Révolutionner la fabrication d’actionneurs pneumatiques souples grâce à l’impression 3D silicone et la robotique
La Fabrication Additive (FA), également connue sous le nom d’impression 3D, a suscité un intérêt considérable ces dernières années en raison de ses nombreux avantages par rapport aux méthodes de fabrication traditionnelles.
Un domaine où l’impression 3D liquide (également appelée écriture directe d’encre dans le secteur de la recherche et MEX dans l’industrie) est particulièrement prometteuse est la production d’Actionneurs Pneumatiques Souples (APS). Les APS sont largement utilisés dans le domaine de la robotique et présentent des conceptions complexes nécessitant souvent des matériaux flexibles. Les techniques traditionnelles de fabrication par moulage limitent les possibilités de conception et entravent l’intégration de nouvelles fonctionnalités.
Dans cet article, nous proposons une nouvelle méthode appelée Local Layer Splitting (LLS) qui révolutionne la fabrication des APS en définissant leurs propriétés mécaniques lors de la phase de fabrication plutôt que lors de la modélisation 3D. Cette méthode permet une plus grande liberté de conception, personnalisation et contrôle des propriétés mécaniques des APS.
Lien pour télécharger l’article complet à la fin de cet article.
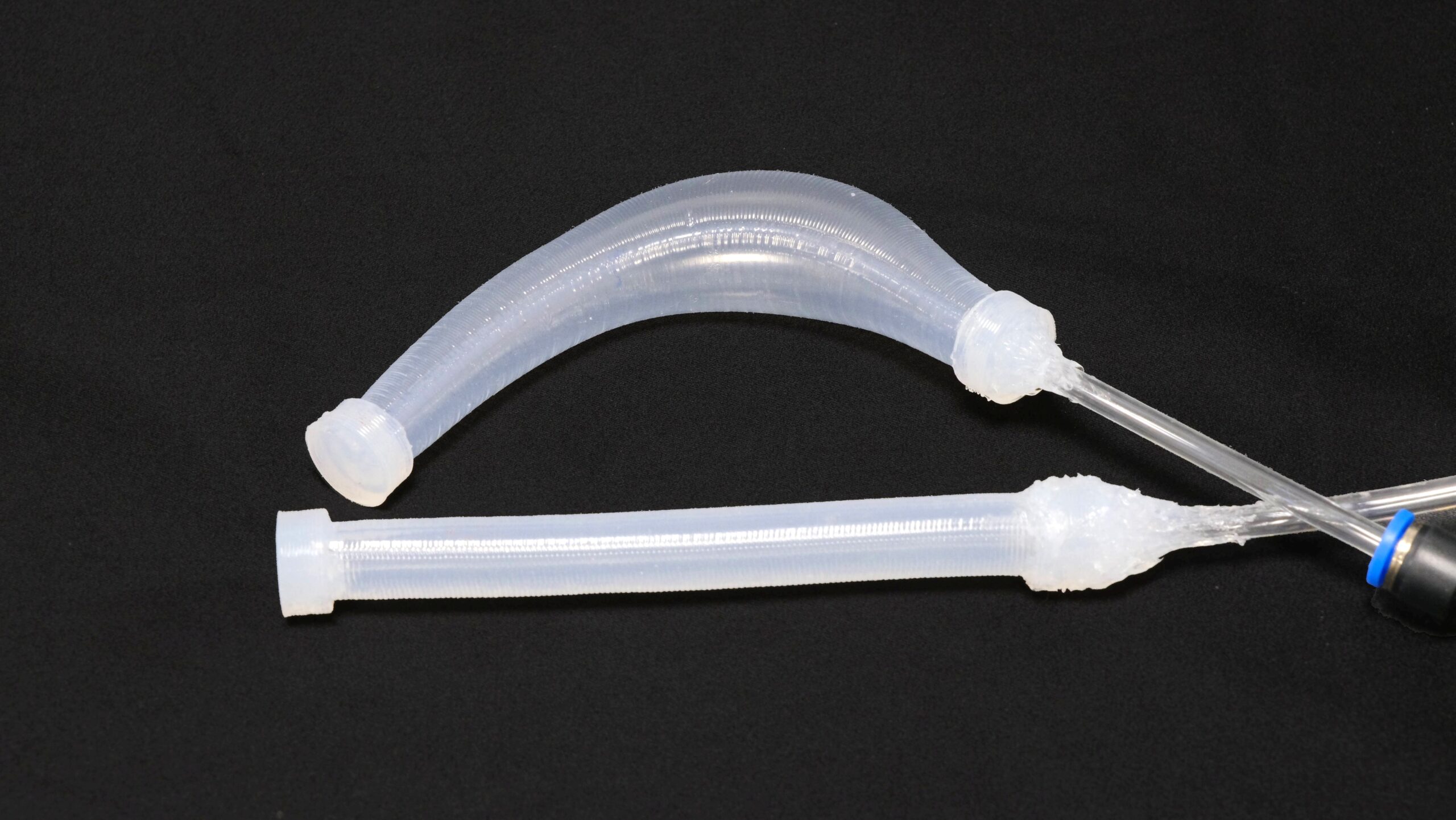
Actionneur Pneumatique Souple imprimé en 3D utilisant notre technique de fabrication LLS. (Bas) La forme de l’actionneur reste inchangée lorsqu’il n’est pas sous pression. (Haut) L’actionneur se plie sous pression.
Local Layer Splitting : La Méthode de Fabrication
La méthode de fabrication LLS introduit une variation locale de la hauteur de couche du silicone imprimé en 3D, ce qui crée des propriétés mécaniques anisotropes non uniformes dans les APS. Contrairement aux processus traditionnels de fabrication additive, où la hauteur de couche reste constante tout au long du processus d’impression, le LLS permet d’avoir des hauteurs de couche différentes au sein d’une seule couche. Cette technique affecte la rigidité des parois en silicone imprimées localement, ce qui entraîne une déformation mécanique contrôlée sous pression. Les propriétés mécaniques de l’APS sont définies lors de la phase de fabrication, les rendant indépendantes de l’aspect de l’objet. Cette approche ouvre de nouvelles possibilités pour créer des APS avec différents comportements de flexion sans modifier le modèle 3D.
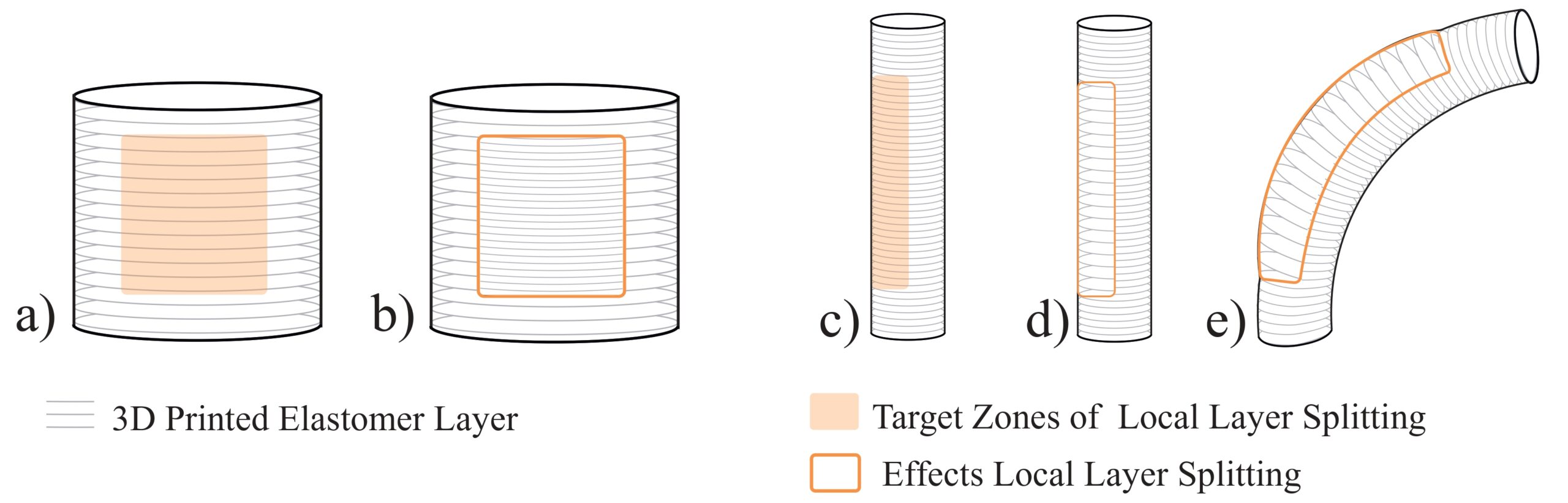
Illustration de la technique LLS. (a) Une pièce imprimée en 3D, la zone orange, est la cible du LLS. (b) La zone encadrée montre l’effet du LLS, entraînant une hauteur de couche différente. (c) Illustration cylindrique d’un APS avec une zone cible du LLS. (d) L’effet du LLS à l’état de repos et (e) montre l’actionneur en état gonflé
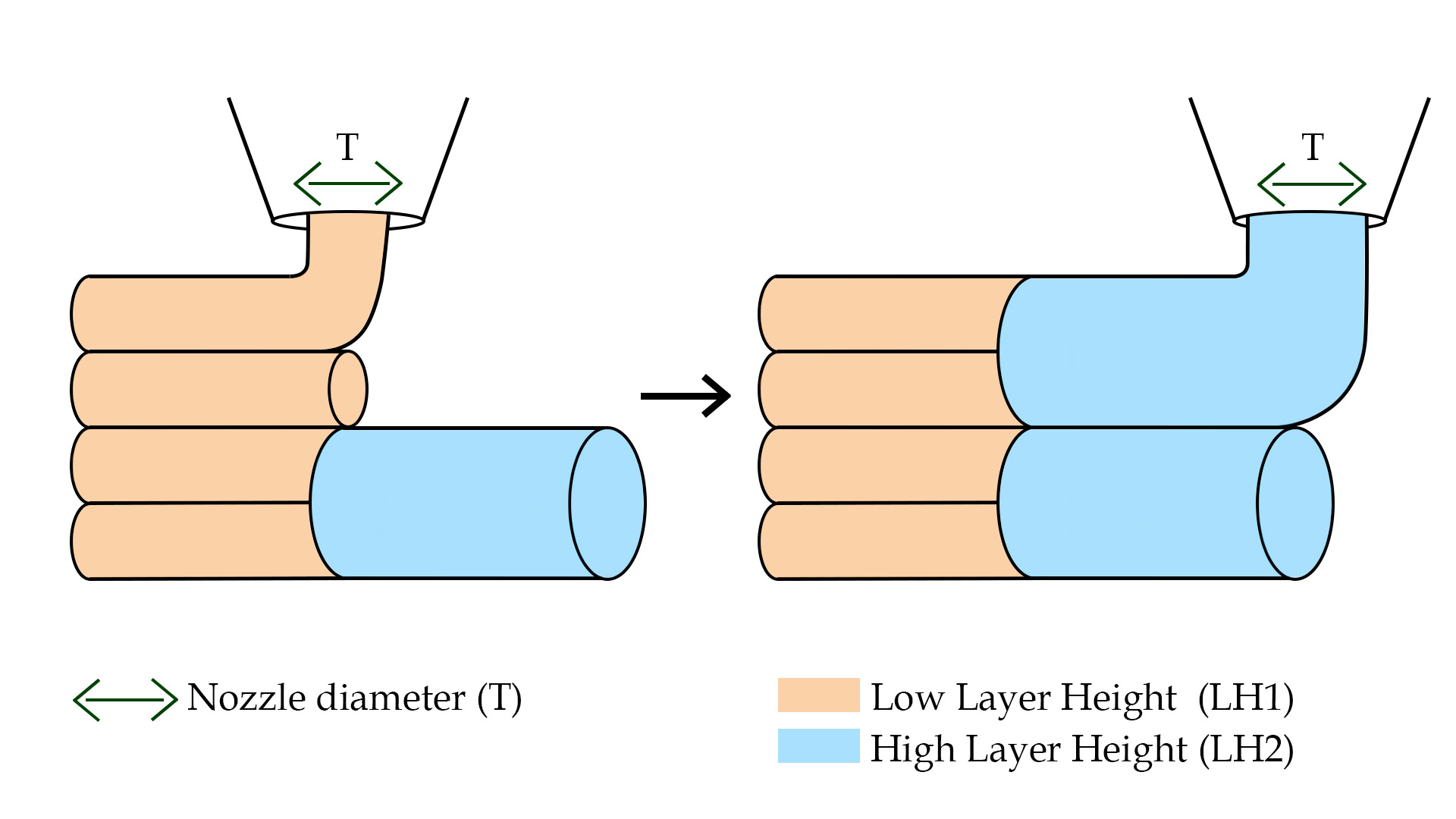
Illustration du processus d’impression 3D LLS.
Caractérisation Expérimentale
Pour valider la méthode LLS, nous avons réalisé plusieurs tests expérimentaux. Tout d’abord, nous avons évalué l’impact des paramètres de hauteur de couche sur la rigidité du silicone imprimé en 3D par des tests de traction. Les résultats ont montré que la hauteur de couche affecte directement la rigidité du matériau. Nous avons également développé un programme spécial pour générer des G-codes avec des variations locales de la hauteur de couche, permettant ainsi d’intégrer le LLS dans le processus de fabrication.
Nous avons ensuite fabriqué des APS cylindriques en utilisant le processus LLS et évalué leurs angles de flexion et leurs forces bloquées sous différentes pressions internes d’air.
Les résultats ont démontré que les APS activés par LLS atteignaient des angles de flexion significatifs et présentaient des performances comparables aux APS de pointe. Le comportement de flexion pouvait être précisément contrôlé en ajustant la hauteur de couche et le diamètre de la buse.
Révolutionner la Fabrication d’Actionneurs Pneumatiques Souples grâce à l’Impression 3D en Silicone et à la Robotique
Impact et Applications du LLS
La technique LLS offre de nombreuses opportunités pour la conception et la fabrication d’APS. En dissociant les propriétés mécaniques de la conception de l’objet, le LLS permet une conception itérative et une personnalisation des APS. Le processus de fabrication est entièrement automatisé, ce qui permet de gagner du temps et de réduire les erreurs. Nous avons présenté deux exemples pour illustrer les applications potentielles du LLS : une pince à trois doigts et un actionneur à multiples comportements de flexion.
La pince à trois doigts a démontré ses capacités de préhension, tandis que l’actionneur a présenté les possibilités mécaniques complexes rendues possibles par le LLS.
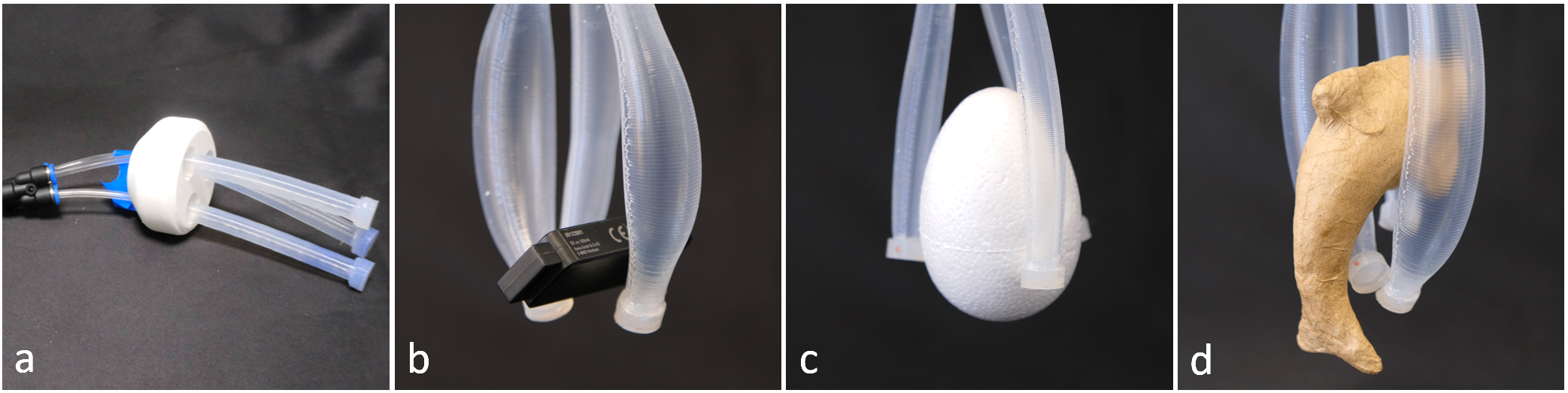
Test de préhension de la pince à trois doigts. (a) Deux doigts ont un diamètre de buse T=0,86 mm et le dernier T=0,69 mm pour une résistance accrue, simulant ainsi un pouce. La pince a démontré son potentiel de manipulation d’objets ; (b) une clé USB (25,4 g), (c) un œuf en polyester (8,6 g) et un modèle en carton (36,7 g)..
Discussion et Travaux Futurs
La méthode LLS représente une avancée significative dans la fabrication des APS, offrant une plus grande souplesse de conception, personnalisation et contrôle du comportement mécanique des APS. Cependant, il reste encore des possibilités d’exploration et d’amélioration. Les travaux futurs comprennent l’exploration de paramètres de contrôle de fabrication additive supplémentaires, l’optimisation du programme spécial pour une utilisation conviviale et l’étude d’autres formes d’APS et variations de remplissage. En continuant à affiner et à développer la technique LLS, nous pouvons ouvrir encore plus de possibilités pour des conceptions d’APS innovantes et des applications.
En conclusion, la méthode LLS présente une approche novatrice pour la fabrication d’APS avec des propriétés mécaniques définies pendant la phase de fabrication. En intégrant des variations locales de hauteur de couche, les APS peuvent présenter une déformation mécanique contrôlée et des propriétés anisotropes.
Télécharger l’article complet et détaillé (en anglais):