L’impression 3D de céramique technique en filament
Définition, application, procédés
Chez Lynxter, nous réalisons des impressions 3D céramiques sous forme de pâtes mais aussi sous forme de filaments. A travers les recherches de CERAMATHS sur les filaments alumine de Zetamix, nous présenterons dans cet article comment la céramique technique est un élément essentiel dans l’industrie et comment son impression entraine une réduction des coûts et un gain de temps précieux.
L’impression 3D céramique est encore souvent associée à la création artistique, une rencontre entre le savoir-faire ancestral et les nouvelles technologies. Mais la céramique n’est pas seulement le matériau des artisans et designers, Elle est aussi largement utilisée dans l’industrie car elle offre des propriétés difficilement atteignables par les métaux et les plastiques.
Définition : Qu’est-ce que la céramique technique ?
Pour comprendre les avantages de l’impression 3D céramique, commençons par la base, sa définition :
Chimiquement la céramique est un matériau minéral qui n’est ni organique, ni métallique.
Dans la famille des céramiques, on compte les céramiques traditionnelles (argile, grès, porcelaine), et les céramiques techniques, qu’on nomme aussi « céramiques fines » qui possèdent une structure cristalline. Ces céramiques techniques sont destinées aux applications industrielles nécessitant des propriétés hautes performances.
Leurs résistances à de hautes températures, à l’abrasion, leurs inerties chimiques, ou encore leurs caractéristiques isolantes (électriques et thermiques) les rendent particulièrement adaptées aux applications dans un environnement extrême.
C’est pourquoi des secteurs majeurs de l’industrie comme l’aéronautique, le spatial, l’automobile ou bien la santé font le choix des céramiques industrielles comme matière première.
Par exemple elles permettent de remplacer un élément dysfonctionnel du corps humain (substituts osseux, prothèses, implants) en étant biocompatible, et stable chimiquement. Résistantes à de fortes températures et à la corrosion, les céramiques techniques servent entre autres à réaliser des capteurs de températures et des structures de protection spatiales telles que les matériaux ablatifs, les carters de batteries ou bien même le nez des fusées. L’automobile les utilise aussi pour améliorer sa production et la durabilité de ses éléments mécaniques (soudage par résistance, guide de fils textile).
Pouvant supporter des températures jusqu’à 1700°C, elles composent par exemple les résistances de four hautes températures industriels dans divers secteurs.
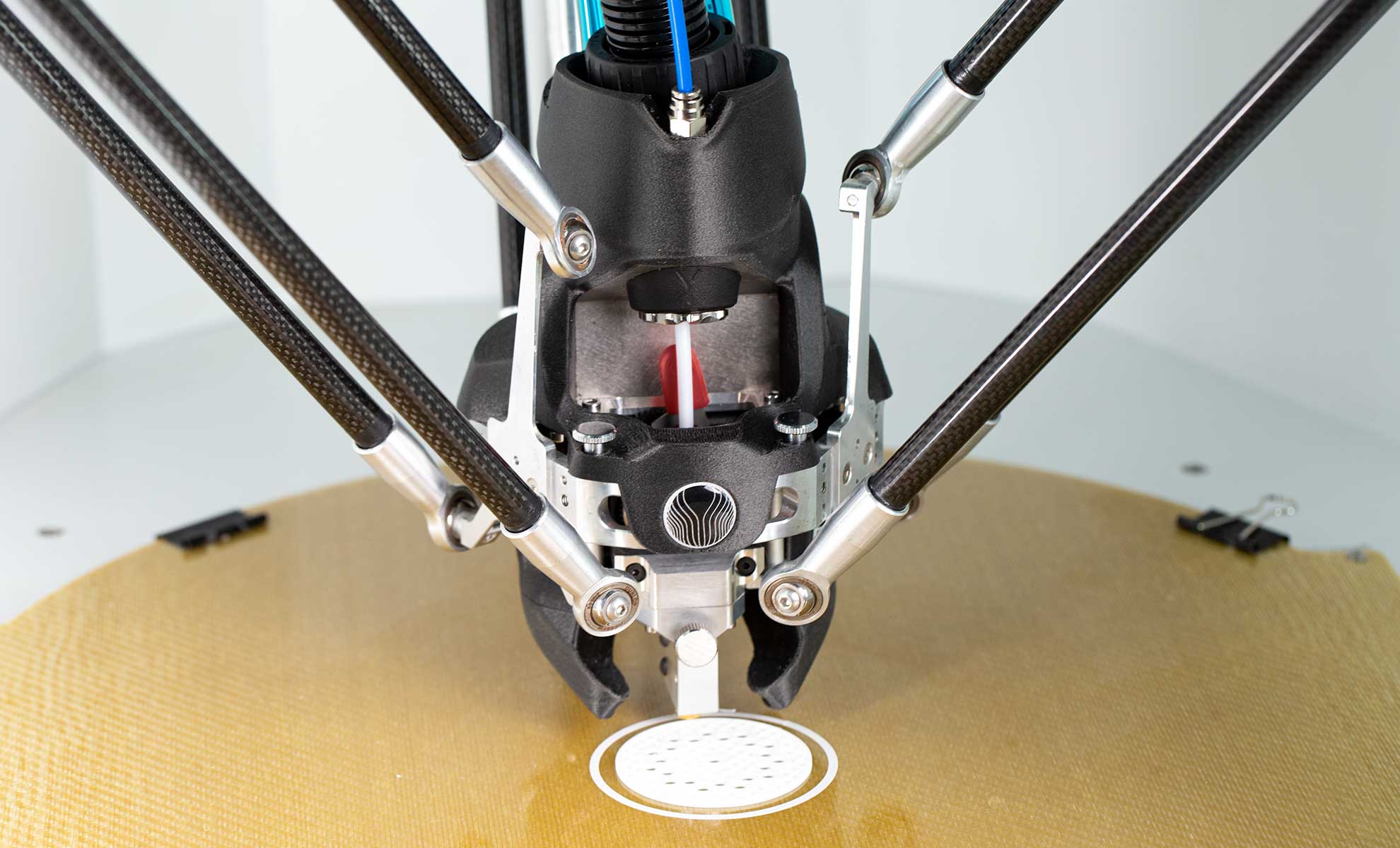
Impression de filaments chargés alumine par la tête-outil Direct Drive FIL21 de Lynxter
L’impression 3D de la céramique
Maintenant que vous connaissez son utilisation, il est important de comprendre le procédé de fabrication de pièces céramiques mises en forme par extrusion de filament chargé.
Contrairement aux filaments thermoplastiques traditionnels, la mise en forme par impression 3D de pièces céramiques se différencie de l’impression de filaments thermoplastiques (PLA, PC, PETG) en plusieurs points :
Tout d’abord, lorsque l’on travaille avec des filaments chargés en poudre (métallique ou céramique) le procédé de fabrication est indirect : les pièces doivent subir des traitements post impression avant de pouvoir être utilisées. Ces post traitements nécessitent des équipements spécifiques parmi lesquels on peut citer des fours hautes températures.
Une autre différence, directement liée à la composition des filaments, réside dans les propriétés mécaniques. Le convoyage et l’extrusion d’un filament thermoplastique sont facilités du fait de sa bonne résistance à la flexion. Cependant dans le cas des filaments chargés, l’ajout de poudre céramique dans la composition filament va sensiblement modifier ses propriétés mécaniques :
Le taux de charge en particules céramiques étant élevé pour garantir l’obtention d’objets denses (généralement supérieur 50% du volume), le filament composite devient alors plus fragile et plus cassant ce qui rend sa manipulation et son impression plus difficiles.
Avant d’être mis en forme, le filament doit être conditionné sous forme de bobine puis acheminé de cette bobine à l’extrudeur à l’aide d’un système de convoyage de type roues crantés/Bowden. Lors de ces deux étapes, le matériau est soumis à des contraintes de flexion importantes pouvant aller jusqu’à la rupture du filament.
L’impression 3D de ces filaments cassants est néanmoins possible avec des têtes d’impression direct drive comme la tête-outil FIL21 de Lynxter. Associée à notre imprimante 3D modulable S600D, La FIL21 fait face aux contraintes citées plus haut et peut imprimer nombreux filaments chargés avec des poudres d’alumine et de zircone.
Les étapes nécessaires à l’impression 3D céramique
1- La mise en forme par impression 3D
La fabrication additive de pièces en céramiques techniques répond aux besoins de produire en petite quantité ou bien de créer rapidement des pièces à formes complexes.
Disponible sous la forme de filaments « chargés » et cassants, l’impression 3D de céramique technique est possible via la technologie de dépôt de fil fondu MEX (FDM ou FFF) si elle est associée à une tête-outil Direct Drive : en plaçant l’extrudeur directement au-dessus du bloc de chauffe, et en limitant le rayon de courbure, l’extrusion est parfaitement maitrisée.
Une étape importante est de bien renseigner la taille de la pièce lors de l’impression 3D. En effet la céramique réduit de taille lors des deux étapes suivantes (déliantage et frittage). Elle doit donc être imprimée en considérant ce retrait, de l’ordre de 15% à 20% en fonction des épaisseurs.
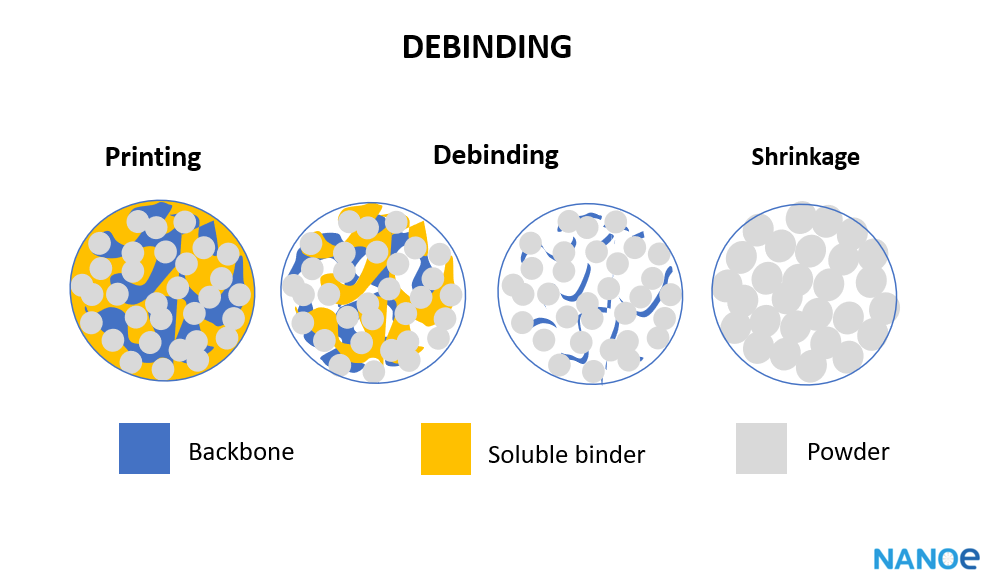
Schéma de déliantage du filament céramique zetamix-Nanoé
2- Le déliantage
La composition des objets mis en forme est la même que celle d’un filament : système liant polymère associé à des particules céramiques.
Une fois la mise en forme effectuée avec succès, il reste deux étapes incontournables : le déliantage puis le frittage. Ces post traitements permettent d’obtenir des pièces finales denses composées uniquement de céramiques afin de présenter les propriétés attendues.
L’objectif du déliantage est d’enlever, de dégrader le système liant des pièces (là pour permettre la mise en forme de la poudre par extrusion). Le système liant étant généralement composé d’un mélange de plusieurs polymères, on peut être amené à réaliser cette opération en plusieurs étapes. Il peut se faire de deux façons différentes : chimique ou thermique.
– Déliantage chimique (dissolution, dégradation chimique) dans un premier temps pour enlever le composant 1. (Soluble binder)
– Déliantage thermique : on brûle le composant 2 en l’exposant à des températures supérieures à sa température de dégradation. (Backbone)
Les paramètres de déliantage dépendent la nature des liants ainsi que de la nature de la poudre (métallique ou céramique). Cette étape est très importante est doit être exécutée avec soin afin de ne pas détériorer les géométries ou inclure des impuretés. Elle entraine un premier retrait du volume de la pièce.
3- Frittage
L’objectif du frittage est de densifier la pièce, de créer une cohésion entre les particules céramiques afin d’obtenir un matériau dense présentant de bonnes propriétés mécaniques.
Cette opération consiste à créer des liaisons entre les grains de poudre par la diffusion d’atomes sous l’action de la température. Elle a pour effet de consolider la pièce. Un retrait est généralement observé à l’issue de cette étape.
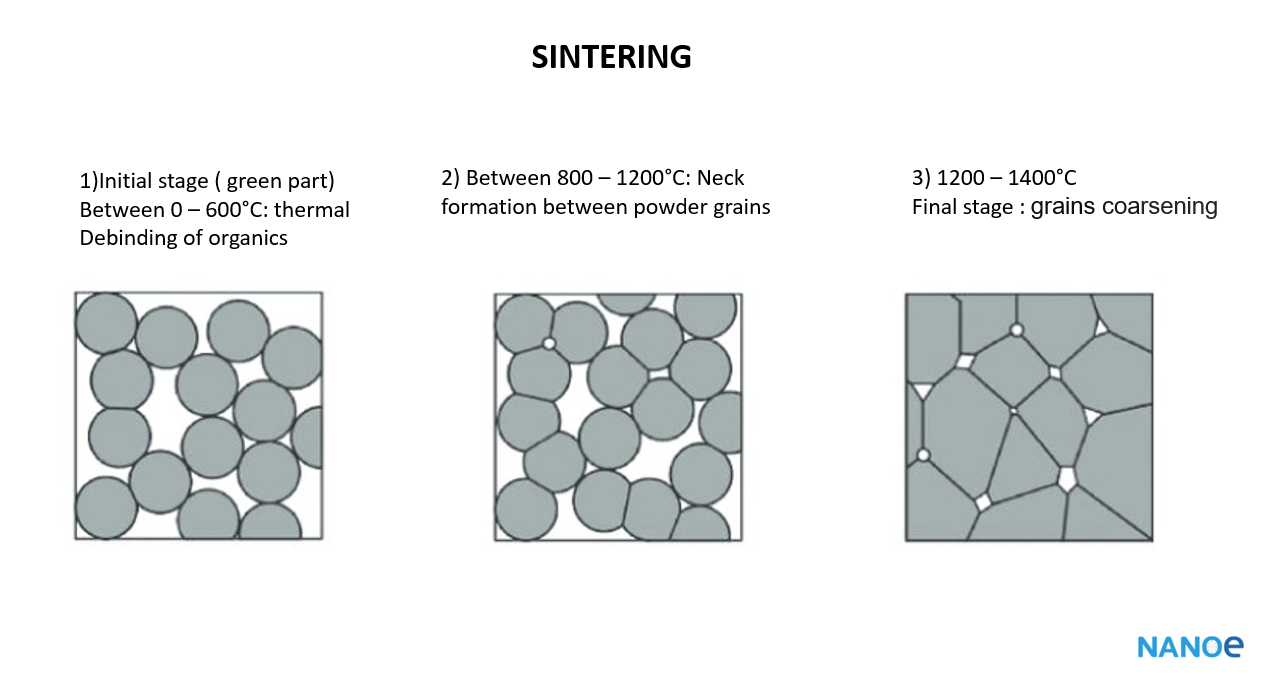
Schéma du frittage du filament céramique Zetamix-Nanoé
Un exemple : Alumine et Zircone Zetamix Prenons l’exemple des filaments chargés Zetamix de Nanoe, ils sont composés de poudres céramiques et de deux liants. (Schéma précédent)Les liants sont éliminés entre 300°C et 600°C, le frittage lui va être effectué entre 1120°C et 1600°C selon les poudres : l’alumine de Zetamix se fritte par exemple à 1550°C et la Zircone noire à 1450°C. |
Par ailleurs le choix du four de frittage est très important et doit se faire en fonction de la nature de la céramique travaillée. Il doit pourvoir fournir les conditions nécessaires pour créer l’atmosphère de frittage requise afin de conserver ses propriétés techniques et ainsi produire les propriétés attendues de la céramique.
Cas d’application impression 3D ceramique : les recherches de Ceramath-DMP
Allons plus loin et voyons le cas précis de l’utilisation des céramiques techniques par le Département Matériaux et Procédés, DMP (anciennement LMCPA), du laboratoire CERAMATHS (Matériaux Céramiques et Mathématiques), de l’Université Polytechnique Hauts-de-France. Il est spécialisé dans l’élaboration des céramiques techniques appliquées aux domaines du médical et du développement durable.
Un de leurs travaux concerne notamment les technologies de fabrication additive et leur intérêt dans le domaine de la santé, en particulier pour la fabrication d’implants osseux synthétiques. Ces « biocéramiques » sont des matériaux de choix pour ce type d’implant et présentent des propriétés de biocompatibilité et de biodégradabilité favorisant le processus naturel de repousse osseuse.
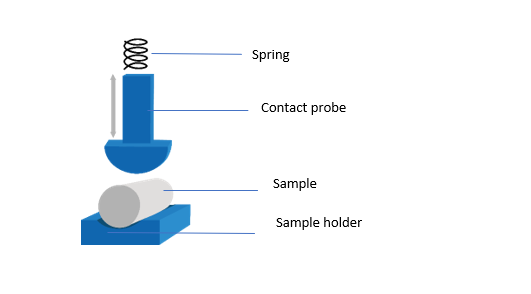
Schèma de l’expérience de dilatométrie de Ceramath
Parmi les techniques de caractérisations couramment utilisées lors de l’élaboration de ces matériaux, on retrouve l’étude dilatométrique et l’analyse thermo-gravimétrique (ATG). Ces deux méthodes permettent d’avoir accès à des paramètres clés liés au comportement des matériaux en température : respectivement l’étude de la variation dimensionnelle et de l’évolution de la masse lors d’un cycle thermique.
Ces équipements complexes nécessitent des consommables très chers et devant résister en température. Les céramiques techniques sont alors idéales pour ces cas d’application par leur performance : tenue hautes températures, faible coefficient de dilatation thermique et compétitivité du fait de leur faible coût (versus le coût des consommables métalliques en platine, acier, aluminium, or, cuivre)
Conscient de cette économie potentielle, ce laboratoire s’est alors tourné vers les filaments chargées et utilise aujourd’hui les filaments de zircone et d’alumine Zetamix pour produire des consommables de laboratoire et autres dispositifs en relation avec leurs recherches.
Creusets d’analyse thermogravimétrique (ATG) :
L’ATG est une technique mesurant la variation de masse d’un échantillon lorsqu’il est soumis à une programmation de température, sous atmosphère contrôlée. Cette variation de masse peut être une perte (émission de vapeurs) ou gain (fixation de gaz). Les matériaux étudiés sont placés dans un creuset. Cette pièce est coûteuse en raison de sa petite taille et de la technicité de son élaboration. Son nombre d’utilisations est limité par le risque de pollution d’un matériau à l’autre (usage unique recommandé). Une gestion précise des stocks est nécessaire pour éviter l’interruption des mesures. Pour toutes ces raisons, CERAMATHS a choisi d’internaliser la production de ces pièces grâce à l’impression 3D de filaments Zetamix afin de réduire ses coûts de gagner en réactivité.
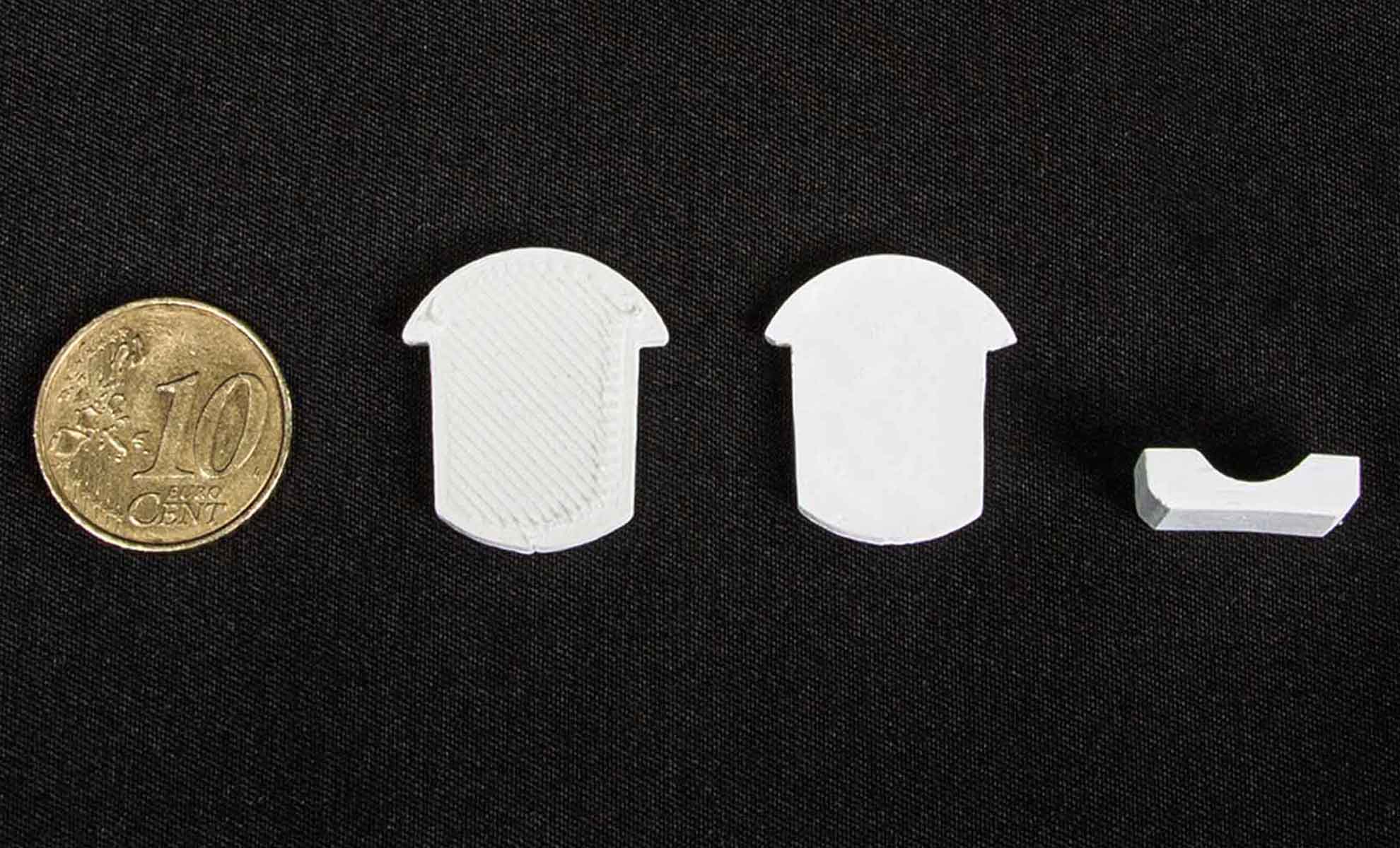
Pièces du dialomètre imprimées en alumine par la S600D
Consommables pour dilatomètres :
Le CERAMATHS-DMP produit également des consommables utilisés pour l’étude dilatométrique des matériaux lors du frittage.
La dilatométrie est une technique analytique puissante permettant de déterminer les variations dimensionnelles d’un matériau en fonction de la température. Dans une expérience de dilatométrie, un échantillon est placé dans un porte-échantillon dont une extrémité est mise en contact avec une tige de poussée. Le déplacement de cet élément au cours du temps permet de connaitre l’évolution dimensionnelle de l’échantillon en fonction de la température.
Cependant, les hautes températures utilisées lors de cette mesure (frittage) peuvent déformer ou endommager le porte-échantillon et la tige avec le temps. Pour assurer la précision, ainsi que la répétabilité des analyses réalisées, le laboratoire remplace régulièrement ces consommables grâce à l’impression 3D.
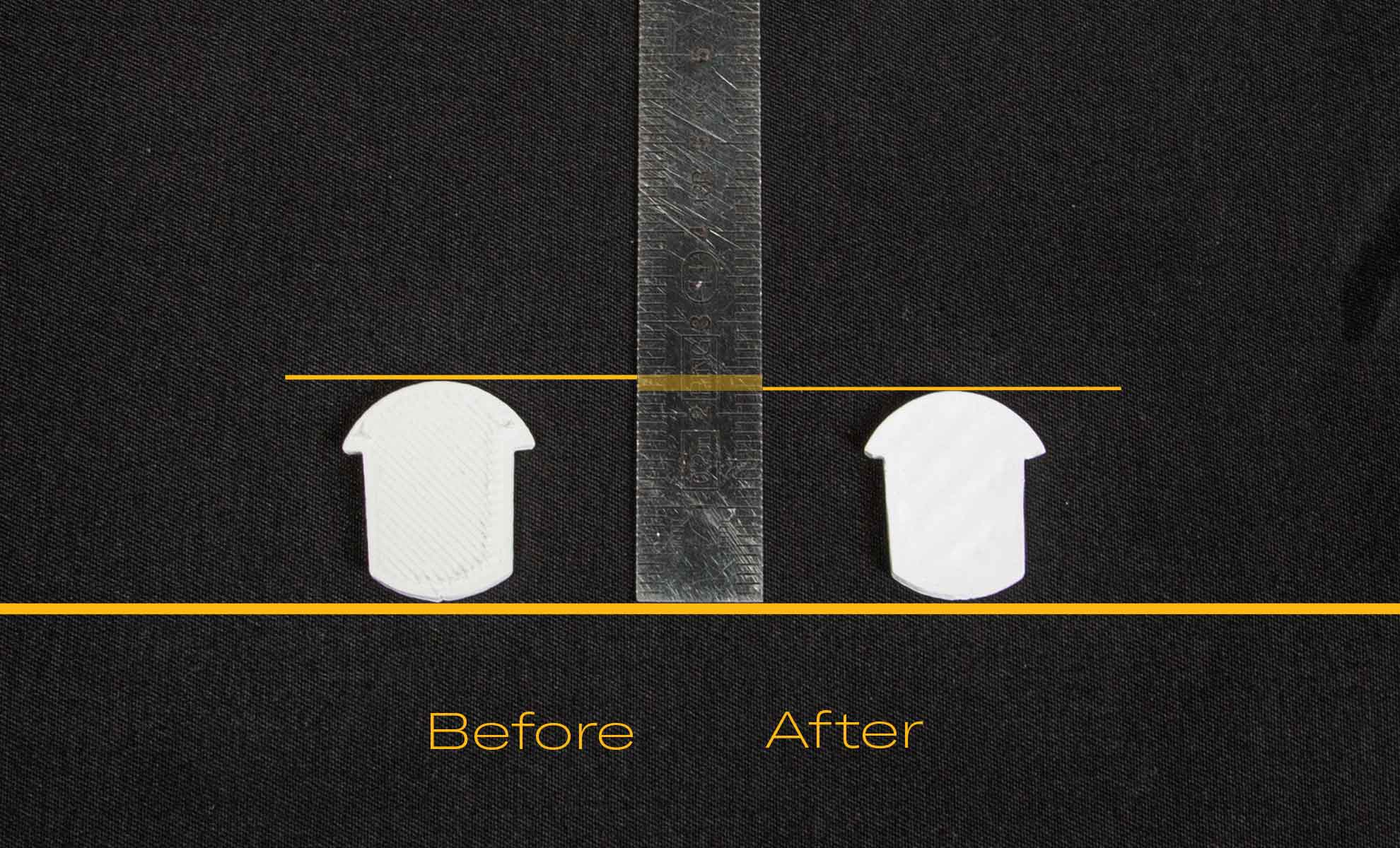
Pièces du dialtomètre imprimées avant et après cuisson
L’impression 3D de céramiques techniques est en pleine expansion et permet aujourd’hui une amélioration des coûts et un gain de temps important sur les opérations où elle intervient (médical, industrie, recherche et aéronautique).
Avec la FIL21 et l’imprimante 3D S600D, l’impression de céramiques techniques se fait en toute sécurité, tout en assurant des vitesses et performances d’impression élevées. Les filaments céramiques (alumine, zircone) et les filaments métalliques (316L) sont d’ores et déjà supportés et de nouvelles références arriveront prochainement dans l’écosystème.
Résumé technique du cas d’application
SECTEUR | Université – Centre de recherche |
APPLICATION | Dilatomètre |
MATIÈRE | Alumine Zetamix |
DIMENSIONS | 23 mm x 17 mm x 1,2 mm |
TECHNOLOGIE D’IMPRESSION | Imprimante S600D et FIL21 |
TEMPS D’IMPRESSION | 00H15 |
QUANTITÉ DE MATIÉRE | 1,56 gr |
COÛT MATIÈRE | 599 €/kg |
HAUTEUR DE COUCHE | 0,2 mm |
TAILLE DE BUSE | 0,4 mm |
VOLUME DE PRODUCTION | Unitaire |