NIRYO x LYNXTER : AN INNOVATIVE PARTNERSHIP FOR BESPOKE ROBOTIC SOLUTIONS
The field of soft robotics—both industrial and educational—is in constant evolution, with an ever-growing demand for flexible and adaptable gripping tools. This is precisely what led to the collaboration between Niryo, a manufacturer of educational and professional robots, and Lynxter, a leader in industrial 3D printing and a specialist in silicone 3D printing. Together, they are optimizing robotic solutions and their applications.
Niryo, a French company specializing in the design of 6-axis collaborative robotic arms since 2017, focuses on educational solutions while also integrating professional robots to streamline and enhance industrial processes in an intuitive and secure manner.
Lynxter, renowned for its expertise in multi-material 3D printing — particularly in silicone 3D printing — enables the creation of highly customizable grippers. These advanced gripping tools provide unmatched flexibility and precision, manufactured using Lynxter’s cutting-edge 3D printers, including the S300X – LIQ21 | LIQ11, which leverages IDEX technology to fabricate complex structures.
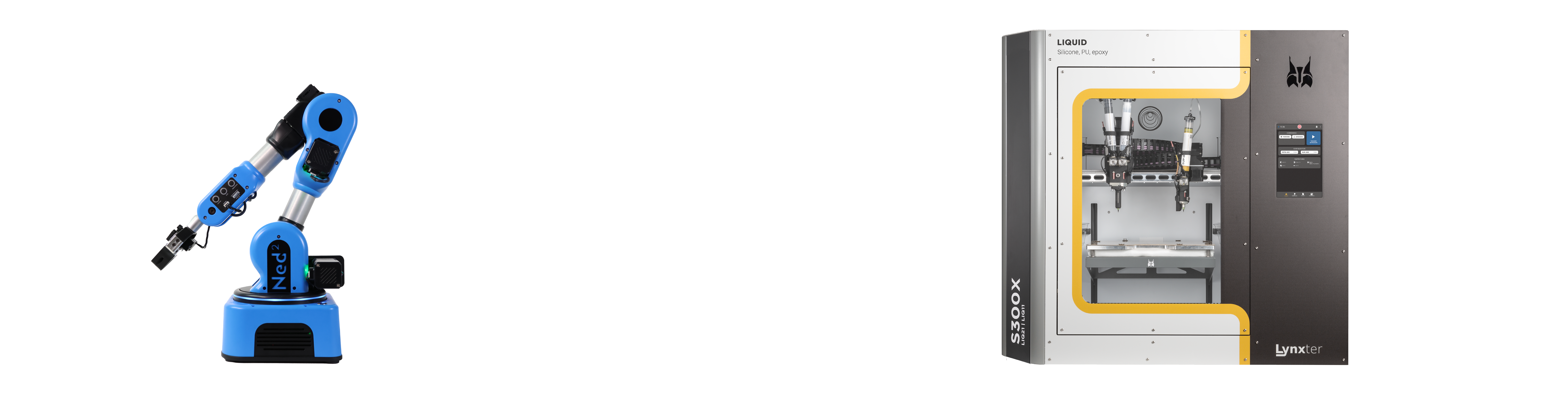
3D PRINTING AND SOFT ROBOTICS
Robots require gripping tools capable of adapting to a wide range of tasks, from handling delicate objects to transporting irregularly shaped loads. By 3D printing silicone grippers, Niryo enhances the versatility and efficiency of its robots, ensuring seamless integration into its robotic ecosystem.
The collaboration will be officially presented at Formnext 2024, showcasing its impact on the future of robotics.
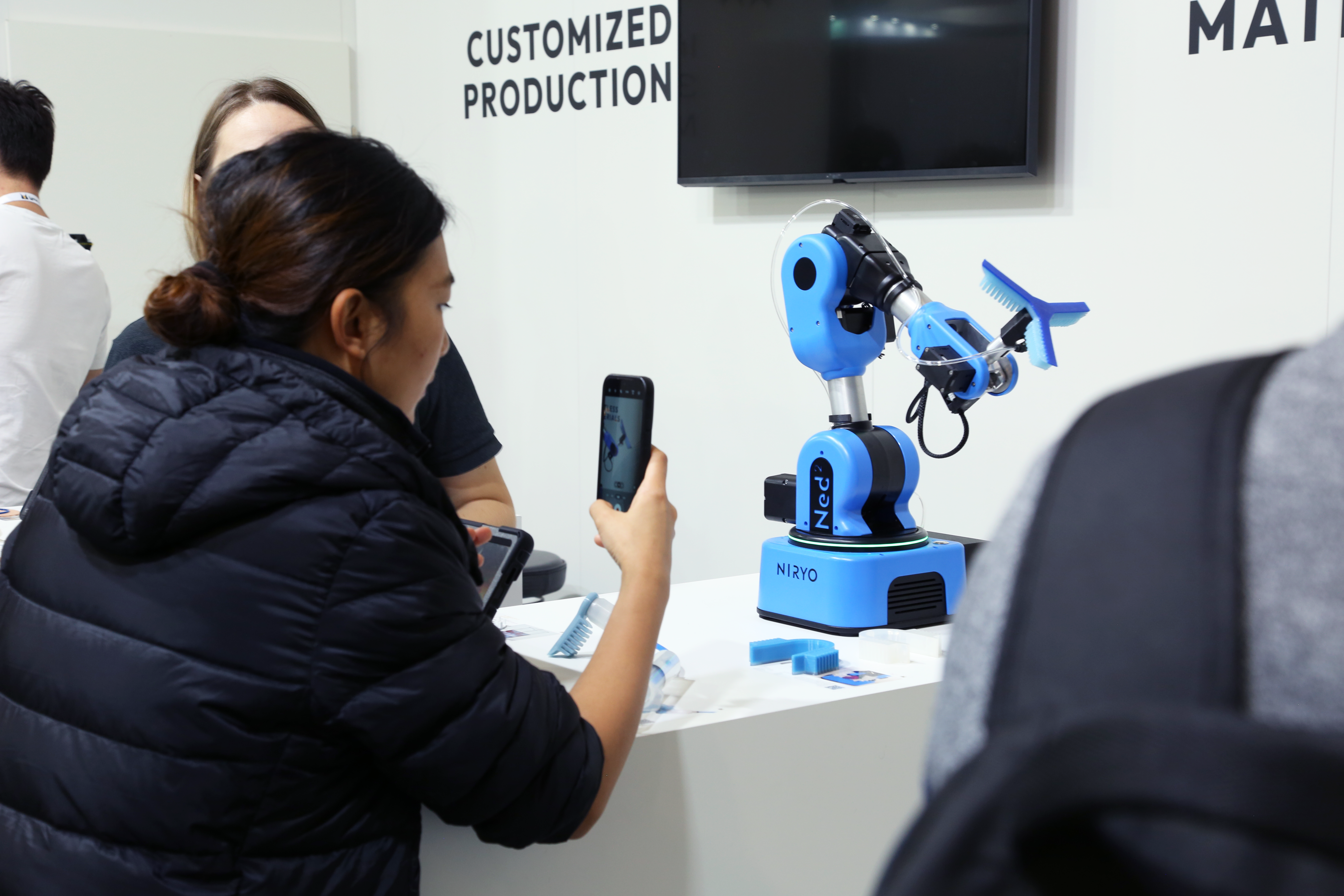
CUSTOMIZED SILICONE 3D-PRINTED GRIPPERS
A key advantage of this partnership lies in the customization of grippers. Lynxter’s expertise in silicone 3D printing allows for tailor-made solutions that meet the specific needs of Niryo’s clients. Whether for R&D projects, handling delicate components, food products, or industrial parts, the grippers can be adjusted in shape, texture, rigidity, color, and size.
This innovative approach enables rapid and easy integration onto robots, offering a true plug-and-play experience that minimizes setup time and costs. Traditional methods require extensive resources to design silicone parts for robotics, including mold creation and material casting. Moreover, conventional molding techniques struggle to accommodate the intricate designs of grippers, which often feature internal channels, cavities, and flexible deformation angles. Only liquid IDEX 3D printing can achieve such complexity with efficiency.
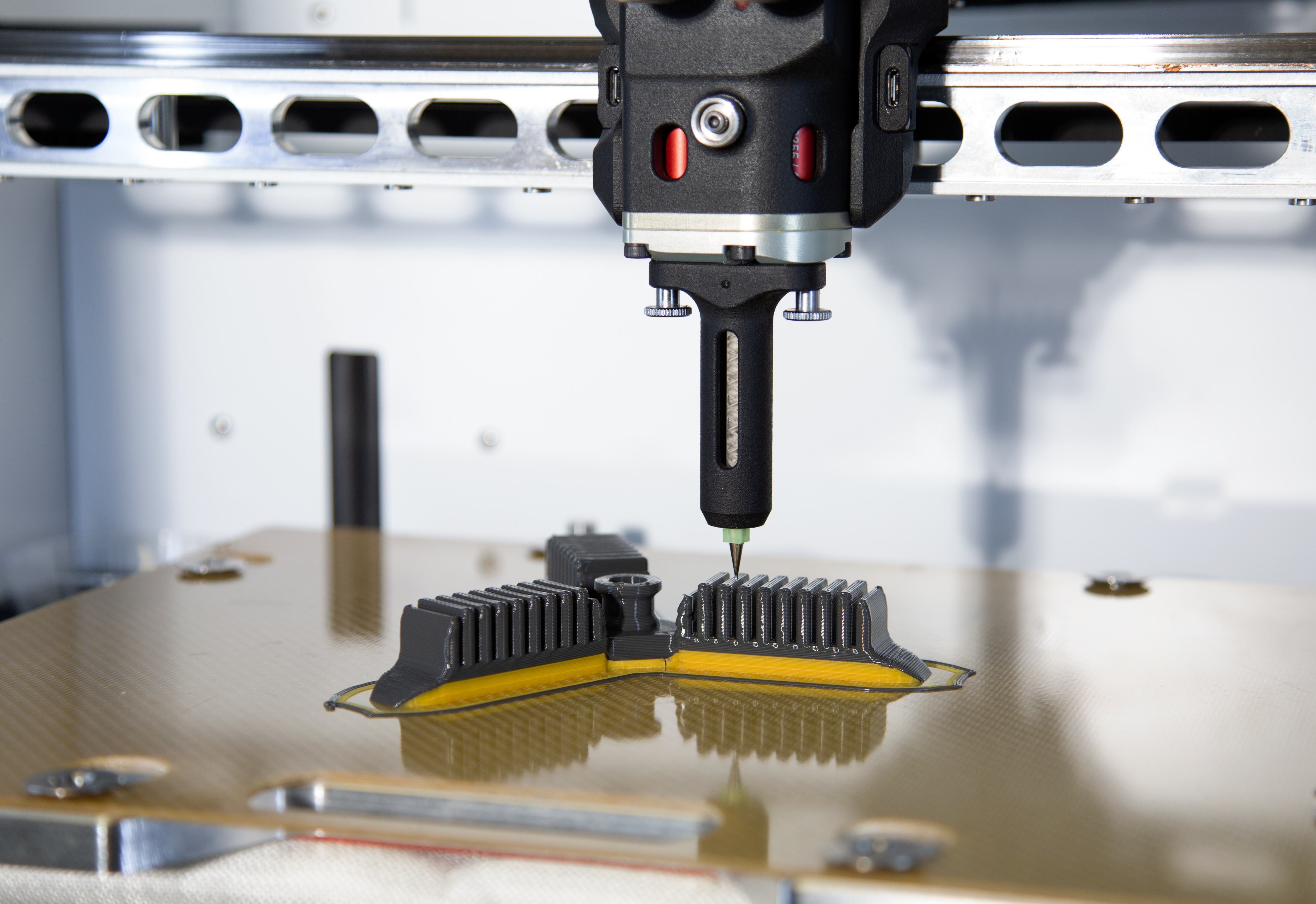
SILICONE: THE IDEAL MATERIAL FOR SOFT ROBOTICS
Mastering the design of soft robots goes beyond shaping the structure—it also involves optimizing the deformation properties of the material to achieve the desired movement. Silicone is particularly suited for soft robotic applications due to its ability to deform under minimal stress, high elasticity, and excellent wear resistance.
A VERSATILE SOLUTION FOR MULTIPLE INDUSTRIES
Soft robotics takes many forms: grippers, suction cups, flexible pincers, crawling robots, and more. 3D printing enables the production of these highly adaptable components for diverse industries, including:
- Agri-food: Handling delicate food products
- Logistics: Transporting items of various shapes and sizes
- Healthcare: Manipulating medical instruments and pharmaceutical products
- Education & R&D: Providing students, educators, and researchers with innovative tools to explore new applications in robotics and additive manufacturing
ENHANCED CONTROL THROUGH SILICONE 3D PRINTING
Silicone 3D printing offers full control over key parameters:
- Geometry: creating complex shapes that would be impossible with traditional methods
- Texture: optimizing surface finishes to match industrial requirements or specific projects
- Rigidity: adjusting flexibility through multi-density silicone printing
- Functional integration: embedding features such as pressure sensors, a breakthrough developed by R&D engineer Brice Parilusyan using 3D printed silicone.
For more details, the summary of his research thesis is available in our dedicated article.
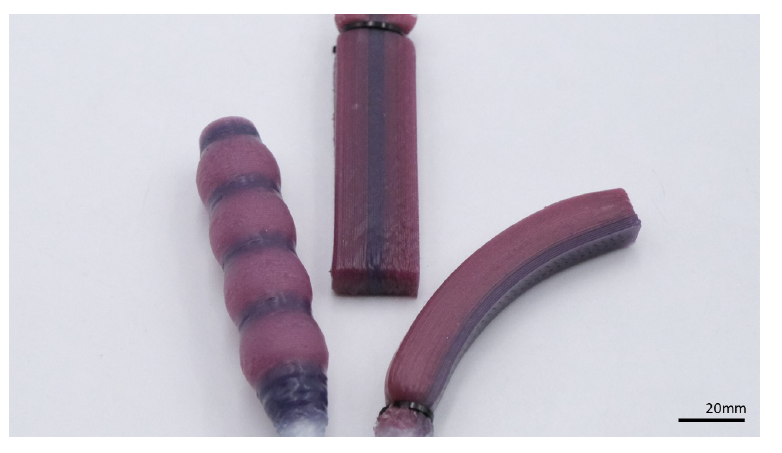
A PERSONALIZED APPROACH FOR YOUR PROJECTS
This partnership between Niryo and Lynxter opens new horizons for the robotics sector, bringing innovative solutions to life. Together, they provide a plug-and-play ecosystem designed to accelerate R&D projects. Whether for industries, educational institutions, or research centers, this collaboration delivers customized, efficient, and future-proof robotic solutions.
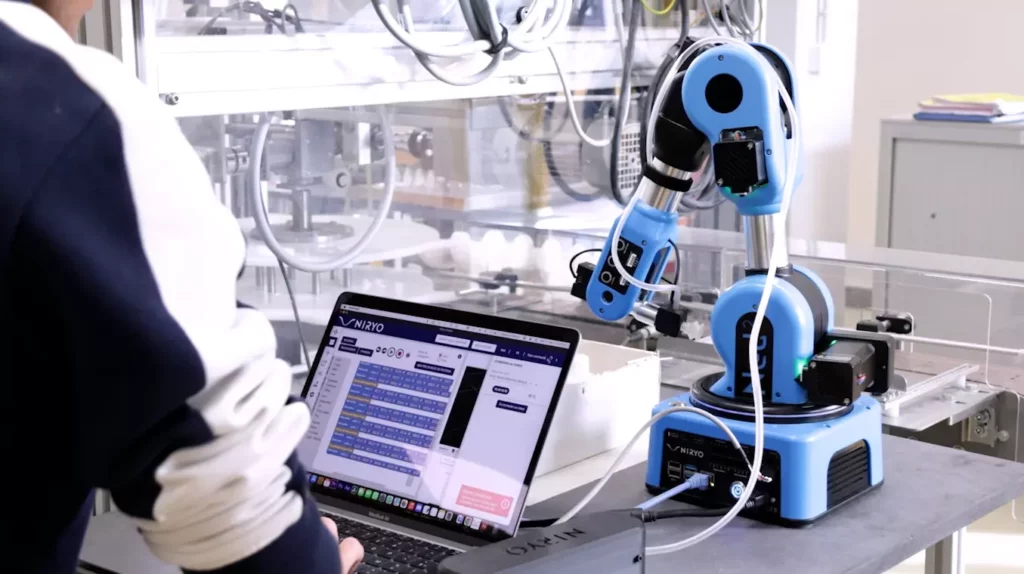
ABOUT NIRYO
Since 2017, Niryo has been developing 6-axis collaborative robotic arms, offering turnkey educational solutions for all levels. As of 2024, the company has expanded its offerings to researchers, industrial players, and professionals, providing seamless and secure robotic integration. These solutions are designed to relieve workers from repetitive and strenuous tasks, enhancing efficiency in production environments.
Learn more about silicone 3D printing and soft robotics with our e-book :