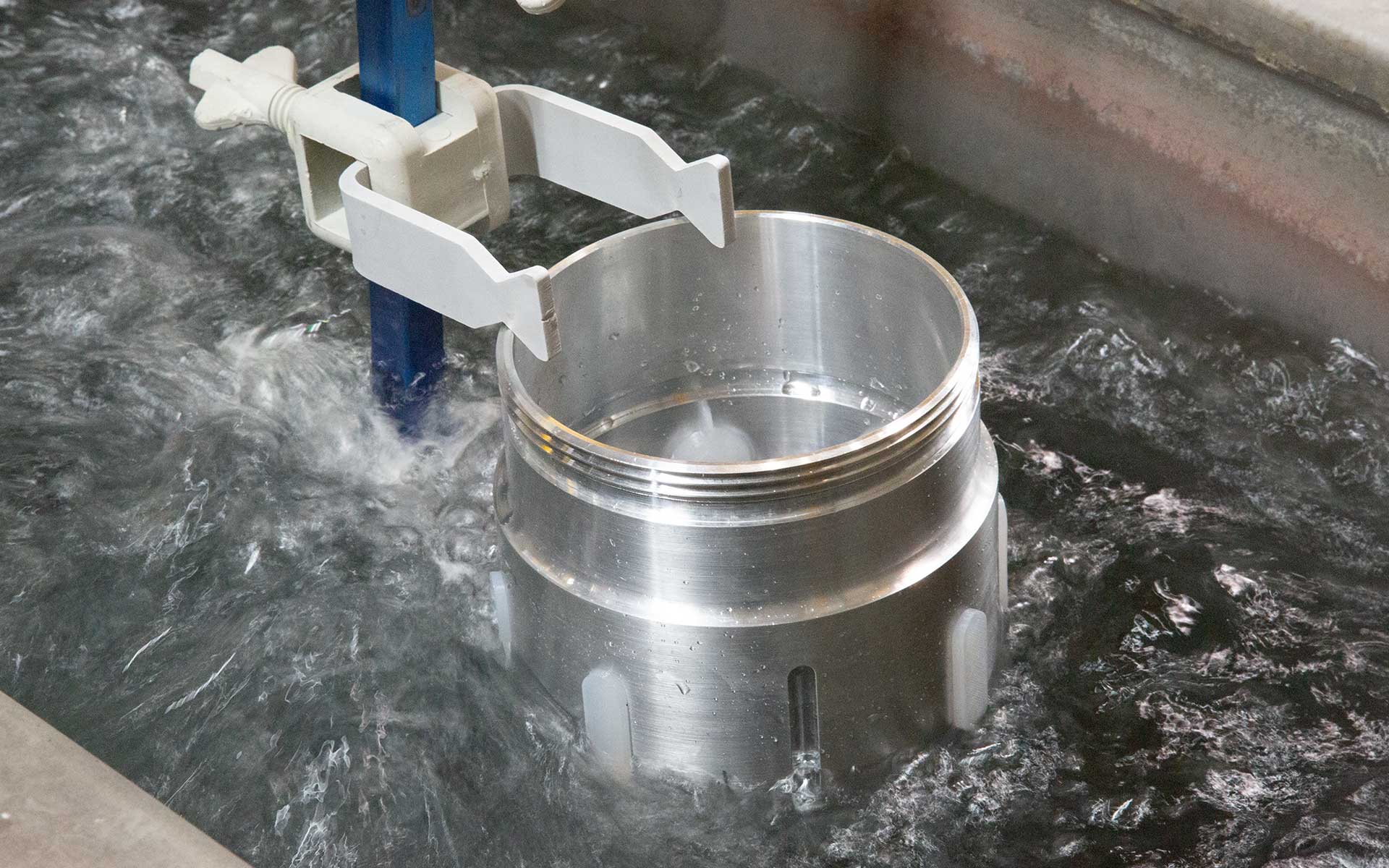
Wet surface treatment
Here are a few benefits of using silicone 3D printer to produce limited series of masks or plugs for wet chemical treatment.
Faster lead time: Silicone 3D printing enables the creation of masks tailored to specific applications, ensuring optimal performance in various geometries and treatment scenarios.
Improved compliance indicators: The flexibility of silicone 3D printed masks ensures superior sealing, preventing leaks and optimizing the efficacy of wet surface treatment.
Improved staff workflow: Silicone masks are easily removed, cleaned, and disinfected, saving time, promoting hygiene and suitability for repeated use.
Gain in flexibility: Silicone’s resistance to various chemicals enhances the durability of the mask, making it apt for a diverse range of wet surface treatments.
Diverse Applications Across Industries
Silicone masking tools find diverse applications across industries such as electronics, aerospace, automotive, and medical devices. These tools are employed to precisely cover and protect specific sections of the part that should not be exposed to the wet chemical etching solution.
In aerospace and automotive manufacturing, they are utilized to safeguard critical metal parts during surface treatments for enhanced performance and durability.
In medical device production, medical coating refers to the application of specialized materials onto medical devices and components to enhance their performance, durability, and safety. Medical coatings serve various purposes, such as improving biocompatibility, reducing friction, preventing infection, enhancing wear resistance, and facilitating drug delivery. Silicone masking tools serve as well as barriers to prevent the application of coatings to designated areas, preserving the original properties or functionality of those regions.
Range of surface treatments on a flange in the aerospace sector
Use case: Surface treatment range on one part
Part: Flange from the aerospace sector.
This part is an example of a flange used in the aerospace sector, serving as a demonstration piece. Developed in collaboration with Spi Aero (Lopitz Group), it showcases a range of complex surface treatments (multi-treatment).
Spi Aero is a recognized player in the field of surface treatment dedicated to the aerospace sector.
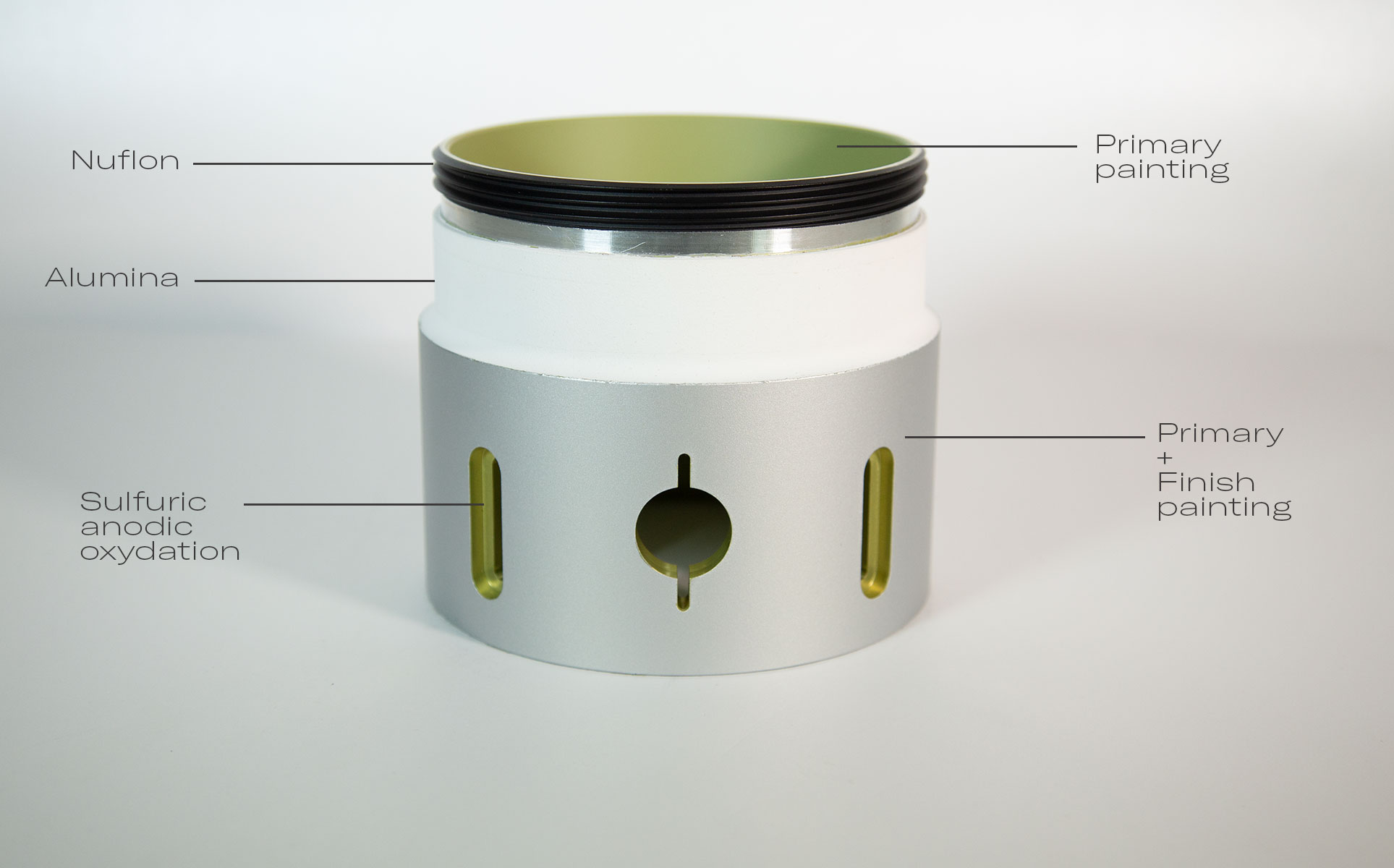
Details of the aspect and processes
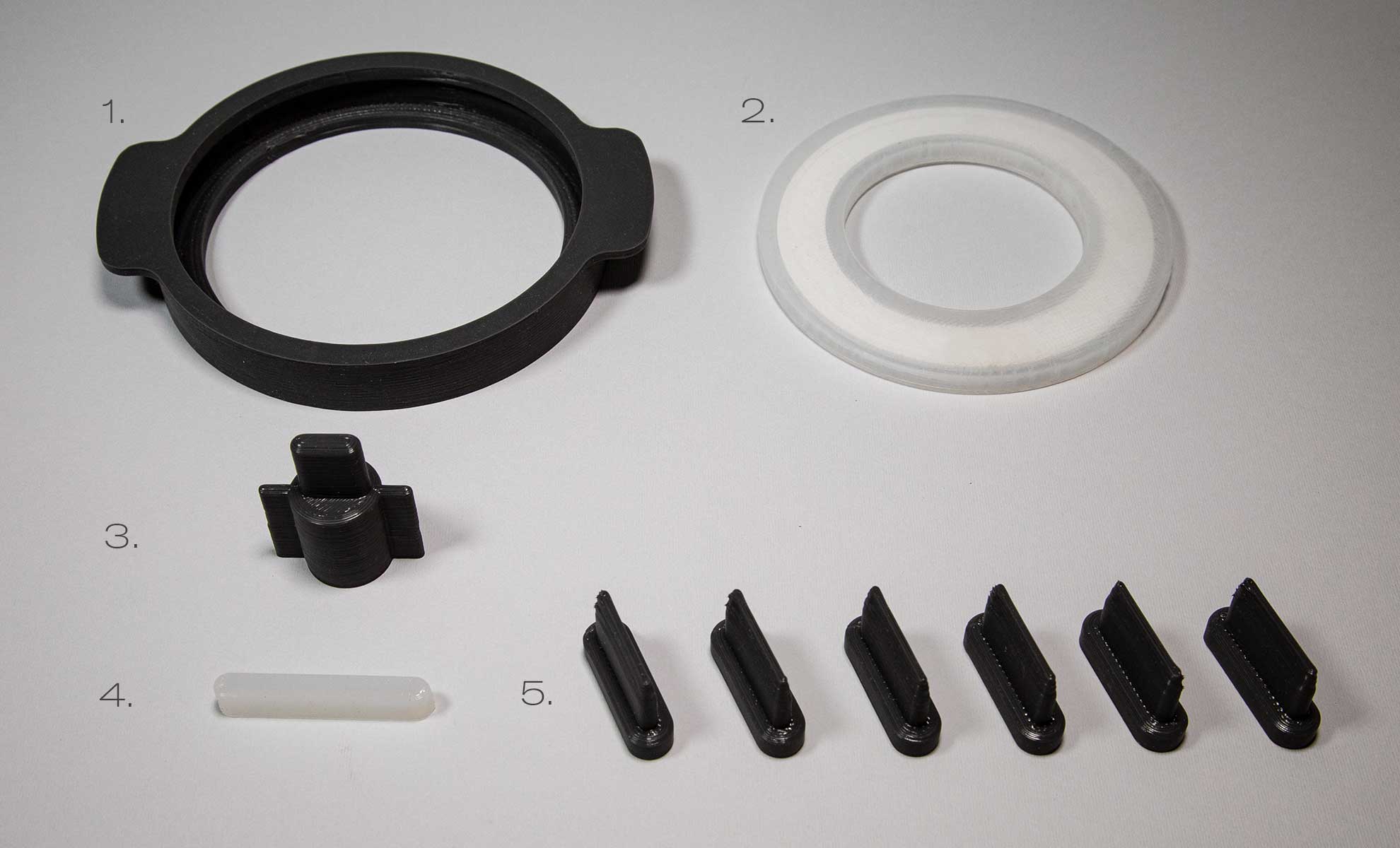
Silicone printed masks 1. Upper zone – 2. Internal groove – 3-4- 5 external cavities
The processes
Multi surface treatment
Step 1 : Dip coating – wet chemical immersion with Spi Aero. OP (operation) 10: Sulfuric anodic oxidation – Areas to be saved during the process: Threading and inner groove. We used the silicone printed disc (2) with inner filling filament to mask this zone.
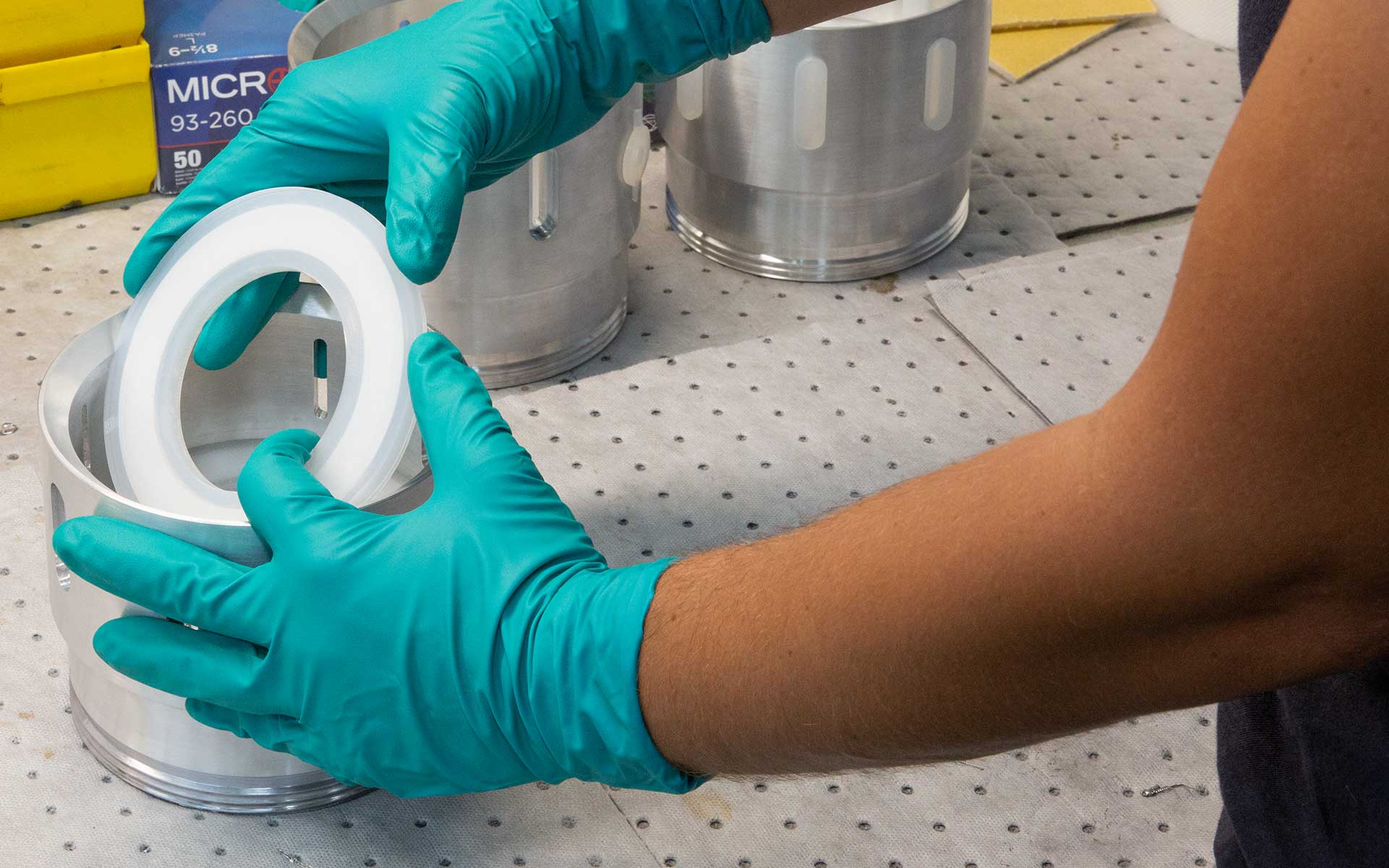
The disk mask (2) is placed in the metal part.
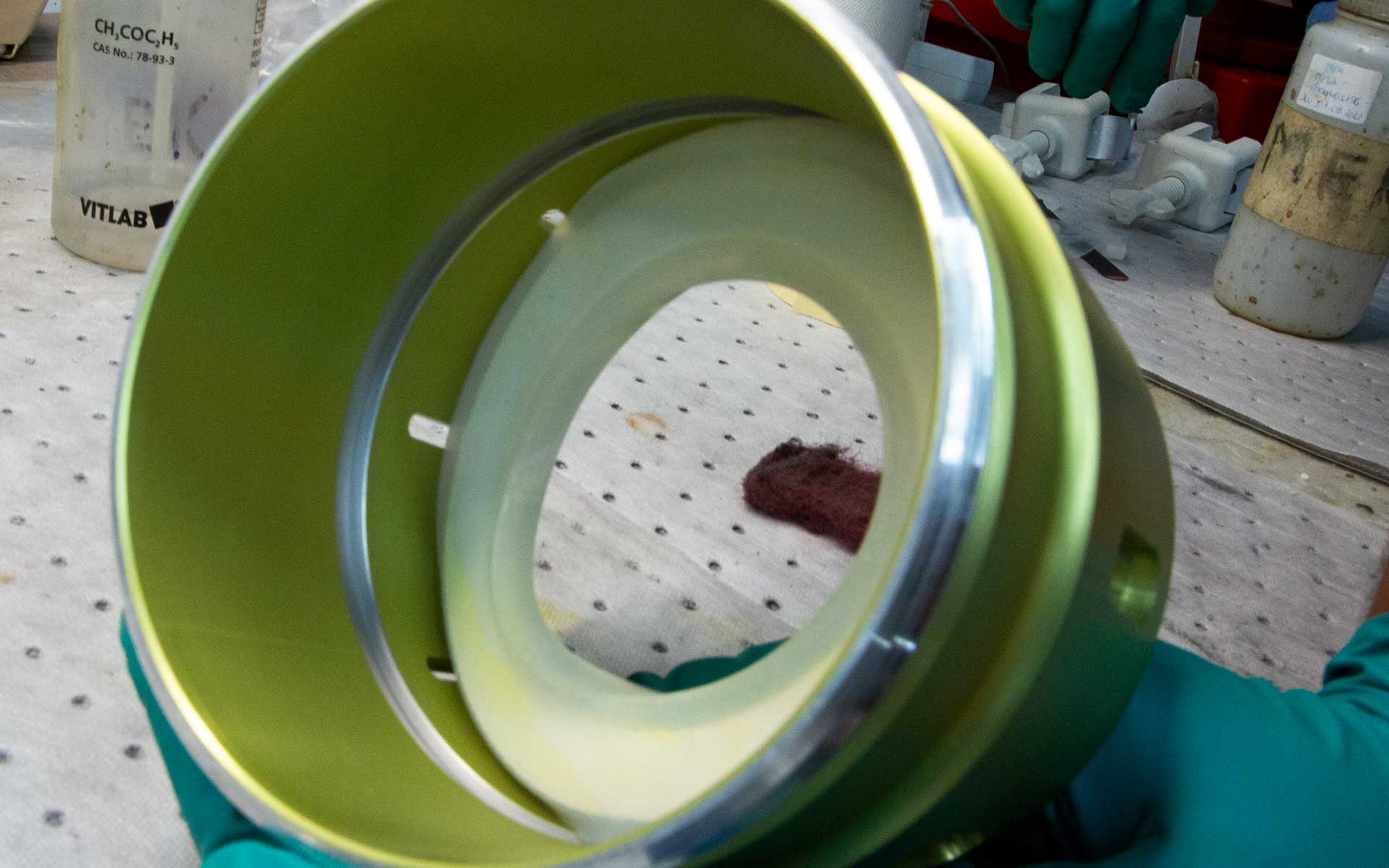
The disc was easily removed before the next process.
Step 2 : Manual Alodine deposition with Spi Aero. OP 20 : Alodine buffer on Zone 6 from the schema. This operation was made manually with a pencil.
Step 3 : Dry coating spraying with Alumina with APS Coating. OP 30: Ceramic Alumina plasma coating Zone A. The rest of the part was easily cover and protected with tapes and mask 1.
Step 4 : Nuflon coating with APS Coating. OP 40: NUFLON TGBT5 spraying with pneumatic or electrostatic gun on Zone B.
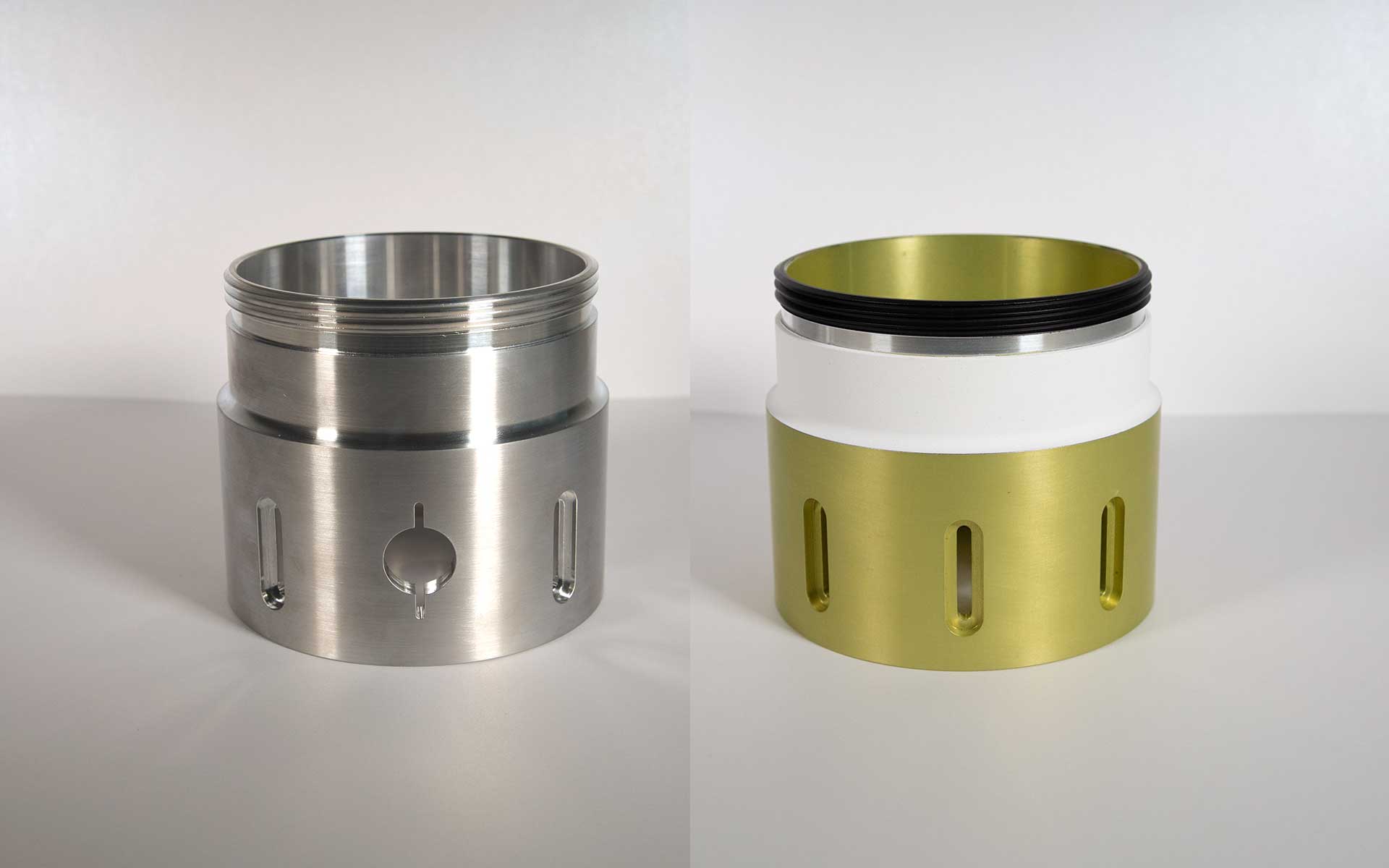
Before and after process up to step 4
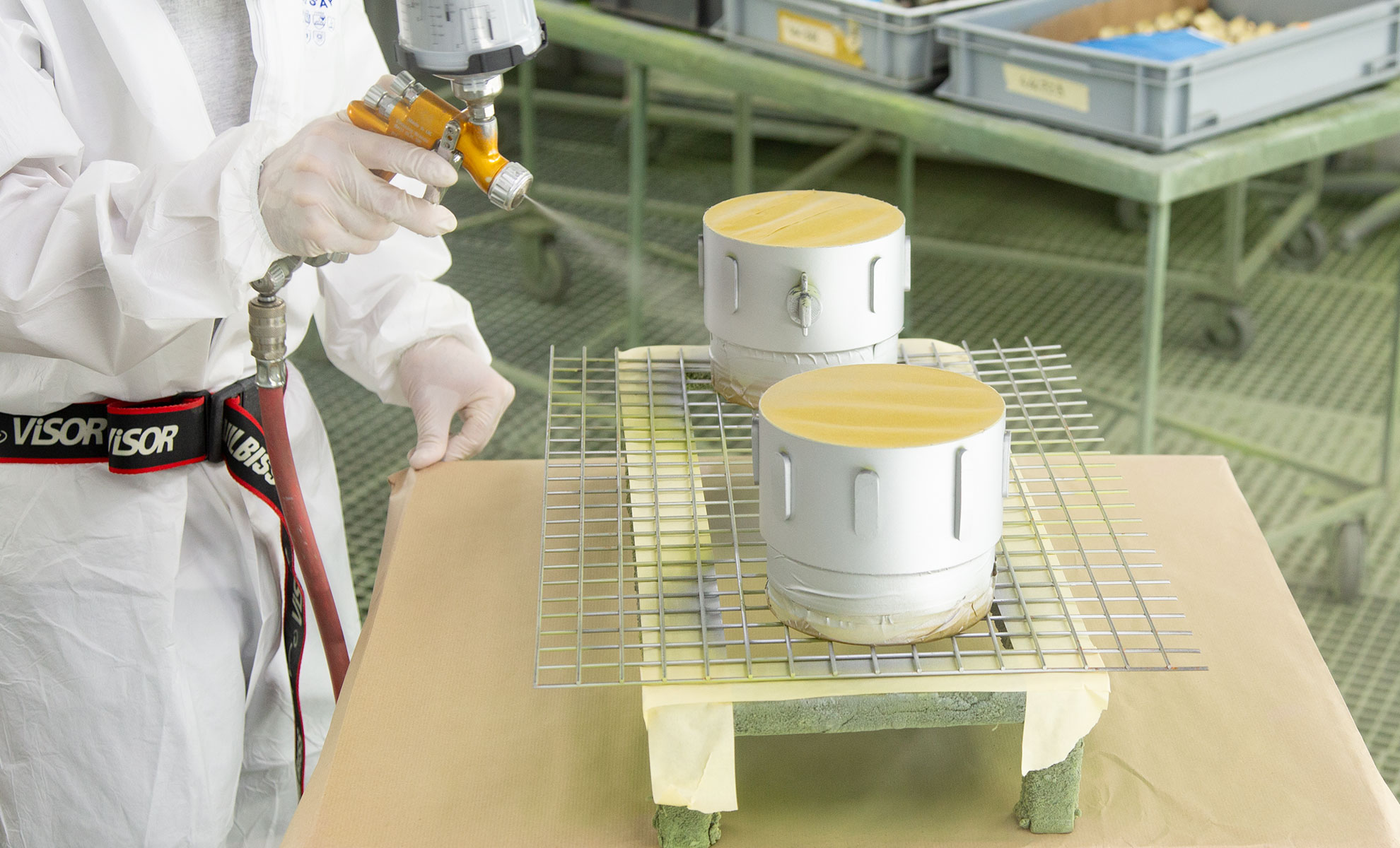
Spraying primary paint (step 5)
Step 5 : Primary Painting with Spi Aero. OP 50: Primary painting gun spray – Spi Aero. Areas to be saved during the process: Inner groove + Threading + Hop holes. We used the silicone printed plugs (3, 4 and 5) to mask those areas during the surface treatment process.
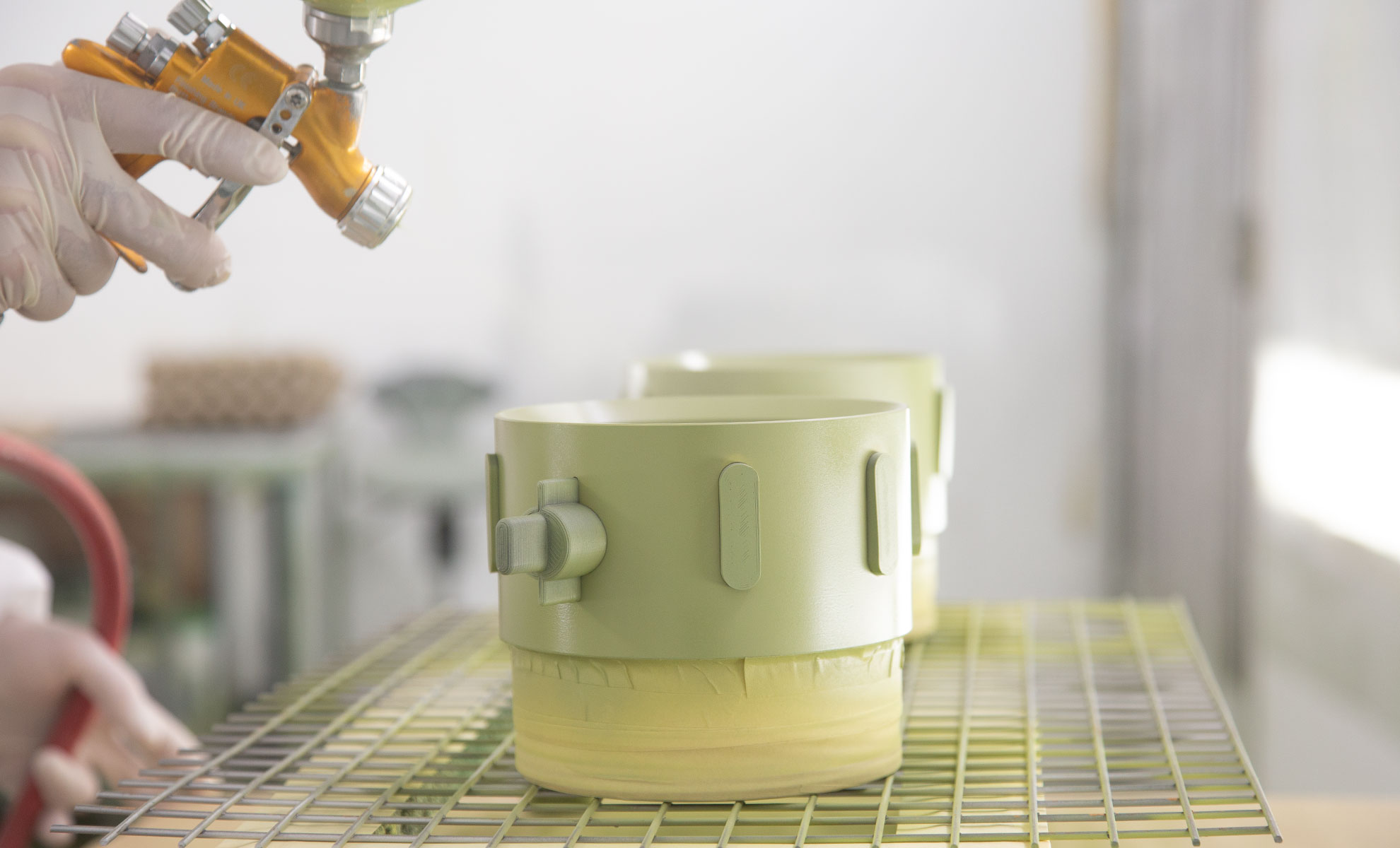
Spraying finishing paint (step 6)
Step 6 : Finish Painting – Spi Aero. OP 60: Finish Painting – Spi Aero on Zone 3. Areas to be saved during the process: Inner groove + Threading + Hop holes. We used the silicone printed plugs (3, 4 and 5) to mask those areas
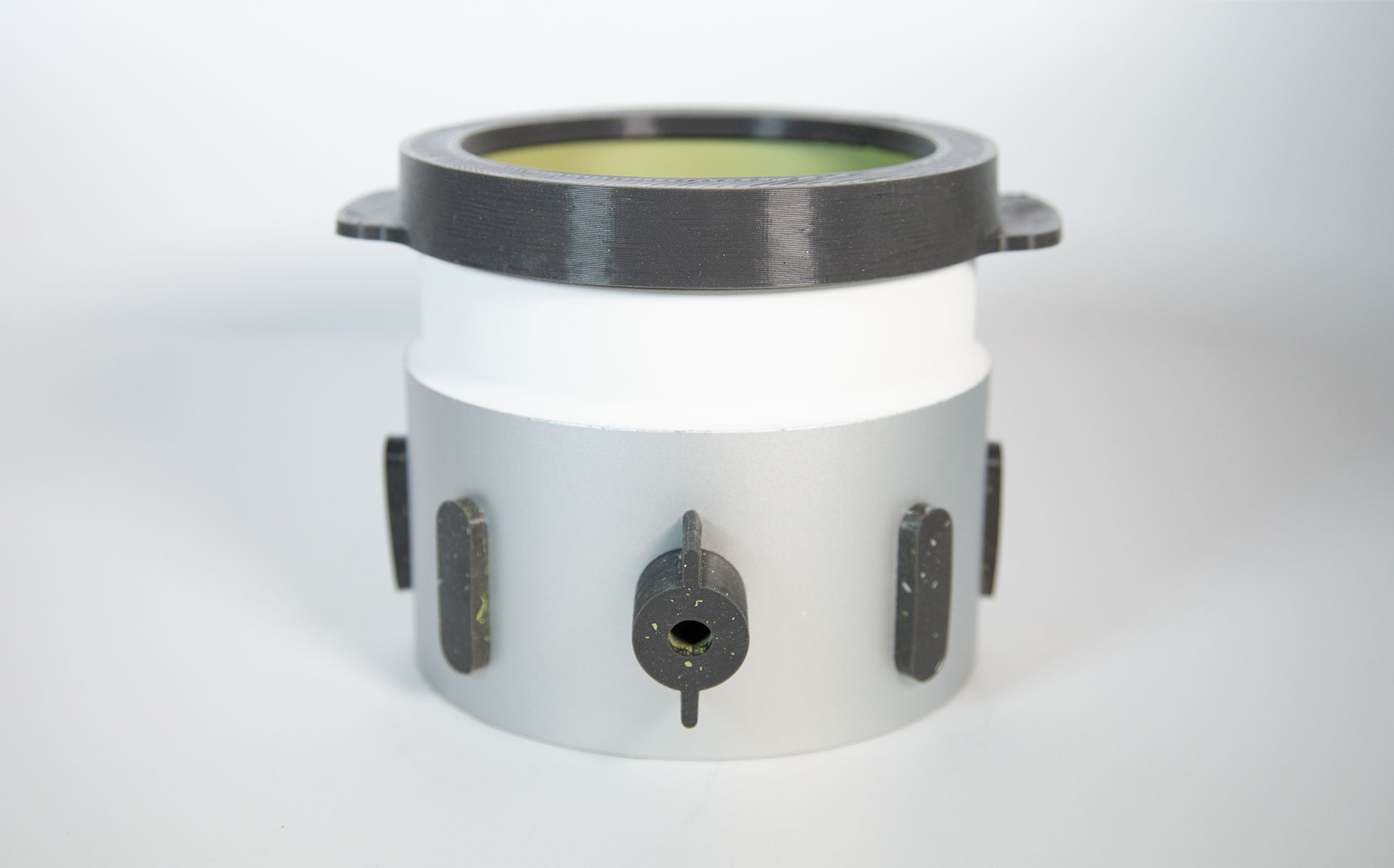
Example of silicone 3D printed mask placement
Key learnings
In conclusion, silicone 3D printed masks stand as revolutionary tools in wet surface treatment, offering unparalleled precision, durability, and versatility across a wide range of applications. The showcased example illustrates the exceptional adaptability of silicone 3D printing, transforming the masking process seamlessly from wet to dry treatments. This not only significantly reduces masking and unmasking time but also capitalizes on hidden time during the printing phase, with tools that are repeatable for certain processes, such as up to five times for plasma spray applications.
As industries seek efficient and reliable solutions, these masks emerge as strategic assets in aerospace, automotive and healthcare. By understanding the strategic advantages and diverse applications of silicone 3D printed masks and plugs, businesses can harness their potential for optimized surface treatment processes, fostering efficiency and innovation.
A big thanks to Spi aero for their support on this project.
Want to lean more about this matter? Contact our team.
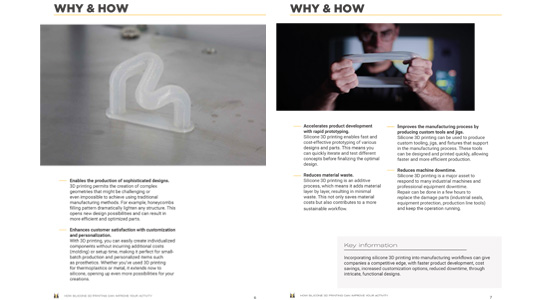
DOWNLOAD THE WHITE PAPER
Download now “Improve your workflow with silicone 3D printing”.
Discover how this new technology can enhance your productivity and innovation.
Don’t miss this opportunity to gain a new competitive advantage.