Comment réduire le poids d’une pièce métallique de 70% avec l’impression 3D
Combiner taille, légèreté et ultra résistance avec le PEKK.
Le poids d’une pièce est une qualité essentielle et stratégique dans la course aux performances aérospatiales et automobiles. Aujourd’hui avec l’impression 3D la possibilité d’alléger un assemblage lourd devient possible.
Découvrez le travail des équipes R&D de Lynxter pour produire des pièces techniques et innovantes : comment augmenter les performances d’une pièce moteur en l’allégeant ? Nous vous détaillerons ici comment en plus de réduire le poids, l’impression 3D vous permet de gagner en temps de production et en coût.
Remplacer une pièce métallique lourde
Au service R&D de Lynxter, nos équipes transfèrent quotidiennement leurs savoir-faire dans le développement d’applications ambitieuses et innovantes pour différents secteurs et industries.
Tester de nouveaux matériaux, lever des verrous technologiques pour repousser les limites du procédé, optimiser la résistance de pièces techniques imprimées sont quelques exemples de leur champ d’études.
Pour cette application, les équipes ont travaillé sur l’amélioration de la masse d’un collecteur d’admission en fonte aluminium. Afin d’optimiser la masse de cet ensemble moteur, nos équipes ont alors dû repenser son design et sa composition.
Du croquis au fichier STL
Le collecteur d’admission est une pièce de moteur utilisée pour repartir le flux d’air pour chaque piston. En partant de l’existant, le technicien de fabrication additive Louis Servel a redessiné la pièce dans le but de l’imprimer en 3D. Il a donc commencé par en faire les croquis.
La pièce est composée d’une conduite principale avec une paroi en structure isogrid.
L’isogrid est un type de structure composée de nervures de raidissement triangulaires intégrées. Ce design utilisé dans les domaines de l’aéronautique et du spatiale créé alors une rigidité par son jeu de nervure : la conduite est alors très résistante malgré une épaisseur de 2 mm et un poids total prévu de seulement 1,5 kilos.
Cette structure est notamment conçue pour éviter les concentrations de contraintes en les redistribuant de façon homogène.
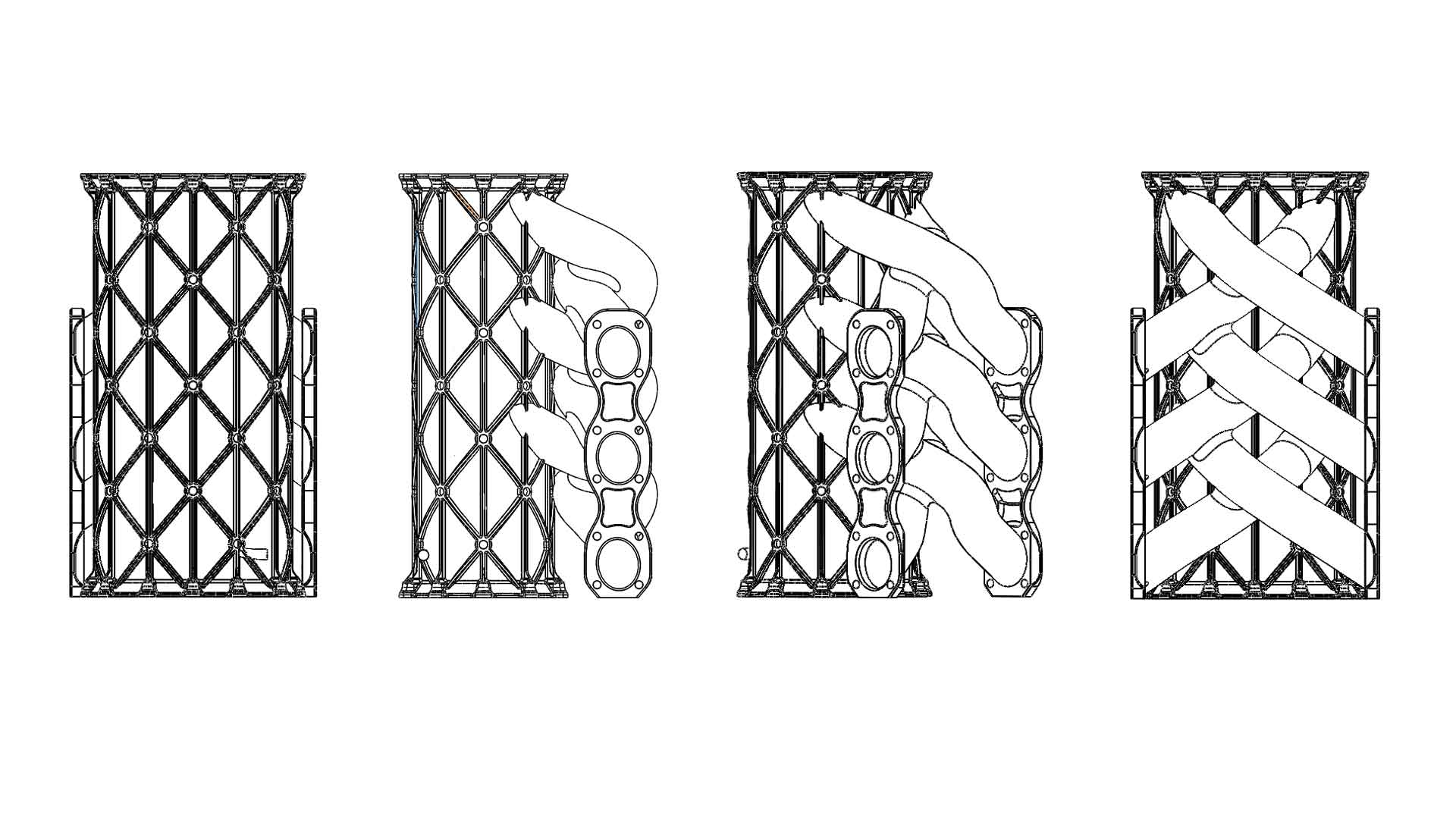
Cette arrivée d’air est prévue pour l’installation d’un filtre haute performance réduisant au maximum les pertes de charges, influençant ainsi le volume d’air admissible. En sortie du filtre on retrouve des conduites entrelacées, celles-ci acheminent l’air du filtre à l’entrée de la chambre de combustion.
L’ajout d’inserts filetés fonctionnalise ce collecteur d’admission et facilite le montage de la pièce sur le système existant. Ces inserts sont montés à chaud augmentant ainsi la résistance de leur intégration à la pièce.
Cette pièce regroupe alors les fonctions suivantes :
– Support du filtre d’air
– Guidage du flux d’air
– Fixation sur bloc moteur existant.
– Maintien des joints d’entrée (par deux gorges à l’avant et l’arrière de l’arrivée d’air)
– Support des capteurs de températures et de pression.

Tout ce travail a été réalisé sur un logiciel de conception 3D puis exporté en un fichier viable pour l’imprimante : le STL. Cette optimisation a nécessité environ 40 heures de dessin.
Ultra performant, ce collecteur est utilisé dans le secteur du sport automobile mais cette modification peut aussi être appliquée à d’autres domaines tels que le ferroviaire, l’aéronautique et le spatiale.
Cette structure complexe à réaliser est généralement fabriquée en 3 à 4 semaines par soustraction de matières type usinage, son poids se situe autour de 5 kilos. Malgré sa difficulté géométrique, le procédé d’impression FFF/MEX/EAM (FDM) de la S600D permet de réaliser cette pièce en une seule étape de 120 h et en un ensemble ce qui induit naturellement une baisse des coûts de fabrication par l’absence de post traitement ou d’outillage et par le temps de production.
Les équipes se sont enfin demandées quel matériau serait le plus à même d’allier légèreté, haute résistance en mécanique et en température.
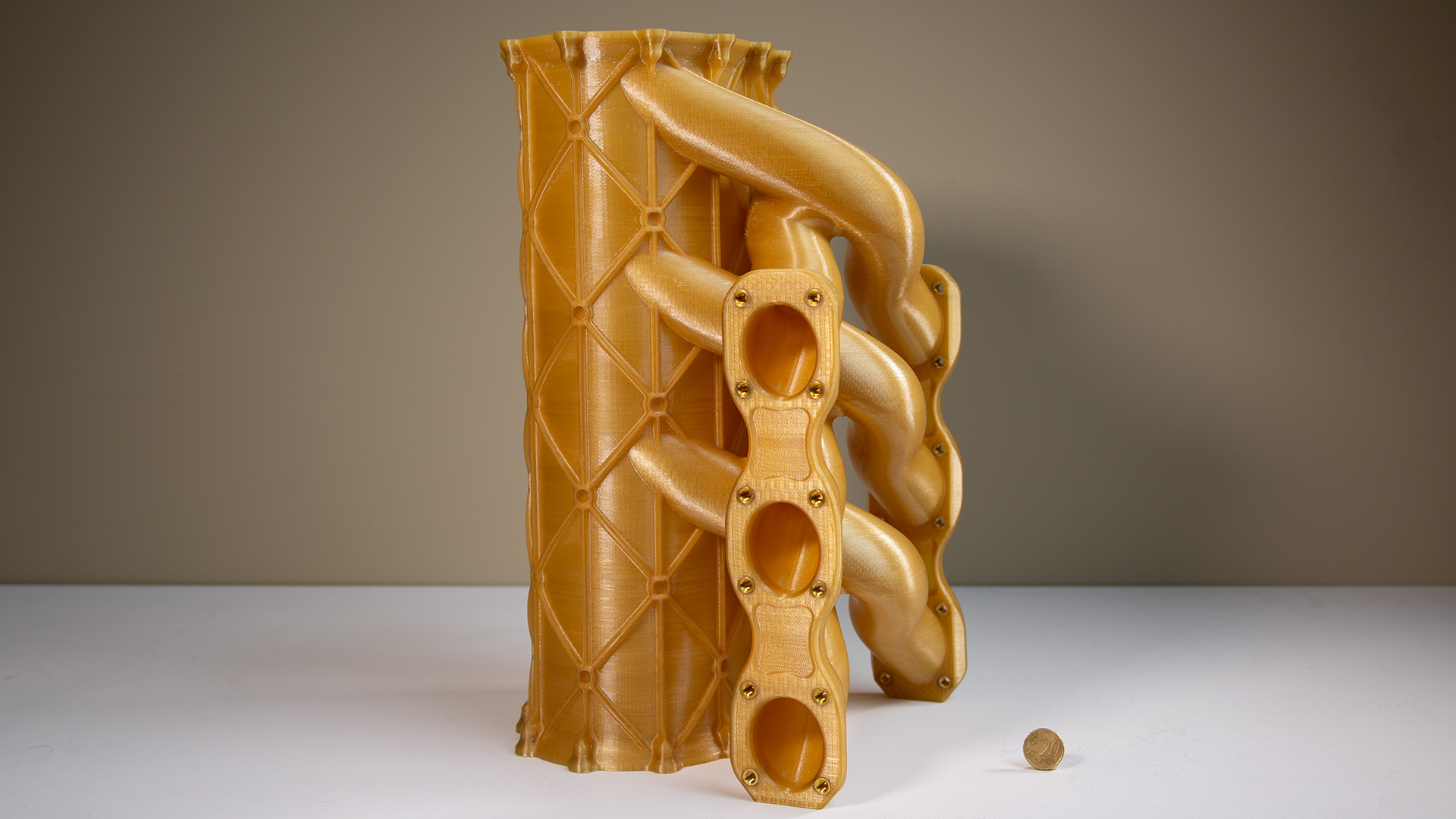
Le choix de l’impression en PEKK
Le polyéthercétonecétone ou autrement nommé PEKK appartient à la famille des PAEK, il est composé principalement de motifs cétones et d’éthers.
Cette combinaison permet au PEKK de supporter des hautes températures de travail ce qui le rend particulièrement indiqué pour des applications industrielles de performance. En plus de sa haute résistance thermique, le PEKK est reconnu pour sa stabilité diélectrique qui lui permet de ne pas interférer avec des courants électriques, et pour ses propriétés ininflammables.
Tout cela fait du PEKK un matériau clef pour des projets d’impression 3D qui doivent s’accommoder d’environnements extrêmes. (Aéronautique – Aerospatiale- Nucléaire)
Le PEKK est donc un matériau de référence quand il s’agit de produire une pièce ultra performante en impression 3D FDM. Cela s’explique notamment par sa résistance haute température (jusqu’ à 170 degrés) sa résistance chimique aux hydrocarbures, solvants organiques et produits corrosifs, et aussi par sa résistance mécanique (traction et compression, chocs et impacts).
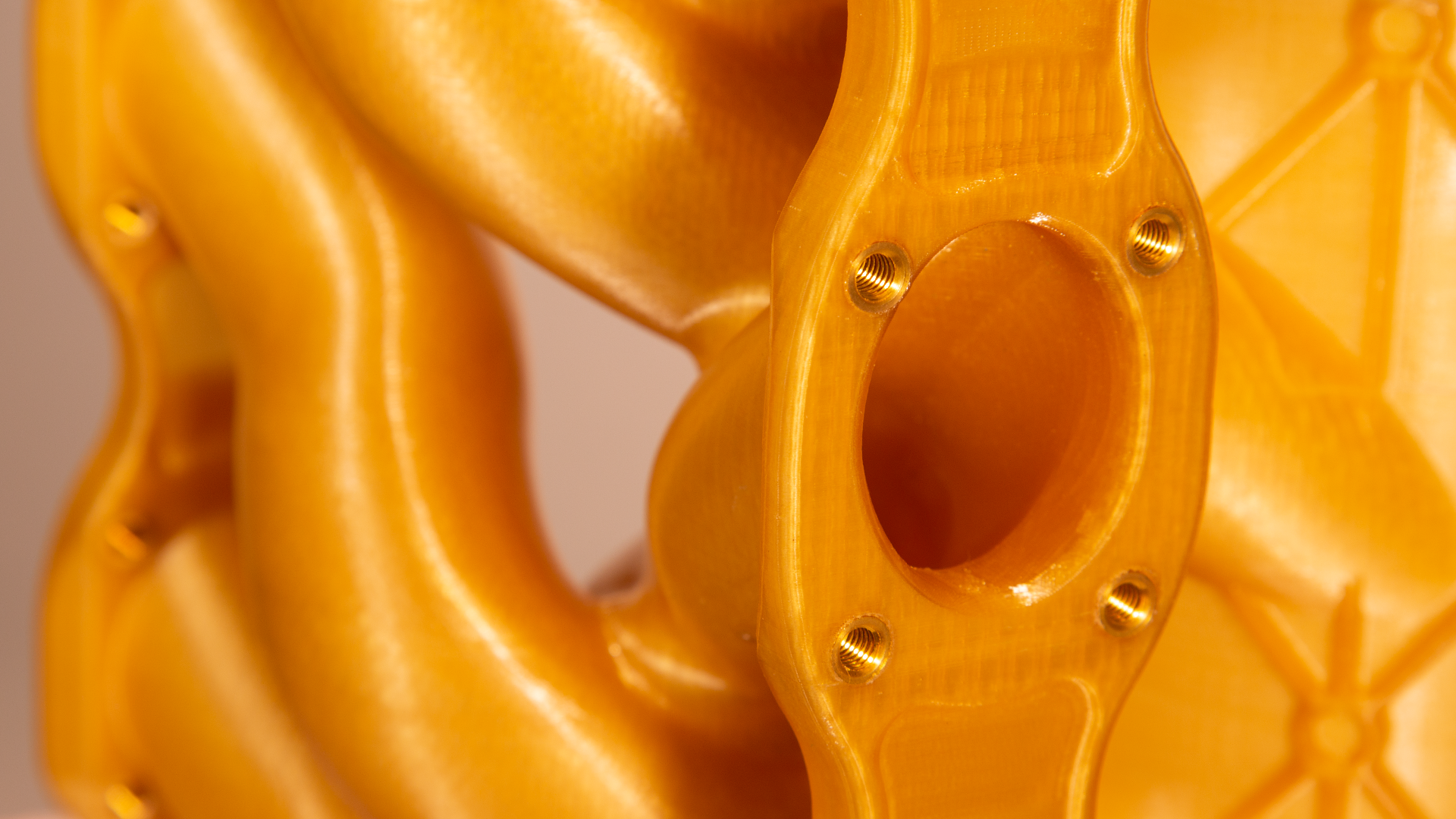
Face aux métaux qui composent habituellement les assemblages mécaniques, ce thermoplastique semi-cristallin est un atout majeur pour l’allègement de machine par son ratio résistance vs poids.
Le choix s’est donc naturellement porté sur le PEKK.
Oui mais dans quelles conditions peut-on imprimer du PEKK en fabrication additive ?
Sa température d’extrusion étant comprise entre 340 et 365 degrés, l’impression du PEKK doit se faire dans une chambre fermée, avec un plateau chauffant et avec une buse d’extrusion supportant ces températures.
L’imprimante 3D S600D de Lynxter équipée de la tête-outil FIL11 qui supporte des températures de chambre à 70 degrés répondent aux conditions d’impression du PEKK.
Pour récapituler:
IMPRESSION 3D FONDERIE + USINAGE
DELAIS | 120h soit 5 jours | 3 à 4 semaines |
POIDS | 1,5kg avec le PEKK | Environ 5kg |
COÛT | Matière Utilisation machine |
4 semaines de production Petite série Matière |
PERFORMANCES | Les performances techniques de la pièce sont inchangées, l’ensemble lui gagne en légèreté. |
Vous voulez en savoir plus sur ce cas d’application ? N’hésitez pas à nous joindre pour obtenir plus d’information.
Les conditions d’impression 3D avec la S600D– L’échangeur thermique a été réalisé en PEKK- 3DXtech. |