Soft Robotics: what are soft sensitive actuators?
Most living organisms have soft and stretchy tissues. These tissues are beneficial because they can adapt by changing shape, are sensitive, and have a good balance of weight and strength. This adaptability allows tissues to adjust to physical forces, like how the skin and flesh of hands change shape to grip objects better. In contrast, most robots today are made of hard materials like metal, plastic, and wood. While these materials are strong and easy to build with, they don’t have the flexibility, sensitivity, or efficiency of soft, flexible materials found in living tissues.
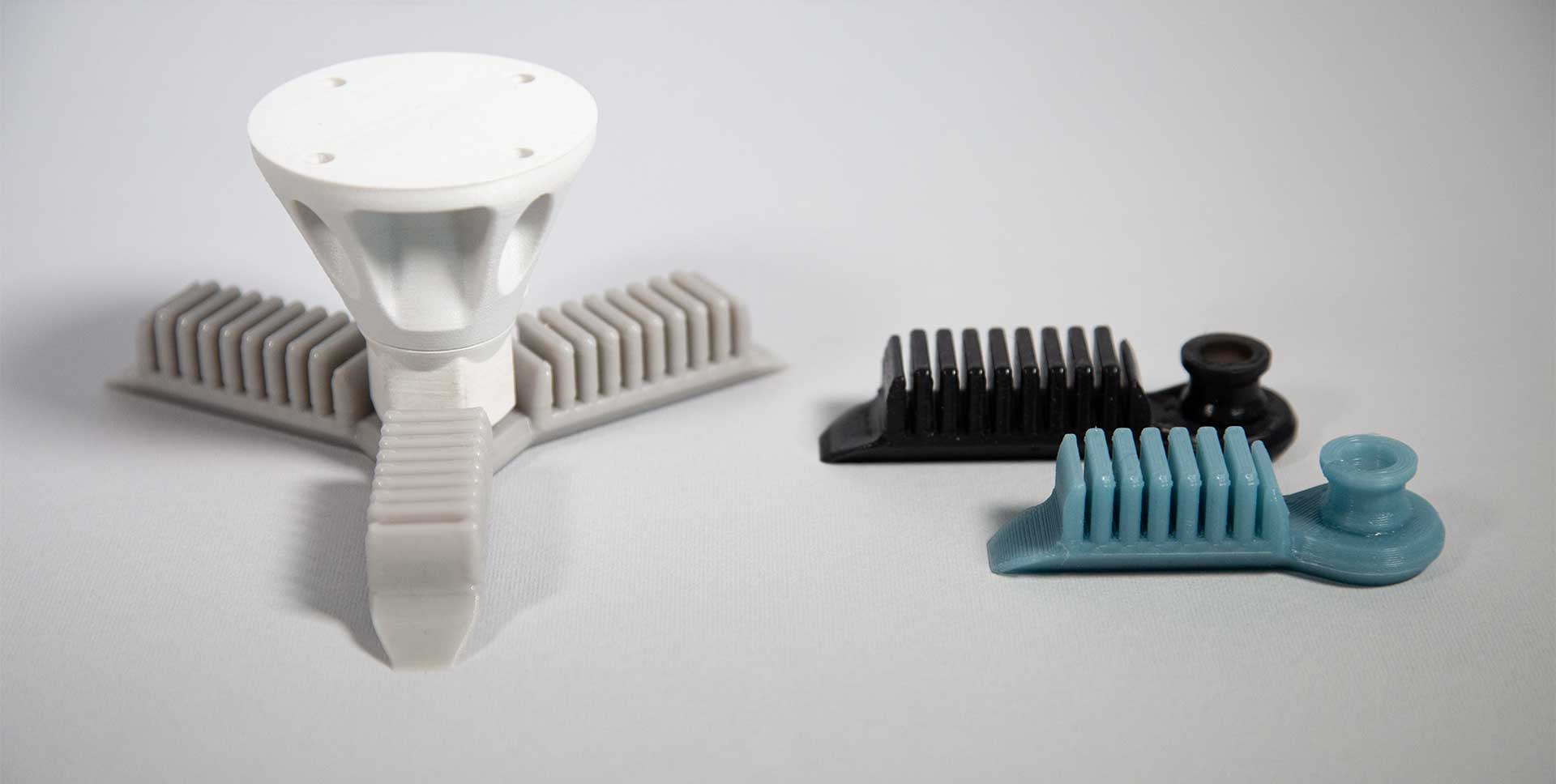
Soft robotics grippers
“A robot is a physical or virtual agent that can sense its environment and take actions that change it “Rodney Brooks
From this idea, soft robotics was created. It focuses on developing flexible and stretchy robots that are highly adaptable and sensitive to their surroundings (sensors) and can exert strong force while remaining lightweight (actuators). Soft robotics aims to build robots that can handle tasks needing adaptability and flexibility, like gripping odd-shaped objects, interacting with people, and being used in medical applications.
At Lynxter, Research & Development Engineer Ph.D Brice Parilusyan advanced the field by using silicone 3D printing to merge soft sensors with actuators, thereby creating what are known as Soft Sensitive Actuators or soft robots.
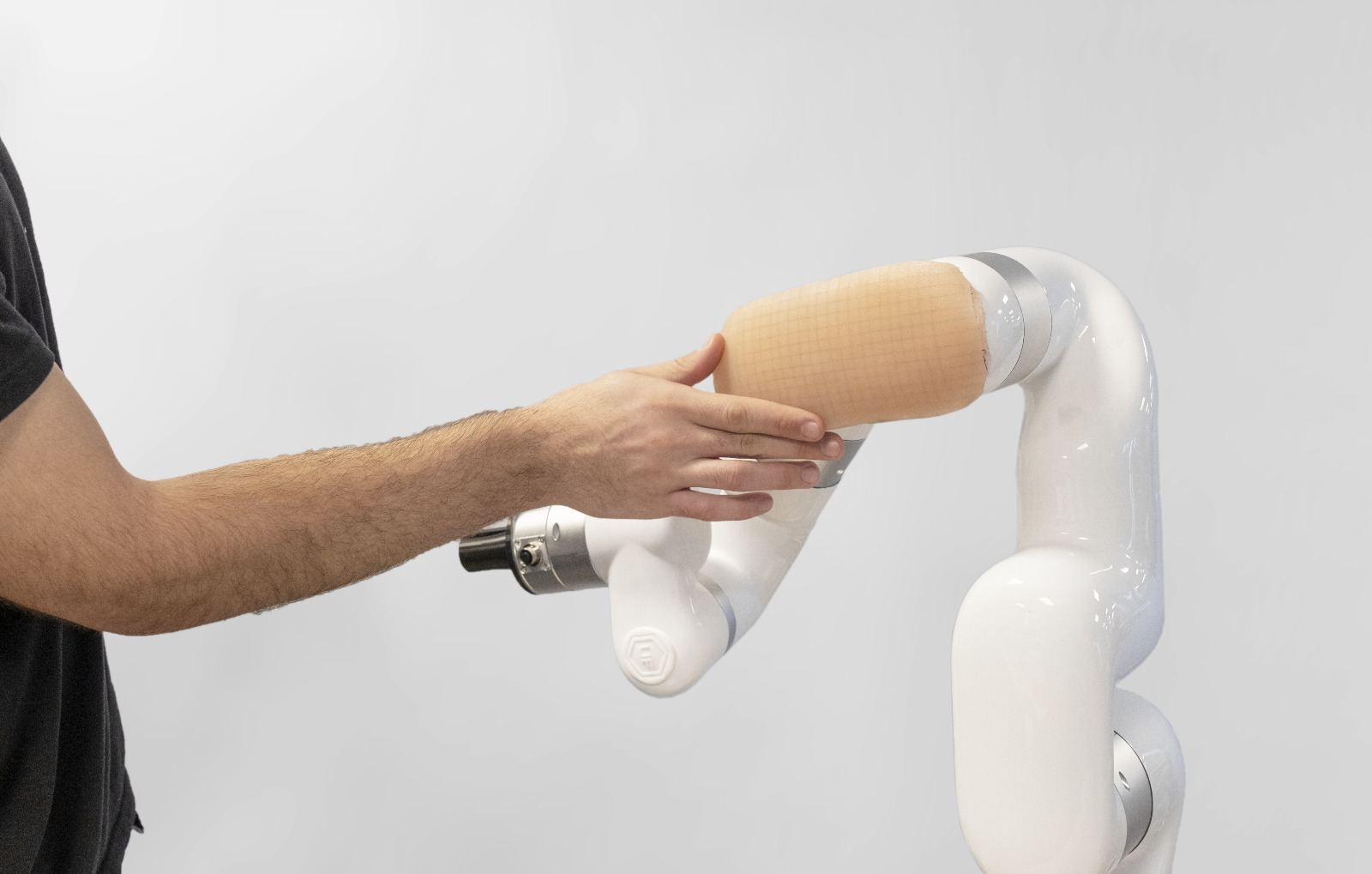
Integrating sensors through silicone molded techniques
Soft touch sensors with molding technique
Sensors detect external stimuli and convert them into signals that can be read. There are various types, like chemical, electrical, and mechanical, used in many fields such as industry, medicine, and climate science. Traditional sensors are rigid and can’t be used in environments with a lot of movement or pressure. Flexible sensors can adapt to these conditions and are better suited for irregular surfaces and high-pressure areas.
Silicone 3D Printing and Soft Robotics
Materials used in flexible sensors need to be conductive (common materials include metals, carbon) and stretchable (polymers). Each chosen for its ability to conduct electricity while remaining flexible and durable. Flexible sensors are useful in many applications, especially in interactions between humans and machines and in medicine. They can fit complex shapes and provide touch feedback, improving user experience and functionality. In robotics, flexible sensors allow for precise and gentle handling, making them ideal for working with delicate items without causing damage.
The fabrication process involves creating silicone layers, positioning electrodes, and adding a viscous silicone layer. This method ensures the sensor is robust and adaptable to various shapes.
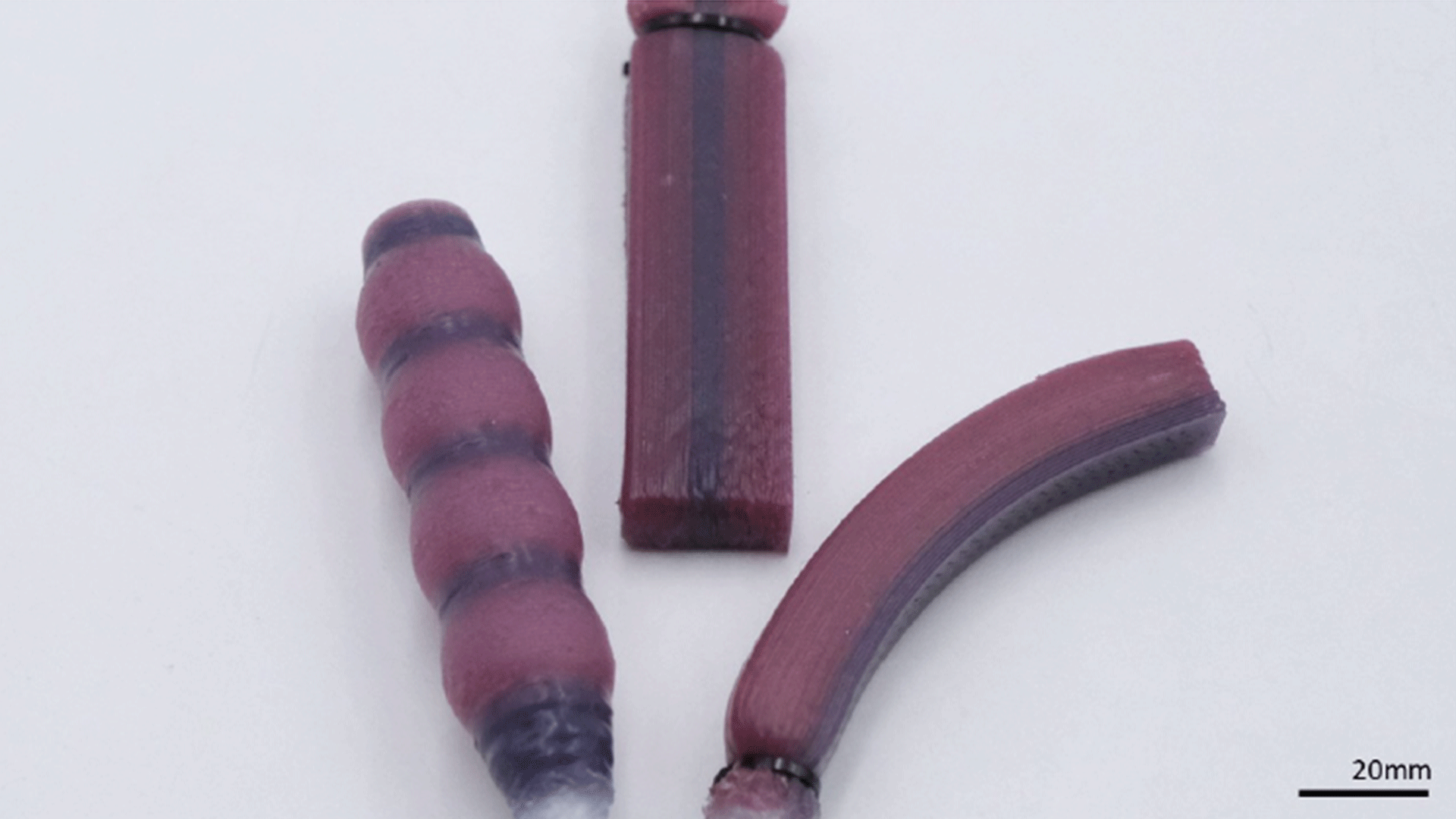
Two parts or bi-component silicone soft actuators with ratio variation
Soft actuators with silicone 3D printing
We will now focus on how soft robots move using soft actuators.
Soft actuators can use different energy sources like temperature and humidity to create movement. Pneumatic actuators, powered by air pressure, are very common because they are simple, cheap, and can be made using common materials. They can bend, stretch, contract, and twist. Soft actuators have different shapes depending on their movements, one of the most common types are PneuNet actuators. Soft pneumatic actuators (SPAs) are especially useful in medical devices, human-machine interfaces, and industry. They are flexible and can grip and manipulate objects gently, making them ideal for delicate tasks.
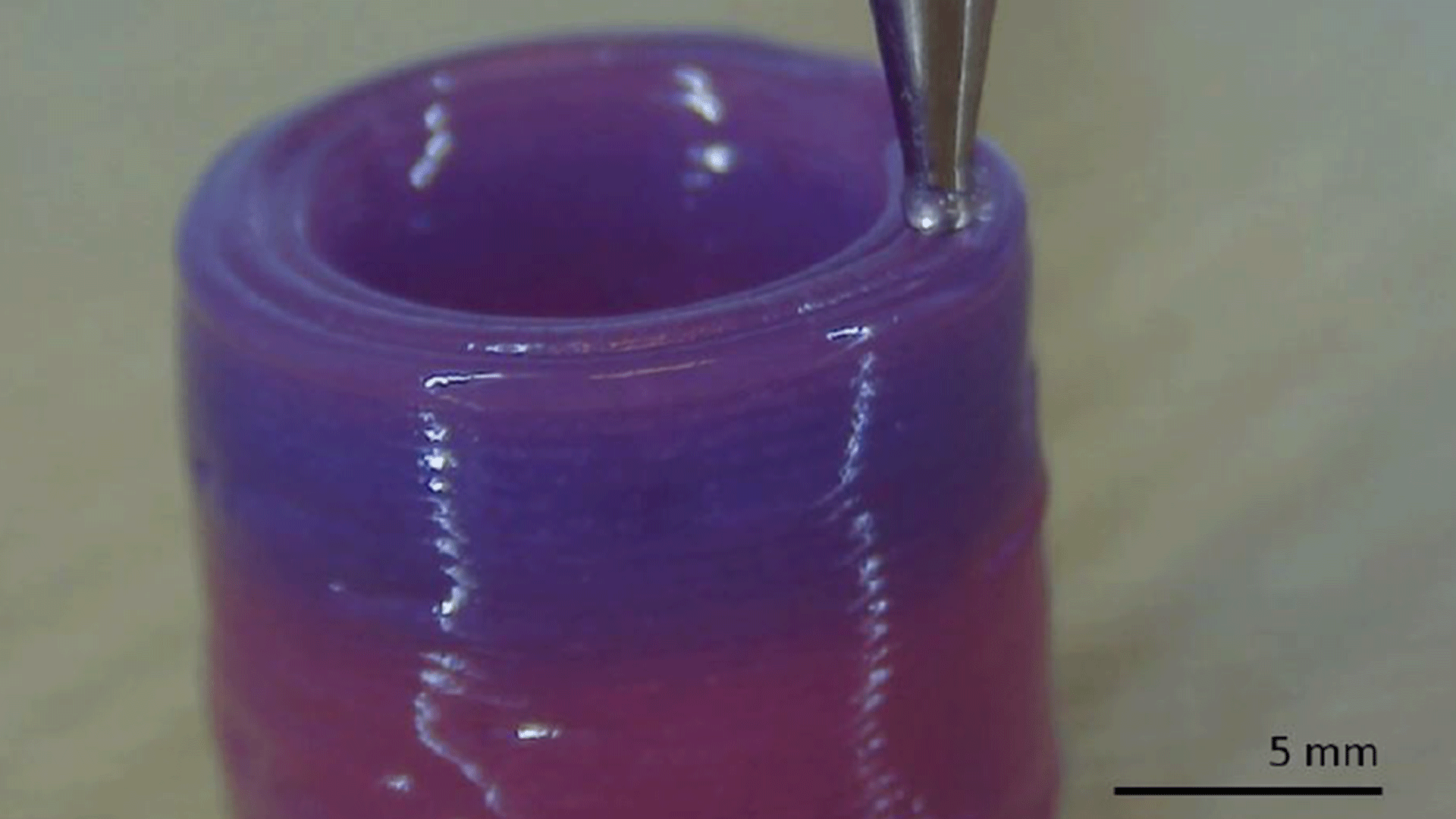
Printing the soft actuators with ratio variation
Molding is one of the oldest and most common methods, especially for making soft robots using materials like silicone. As soft robotics has grown, the designs have become more complex and diverse. 3D printing methods have become a new solution, including Fused Deposition Modeling (FDM), Selective Laser Sintering (SLS), inkjet printing, and stereolithography (SLA). These methods offer benefits like fast prototyping and high precision but also have drawbacks, such as limited material choices.
Direct Ink Writing (DIW) or Material extrusion (MEX) is highlighted for its use of liquid materials like silicone or hydrogels, allowing flexible and complex designs. MEX is promising for soft robotics, but challenges remain in optimizing multi-material printing and integrating sensors.
MEX manufacturing can change the mechanical properties of printed silicone structures by varying layer height for example. By adjusting the mix ratio of the silicone parts, we can create different levels of stiffness and strength within a single printed part. This method makes it easier to produce pneumatic actuators with specific deformation properties during manufacturing without needing complex multi-material designs. These two methods were implemented on the S600D using a custom tool head developed specifically for this research. This was made possible by the open features of the 3D printer. (you can read more about it in this article)
This technology highlights the need to improve manufacturing processes to keep up with the evolving demands of soft robotics, aiming for more advanced and integrated designs.
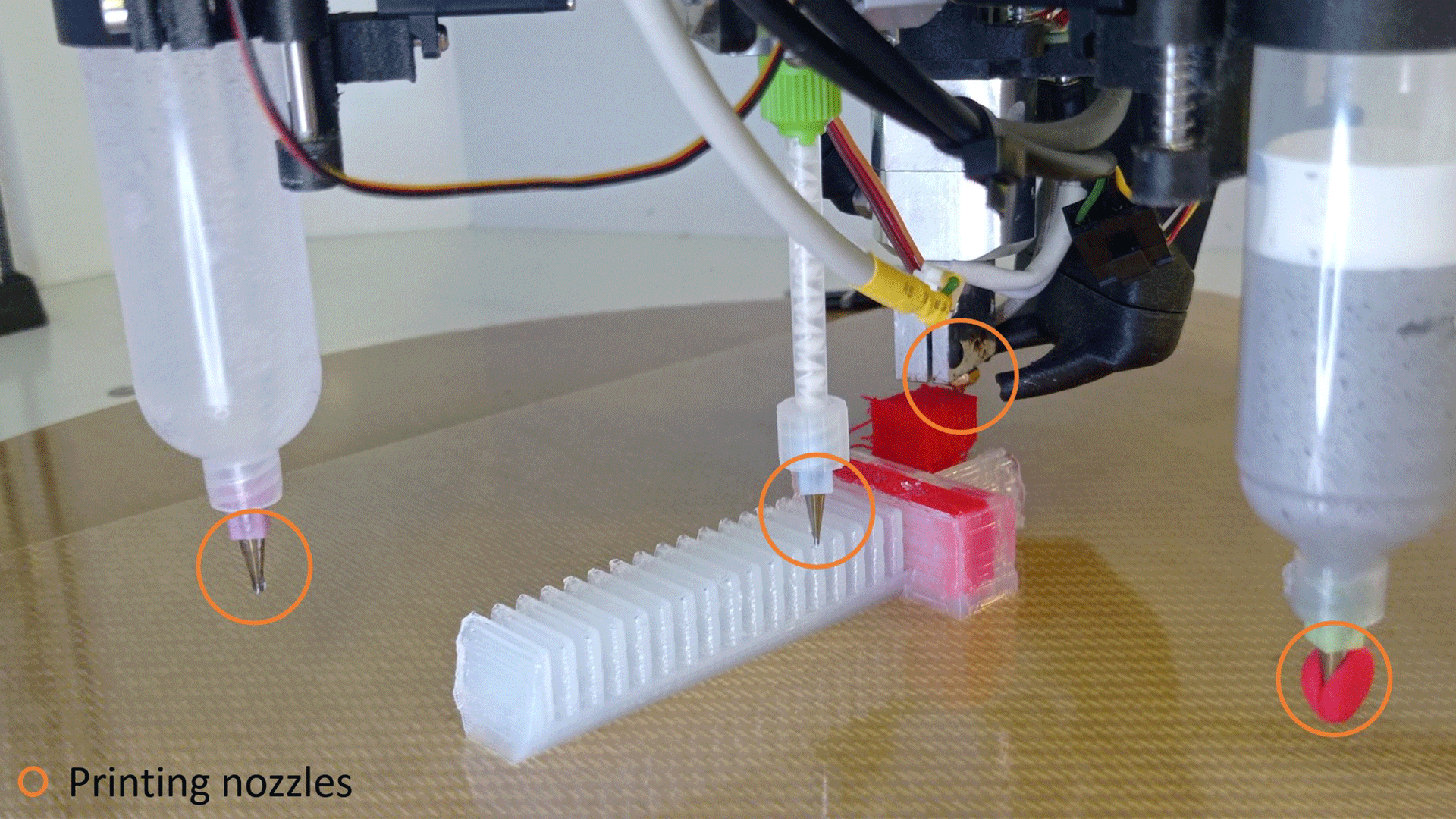
Soft robot multi-material printing with custom toolhead with 4 printing nozzles: gel/ silicone/ thermoplastic, and conductive material
Combining sensors and actuators with silicone 3D printing: soft sensitive actuator
By definition, robots integrate both sensing and actuating parts. While traditional robotics are made of several small components connected, soft robots are often a single complex structure. This monolithic system hardly allows small components connection, and everything is merged during fabrication. Thus, sensors can be integrated directly inside actuators and must bear the mechanical stress induced by the actuators’ movements and stretching.
Manufacturing a soft robot integrating multiple materials and functions is a challenge. Their fabrication process can still be improved due to repeatability and watertightness issues. However, 3D printing is evolving to answer this challenge to make soft robots able to perceive and interact with their environnement seamlessly.
Research Focus
Brice Parilusyan thesis poses the question of how to manufacture these sensors and actuators through silicone 3D printing to ensure their integration and proper functioning, as well as the impact this manufacturing process will have on the final piece. The question addressed is: How to manufacture soft and sensitive actuators without shape constraints for soft robotics?
Download Ph.D Brice Parilusyan’s complete thesis here