SILICONE 3D PRINTING GUIDE: LIQUID DEPOSITION
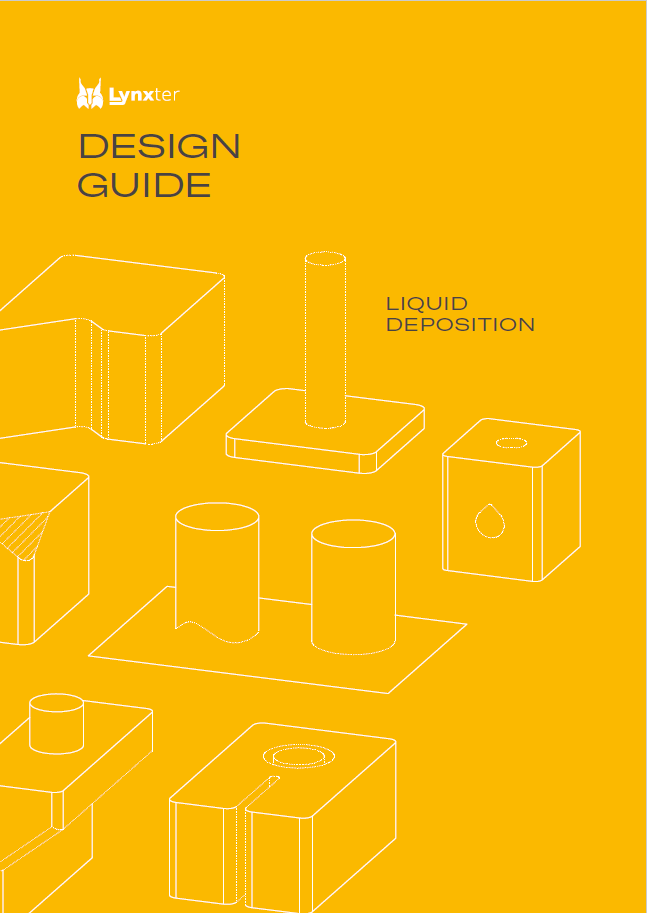
SILICONE 3D Printing
Design guide 2023
Discover our new guide for the design and production of 3D printed parts using liquid deposition, with and without support.
Download our guide by providing your email below.
EXCERPT
Optimal Printing guidelines
Additive manufacturing of liquids and pastes should, as with all processes, be performed in accordance with design rules. In this process, fine strings of material are added layer-upon-layer to create a part.
This process is similar to Fused Filament Fabrication (FFF, MEX or FDM) but differs in that the string of material laid down does not harden or in this case, does not “cure” in a matter of seconds. Moreover, the printed parts can be very soft and flexible and certain precautions must be taken when designing them.
This document provides advice and key dimensions, highlighting areas where particular care should be taken when designing your parts in order to achieve the best results when printing.
-
DIMENSIONS OF STRING
When depositing fluids, the string of material is less compressed than with thermoplastic filament; layer height is superior, whereas extrusion width is similar to the diameter of the nozzle.
0.4 x ø Nozzle < Lh < 0.7 x ø Nozzle
0.8 x ø Nozzle < Ew < 1.15 x ø NozzleSHARP ANGLES
Avoid protruding edges on XY.Instead use a connecting radius of:
2x Nozzle diameter