A NEW MAJOR BREAKTHROUGH IN ORTHOPEDICS: 3D PRINTING OF TAILORED SILICONE LINERS
COP Chimie x LYNXTER
Until very recently, silicones have been almost impossible to 3D print. Today, silicone additive manufacturing is booming in France and throughout the world.
Silicone 3D printing in healthcare
To broaden its range of silicones compatible with the S600D and in particular to make silicone 3D printing available to the healthcare sector, Lynxter is working with the French silicone manufacturer, COP Chimie. COP Chimie specializes in silicone chemistry for external orthopedic devices and commercializes a printable range of skin-friendly silicones: COPSIL 3D. A partnership between the two companies was therefore natural in order to develop solutions for healthcare applications in 3D.
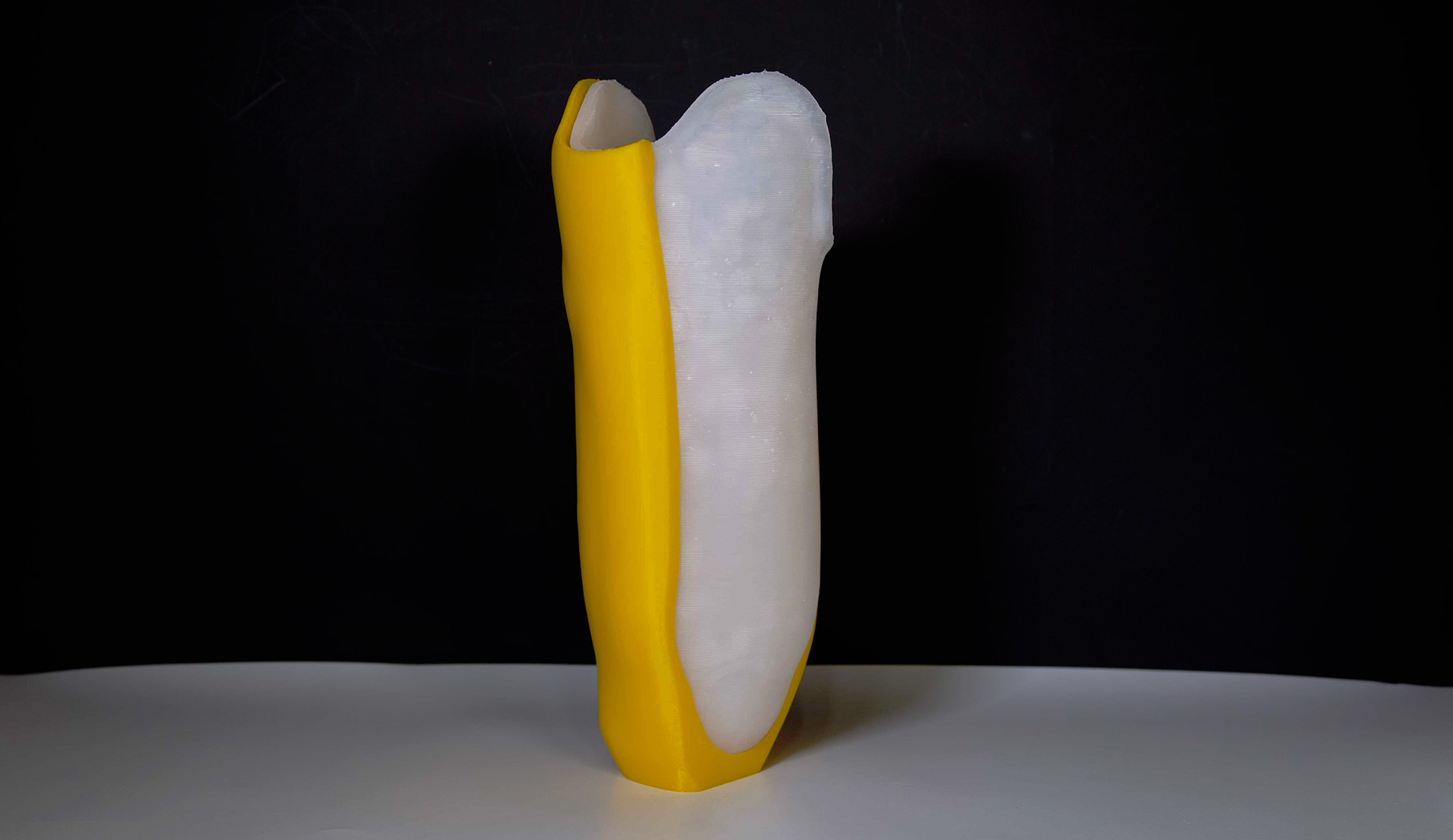
An example of collaborative innovation: the silicone liner
Lynxter and COP Chimie have developed a specific application for this technology: the 3D silicone liner (the interface between the amputee’s skin and the prosthetic socket).
There are currently numerous standard-size liners as well as custom-crafted liners available on the market. It is easy to see that these solutions require improvement in terms of patient comfort (damaged skin, sensitivity, specific shape of the stump) and manufacturing time (several different manufacturing stages are required to produce a custom-crafted liner which can sometimes take days to make with a large amount of waste). The current solutions are not digital and it is difficult to follow and adapt a patient’s treatment efficiently while at the same time ensuring an optimal level of performance.
Together, Lynxter and COP Chimie have developed a solution to print a lightweight customized liner of adjustable hardness using the S600D and the LIQ21 toolhead, in only four hours of print time. The liner is printed in COPSIL 3D 1025, two-component RTV-2 silicone, certified for skin-contact (ISO 10993-5) and formulated by COP Chimie, already a reference in the sector. In addition to reducing manufacturing time and complexity, the process is repeatable, of high precision and enables follow-up treatment.
A new way of approaching and tackling the manufacture of orthopedic devices is emerging.
Digital integration of the technology, reducing the weight of devices, personalization and functionalization are the challenges to be met and that will revolutionize external orthopedic devices.
This partnership is the precursor of development in other areas of application, further widening the field of possibilities. Innovation is serving both healthcare professionals and patient comfort.
3D printing with silicone, a brief summary
Lynxter is a forerunner of this technology in the market and proposes two toolheads, LIQ11 and LIQ21, capable of printing this range of materials with its machine, the S600D.
The constant innovation of the company makes the technology accessible to more people and business sectors, widening the field of applications.
Silicones, generally in the form of oils or translucid elastomers that can be easily colored, are appreciated for their resistance to heat, their flexibility and their hydrophobic and texturing characteristics.
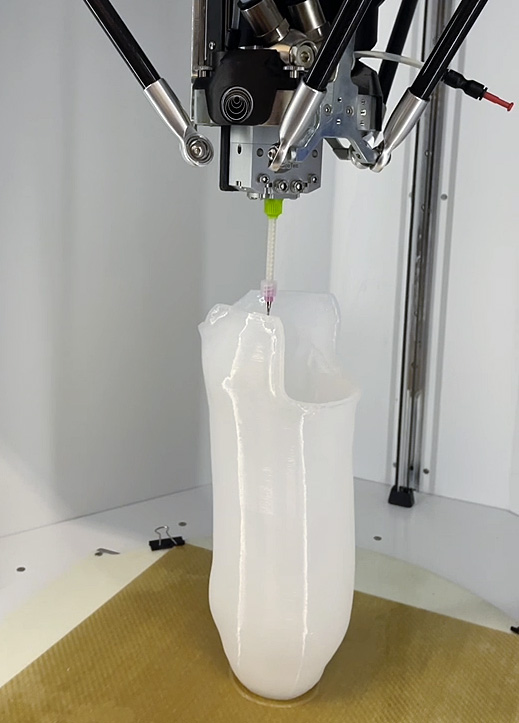
Lynxter has mastered this process and has a robust material supply chain, a print profile library and toolheads for the precise depositing of strings of silicone. Today the company proposes a range of direct additive manufacturing technologies that require no UV curing for one-component (RTV-1) or two-component (RTV-2) silicones.
Silicone 3D printing opens up new possibilities for made-to-measure manufacturing; in healthcare and in particular for patient-specific external orthopedic devices; in industry with on-demand manufacturing of airtight parts and in other sectors such as dentistry, electronics, soft robotics, aeronautics, automobile, railway etc.
About COP Chimie
Founded over 35 years ago, COP Chimie is European leader in the design, formulation and supply of polymers in the external orthopedic device field. A French SME of over 20 employees, COP Chimie has both its own silicone synthesis unit and research laboratory on its production site and synthesizes and formulates a skin-friendly range of silicones.
Following thesis work in partnership with the IMP laboratory, INSA Lyon and INSAVALOR, COP Chimie developed a range of printable silicones: COPSIL3D. Designed for liquid additive manufacturing of soft parts, the COPSIL3D range is based on a two-component RTV2 silicone technology, certified for skin contact (ISO 10993-5) and enables the manufacture of parts with hardness levels varying from 5 to 45 ShA with the same mechanical properties as those made using traditional processes.
Made in partnership with
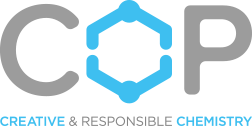