3D printing of technical Ceramic filament
Definition, application, processes
At Lynxter, we produce ceramic 3D prints in both paste and filament forms. Through CERAMATHS‘ research on Zetamix alumina filaments, we will present in this article how technical ceramics is an essential element in the industry and how its printing leads to cost reduction and time saving.
Ceramic 3D printing is still often associated with artistic creation, between ancient know-how and new technologies.
But ceramics is not only the material of craftsmen and designers, but it is also widely used in industry because it offers properties that are difficult to obtain with metals and plastics.
Definition: What are technical ceramics?
To understand the advantages of ceramic 3D printing, let’s start with the basics, its definition:
Chemically, ceramic is a mineral material that is neither organic nor metallic.
The family of ceramics includes traditional ceramics (clay, stoneware, porcelain) and technical ceramics, also known as “fine ceramics”, which have a crystalline structure. These technical ceramics are intended for industrial applications requiring high performance properties.
Their resistance to high temperatures, abrasion, chemical inertia, and insulating properties (electrical and thermal) makes them particularly suitable for applications in extreme environments.
Major industrial sectors such as aeronautics, space, automotive or health choose industrial ceramics as a raw material.
For example, they can be used to replace a dysfunctional element of the human body (bone substitute, prosthesis, implant) by being biocompatible and chemically stable. Resistant to high temperatures and corrosion, technical ceramics are used, among other things, to make temperature sensors and space protection structures such as ablative materials, battery casings or even the nose of rockets.
They are also used in the automotive industry to improve production with the durability of mechanical components (resistance welding, textile wire guides).
They can withstand temperatures of up to 1700°C and are used, for example, in resistors for high-temperature industrial furnaces in various sectors.
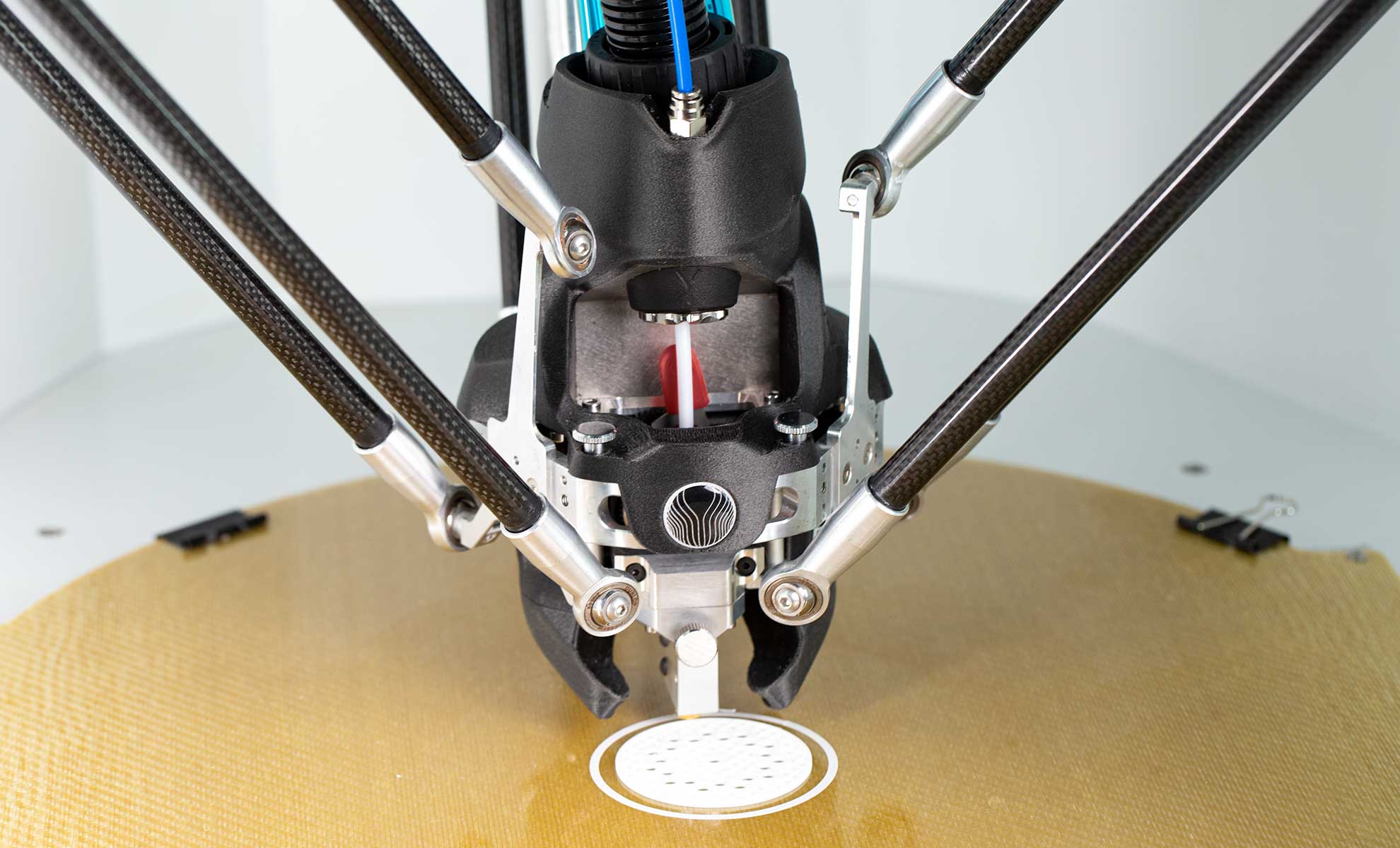
Alumina 3D Printing with Lynxter’s Direct Drive FIL21 toolhead
Ceramics 3D Printing
Now that you are familiar with its use, it is important to understand the process of manufacturing ceramic parts shaped by extrusion of filled filament.
Unlike traditional thermoplastic filaments, 3D printing of ceramic parts differs from printing thermoplastic filaments (PLA, PC, PETG) in several ways:
Firstly, when working with powder-filled filaments (metallic or ceramic) the manufacturing process is indirect: the parts must undergo post-printing treatments before they can be used. These post-treatments require specific equipment, including high temperature ovens.
Another difference, directly linked to the composition of the filaments, lies in the mechanical properties. The conveying and extrusion of a thermoplastic filament is facilitated by its good resistance to bending. However, in the case of filled filaments, the addition of ceramic powder to the filament composition will significantly modify its mechanical properties:
As the filler content of ceramic particles is high to ensure dense objects (generally more than 50% of the volume), the composite filament becomes more brittle and fragile, which makes handling and printing more difficult.
Before being shaped, the filament must be packaged in the form of a spool and then conveyed from the spool to the extruder using a notched wheel/Bowden type conveyor system. During these two stages, the material is subjected to significant bending stresses that can lead to the filament breaking.
3D printing of these brittle filaments is nevertheless possible with direct drive print heads such as Lynxter’s FIL21 toolhead. Combined with our S600D modular 3D printer, the FIL21 can cope with the above constraints and can print many filaments filled with alumina and zirconia powders.
The necessary steps for ceramic 3D printing
1- 3D printing shaping
Additive manufacturing of technical ceramic parts meets the need to produce small quantities or to create parts with complex shapes, quickly.
Available in the form of “charged” and brittle filaments, 3D printing of technical ceramics is possible via MEX (FDM or FFF) fused wire deposition technology if it is associated with a Direct Drive toolhead: by placing the extruder directly above the heating block, and by limiting the radius of curvature, the extrusion is perfectly controlled.
An important step is to inform the right size of the part during 3D printing. Indeed, the ceramic reduces in size during the two following steps (debinding and sintering). It must therefore be printed considering this future shrinkage, of the order of 15% to 20% depending on the thickness.
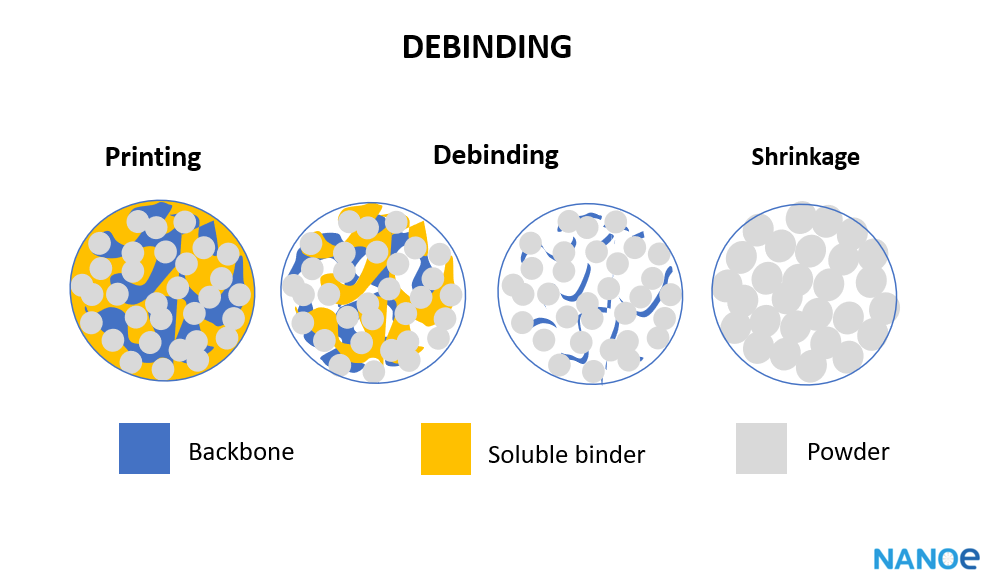
Schema of the debinding from Zetamix-Nanoé ceramic filament
2- Debinding.
The composition of the shaped objects is the same as that of a filament: a polymer binder system associated with ceramic particles.
Once the shaping has been successfully completed, there are two essential stages: debinding and sintering. These post-treatments enable us to obtain dense final parts composed solely of ceramics to present the expected properties.
The purpose of debinding is to remove, to degrade the binder system of the parts (there to allow the shaping of the powder by extrusion). As the binder system is generally composed of a mixture of several polymers, this operation may be carried out in several stages. It can be done in two different ways, chemical or thermal.
– chemical debinding (dissolution, chemical degradation) in the first instance to remove component 1 (soluble binder)
– Thermal debinding: component 2 is burned by exposing it to temperatures above its degradation temperature. (Backbone)
The binder parameters depend on the nature of the binders and the nature of the powder (metallic or ceramic). This step is very important and must be carried out with care so as not to deteriorate the geometries or include impurities. It leads to an initial shrinkage of the part volume.
3- Sintering
The objective of sintering is to densify the part, to create cohesion between the ceramic particles to obtain a dense material with good mechanical properties.
This operation consists of creating links between the grains of powder by the diffusion of atoms under the action of temperature. This has the effect of consolidating the part. Shrinkage is generally observed at the end of this stage.
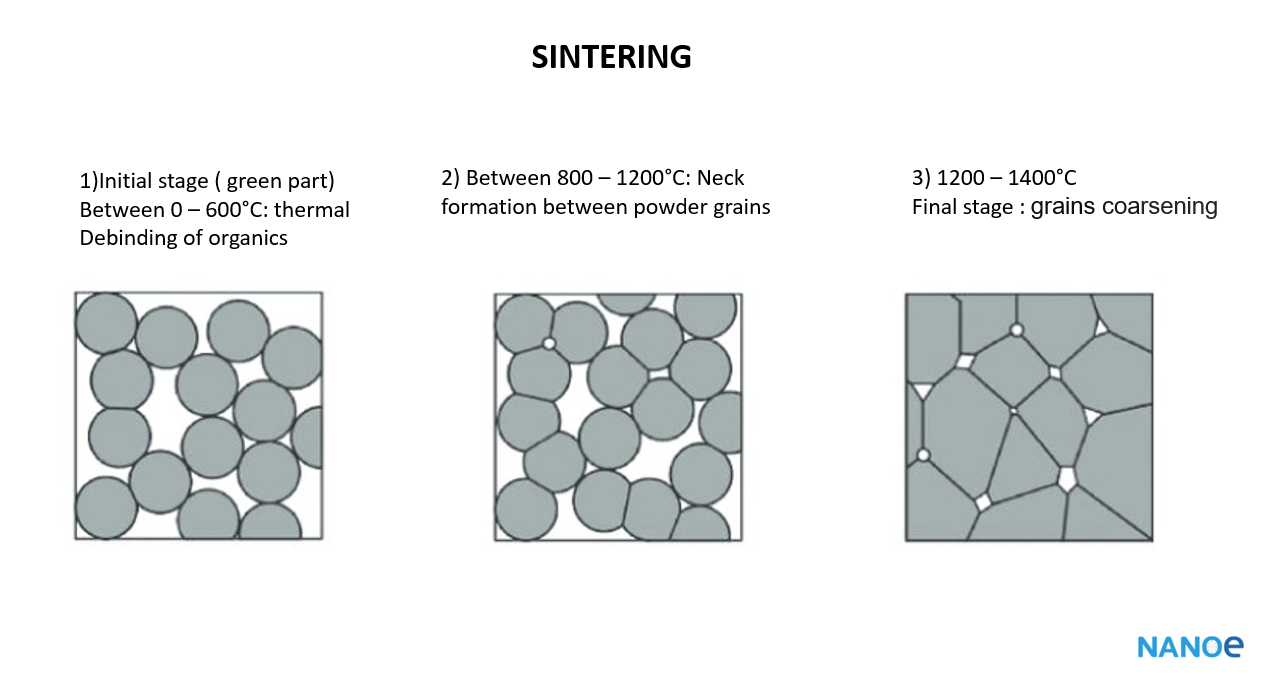
Schema of the sintering from Zetamix-Nanoé
Example: Zetamix Alumina and Zirconia Let’s take the example of Nanoé’s Zetamix filaments, which are composed of ceramic powders and two binders. (Previous diagram) The binders are eliminated between 300°C and 600°C, the sintering will be carried out between 1120°C and 1600°C according to the powders: the alumina of Zetamix is sintered for example at 1550°C and the black Zirconia at 1450°C. |
The choice of sintering furnace is very important and must be made according to the nature of the ceramic being worked on. It must be able to provide the necessary conditions to create the sintering atmosphere required to preserve its technical properties and thus produce the expected properties of the ceramic.
Ceramic 3D printing case study: Ceramath-DMP research
Let’s go further and look at the specific case of the use of technical ceramics by the Department of Materials and Processes, DMP (formerly LMCPA), of the CERAMATHS (Ceramic Materials and Mathematics) laboratory of the Hauts-de-France Polytechnic University.
It specializes in the development of technical ceramics applied to the medical and sustainable development fields.
One of their works concerns additive manufacturing technologies and their interest in the field of health, for the manufacture of synthetic bone implants. These “bio ceramics” are the materials of choice for this type of implant and have biocompatibility and biodegradability properties that favor the natural process of bone regrowth.
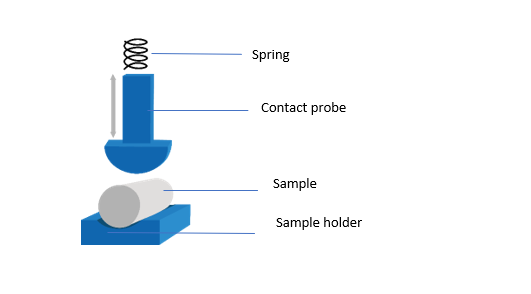
Schema of Ceramath ‘s dilatometric studies
Among the characterization techniques commonly used in the development of these materials are dilatometric studies and thermo-gravimetric analysis (TGA). These two methods provide access to key parameters related to the behavior of materials at temperature: respectively the study of dimensional variation and mass evolution during a thermal cycle.
This complex equipment requires very expensive consumables that must withstand temperature. Technical ceramics are therefore ideal for these applications because of their performance: high temperature resistance, low thermal expansion coefficient and competitive cost (compared to the cost of metallic consumables made of platinum, steel, aluminum, gold, or copper).
Recognizing this potential saving, the laboratory turned to charged filaments and now uses Zetamix zirconia and alumina filaments to produce laboratory consumables and other devices related to their research.
Thermogravimetric analysis crucibles (TGA):
TGA is a technique that measures the change in mass of a sample when it is subjected to a temperature program under a controlled atmosphere. This mass change can be a loss (emission of vapors) or a gain (fixation of gases). The materials under study are placed in a crucible. This part is expensive because of its small size and the technical nature of its production. Its number of uses is limited by the risk of pollution from one material to another (single use recommended). Precise stock management is necessary to avoid the interruption of measurements. For all these reasons, CERAMATHS has chosen to internalize the production of these parts thanks to the 3D printing of Zetamix filaments in order to reduce its costs and gain in responsiveness.
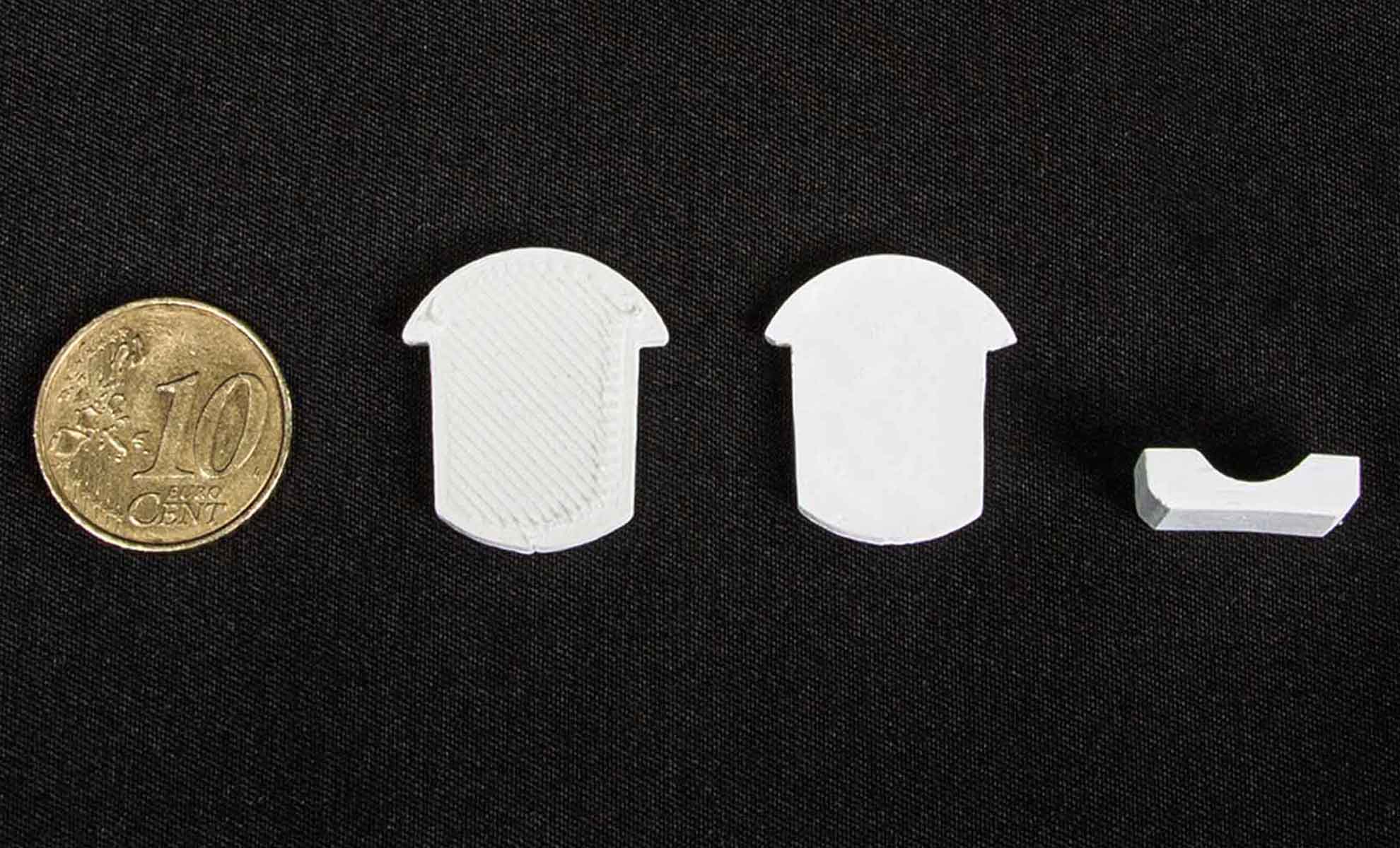
Dialometer parts printed in alumina by the S600D
Consumables for dilatometers :
CERAMATHS-DMP also produces consumables used for the dilatometric study of materials during sintering.
Dilatometry is a powerful analytical technique for determining the dimensional variations of a material as a function of temperature.
In a dilatometry experiment, a sample is placed in a sample holder with one end in contact with a push rod. The displacement of this element over time allows the dimensional evolution of the sample to be determined as a function of temperature.
However, the high temperatures used in this measurement (sintering) can deform or damage the sample holder and rod over time.
To ensure the accuracy, as well as the repeatability, of the analyses carried out, the laboratory regularly replaces these consumables using 3D printing.
The 3D printing of technical ceramics is in full expansion and allows today an improvement of costs and a significant saving of time on the operations where it intervenes (medical, industry, research, and aeronautics).
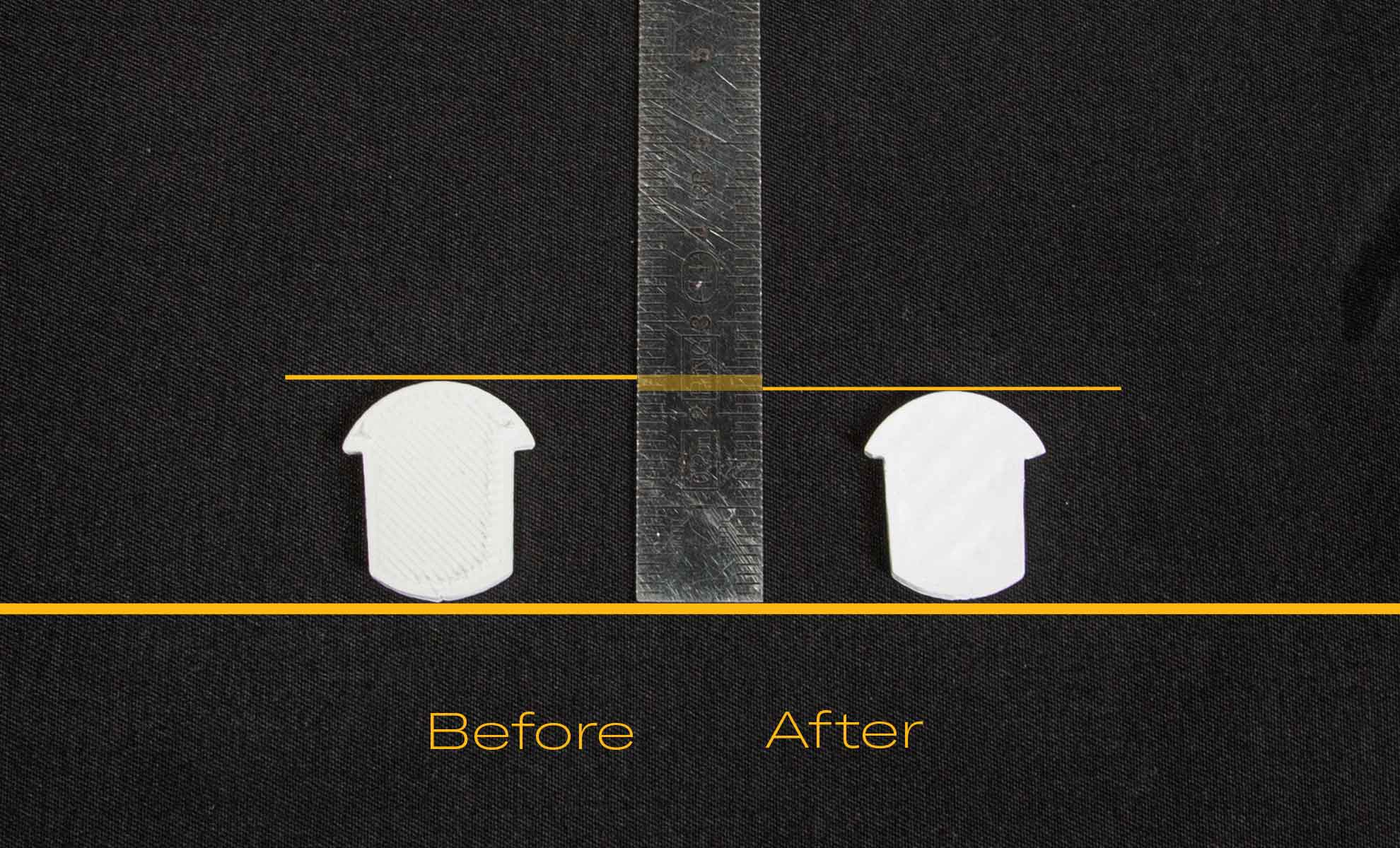
Alumina parts’ sizes before and after debinding
With the FIL21 and the S600D 3D printer, the printing of technical ceramics is done in complete safety, while ensuring high printing speeds and performances. Ceramic filaments (alumina, zirconia) and metal filaments (316L) are already supported, and new references will soon be added to the ecosystem
Technical summary of the case study
SECTOR | University – Research Centre |
APPLICATION | Dilatometer |
MATERIAL | Alumina Zetamix |
DIMENSIONS | 23 mm x 17 mm x 1,2 mm |
PRINTING TECHNOLOGY | S600D 3D printer & FIL21 |
PRINTING TIME | 00H15 |
MATERIAL QUANTITY | 1,56 gr |
MATERIAL COST | 599 €/kg |
COAT HEIGHT | 0,2 mm |
NOZZLE SIZE | 0,4 mm |
PRODUCTION VOLUME | Unit |