Silicone 3D Printing: Custom Formulation for Innovative Applications
Among the vast number of polymers that can be transformed by additive manufacturing, silicone is one of the most versatile. Combining excellent chemical and thermal resistance, it is suitable for a wide variety of industrial and medical applications.
Implemented through 3D printing, silicone covers a range of uses, from prototyping to spare parts, from custom single-unit production to small and medium series manufacturing.
Since 2017, Lynxter has been developing its expertise in silicone 3D printing. As such, the R&D department supports clients in the creation and formulation of innovative materials to meet demanding industrial and medical applications.
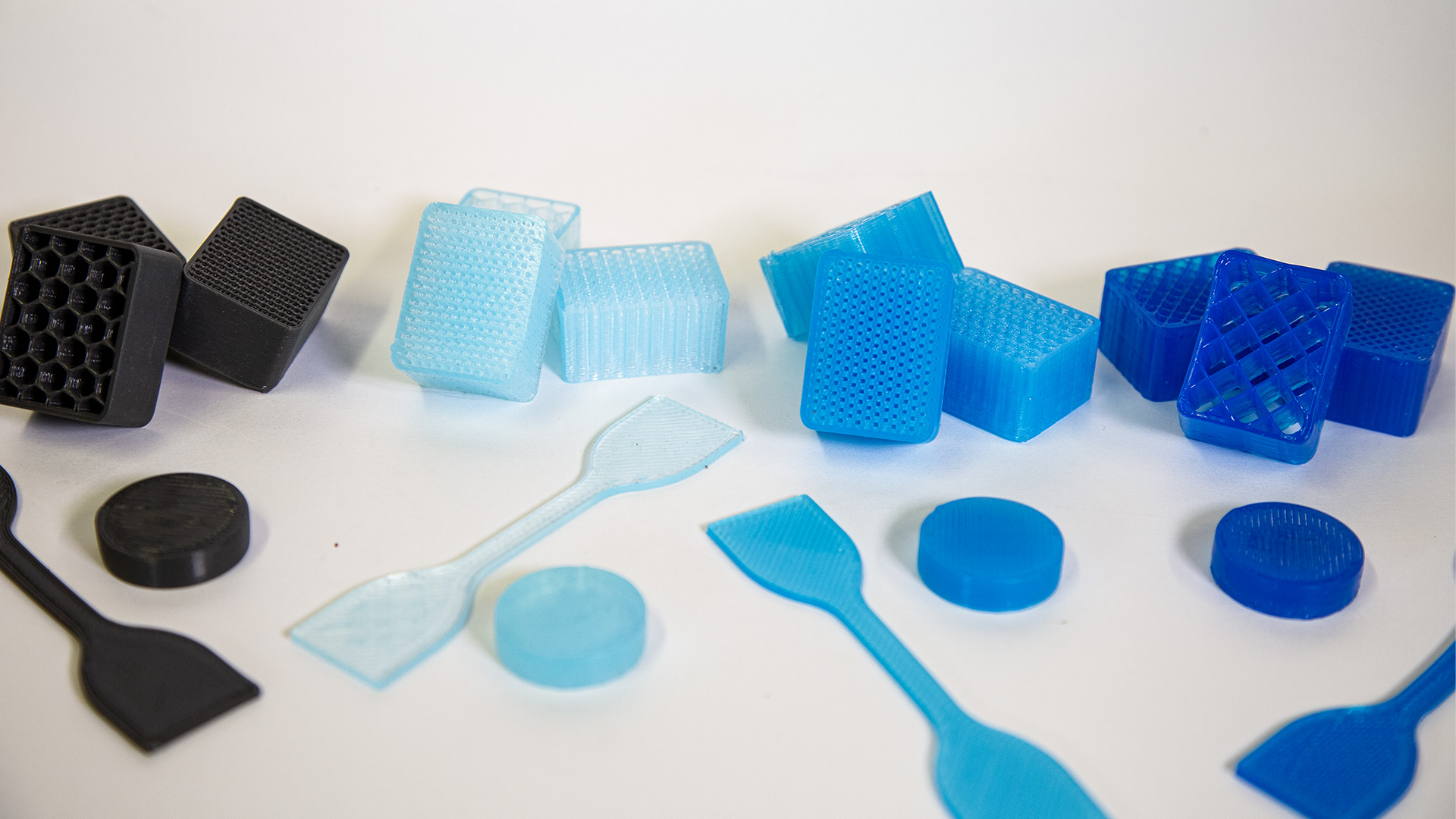
FORMULATE, COLOR, AND PACKAGE CUSTOM SILICONES
The word “silicone” is a common term that refers to polysiloxane polymers.
Polysiloxanes are a family of polymers with a backbone composed of a chain of Si-O bonds (of varying lengths). Polymer chains can be modified and functionalized during synthesis to adjust the final properties of the material: mechanical properties, chemical resistance, thermal resistance, and more.
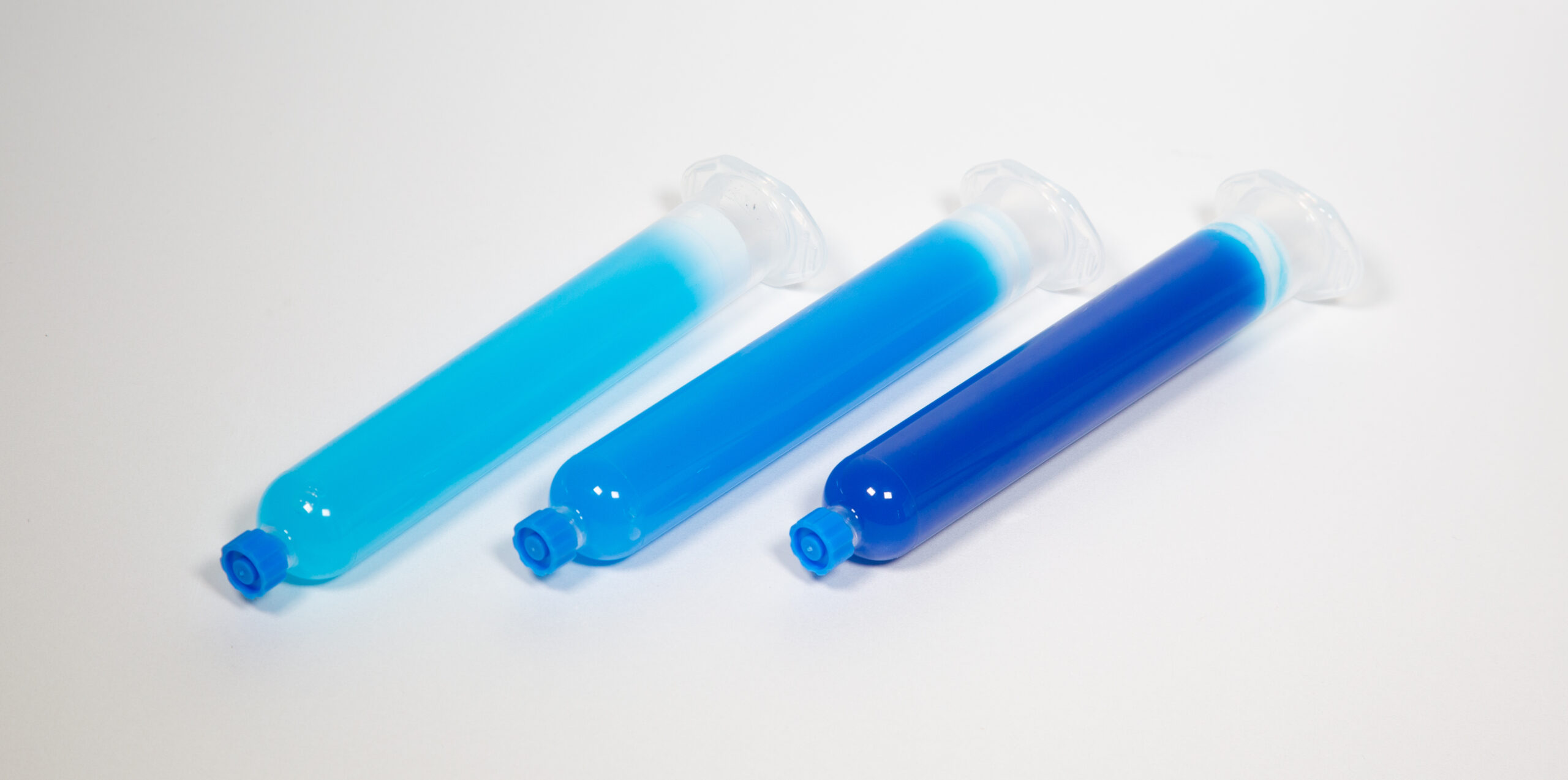
Silicone 3D printing of demonstrators
During the formulation stage, certain additives, fillers, or pigments can be added to alter the polymer’s behavior and final properties:
- Mechanical properties: By adjusting the formulation, it is possible to improve tear resistance or increase silicone hardness, for example
- Optical properties: A wide range of dyes or pigments can be used to modify the color or opacity of the material
- Viscosity and ease of processing
- Fire resistance, magnetic properties, etc.
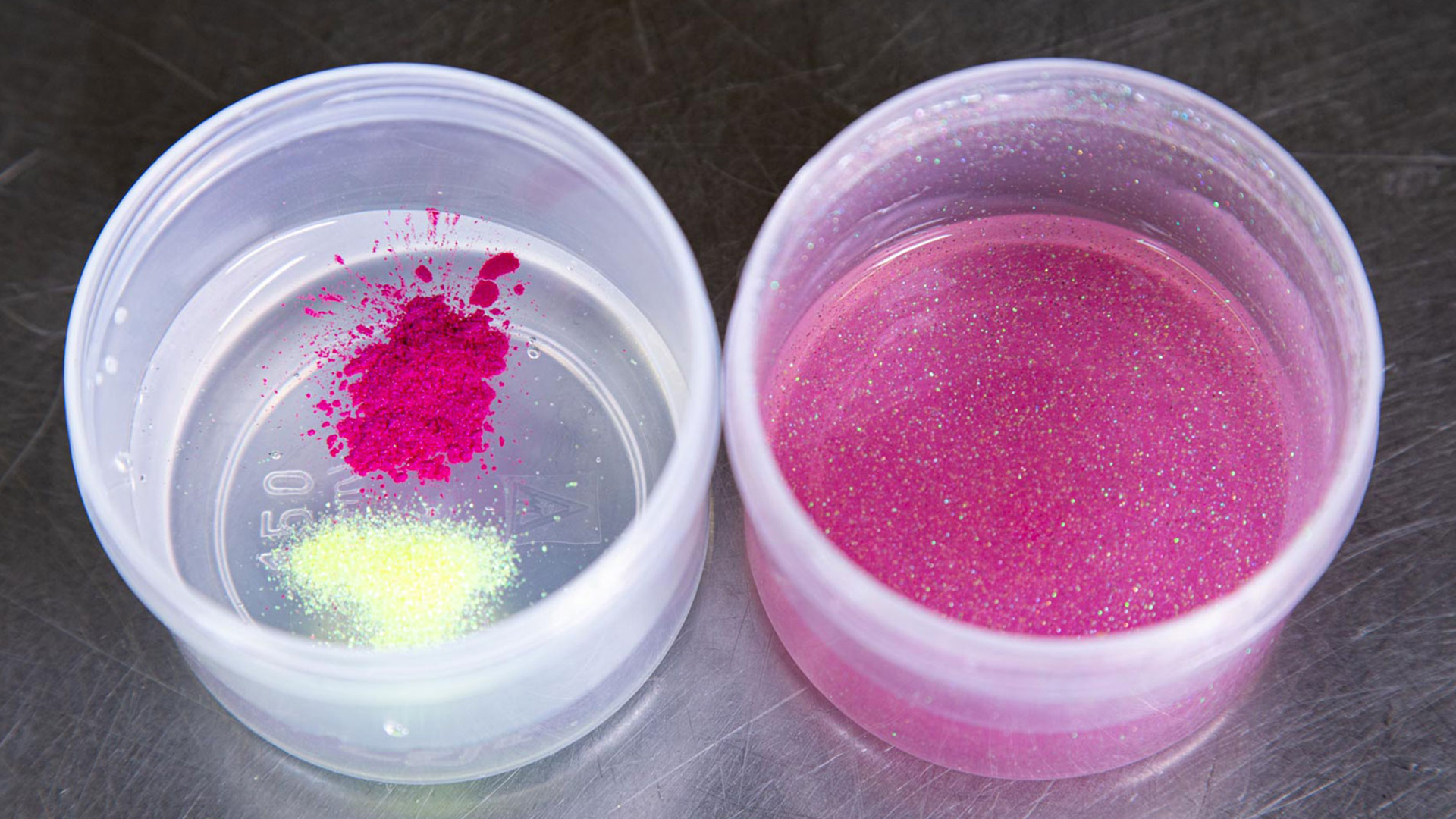
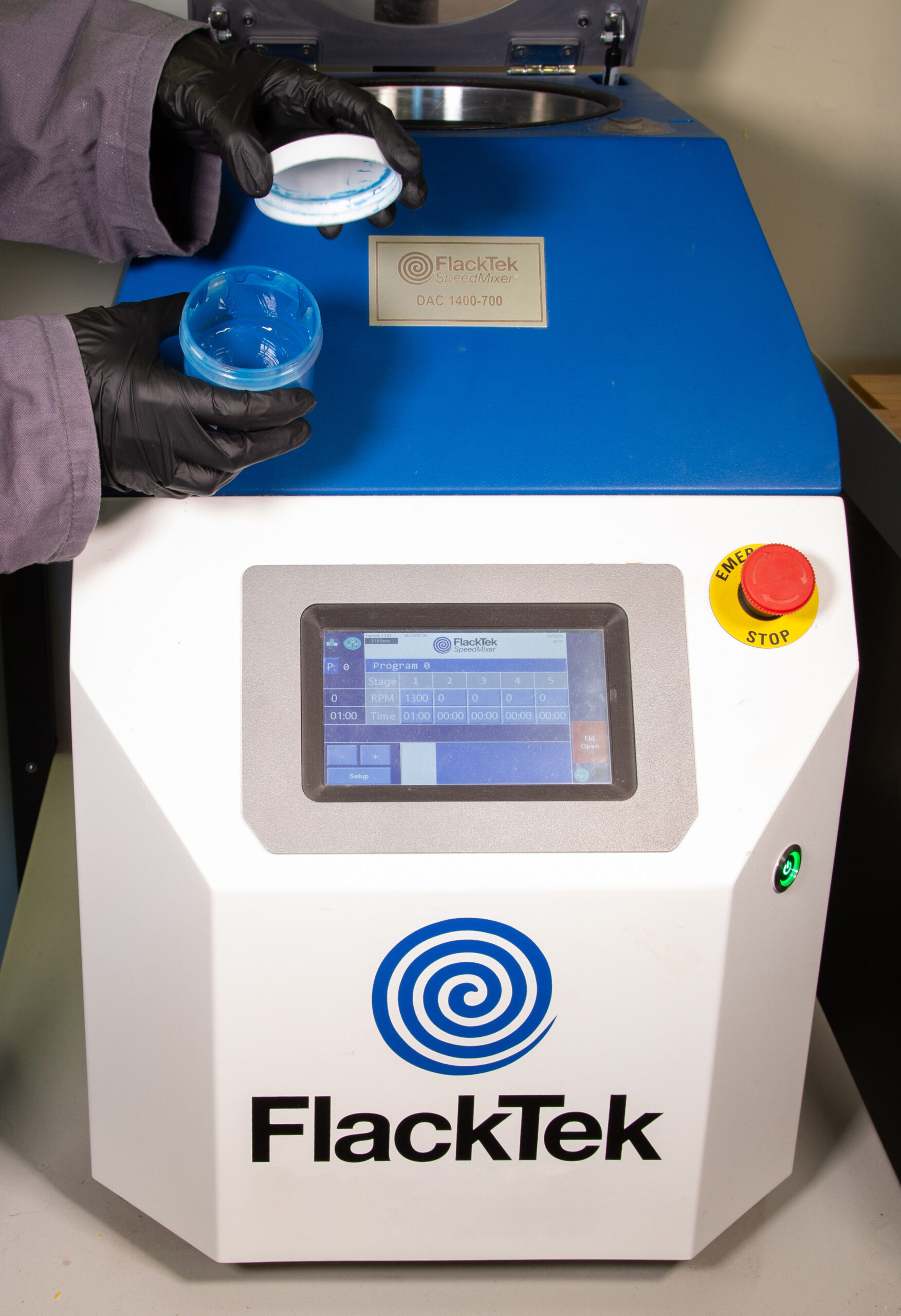
Mixing the material with the FlackTek mixer
The formulation of silicones opens the door to applications that address specific technical challenges for prototyping or functional part production. The addition of pigments, for example, allows the creation of custom-colored silicone guards. Functional fillers can also enhance certain specific properties, such as fire resistance for the rail and aerospace sectors, conductivity for electronics, or new virucidal properties for the medical field. Silicone can be easily customized using a planetary mixer, such as the one from FlackTek.
Custom formulations also help meet specific industry standards and regulations, ensuring the compliance of finished products. This is particularly crucial in sectors such as automotive, aerospace, and medical, where performance and safety requirements are very stringent.
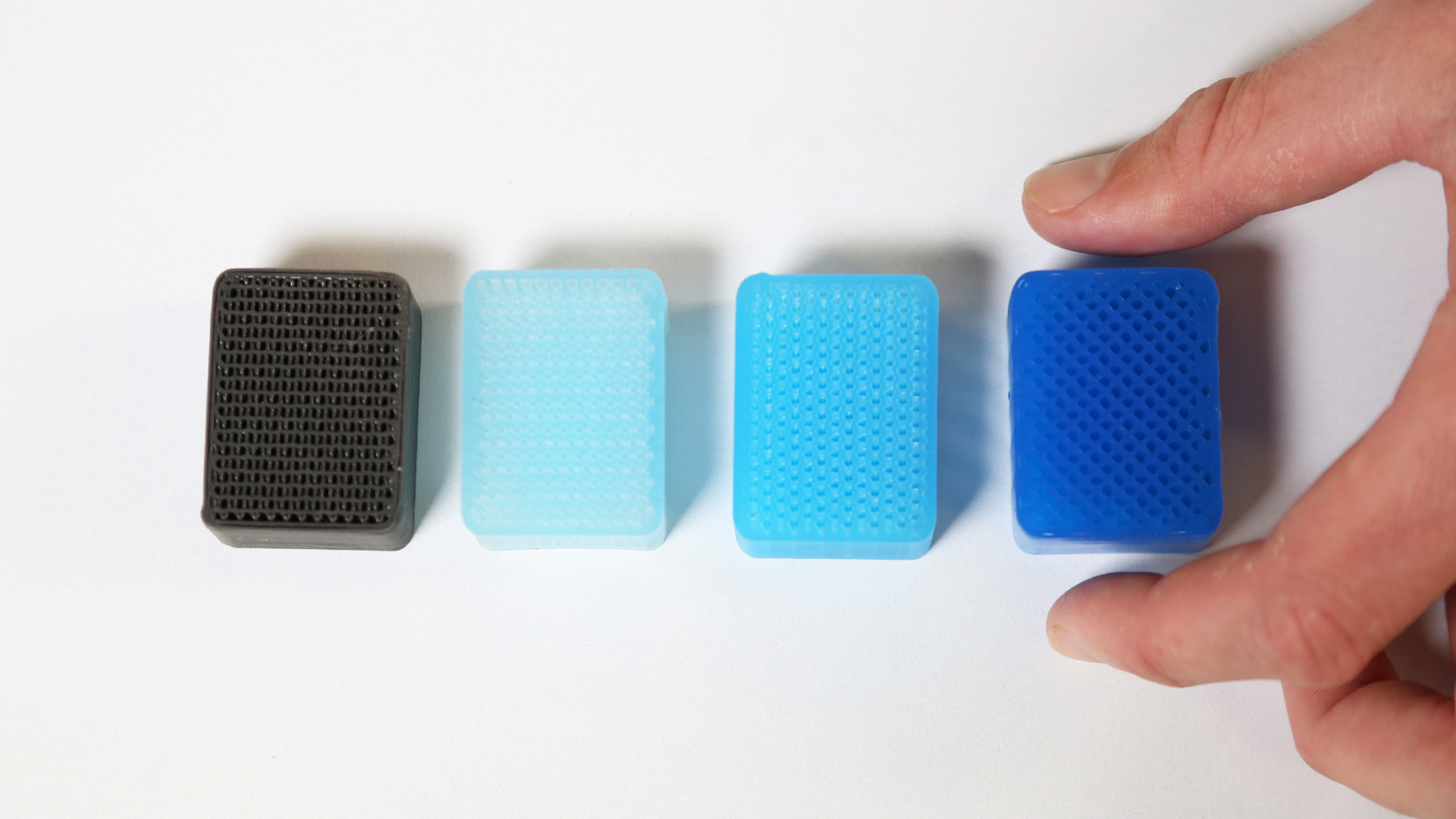
CHARACTERIZING SILICONES TO OPTIMIZE 3D PRINTING PERFORMANCE
Thanks to their heat resistance, biocompatibility, and elasticity, silicones have become essential materials for a wide range of applications.Thermal resistance:High Temperature: Silicones can withstand high temperatures, up to 250°C in continuous use, and in some specific cases, up to 300°C. Low Temperature: They remain elastic and functional at very low temperatures, often below -60°C, ideal for applications exposed to extreme environments.Chemical Resistance: Silicones are resistant to many chemicals, including oils, solvents, acids, and bases, making them particularly suitable for wet masking applications, fluid sealing, or food and medical applications that require thorough cleaning.
Silicone hardness analysis
Silicone elongation test
- Tensile strength: Using a tensile machine, the objective is to measure the maximum force at which the test specimen, with a known cross-section, breaks. This breaking stress is associated with maximum deformation (elongation at break). These values make it possible to compare the tensile strength of two materials and guide material selection, for example, by increasing thicknesses to ensure better resistance.
- Hardness (shA): The Shore A hardness scale allows for the comparison of different elastomers based on their hardness. It indicates the resistance of the part to penetration or deformation under pressure.
- Tear resistance: Similar to tensile strength testing, this test is conducted on a pre-notched specimen. The test measures the maximum force at which the pre-notched specimen breaks, demonstrating its ability to resist tear propagation.
- Compression set: A standardized specimen is compressed at a specific rate for a set duration and placed in an oven at a given temperature. After cooling and release, the specimen is measured to obtain the observed residual compression. This metric indicates the part’s ability to return to its original shape after compression and is useful for determining deformability and elastic recovery, such as for seals.
- Resilience – rebound: This metric quantifies the amount of energy returned by a material. If the value is low, the materials are particularly suitable for energy absorption applications; if the energy returned is high, the material has good rebound properties.
- Chemical resistance: Various test specimens of the same material are immersed in solvents, oils, acid-base solutions, and hydrocarbons. After immersion, the specimens are measured to assess swelling. After 24 hours out of the solution, mechanical tests (such as those previously presented) are performed to measure any loss or retention of mechanical properties due to fluid exposure.
All of these characterizations are crucial to outline the technical profile of a material, but they also contribute to a better understanding of the process and the impact of printing parameters on the performance of parts obtained by additive manufacturing. Indeed, silicone parts obtained through MEX additive manufacturing have the same properties as silicone parts obtained by casting or molding. The silicone crosslinking reaction takes place during and after printing, creating covalent chemical bonds between layers. This enables the production of fully isotropic parts.
MASTERING AND ENSURING THE PRINTABILITY OF LIQUID MATERIALS
Silicone rheological testing
- Optimization of printing parameters
- Development of new innovative materials
- Quality control and assurance of printing performance
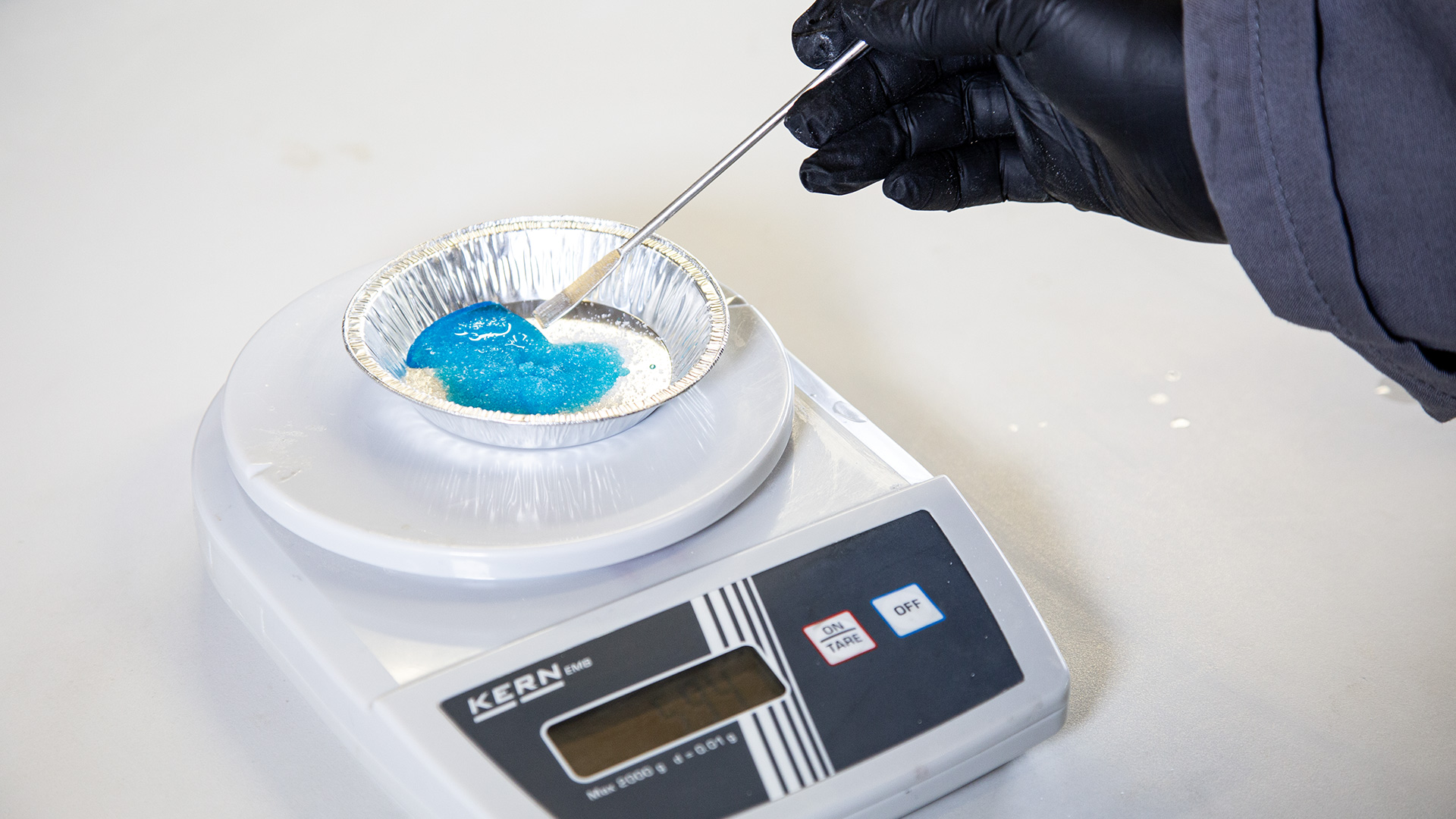
WHY CHOOSE LYNXTER FOR SILICONE 3D PRINTING?
For seven years now, Lynxter has established itself as a key player in the field of silicone 3D printing, offering innovative and tailored solutions for various industrial and medical applications.
- Expertise: Lynxter masters the entire 3D printing process, from material design to final printing, including printable support.
- Quality control: Enhanced quality control (verification of repeatability and traceability of batches produced by Lynxter)
- Support: Material experts pay special attention to each R&D project to ensure successful developments on the S300X – LIQ. Find all the design guidelines related to 3D printing of elastomeric liquid materials here.
- Custom formulation development: With specialized equipment and a network of formulation partners, Lynxter can assist clients in developing custom silicone formulations that precisely meet their needs.
- Specific grades: Design of ready-to-use technical materials that meet specific specifications and regulatory frameworks
- MEX: All liquid materials available in the Lynxter material range are formulated to behave appropriately for MEX additive manufacturing. These precision tools also support the quality control of our materials at the end of production.
To discover how our silicone solutions can transform your projects, do not hesitate to contact us.