COMMENT L’IMPRIMANTE 3D INDUSTRIELLE S600D PERMET D’ÊTRE RÉACTIF DANS UNE SITUATION D’URGENCE ou DE RUPTURE DE SUPPLY CHAIN ?
Lynxter et sa machine-outil de fabrication additive, la S600D, ont été sollicités par une entreprise du secteur ferroviaire pour résoudre une problématique de maintenance sur un train.
L’impression 3D silicone face à l’imprévu
L’entreprise doit changer une pièce défectueuse sur l’un de ses trains et se retrouve face à une rupture de stock. Cette pièce habituellement produite par injection, nécessite un délai d’approvisionnement de plusieurs mois. Un délai que l’entreprise n’a pas pu anticiper du fait du caractère imprévisible de l’évènement. Dès lors que cette pièce est endommagée ou manquante, le train peut rester immobilisé, ce qui entraine des pertes financières importantes pour l’entreprise.
La pièce en question est un soufflet d’étanchéité pour un système de frein qui a pour fonction d’assurer l’étanchéité du système face à l’eau, la poussière, graisse et ballaste. Il est peu exposé et nécessite l’utilisation d’un matériau très souple : le silicone est donc le matériau idéal.
La fabrication additive en silicone se présente alors comme une alternative idéale pour répondre rapidement à ce besoin ponctuel et urgent. Comment passer d’une pièce moulée à une pièce imprimée en 3D?
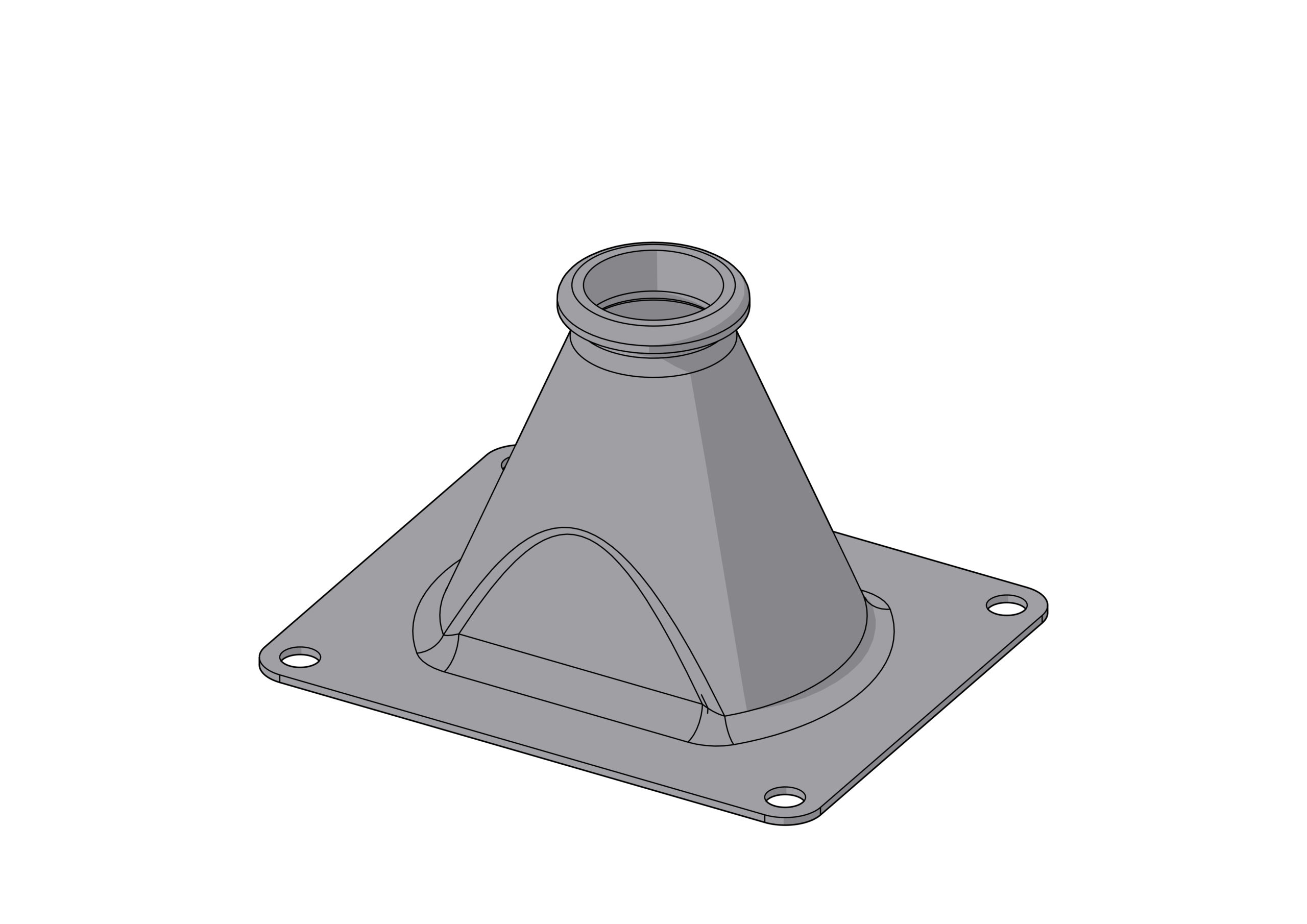
À chaque procédé, sa CAO
Le soufflet en silicone a été imprimé en 3D par Lynxter sur sa machine-outil de fabrication additive, la S600D, à l’aide de l’outil de dépose liquide bi-composant LIQ21 . Cette première version a été imprimée selon le modèle fourni par l’entreprise, initialement dessiné pour l’injection.
Le résultat : les congés en dessous de la pièce imprimée en 3D et la bordure supérieure du soufflet ne s’impriment pas correctement.
La conclusion est rapide, la pièce dessinée pour l’injection n’est pas exploitable en impression 3D. Les défauts induits par les limitations sont trop importants pour que la pièce puisse être mise en application (bavures, dégradation des surfaces supportées, affaissement dus à des zones trop fines).
La conception d’une pièce doit être adaptée au procédé de fabrication utilisé : les règles de design sont différentes en fonction des possibilités et limites de chaque procédé de production.
En modifiant légèrement la CAO dans la limite des fonctions définies par le bureau d’étude, il a été possible d’imprimer une seconde version de la pièce en fabrication additive grâce à l’imprimante 3D industrielle de Lynxter : la S600D. Il est important de retenir que la technologie utilisée par la S600D repose sur la superposition de couches de matière. Il est souvent impossible d’imprimer une couche de silicone dans le vide, il faut donc s’assurer que la couche supérieure repose entièrement ou partiellement sur une couche inférieure. Les angles en porte-à-faux « overhangs » sont à éviter ainsi que les congés trop importants.
Pour la bordure supérieure du soufflet, le porte-à-faux à 90° a été remplacé par un chanfrein afin que chaque couche puisse reposer partiellement sur la couche antérieure.
Dans le cas du congé en dessous de la pièce, l’angle arrondi ne permet pas une correcte superposition des couches. Dans ce cas, il est préférable de modéliser un angle à 45° type chanfrein.
La conception assistée par ordinateur (CAO) a permis d’optimiser rapidement une modélisation afin de l’adapter pour la fabrication additive par dépose de liquide. De manière générale, il est recommandé pour une impression en silicone d’avoir des porte-à-faux inférieurs à 45° afin de s’assurer de l’imprimabilité de la pièce.
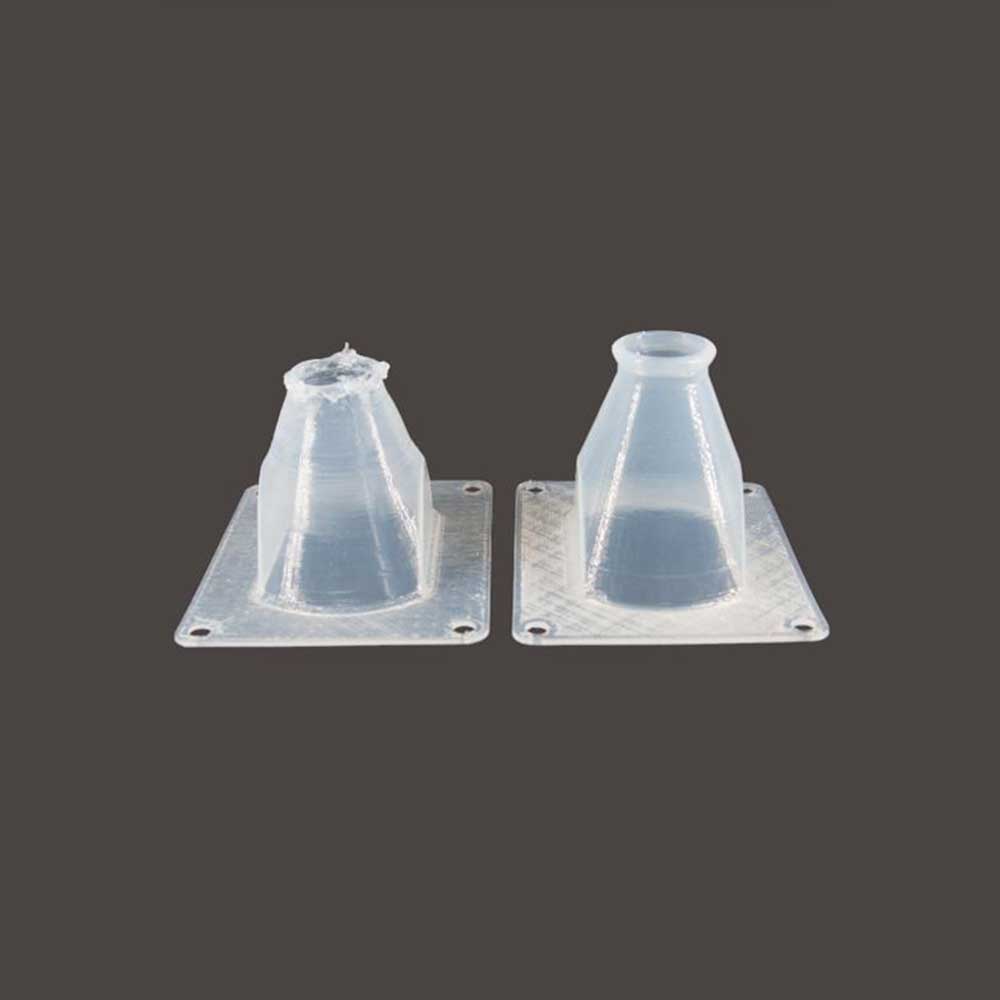
Résultat : un gain de temps précieux
La situation de blocage a pu être levée rapidement grâce à la fabrication additive ainsi qu’à une rapide modification de la CAO d’origine. Cette opération de maintenance qui aurait demandé plusieurs semaines avec la supply chain classique, n’a duré que quelques jours en ayant recours à la S600D.
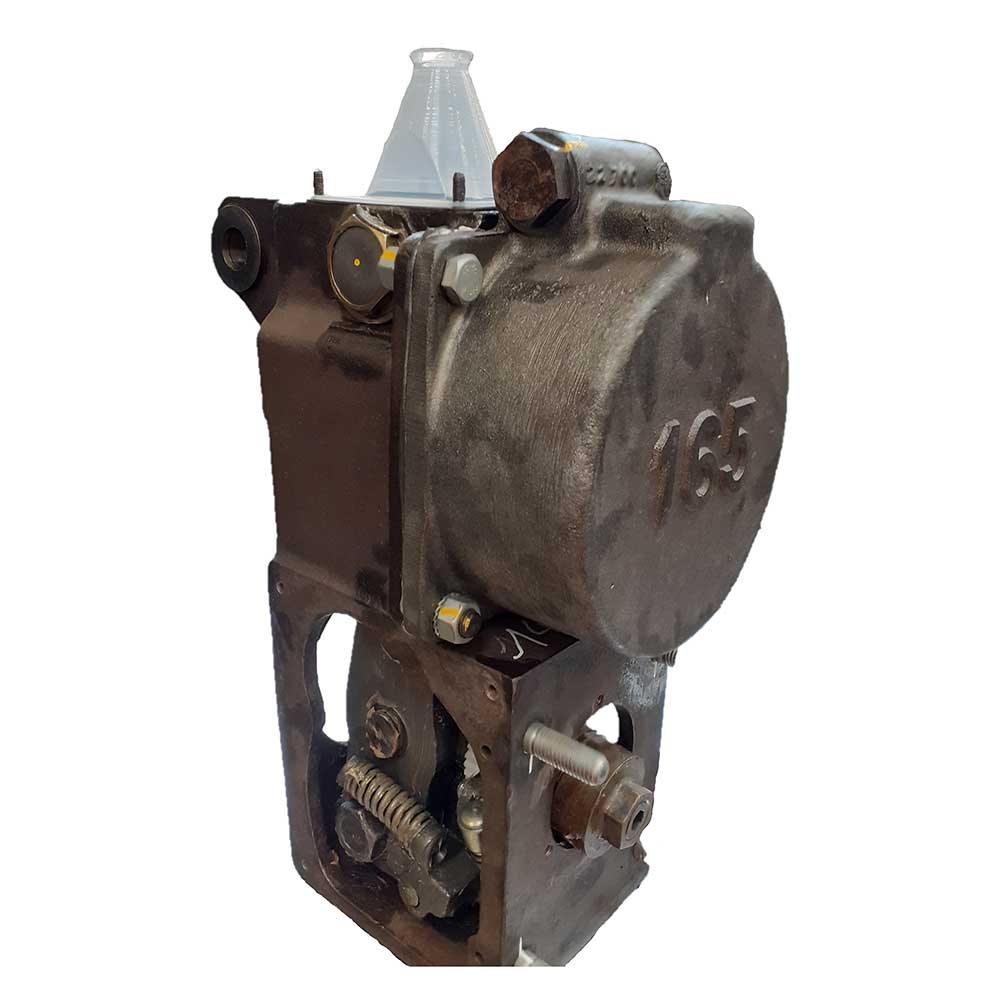