Local Layer Splitting: Revolutionizing Soft Pneumatic Actuator Fabrication with Silicone 3D Printing and Robotics
Additive Manufacturing (AM), also known as 3D printing, has gained significant attention in recent years due to its numerous advantages over traditional fabrication methods. One area where Liquid 3D printing (also known as Direct Ink Writing in the research sector and MEX in the industry) is particularly promising is in the production of Soft Pneumatic Actuators (SPAs). SPAs are widely used in the field of robotics and have complex designs that often require flexible materials. Traditional molding fabrication techniques limit the design possibilities and hinder the integration of new features.
In this article, we propose a novel method called Local Layer Splitting (LLS) that revolutionizes SPA fabrication by defining their mechanical properties during the fabrication phase rather than the 3D modeling phase. This method allows for greater design freedom, customization, and control over the mechanical properties of SPAs.
Link to download full paper at the end of this article.
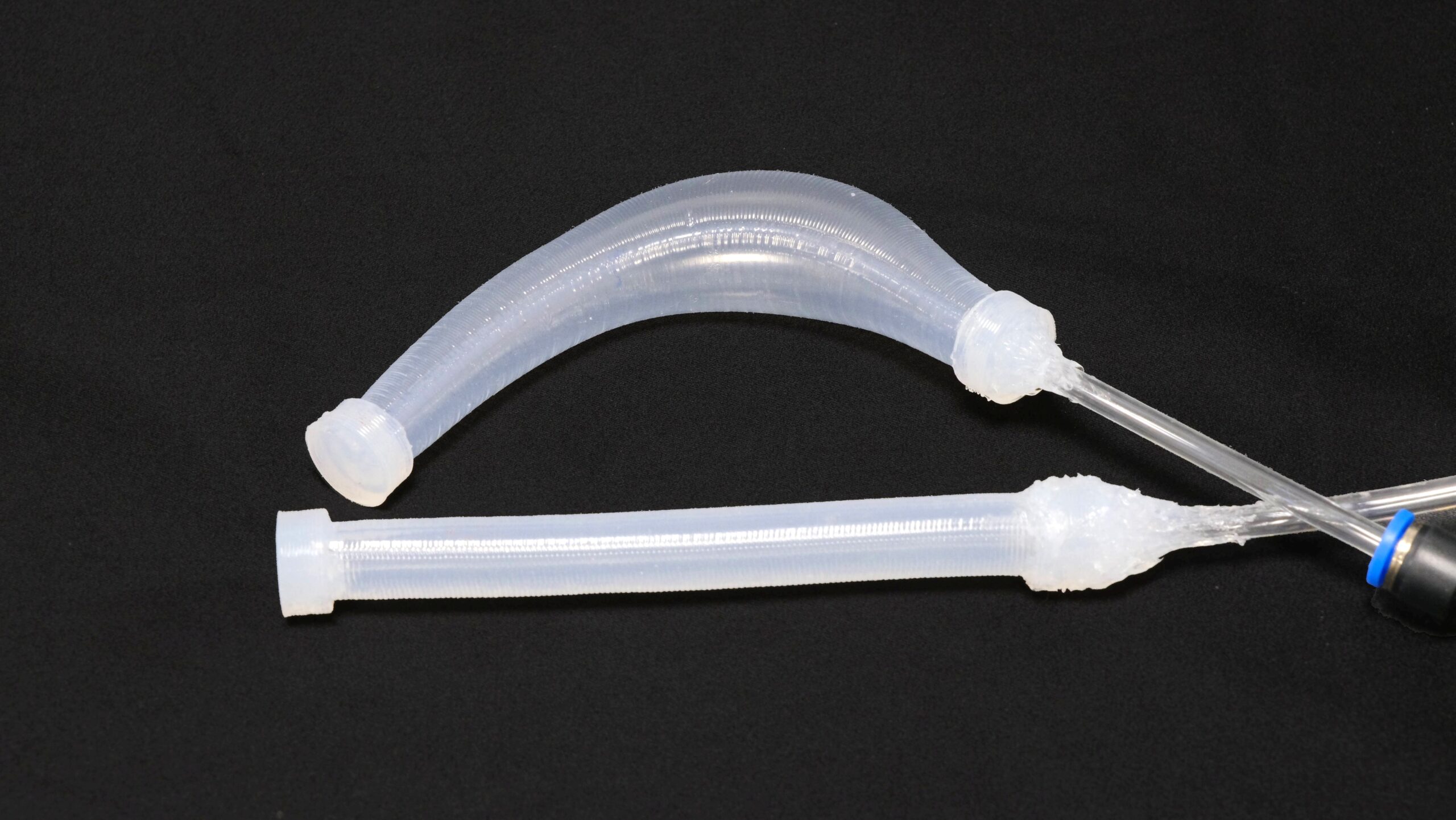
3D printed Soft Pneumatic Actuator using our LLS fabrication technique. (Bottom) The actuator shape is unaltered when non-pressurized. (Top) The actuator bends when pressurized.
Local Layer Splitting: The Fabrication Method
The LLS fabrication method introduces a local variation in the layer height of the 3D-printed silicone, which in turn creates non-uniform anisotropic mechanical properties in SPAs. Unlike traditional additive manufacturing processes, where the layer height remains constant throughout the entire printing process, LLS allows for different layer heights within a single layer.
This technique affects the stiffness of the printed silicone walls locally, resulting in controlled mechanical deformation when pressured. The mechanical properties of the SPA are defined during the fabrication phase, making them independent of the object’s aspect. This approach opens up new possibilities for creating SPAs with diverse bending behaviors without modifying the 3D model.
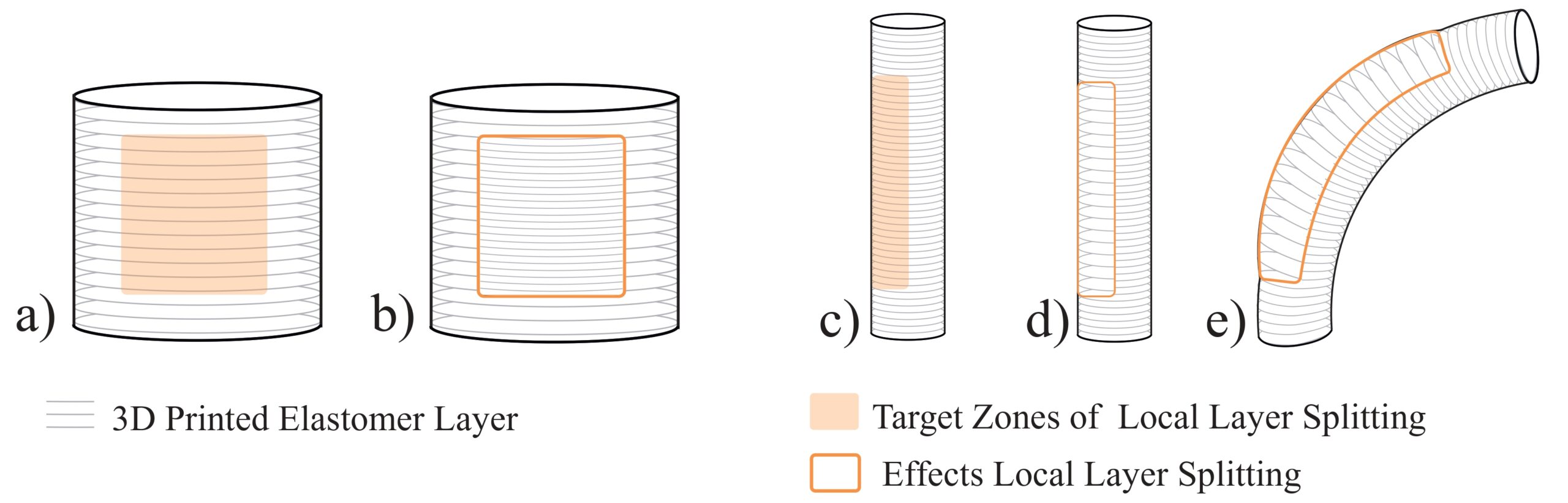
Illustration of LLS technique. (a) A 3D printed part, the orange area, is the target of LLS. (b) The framed area shows the effect of LLS, leading to a different layer height. (c) Cylindrical illustration of a SPA with a target zone of LLS. (d) The effect of LLS in the relaxed state and (e) shows the actuator in an inflated state.
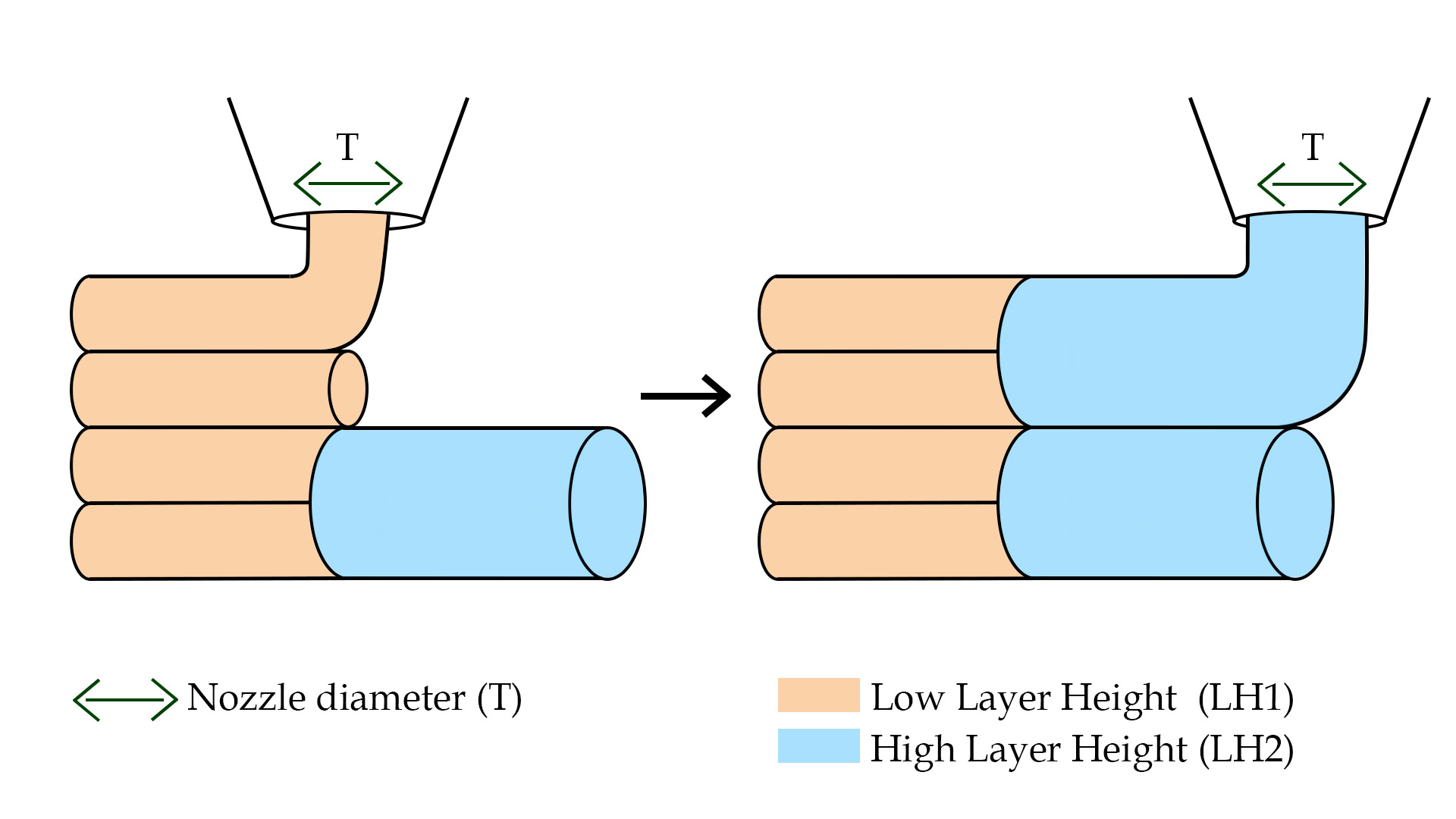
Illustration of the LLS 3D printing process.
To validate the LLS method, we conducted several experimental tests. First, we evaluated the impact of layer height parameters on the stiffness of 3D-printed silicone through tensile tests. The results showed that the layer height directly affects the tensile stiffness of the material. We also developed a custom slicer to generate G-codes with local layer height variations, enabling the integration of LLS into the fabrication process.
We then fabricated cylindrical SPAs using the LLS process and evaluated their bending angles and blocked forces under varying internal air pressure. The results demonstrated that LLS-enabled SPAs achieved significant bending angles and exhibited comparable performance to state-of-the-art SPAs. The bending behavior could be precisely controlled by adjusting the layer height and nozzle diameter.
Revolutionizing Soft Pneumatic Actuator Fabrication with Silicone 3D Printing and Robotics
Impact and Applications of LLS
The LLS technique offers numerous opportunities for SPA design and fabrication. By decoupling the mechanical properties from the object’s design, LLS allows for iterative design and customization of SPAs. The fabrication process is fully automated, saving time and reducing errors. We presented two examples to illustrate the potential applications of LLS: a three-finger gripper and an actuator with multiple bending behaviors. The three-finger gripper demonstrated its grasping capabilities, while the actuator showcased the complex mechanical possibilities enabled by LLS.
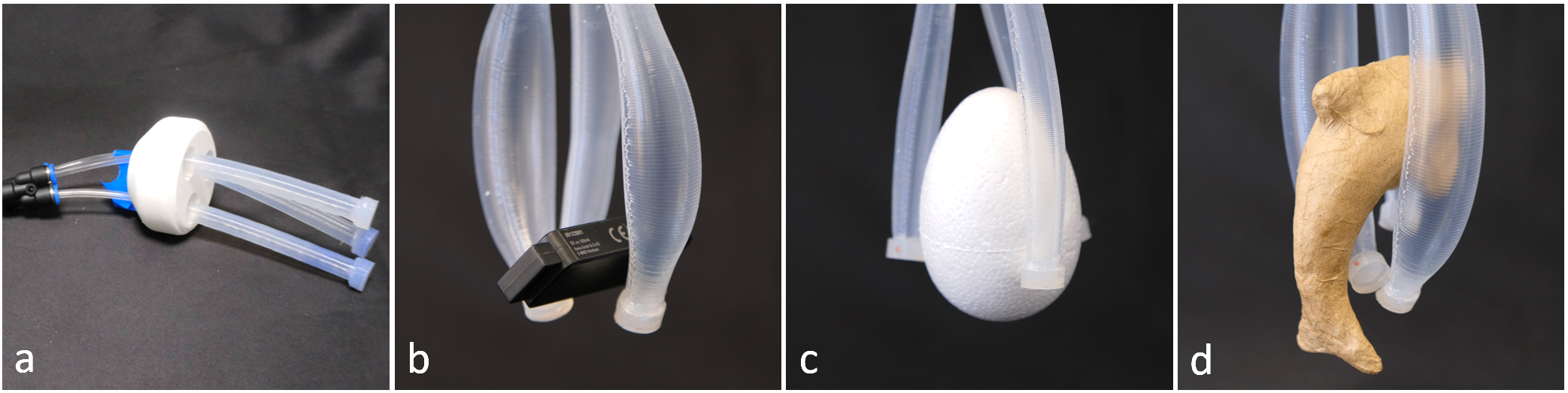
Three-finger gripper grasping test. (a) Two fingers have a nozzle diameter T= 0.86mm and the last T= 0.69mm to deliver increased strength, thus simulating a thumb. The gripper demonstrated his handling potential of objects; (b) a USB key (25.4g), (c) a polyester egg (8.6g), and a cardboard miniature (36.7g).
Discussion and Future Work
The LLS method represents a significant advancement in SPA fabrication, offering greater design flexibility, customization, and control over the mechanical behavior of SPAs. However, there is still room for further exploration and improvement.
Future work includes exploring additional additive manufacturing control parameters, optimizing the custom slicer for user-friendly operation, and investigating other SPA shapes and infill variations. By continuing to refine and expand the LLS technique, we can unlock even more possibilities for innovative SPA designs and applications.
In conclusion, the LLS method presents a novel approach to fabricating SPAs with defined mechanical properties during the fabrication phase. By integrating local layer height variations, SPAs can exhibit controlled mechanical deformation and anisotropic properties. The LLS technique offers greater design flexibility, customization, and control over the mechanical behavior of SPAs.
It represents a significant step towards unlocking the full potential of additive manufacturing in the field of robotics. With further development and exploration, LLS has the potential to revolutionize SPA fabrication and pave the way for new advancements in soft robotics.
Download the full and detailed paper here :