Silicone 3D Printing for Ligier Automotive
Rethinking the Transmission Bellows
Ligier Automotive is a French car manufacturer with a rich history in motorsport. Founded by Guy Ligier in 1969, the company became known for its involvement in Formula 1 racing during the 1970s. The team, which finished as Vice-Constructors’ Champion in 1980, secured 9 wins, 9 pole positions, and achieved 50 podiums. Since 2013, the French sports brand has been revitalized under the leadership of its President Jacques Nicolet, who took up the torch.
In 2019, to mark the brand’s 50th anniversary, the French manufacturer launched the Ligier JS2 R, a GT car that reinterprets the lines of Guy Ligier’s 1970s JS2, which finished second in the 1975 24 Hours of Le Mans. The car is designed exclusively for racing.
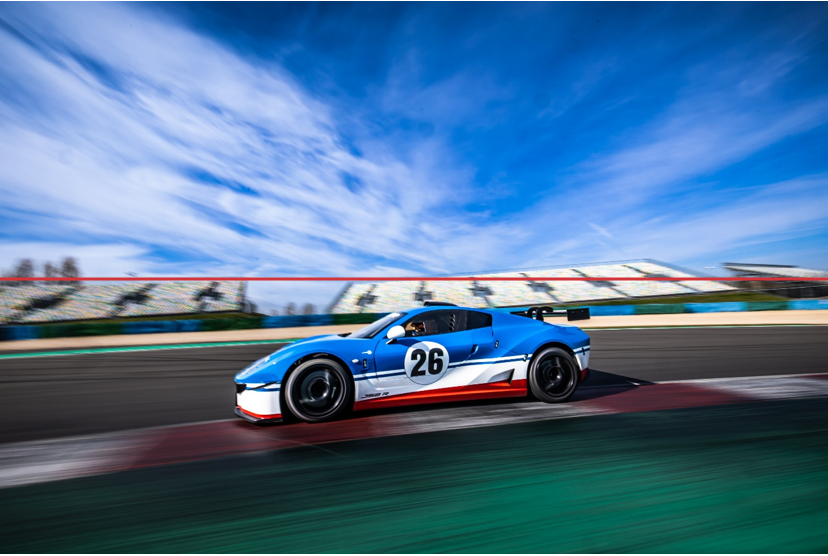
Ligier JS2 R
In the thrill of motorsport, where victory often hinges on the smallest details, technological ingenuity reigns supreme. Leveraging the precision of 3D printing, the engineers at Ligier Automotive’s design office have showcased an interesting case of silicone 3D printing: a transmission bellows.
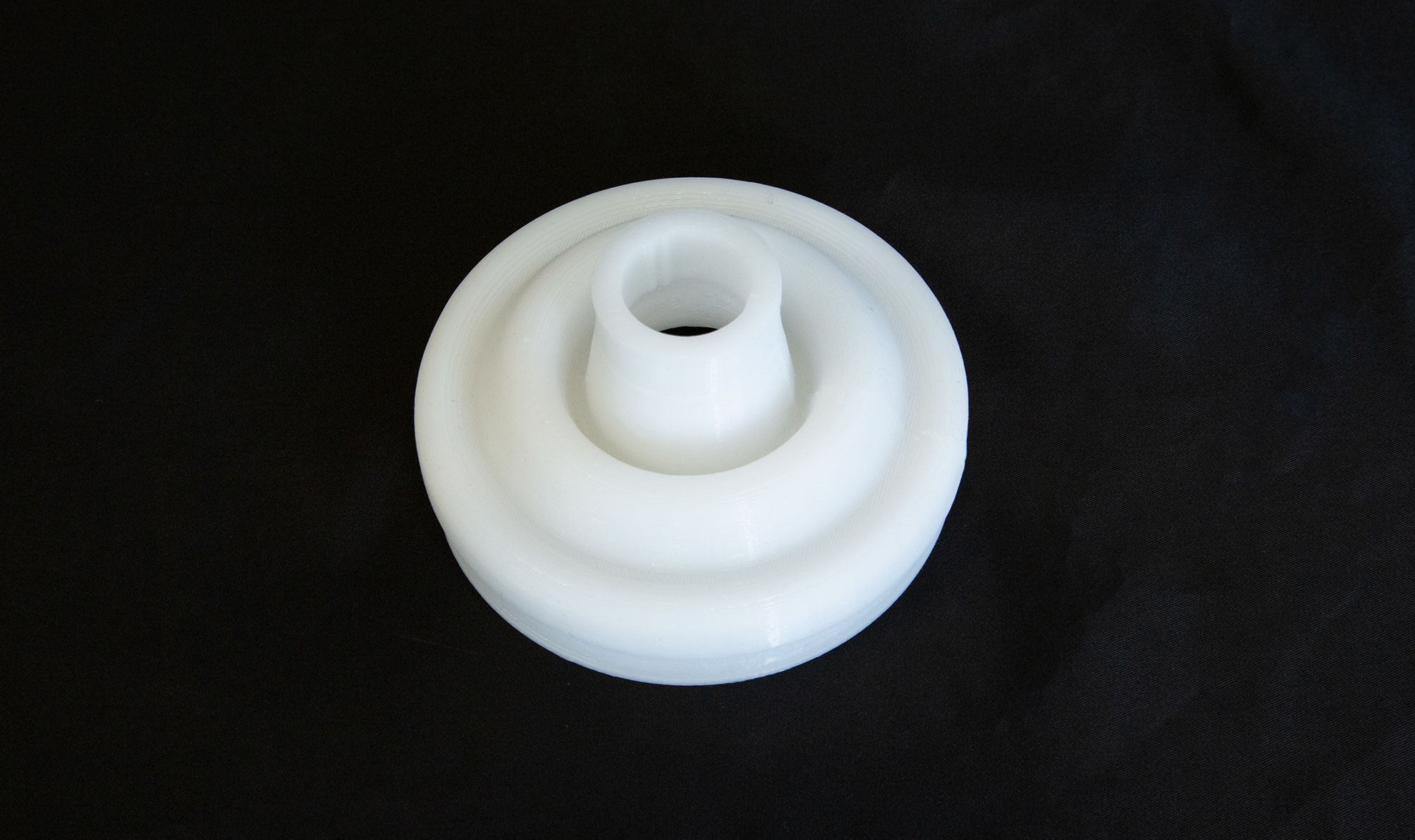
Silicone-printed transmission bellows
Why use 3D printing to produce bellows?
Ligier Automotive’s initial goal was to find an alternative to producing a molded part, which requires specific tools and is not cost-effective for single or very small series production.
Printing and testing the silicone 40 ShA transmission bellows on the Ligier JS2 R
What was the goal of this 3D printing?
Ligier Automotive also wanted to explore the new technology of silicone 3D printing, its process, and how it can impact the design of bellows in a particularly challenging environment: high temperature, high rotation speed (centrifugation), resistance to grease and oils, etc.
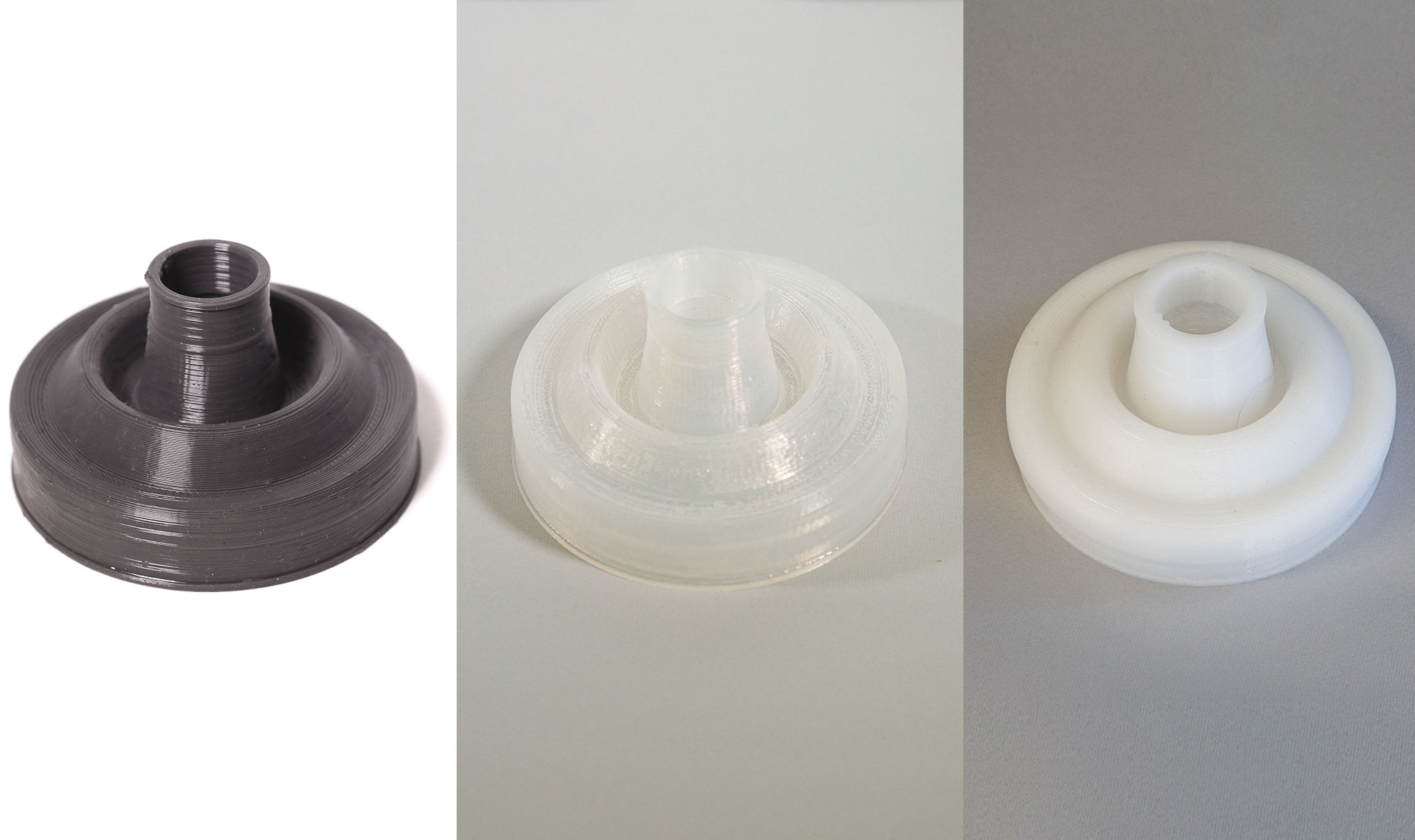
Material testing and final version of the transmission bellows
The first versions highlighted the need to adjust the bellows’ geometry to fit the 3D printing process, especially in the radii, to ensure good adhesion of the deposited layers and consistent mechanical strength in these areas. With a printing time of 3 hours 50 minutes per part, and rapid CAD design modifications (thickness), 2 business days are sufficient to finalize the part’s development.
In this case, it resulted in an increase in thickness, which was negligible in terms of weight (minimal) but proved beneficial in terms of skin stiffness, ensuring that the shape holds well at high rotation speeds.
Tests were conducted on the manufacturer’s Ligier JS2 R development car. These initial tests were particularly positive as the bellows responded perfectly: resistance to temperature, behavior at high speed: no deformation, no grease ejection. The technology thus appears compatible with these significant technical constraints and could offer an interesting solution for prototyping and small series of bellows of all types (transmission bellows, steering bellows, etc.).
A Silicone-Printed Dial Bellows
Let’s return to the role of the dial bellows. At the heart of every racing machine is the transmission bellows, a key element of the transmission system, synonymous with the relentless pursuit of power and performance. Here’s why it’s so important.
Effective Protection: The transmission bellows play a crucial role in protecting the internal components of the transmission from contaminants such as dust, dirt, and moisture. This protective barrier helps prolong the life of mechanical parts and maintain optimal performance. By preventing premature wear and potential failures, the transmission bellows ensure the machine’s reliability and durability, even in the most demanding conditions.
Redefined Flexibility: In the heat of competition, where every turn demands perfection, the transmission bellows emerge as a testament to adaptability. Its unmatched flexibility and wide range of movement facilitate integration within the transmission, effortlessly accommodating track demands without succumbing to stress or compromise.
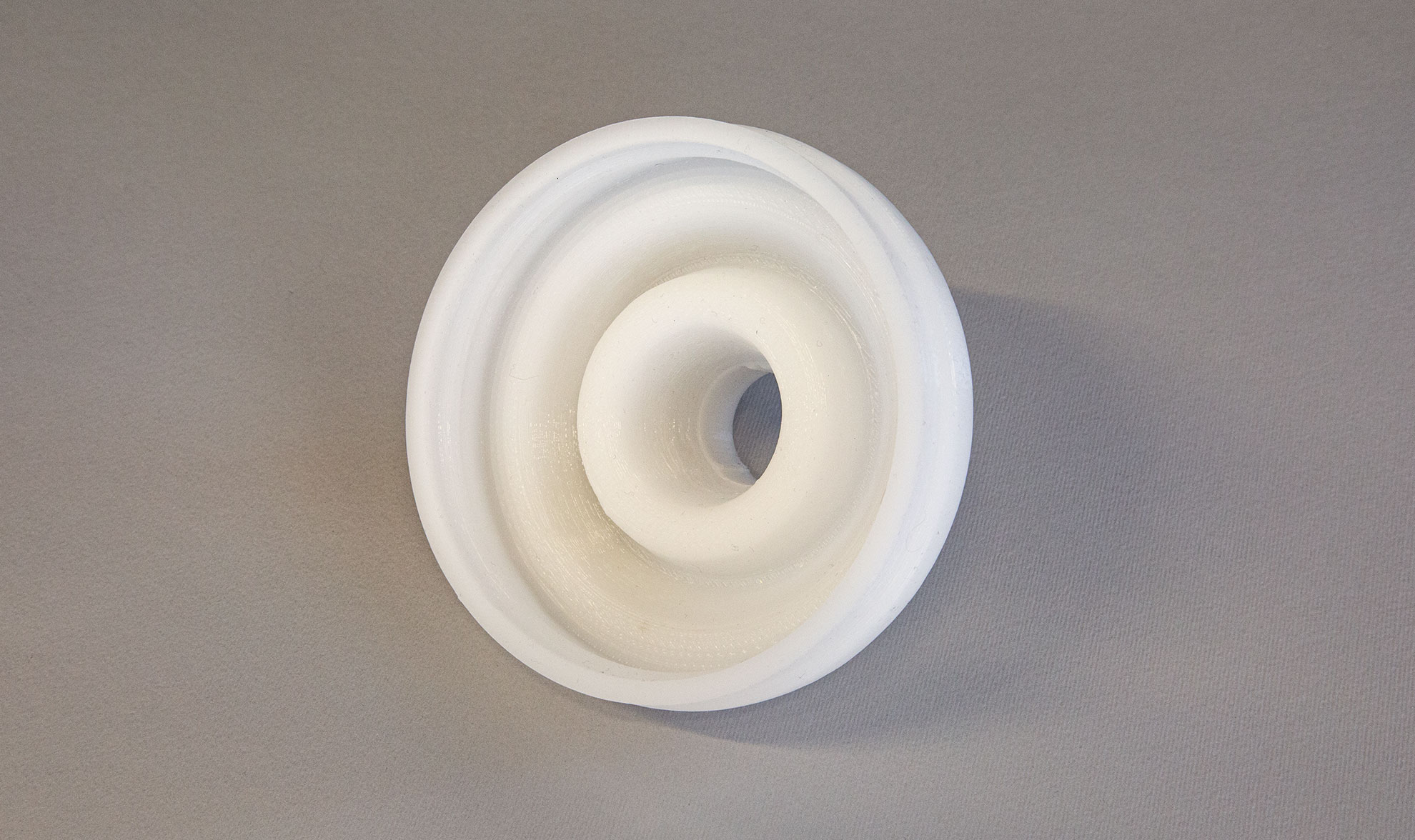
Another view of the dial bellows
The application of silicone 3D printing for the manufacturing of transmission bellows in the automotive field, particularly by Ligier Automotive, marks a significant advancement in the prototyping stage. This initiative, driven by innovation and the search for alternative solutions, demonstrates the ability of 3D printing to meet technical and environmental requirements.
Ligier’s legacy in motorsport history shows how their innovation and technology are always tied to better car performance. They continue to push the boundaries in racing, shaping the future of the sport with every new idea.
Printing Details
SECTOR | Automotive |
APPLICATION | Transmission joint |
MATERIALS | SIL 4050 |
DIMENSION | 111.57 x 111.57 x 57.76 mm |
3D PRINTER | MEX – S300X LIQ21 | LIQ11 |
PRINTING TIME | 3h50 / piece |
MATERIAL QUANTITY | 95g silicone & 50g support |
LAYER HEIGHT | 0.35 mm |
NOZZLE SIZE | 0.69 mm |
INDUSTRIAL SEALING WITH SILICONE AND PU 3D PRINTING
download our e-book
Discover in just a few pages the possibilities offered by silicone and polyurethane 3D printing for industrial sealing applications, such as the manufacturing of gaskets, bellows, and much more.