Aeroacoustic research using 3D printing
Scientific research may require the use of wind tunnel models for experiments. These models must meet criteria of size, precision, surface quality and strength. 3D printing has become an essential tool in this process to speed up scientific research, enabling researchers to produce complex prototypes more quickly and at lower cost, while improving their flexibility and operational efficiency.
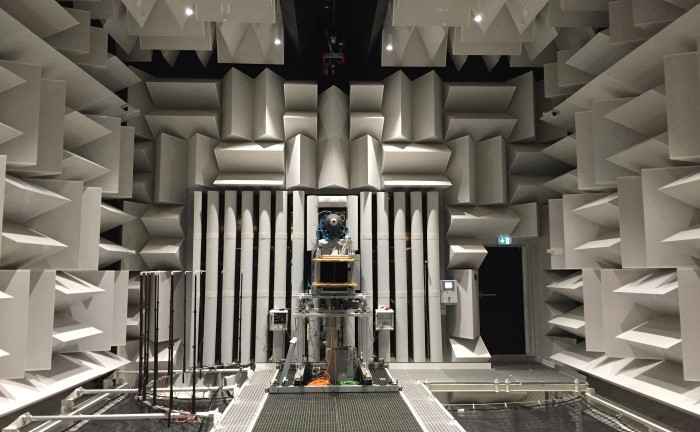
Inside the anechoic chamber at École Centrale de Lyon – source: École Centrale de Lyon
OPTIMISING PROPULSION AND ENERGY: WIND TUNNEL EXPERIMENTS
The Fluid Mechanics and Acoustics Laboratory (LMFA) at the École Centrale de Lyon is a joint CNRS unit (UMR 5509) specializing in research into acoustics, complex fluids and transfer, turbomachinery, turbulence, and stability. It is one of the main components of the Labex CELYA (Centre Lyonnais d’Acoustique) and focuses on the generation of noise by flows (bearing surfaces, jets) and the propagation of sound in inhomogeneous media.
The aim of the experimental wind tunnel work is to use this data to look at the validation of analytical modelling and numerical simulations. Ultimately, as part of an overall strategy to support major transitions, the aim is to reduce the environmental impact of complex systems. This involves not only reducing fuel consumption by optimizing lift, but also reducing noise pollution.
The school’s Acoustics Centre has around 20 permanent staff and an equivalent number of doctoral and post-doctoral students. It has two high-speed open vein wind tunnels (Mach<1.6) leading into a sound chamber.
Over several decades, the Acoustics Centre has established numerous collaborations with academic and industrial partners in the field of airfoils and blowers. The Fluid Mechanics and Acoustics Laboratory at the Ecole Centrale de Lyon has decided to invest in new manufacturing technologies to optimize wind tunnel studies of aerodynamic noise phenomena, to meet its quality and responsiveness requirements and respond to institutional and industrial calls for tender.
3D printing is an innovative method used in many high-tech disciplines. Its customizable and adaptable nature means that it should be widely used in research and development. It shortens the time between the development of a design, its manufacture, and its use in the wind tunnel.
Printing of the NACA profile supporting a distributed propulsion system for the CLEAN SKY project – here printed in PLA for form validation
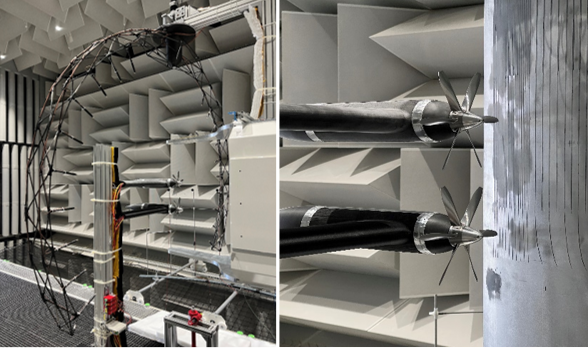
Test bench at the outlet of the subsonic aeroacoustics wind tunnel at the École Centrale de Lyon.
ACCELERATING SCIENTIFIC RESEARCH WITH 3D PRINTING
Acoustics is an area of research where the production of complex prototypes is essential. However, traditional manufacturing methods can be costly and inflexible in terms of lead times. To meet these needs, the Acoustics Centre at École Centrale de Lyon has collaborated with LYNXTER to evaluate the dimensional and structural performance of different materials that can be printed on the S600D 3D printer.
The positive impacts of integrating the 3D printer as a tool into the processes were validated, particularly in terms of manufacturing time, suitability to requirements and economic performance.
Printing models for installation in wind tunnels has become standard practice in the Acoustics Centre’s research activities. Increasingly complex models cannot necessarily be produced using traditional machining methods, and the cost and time involved in machining them can be an obstacle to the smooth running of projects. The budget spent on producing these machined models can quickly run into the thousands of euros, while the investment in an industrial 3D printing solution and the recruitment of an additive manufacturing operator-technician quickly pays for themselves.
Pascal Souchotte, Doctor – Acoustics Engineer, talks to us about the benefits of the S600D in his work.
“Using the S600D 3D printer to manufacture parts now enables us to respond quickly and efficiently to our needs, from simple parts to complex 3D models representing standardized aerodynamic profiles. This solution also gives us the flexibility to adapt parts to the size of our wind tunnel, as well as a varied choice of materials for the profiles. What’s more, the precision of the production process is fully compatible with our requirements.
Since integrating this technology, we have seen
– Greater responsiveness in the manufacture of models
– Greater precision
– Less sub-contracting.
By integrating this technology, we are consolidating our know-how, gaining better control of our costs and lead times, and improving our operating flexibility compared with the traditional model based on subcontracting. From design to manufacture of models, this solution offers considerable advantages for our industrial research activity.”
PLA printed propeller prototype (shape validation)
RESEARCH FOR THE CLEAN SKY AND PIBE PROGRAMMES
3D PRINTING OF NACA PROFILES TO OPTIMISE AERODYNAMIC PERFORMANCE
As part of the Clean Sky programme, the Fluid Mechanics and Acoustics Laboratory is carrying out studies aimed at reducing the fuel consumption of aircraft such as aeroplanes, drones and helicopters, as well as the noise pollution they cause, by studying propeller assembly.
For this experiment, the Laboratory used 3D printing to produce a model supporting the distributed propulsion system. The fuselages supporting the propellers were printed using Lynxter’s S600D, which is capable of printing numerous profiles and large sizes.
The fuselages are made up of several shells in carbon-filled nylon, with cable passages and specific instrumentation, as well as two aerodynamic thrust balances to guarantee structural strength and a surface finish compatible with the requirements of the project.
The main part of the model is a NACA airfoil, with a wingspan of 560 mm and a chord of around 200 mm. The manufacture of the various parts of the model took around 2 days, followed by a day’s finishing work to finalise the surface finish and the positioning of inserts, before assembly including cable routing and the positioning of the propellers. The assembly was then placed in a wind tunnel, where it was subjected to an airflow with a maximum speed of around 100 m/s, or 360 km/h.
The wind tunnel tests were carried out at the end of 2022, with a number of configurations varying the speed of the incident airflow and the speed of rotation of the propellers up to 7,000 rpm, as well as the position of the propellers in relation to the load-bearing structure consisting of the aluminium wing.
The initial results are very promising and constitute a unique database. Interpretations are in the process of being published scientifically, and a presentation will be made at the AIAA Congress in San Diego in June 2023.
Thanks to its versatility, openness (numerous profiles) and printing capacity (size), the S600D is a very interesting solution for research carried out in the laboratory.
Printing information:
SECTOR | Industrial – Aeronautics |
APPLICATION | Wind tunnel propeller support |
MATERIAL | Carbon-filled nylon |
DIMENSIONS | 560 mm x 400 mm x 100 mm |
PRINTING TECHNOLOGY | MEX (FF/FDM) S600D FIL21 |
PRINTING TIME | 2j for the 4 assembly parts |
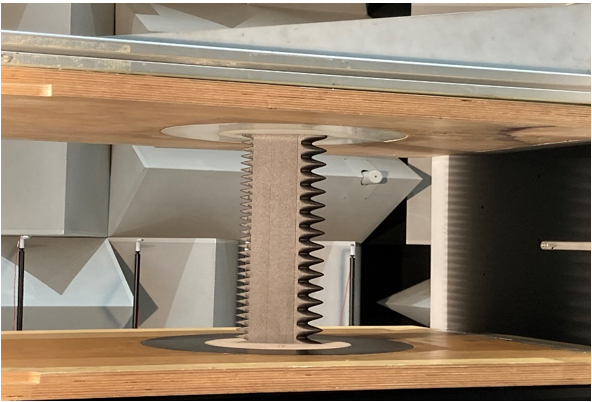
Model of a wind turbine blade optimised to reduce the noise generated by dynamic stall. – source : École Centrale de Lyon
3D PRINTING TO REDUCE NOISE FROM WIND TURBINES
The Fluid Mechanics and Acoustics Laboratory has used the S600D 3D printer as part of the national PIBE programme, which aims to improve methods for predicting the noise impact of wind turbines.
The aim of this study is to reduce the effects of dynamic stall on wind turbine blades. This phenomenon leads to acoustic repetitions that can disrupt the noise environment of wind farms and affect the quality of life of local residents. To minimise this nuisance, the sound of wind turbines must be continuous and almost imperceptible.
3D printing offers a rapid solution for testing different prototype shapes aimed at solving this problem. The ability to produce models in near-real time means that trends observed during tests can be considered. In this study of the wind turbine blade, several leading-edge corrugation and trailing edge serration profiles were produced over the course of the nightly tests, depending on the results obtained the previous day. Another significant advantage of 3D printing is the ability to manufacture objects with very complex shapes in masked time.
Printing information:
SECTOR | Industrial |
APPLICATION | Prototype wind turbine blade models |
MATERIAL | Carbon-filled nylon |
DIMENSIONS | 400 mm x 100 mm x 15 mm |
PRINTING TECHNOLOGY | MEX (FF/FDM) S600D FIL21 |
PRINTING TECHNOLOGY | 10 h / part |
3D printing has proved to be an essential tool for research into aeroacoustic wind tunnels, particularly within the Fluid Mechanics and Acoustics Laboratory at the École Centrale de Lyon. This technology makes it possible to produce complex prototypes more quickly and at lower cost, while improving their quality and strength. 3D printed models also meet researchers’ needs for flexibility and operational efficiency, by speeding up production times and reducing costs. 3D printing is therefore a promising solution for optimising scientific research and contributing to the achievement of major environmental transitions.