Silicone suspended in gel: thin walls and lattices become possible in flexible 3D printing
Creative clients, an open machine, and new application possibilities: a closer look at silicone 3D printing in gel.
A solution to explore with the S300X – LIQ21 | LIQ11 3D printer from Lynxter, which offers adaptable technology thanks to its modularity.
Silicone 3D printing in gel
Gel-based 3D printing is an innovative technique that builds on Lynxter’s expertise in elastomer 3D printing. By extruding material directly into a gel bath, this technology enables the creation of complex structures while minimizing gravity-related constraints. It offers greater design freedom, allowing for the printing of delicate forms with thin and precise walls without requiring rigid supports. This approach also reduces post-processing, simplifying the manufacturing process. Additionally, it is particularly well-suited for flexible materials, opening doors for applications in the medical, industrial, and research fields.
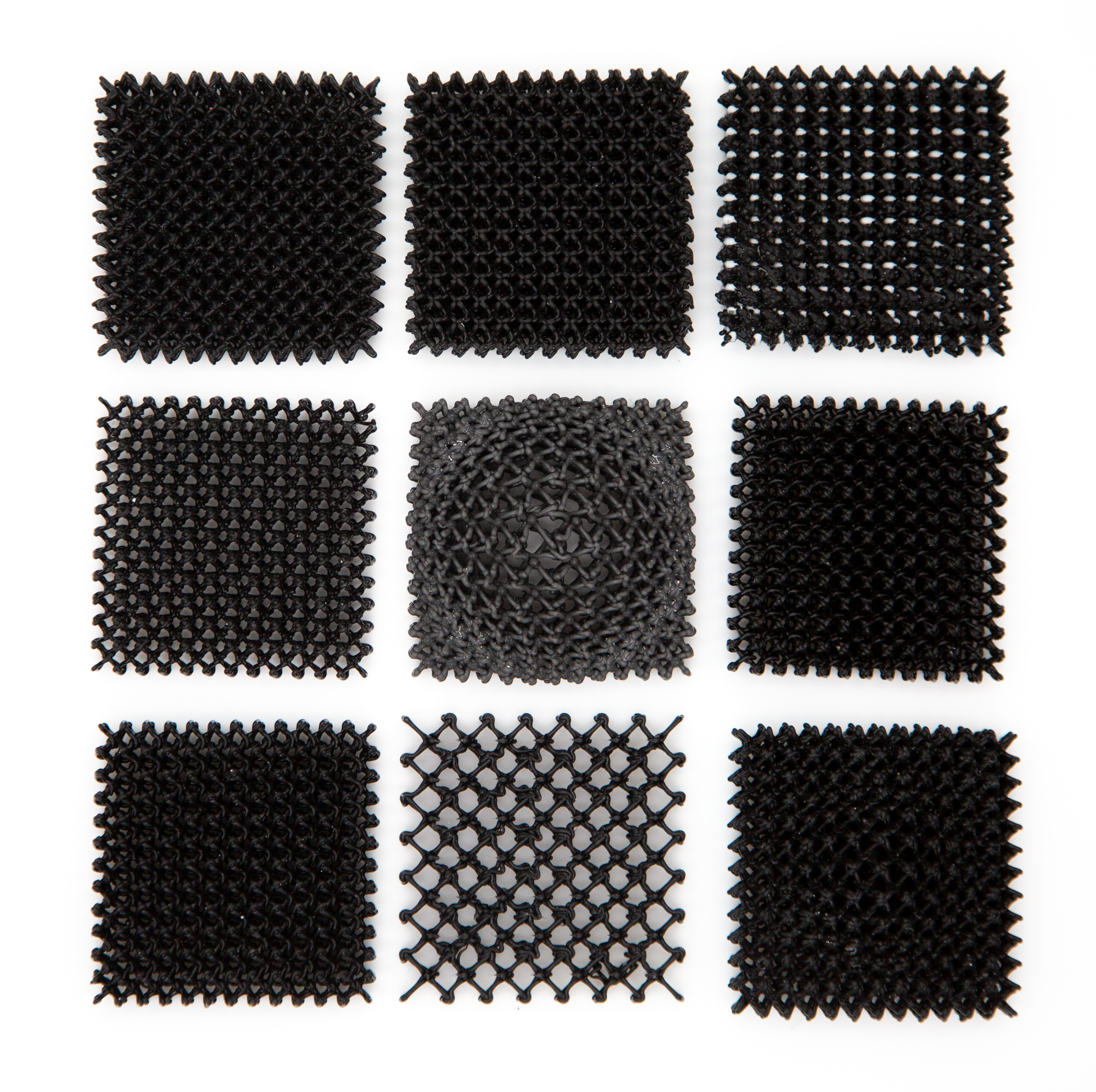
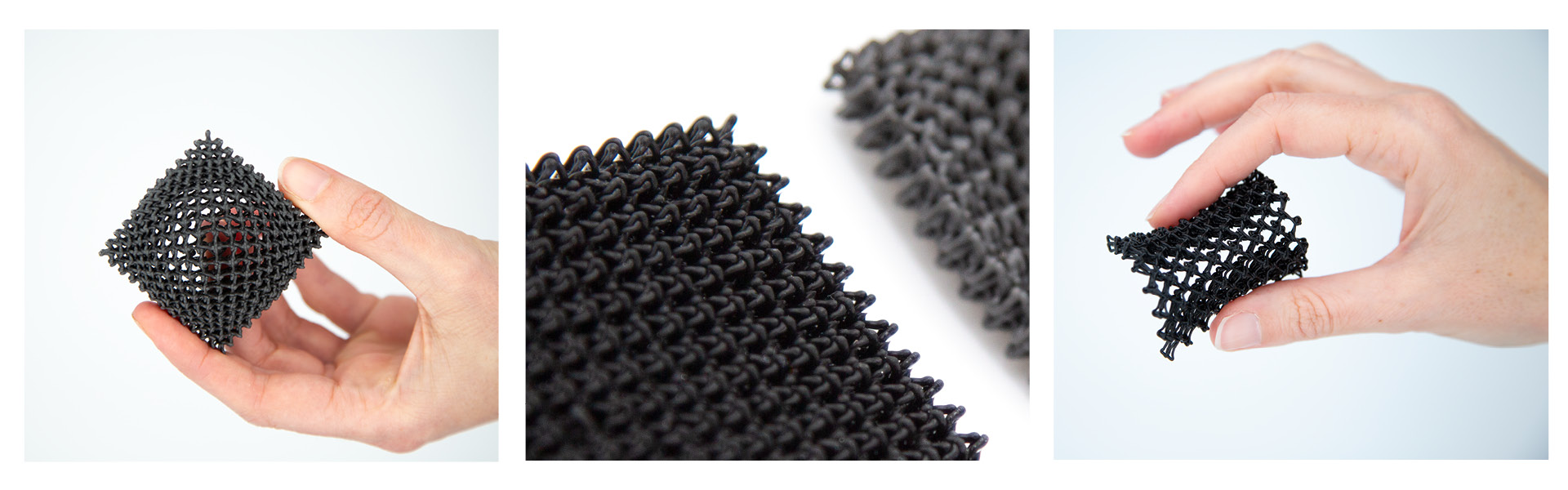
This process enables the creation of lattice structures—repeated patterns that fill a volume or conform to a surface. These structures are ideal for designing lighter parts with properties such as aeration, shock absorption, noise reduction, and vibration damping.
An open technology to address future challenges
Lynxter’s key expertise lies in elastomer 3D printing, thanks to its IDEX machine, the S300X – LIQ21 | LIQ11. As a leader and pioneer in this technology, Lynxter makes complex silicone 3D printing accessible. But its offering does not stop there. With R&D at its DNA, Lynxter continuously pushes boundaries to meet even more demanding manufacturing requirements. This would not be possible without the development of the S300X – LIQ21 | LIQ11 as an open and scalable 3D printer.
We are committed to supporting our prospects and clients in their aspirations by offering an open and tailored solution. Our technology, recognized as innovative by experts and used daily by industry professionals and researchers, is already adapting to the challenges of tomorrow.
Real-world applications of the technology
Some of our clients and partners have been leveraging this technology for years, taking advantage of the design freedom offered by this open machine to push the limits of creativity.
COP is one of our longstanding partners in the development of our expertise in 3D silicone printing. A specialist in polymer chemistry applied to external orthopedic devices, COP has developed a 3D silicone printing solution using an internally formulated support gel. This gel facilitates the deposition of silicone, ensuring precision and stability during the printing process.
COP’s goal is to offer orthotists and prosthetists tailored solutions, among which 3D silicone printing stands out for its ability to meet the sector’s many requirements: customization, comfort, flexibility, lightness, and biocompatibility, among others.
To address various needs, the company has developed and commercialized a gel and a range of skin-contact silicones available in multiple hardness levels (5, 10, 25, and 40 Shore A), allowing 3D printing to be adapted to different orthopedic applications.
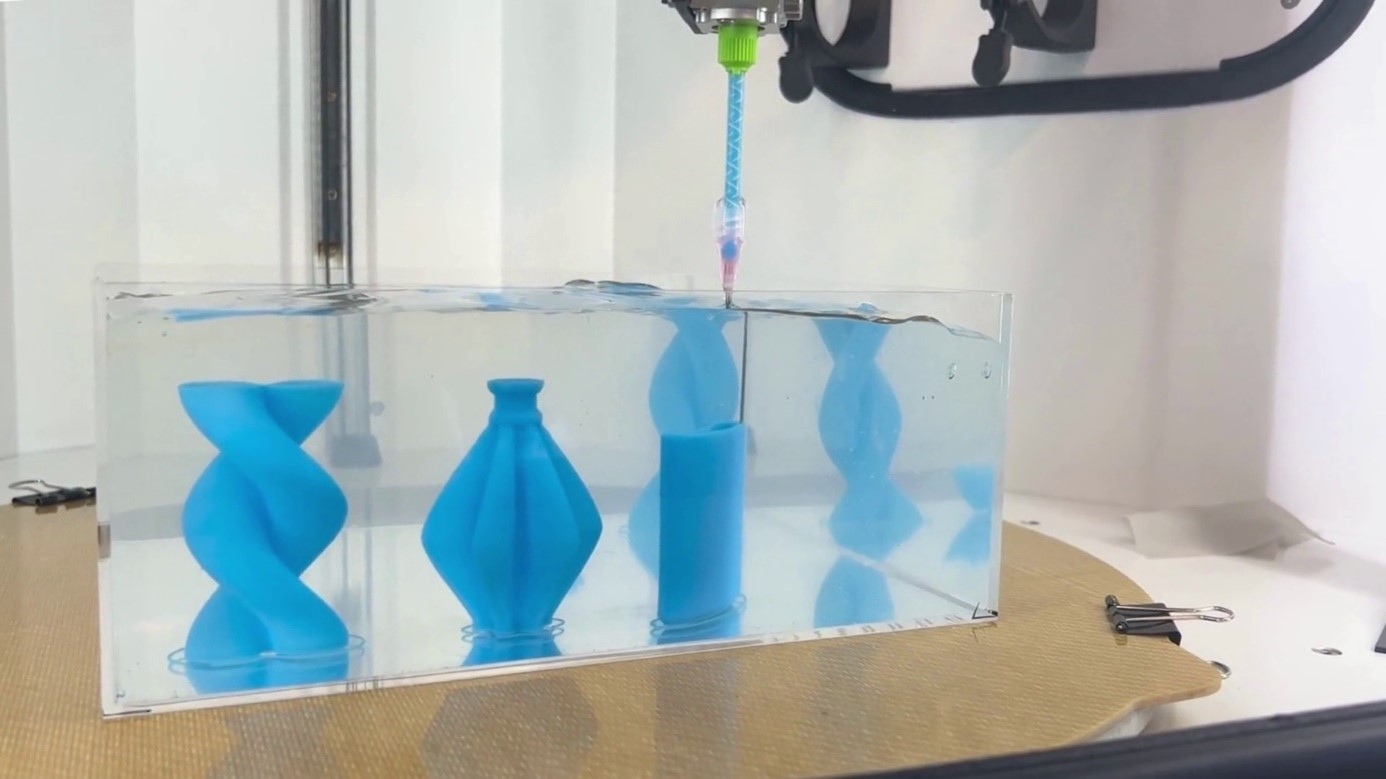
The Biomechanics Institute of Valencia (IBV) is one of our clients using the S300X – LIQ21 | LIQ11 primarily for two applications. First, conducting feasibility studies on 3D printing for anatomical models used in education, particularly for cardiovascular surgery training. Second, manufacturing biomodels that replicate not only size and shape but also texture, especially elasticity. These applications involve complex organic geometries with thin walls, making them particularly suited for gel-suspended printing.
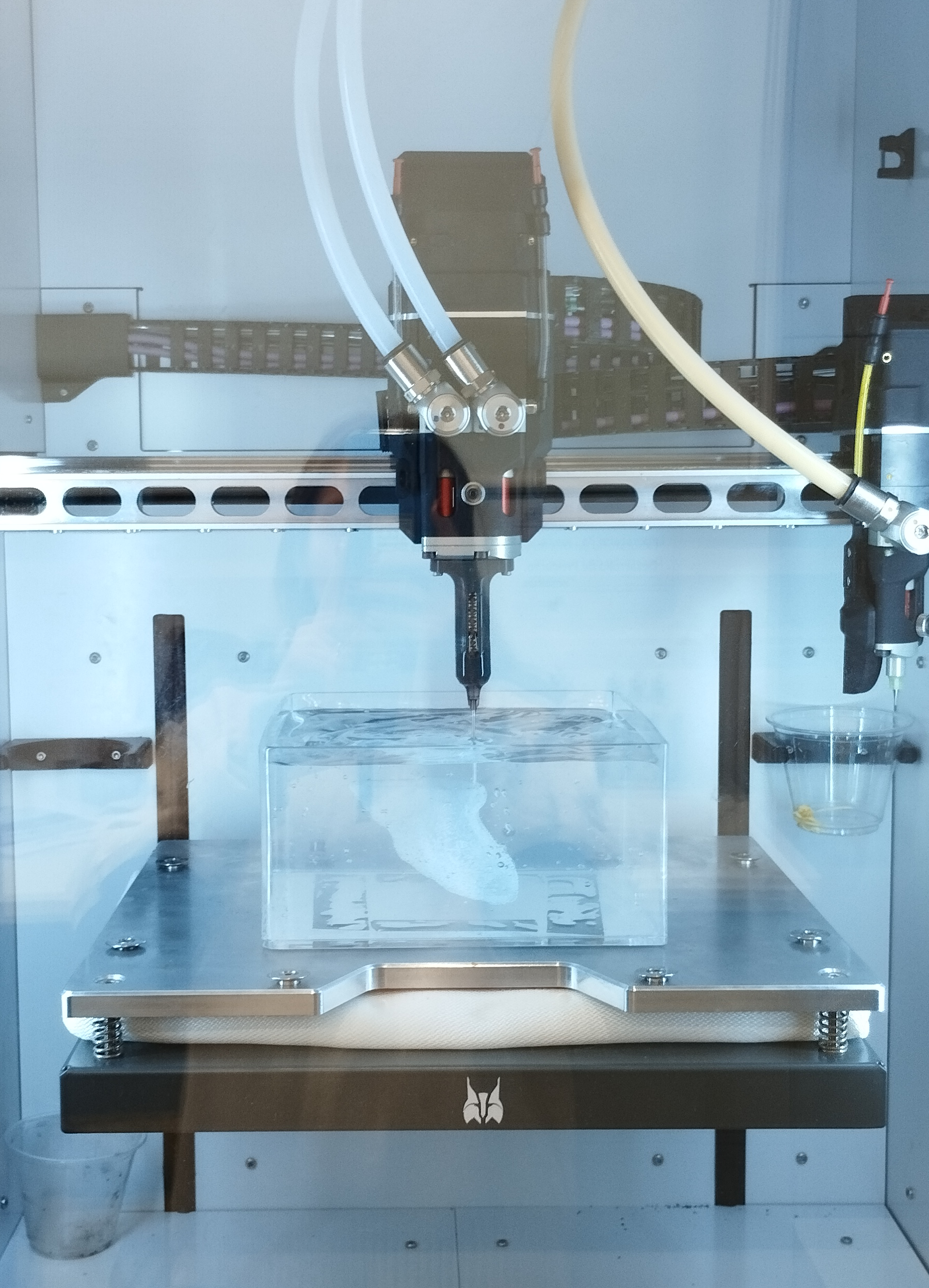
To further expand the material properties of elastomers printed via Material Extrusion (MEX), swapping the gel bath for a powder bath could be a strategic approach. This method allows for the printing of composite materials using the Dynamic Molding process developed by 3Deus Dynamics, which is also compatible with the S300X – LIQ21 | LIQ11. The Lynxter and 3Deus Dynamics teams are available to answer your questions and support your project development with these new industrial manufacturing processes.