3D Printing: An Essential Asset for Production Tooling and Prototyping For Almay
Since its democratization, 3D printing has allowed manufacturers to gain autonomy in the production of tooling parts, prototype development, and even the manufacturing of maintenance parts.
Based near Poitiers, ALMAY Technologies, a major player in the design and manufacturing of mechanical parts and sub-assemblies, first integrated additive manufacturing with the S600D, a modular 3D printer with its FIL21 filament tool head and LIQ21 bi-component liquid tool head. Thanks to this technology, ALMAY’s teams produce production tooling and prototypes using thermoplastic and elastomeric materials (silicones and polyurethanes). This reduces both the time and cost of development associated with these traditionally outsourced operations.
Additive Manufacturing at ALMAY Technologies
Integrated into the company’s expertise alongside other manufacturing processes, 3D printing has become a central axis of innovation.
Mastered by dedicated teams trained by Lynxter, additive manufacturing enables ALMAY Technologies to internally produce draping tools and positioning counterforms for its composite part and sub-assembly manufacturing activities.
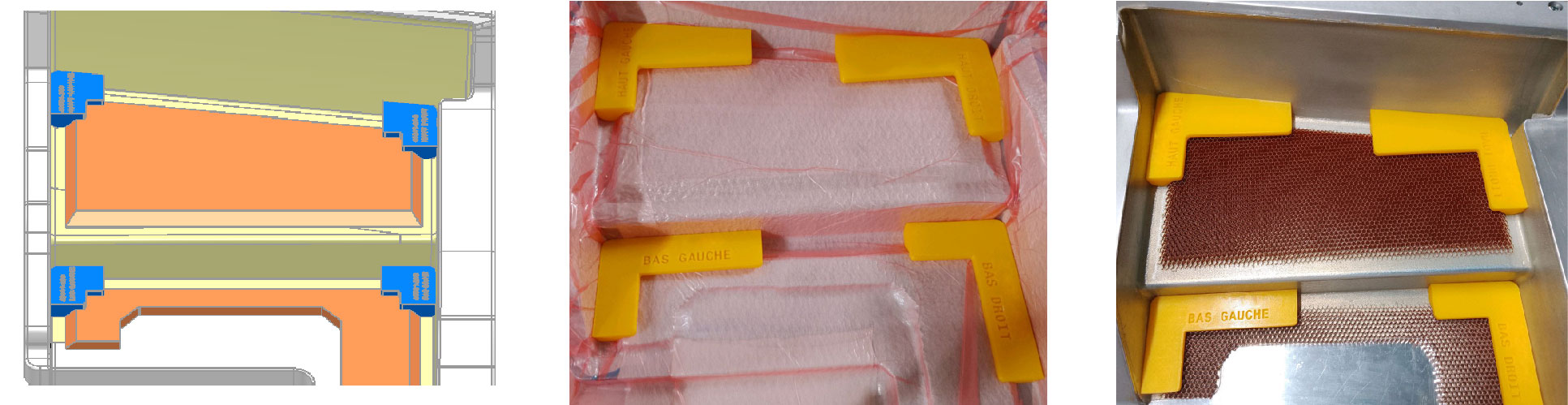
3D printed parts allowed the correct positioning of honeycomb structures during the production of composite parts. Manufacturing parts using composite manufacturing processes often requires multiple iterations to finalize and qualify the method. Tooling may therefore need to evolve (dimensions, mechanical properties, materials, etc.). 3D printing facilitates these iterations by eliminating time and cost constraints. Additive manufacturing is space-efficient, easy to operate, and excels in unit or small series production. By internalizing the production of tools and prototypes, companies can manage risks and confidentiality while also increasing responsiveness and expertise.
Ultimately, unlike conventional processes, additive manufacturing allows easy modification of the internal structures of parts and tooling (fill rate, honeycomb/lattice structures), optimizing print time, weight, and internal production costs.
The Impact of 3D Printing on Process Efficiency and Speed
The adoption of 3D printing has led to significant time and efficiency gains at ALMAY. While cost savings vary depending on project scope, 3D printing consistently proves to be a cost-effective solution.
By bypassing traditional manufacturing workflows—such as design, file programming, and machining—this technology saves time by reducing production lead times, sometimes from several days to just a few hours. This acceleration enhances the “time to market,” a growing priority for ALMAY’s clients.
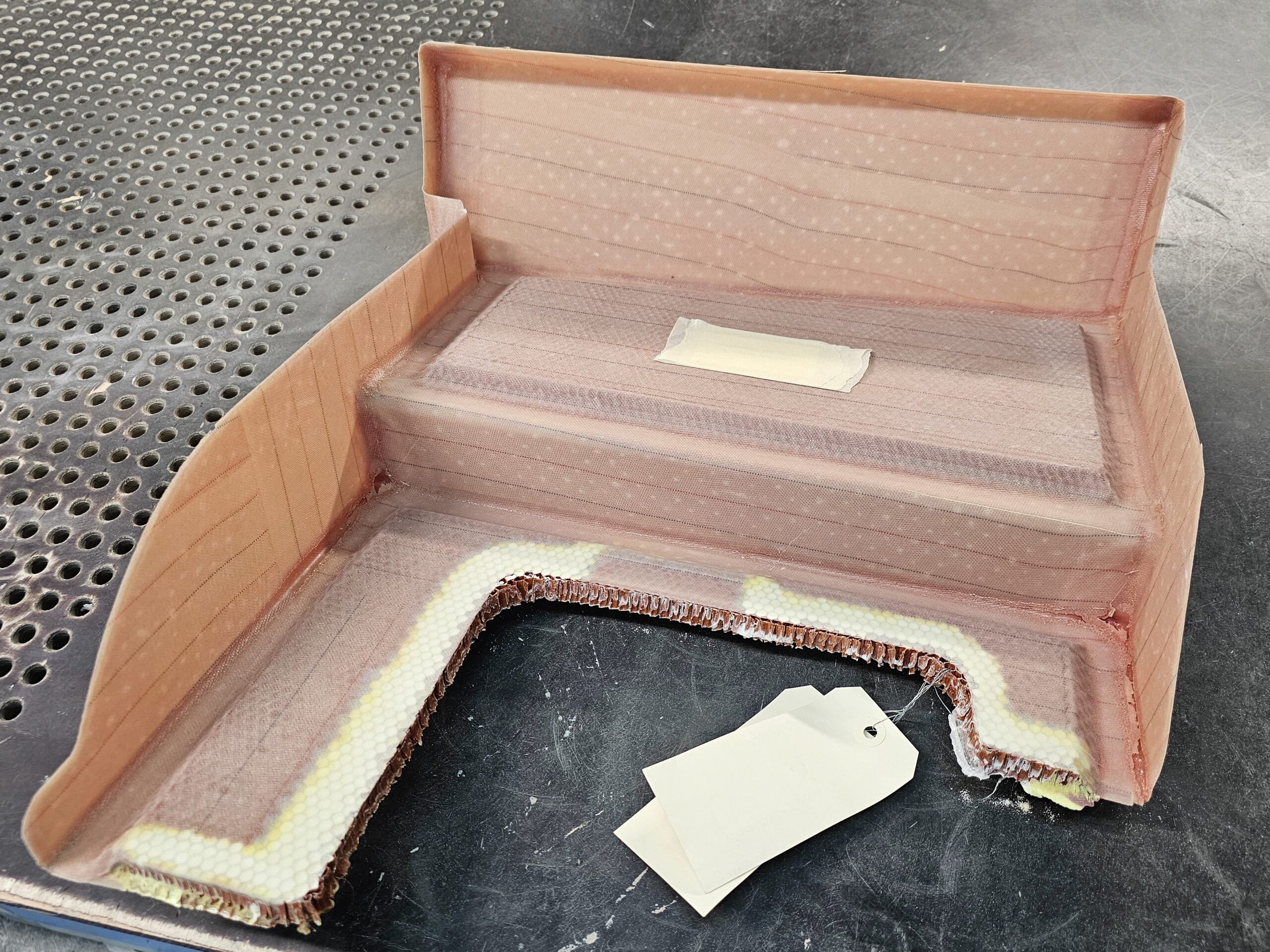
The S600D: Modularity, Volume, and Technical Materials
Chosen for its volume capacity and technical material compatibility, the S600D enables ALMAY Technologies to print flexible thermoplastic materials such as TPE 95 shA and rigid materials like LYNXTER’s PLA-001. These materials offer an ideal balance of strength and flexibility. For more demanding applications requiring enhanced mechanical properties, ALMAY also uses LYNXTER’s PA-001, a carbon-fiber-reinforced polyamide.
The S300X – FIL 11 | FIL11: Filament 3D Printing
Lynxter recently introduced a new machine, the S300X – FIL 11 | FIL11, a dual independent extruder (IDEX) MEX (FFF/FDM) 3D printer. Designed for ultra-fast speeds and high acceleration, it enables the production of dual-material parts in a single print, significantly reducing manufacturing time. This presents an opportunity for ALMAY to create dual-material components in a single fabrication process.
For its scraper tool, ALMAY required an application featuring a soft section to scrape prepreg fabric surfaces and a rigid section for operator handling. It was also crucial that the soft and hard parts remain inseparable.
In contact with the fabric, it was essential that the soft part left no thermoplastic residue in the prepreg, making material selection crucial. In collaboration with LYNXTER, the ALMAY team opted for TPE-001 for the soft section, which is in direct contact with the fabric, and PLA-001 for the rigid section, which directly contacts the matrix.
3D printing with the S300X – FIL 11 | FIL11 provides ALMAY with a versatile and efficient solution for producing its dual-material tools and prototypes. By strategically integrating this technology into its processes, the company is paving the way for a new era of agile and innovative manufacturing.
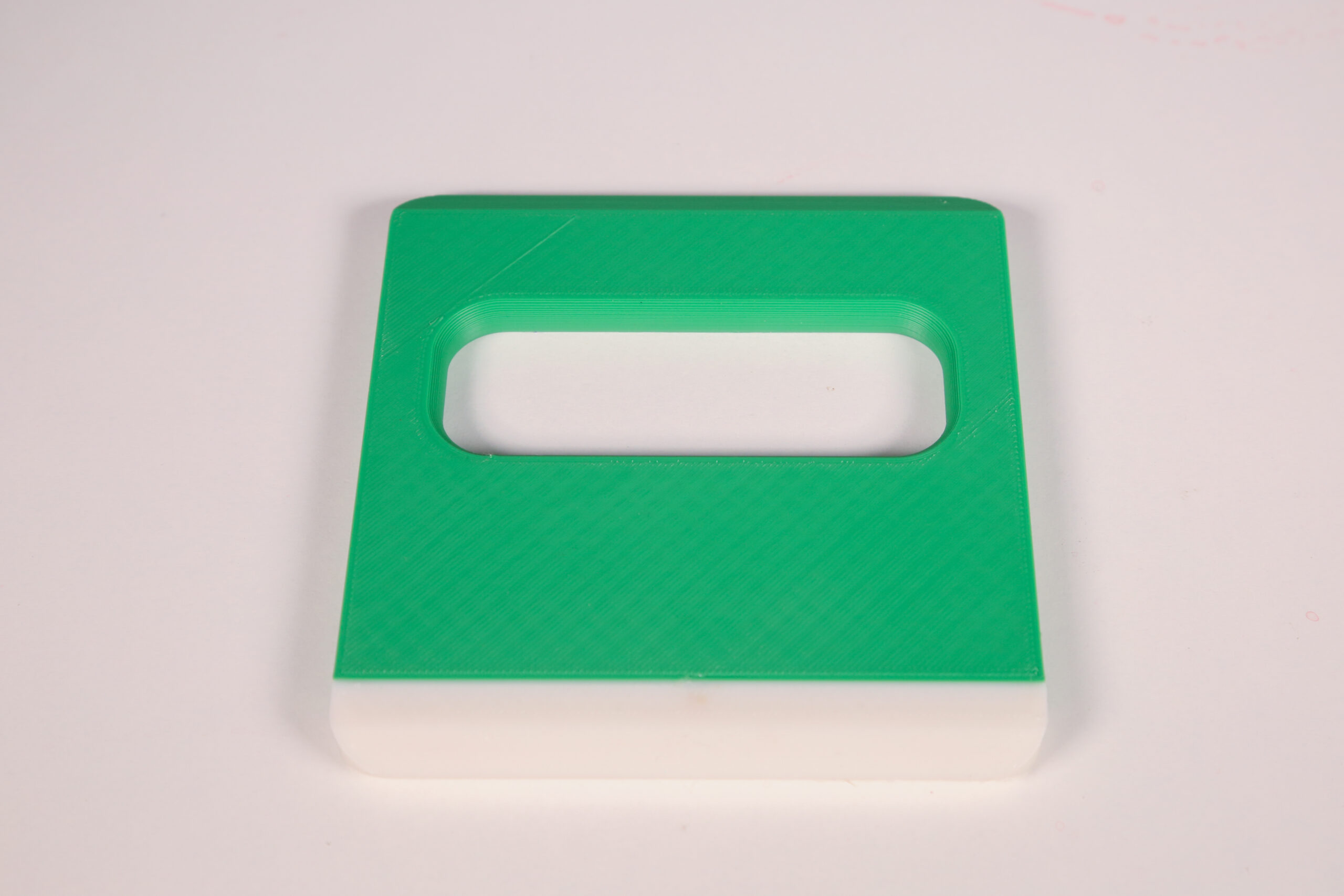
Parameter | Value |
---|---|
Printing time | 2h45 |
Nozzle size | 0.40 mm |
Layer height | 0.20 mm |
Material cost | 3.65 $ |